Information injection-pump assembly
BOSCH
F 019 Z10 615
f019z10615
ZEXEL
101695-3620
1016953620
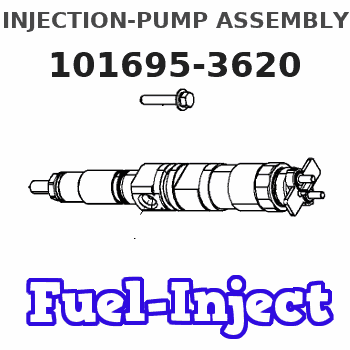
Rating:
Service parts 101695-3620 INJECTION-PUMP ASSEMBLY:
1.
_
5.
AUTOM. ADVANCE MECHANIS
6.
COUPLING PLATE
7.
COUPLING PLATE
8.
_
9.
_
11.
Nozzle and Holder
12.
Open Pre:MPa(Kqf/cm2)
19.6(200)
15.
NOZZLE SET
Cross reference number
BOSCH
F 019 Z10 615
f019z10615
ZEXEL
101695-3620
1016953620
Zexel num
Bosch num
Firm num
Name
Calibration Data:
Adjustment conditions
Test oil
1404 Test oil ISO4113 or {SAEJ967d}
1404 Test oil ISO4113 or {SAEJ967d}
Test oil temperature
degC
40
40
45
Nozzle and nozzle holder
105780-8140
Bosch type code
EF8511/9A
Nozzle
105780-0000
Bosch type code
DN12SD12T
Nozzle holder
105780-2080
Bosch type code
EF8511/9
Opening pressure
MPa
17.2
Opening pressure
kgf/cm2
175
Injection pipe
Outer diameter - inner diameter - length (mm) mm 6-2-600
Outer diameter - inner diameter - length (mm) mm 6-2-600
Tester oil delivery pressure
kPa
157
157
157
Tester oil delivery pressure
kgf/cm2
1.6
1.6
1.6
Direction of rotation (viewed from drive side)
Right R
Right R
Injection timing adjustment
Direction of rotation (viewed from drive side)
Right R
Right R
Injection order
1-5-3-6-
2-4
Pre-stroke
mm
3.6
3.55
3.65
Beginning of injection position
Drive side NO.1
Drive side NO.1
Difference between angles 1
Cal 1-5 deg. 60 59.5 60.5
Cal 1-5 deg. 60 59.5 60.5
Difference between angles 2
Cal 1-3 deg. 120 119.5 120.5
Cal 1-3 deg. 120 119.5 120.5
Difference between angles 3
Cal 1-6 deg. 180 179.5 180.5
Cal 1-6 deg. 180 179.5 180.5
Difference between angles 4
Cyl.1-2 deg. 240 239.5 240.5
Cyl.1-2 deg. 240 239.5 240.5
Difference between angles 5
Cal 1-4 deg. 300 299.5 300.5
Cal 1-4 deg. 300 299.5 300.5
Injection quantity adjustment
Adjusting point
A
Rack position
8.6
Pump speed
r/min
1175
1175
1175
Average injection quantity
mm3/st.
28
27
29
Max. variation between cylinders
%
0
-2.5
2.5
Basic
*
Fixing the lever
*
Injection quantity adjustment_02
Adjusting point
D
Rack position
8.5+-0.5
Pump speed
r/min
500
500
500
Average injection quantity
mm3/st.
