Information injection-pump assembly
ZEXEL
101697-9020
1016979020
NISSAN-DIESEL
16713Z6861
16713z6861
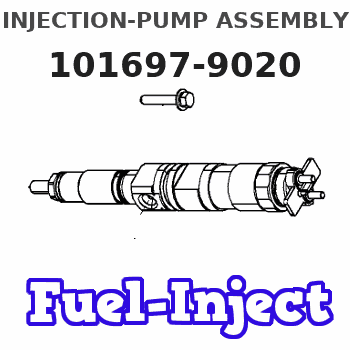
Rating:
Service parts 101697-9020 INJECTION-PUMP ASSEMBLY:
1.
_
7.
COUPLING PLATE
8.
_
9.
_
11.
Nozzle and Holder
16600-Z5578
12.
Open Pre:MPa(Kqf/cm2)
16.7{170}/21.6{220}
15.
NOZZLE SET
Cross reference number
ZEXEL
101697-9020
1016979020
NISSAN-DIESEL
16713Z6861
16713z6861
Zexel num
Bosch num
Firm num
Name
Calibration Data:
Adjustment conditions
Test oil
1404 Test oil ISO4113 or {SAEJ967d}
1404 Test oil ISO4113 or {SAEJ967d}
Test oil temperature
degC
40
40
45
Nozzle and nozzle holder
105780-8140
Bosch type code
EF8511/9A
Nozzle
105780-0000
Bosch type code
DN12SD12T
Nozzle holder
105780-2080
Bosch type code
EF8511/9
Opening pressure
MPa
17.2
Opening pressure
kgf/cm2
175
Injection pipe
Outer diameter - inner diameter - length (mm) mm 6-2-600
Outer diameter - inner diameter - length (mm) mm 6-2-600
Overflow valve
134424-1520
Overflow valve opening pressure
kPa
162
147
177
Overflow valve opening pressure
kgf/cm2
1.65
1.5
1.8
Tester oil delivery pressure
kPa
157
157
157
Tester oil delivery pressure
kgf/cm2
1.6
1.6
1.6
Direction of rotation (viewed from drive side)
Right R
Right R
Injection timing adjustment
Direction of rotation (viewed from drive side)
Right R
Right R
Injection order
1-4-2-6-
3-5
Pre-stroke
mm
3.9
3.85
3.95
Beginning of injection position
Drive side NO.1
Drive side NO.1
Difference between angles 1
Cal 1-4 deg. 60 59.5 60.5
Cal 1-4 deg. 60 59.5 60.5
Difference between angles 2
Cyl.1-2 deg. 120 119.5 120.5
Cyl.1-2 deg. 120 119.5 120.5
Difference between angles 3
Cal 1-6 deg. 180 179.5 180.5
Cal 1-6 deg. 180 179.5 180.5
Difference between angles 4
Cal 1-3 deg. 240 239.5 240.5
Cal 1-3 deg. 240 239.5 240.5
Difference between angles 5
Cal 1-5 deg. 300 299.5 300.5
Cal 1-5 deg. 300 299.5 300.5
Injection quantity adjustment
Adjusting point
-
Rack position
13.7
Pump speed
r/min
700
700
700
Average injection quantity
mm3/st.
99.5
97.5
101.5
Max. variation between cylinders
%
0
-3.5
3.5
Basic
*
Fixing the rack
*
Standard for adjustment of the maximum variation between cylinders
*
Injection quantity adjustment_02
Adjusting point
H
Rack position
10.1+-0.
5
Pump speed
r/min
275
275
275
Average injection quantity
mm3/st.
8.6
6.8
10.4
Max. variation between cylinders
%
0
-10
10
Fixing the rack
*
Standard for adjustment of the maximum variation between cylinders
*
Injection quantity adjustment_03
Adjusting point
A
Rack position
R1(13.7)
Pump speed
r/min
700
700
700
Average injection quantity
mm3/st.
99.5
98.5
100.5
Basic
*
Fixing the lever
*
Boost pressure
kPa
29.3
29.3
Boost pressure
mmHg
220
220
Injection quantity adjustment_04
Adjusting point
B
Rack position
R1-0.05
Pump speed
r/min
1400
1400
1400
Average injection quantity
mm3/st.
103.5
100.3
106.7
Fixing the lever
*
Boost pressure
kPa
29.3
29.3
Boost pressure
mmHg
220
220
Injection quantity adjustment_05
Adjusting point
C
Rack position
R2[R1-0.
3]
Pump speed
r/min
250
250
250
Average injection quantity
mm3/st.
85.5
82.3
88.7
Fixing the lever
*
Boost pressure
kPa
29.3
29.3
Boost pressure
mmHg
220
220
Injection quantity adjustment_06
Adjusting point
D
Rack position
R2-1.3
Pump speed
r/min
250
250
250
Average injection quantity
mm3/st.
63
59.8
66.2
Fixing the lever
*
Boost pressure
kPa
0
0
0
Boost pressure
mmHg
0
0
0
Injection quantity adjustment_07
Adjusting point
I
Rack position
-
Pump speed
r/min
150
150
150
Average injection quantity
mm3/st.
89
89
109
Fixing the lever
*
Boost pressure
kPa
0
0
0
Boost pressure
mmHg
0
0
0
Rack limit
*
Boost compensator adjustment
Pump speed
r/min
250
250
250
Rack position
R2-1.3
Boost pressure
kPa
4
2.7
5.3
Boost pressure
mmHg
30
20
40
Boost compensator adjustment_02
Pump speed
r/min
250
250
250
Rack position
R2[R1+0.
3]
Boost pressure
kPa
16
16
16
Boost pressure
mmHg
120
120
120
Timer adjustment
Pump speed
r/min
1170--
Advance angle
deg.
0
0
0
Remarks
Start
Start
Timer adjustment_02
Pump speed
r/min
450
Advance angle
deg.
1
0.5
1.5
Timer adjustment_03
Pump speed
r/min
(530)
Advance angle
deg.
0
0
0
Remarks
Measure the actual speed.
Measure the actual speed.
Timer adjustment_04
Pump speed
r/min
1120
Advance angle
deg.
0.5
Timer adjustment_05
Pump speed
r/min
1400
Advance angle
deg.
4.5
4
5
Remarks
Finish
Finish
Test data Ex:
Governor adjustment
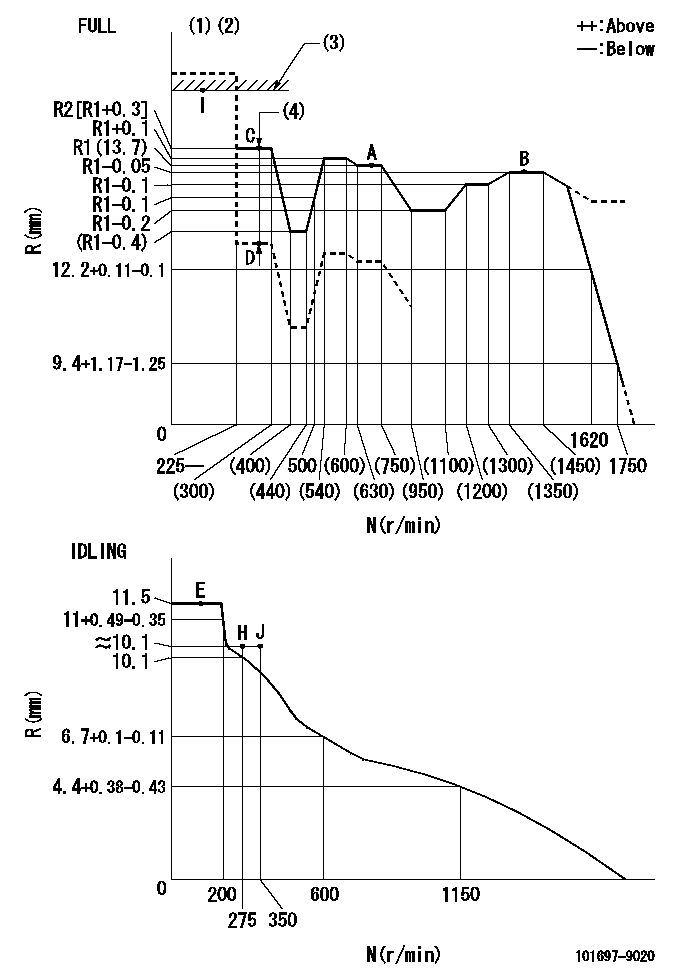
N:Pump speed
R:Rack position (mm)
(1)Torque cam stamping: T1
(2)Tolerance for racks not indicated: +-0.05mm.
(3)RACK LIMIT
(4)Boost compensator stroke: BCL
----------
T1=N24 BCL=1.3+-0.1mm
----------
----------
T1=N24 BCL=1.3+-0.1mm
----------
Speed control lever angle

F:Full speed
I:Idle
(1)Use the hole at R = aa
(2)Stopper bolt setting
----------
aa=36mm
----------
a=25deg+-5deg b=(38deg)+-3deg
----------
aa=36mm
----------
a=25deg+-5deg b=(38deg)+-3deg
Stop lever angle

N:Pump normal
S:Stop the pump.
(1)Use the pin at R = aa
----------
aa=42mm
----------
a=40deg+-5deg b=25deg+-5deg
----------
aa=42mm
----------
a=40deg+-5deg b=25deg+-5deg
0000001501 RACK SENSOR

(VR) measurement voltage
(I) Part number of the control unit
(G) Apply red paint.
(H): End surface of the pump
1. Rack limit adjustment
(1)Fix the rack at the rack limit position Ra.
(2)Install the shim (D) to the rod (C) and tighten nut (E).
(3)Select a shim (D) so that the distance between the end surface of the pump and the nut (E) is L.
(4)Release the rack fixing and mount the joint (B) and fix.
(5)At this time, confirm that the shim (D) does not interfere with the joint (B).
2. Rack sensor adjustment (-0420)
(1)Screw in the bobbin (A) until it contacts the joint (B).
(2)Fix the speed control lever at the full side.
(3)Set the speed to N1 r/min.