8
7
9
Max. variation between cylinders
%
0
-15
15
Fixing the rack
*
Test data Ex:
Governor adjustment
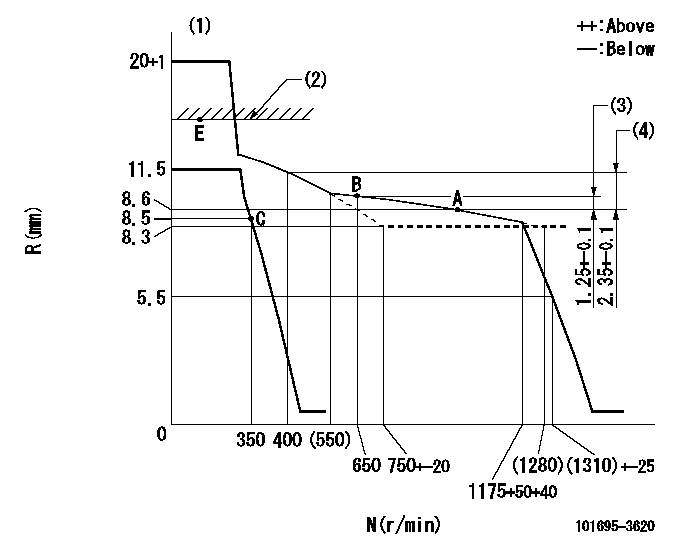
N:Pump speed
R:Rack position (mm)
(1)Notch fixed: K
(2)RACK LIMIT: RAL
(3)Rack difference between N = N1 and N = N2
(4)Rack difference between N = N3 and N = N4
----------
K=20 RAL=15+0.2mm N1=1175r/min N2=650r/min N3=1175r/min N4=400r/min
----------
----------
K=20 RAL=15+0.2mm N1=1175r/min N2=650r/min N3=1175r/min N4=400r/min
----------
Speed control lever angle
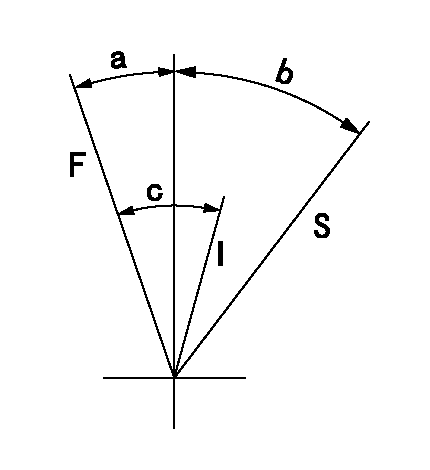
F:Full speed
I:Idle
S:Stop
----------
----------
a=(24deg)+-5deg b=32deg+-3deg c=(27deg)+-5deg
----------
----------
a=(24deg)+-5deg b=32deg+-3deg c=(27deg)+-5deg
Timing setting
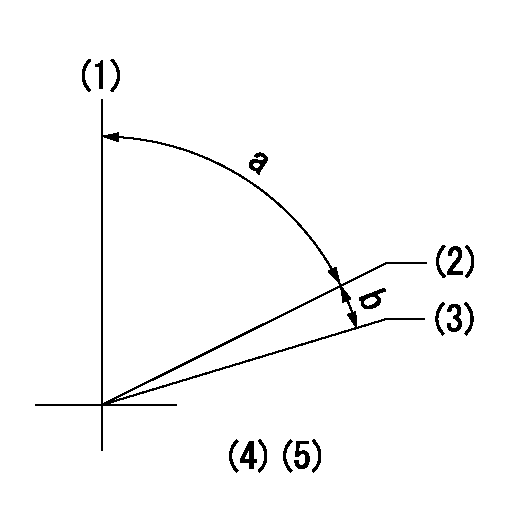
(1)Pump vertical direction
(2)Position of key groove at No 1 cylinder's beginning of injection
(3)Stamp aligning marks on the pump housing flange.
(4)-
----------
----------
a=59deg36min+-3deg b=0deg24min+-30min
----------
----------
a=59deg36min+-3deg b=0deg24min+-30min
Information:
Start By:a. remove cylinder head assemblyb. remove engine balancer group (3114 Engines)c. remove oil pump (3116 Engines)d. remove piston cooling tubes 1. Check the connecting rods and caps for their identification and location in the engine. The connecting rods are to be marked (only by etching) with the number of the cylinder in which they are used. Rods and caps are to be marked on the same side of the rod in relation to the bearing retainer notch.2. Remove rod cap nuts (1) and rod bearing cap (2) from the connecting rod. Remove the lower half of the bearing from the rod bearing cap.
To protect the crankshaft from the threaded portion of the connecting rod bolts, cut short pieces of rubber hose, and install them over the threaded portion of the bolts as shown in Photo C20235P1.
3. Carefully remove the piston and connecting rod from the cylinder block. Remove the upper half of the bearing from the connecting rod.4. Remove the remainder of the pistons and connecting rods as in Steps 1 through 3. The following steps are for the installation of the pistons and connecting rod assemblies. 5. Position the piston ring end gaps 120 degrees apart. Install Tool (A) on the piston as shown.6. Be sure the short pieces of rubber hose are installed on the connecting rod bolts. Install the connecting rod and piston group with the rod forging part number facing to the rear of the engine. The rear of the engine is the flywheel end. Thoroughly lubricate the piston crown, piston skirt and the cylinder bore with clean engine oil just prior to installation of the piston group in the cylinder block.7. With the number one crankshaft throw at bottom center, carefully install the piston and connecting rod assembly in the cylinder block. 8. Put the connecting rod in alignment with the crankshaft. Using a rubber mallet, tap the piston into the cylinder bore until Tool (A) comes off of the piston.9. Before the connecting rod comes in contact with the crankshaft, install the upper half of the rod bearing. Be sure the bearing tab engages with the groove in the connecting rod.10. Apply clean engine oil on the upper rod bearing. Continue tapping the piston down, guiding the connecting rod onto the crankshaft.11. Position the lower half of the rod bearing in the corresponding numbered rod bearing cap. Be sure the bearing tab engages with the groove in the rod bearing cap.13. Put clean engine oil on the lower rod bearing surface. Install the rod bearing cap on the connecting rod with the number on the bearing cap on the same side and same number as on the connecting rod.14. Tighten the connecting rod bolts as follows: a. Put clean engine oil on the bolt threads, and all surfaces that make contact between the bolts and cap.b. Tighten
To protect the crankshaft from the threaded portion of the connecting rod bolts, cut short pieces of rubber hose, and install them over the threaded portion of the bolts as shown in Photo C20235P1.
3. Carefully remove the piston and connecting rod from the cylinder block. Remove the upper half of the bearing from the connecting rod.4. Remove the remainder of the pistons and connecting rods as in Steps 1 through 3. The following steps are for the installation of the pistons and connecting rod assemblies. 5. Position the piston ring end gaps 120 degrees apart. Install Tool (A) on the piston as shown.6. Be sure the short pieces of rubber hose are installed on the connecting rod bolts. Install the connecting rod and piston group with the rod forging part number facing to the rear of the engine. The rear of the engine is the flywheel end. Thoroughly lubricate the piston crown, piston skirt and the cylinder bore with clean engine oil just prior to installation of the piston group in the cylinder block.7. With the number one crankshaft throw at bottom center, carefully install the piston and connecting rod assembly in the cylinder block. 8. Put the connecting rod in alignment with the crankshaft. Using a rubber mallet, tap the piston into the cylinder bore until Tool (A) comes off of the piston.9. Before the connecting rod comes in contact with the crankshaft, install the upper half of the rod bearing. Be sure the bearing tab engages with the groove in the connecting rod.10. Apply clean engine oil on the upper rod bearing. Continue tapping the piston down, guiding the connecting rod onto the crankshaft.11. Position the lower half of the rod bearing in the corresponding numbered rod bearing cap. Be sure the bearing tab engages with the groove in the rod bearing cap.13. Put clean engine oil on the lower rod bearing surface. Install the rod bearing cap on the connecting rod with the number on the bearing cap on the same side and same number as on the connecting rod.14. Tighten the connecting rod bolts as follows: a. Put clean engine oil on the bolt threads, and all surfaces that make contact between the bolts and cap.b. Tighten