(4)Adjust the depth that the bobbin (A) is screwed in so that the control unit's rack sensor output voltage is VR+-0.02 V, then tighten the nut (F).
(5)Apply G at two places.
Connecting part between the joint (B) and the nut (F)
Connecting part between the joint (B) and the end surface of the pump (H)
----------
L=33-0.2mm N1=700r/min Ra=R1(13.7)mm
----------
----------
L=33-0.2mm N1=700r/min Ra=R1(13.7)mm
----------
Timing setting
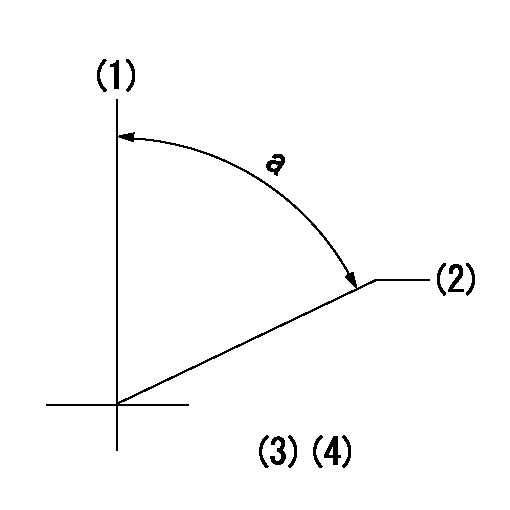
(1)Pump vertical direction
(2)Position of timer's threaded hole at No 1 cylinder's beginning of injection
(3)-
(4)-
----------
----------
a=(60deg)
----------
----------
a=(60deg)
Information:
Test Procedure
System Operation
A contactor is a pressure switch or a contactor is a level switch. Contactors can be adjusted in order to operate at a given temperature or pressure.Contactors are set to shutdown setpoints and monitored by the MMS. When a contactor for the shutdown system closes the MMS secures the engine.
Illustration 1 g00563590
Diagram of a contactor
Illustration 2 g00562905
Schematic of the contactorFunctional Test
Check the electrical connectors and check the wiring.
Bodily contact with electrical potential can cause bodily injury or death.To avoid the possibility of injury or death, ensure that the main power supply has been disconnected before performing any maintenance or removing any modules.
Disconnect the power supply.
Check the electrical connectors and check the wiring for damage or bad connections.
Verify that all modules are properly seated.
Verify the status of the LED on the SLC 5/04.The results of the preceding procedure are in the following list:
All of the components are fully installed. All of the components are free of corrosion. All of the components are free of damage. All of the modules are properly seated. Proceed to 2.
The components are not fully installed. The components are not free of corrosion. The components are damaged. All of the modules are not properly seated. Repair the component. Verify that the repair resolves the problem. STOP.
Check for drift.
Apply pressure or apply temperature. Determine when the contact closes.
Measure the continuity between the common terminal and the normally open terminal. Determine when the contact closes.The results of the preceding procedure are in the following list:
The contact closes when the contact is actuated. Proceed to 3.
The contact does not close when the contact is actuated. Replace the contactor. Verify that the repair resolves the problem. Stop.
Check the contactor for chatter.
Verify that the contactor is adjusted to the original setpoint.The results of the preceding procedure are in the following list:
The contactor does not cycle frequently. Stop.
The contactor cycles frequently. Replace the contactor. Verify that the repair resolves the problem. Stop.
System Operation
A contactor is a pressure switch or a contactor is a level switch. Contactors can be adjusted in order to operate at a given temperature or pressure.Contactors are set to shutdown setpoints and monitored by the MMS. When a contactor for the shutdown system closes the MMS secures the engine.
Illustration 1 g00563590
Diagram of a contactor
Illustration 2 g00562905
Schematic of the contactorFunctional Test
Check the electrical connectors and check the wiring.
Bodily contact with electrical potential can cause bodily injury or death.To avoid the possibility of injury or death, ensure that the main power supply has been disconnected before performing any maintenance or removing any modules.
Disconnect the power supply.
Check the electrical connectors and check the wiring for damage or bad connections.
Verify that all modules are properly seated.
Verify the status of the LED on the SLC 5/04.The results of the preceding procedure are in the following list:
All of the components are fully installed. All of the components are free of corrosion. All of the components are free of damage. All of the modules are properly seated. Proceed to 2.
The components are not fully installed. The components are not free of corrosion. The components are damaged. All of the modules are not properly seated. Repair the component. Verify that the repair resolves the problem. STOP.
Check for drift.
Apply pressure or apply temperature. Determine when the contact closes.
Measure the continuity between the common terminal and the normally open terminal. Determine when the contact closes.The results of the preceding procedure are in the following list:
The contact closes when the contact is actuated. Proceed to 3.
The contact does not close when the contact is actuated. Replace the contactor. Verify that the repair resolves the problem. Stop.
Check the contactor for chatter.
Verify that the contactor is adjusted to the original setpoint.The results of the preceding procedure are in the following list:
The contactor does not cycle frequently. Stop.
The contactor cycles frequently. Replace the contactor. Verify that the repair resolves the problem. Stop.