Information injection-pump assembly
BOSCH
9 400 616 060
9400616060
ZEXEL
101692-3980
1016923980
KOMATSU
6207711281
6207711281
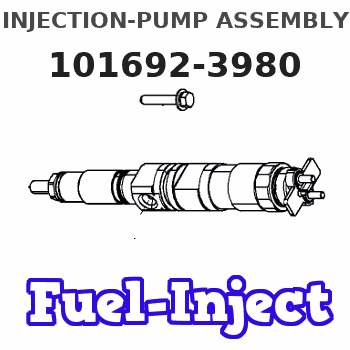
Rating:
Service parts 101692-3980 INJECTION-PUMP ASSEMBLY:
1.
_
5.
AUTOM. ADVANCE MECHANIS
6.
COUPLING PLATE
7.
COUPLING PLATE
8.
_
9.
_
11.
Nozzle and Holder
6207-11-3102
12.
Open Pre:MPa(Kqf/cm2)
19.6{200}
15.
NOZZLE SET
Cross reference number
BOSCH
9 400 616 060
9400616060
ZEXEL
101692-3980
1016923980
KOMATSU
6207711281
6207711281
Zexel num
Bosch num
Firm num
Name
101692-3980
9 400 616 060
6207711281 KOMATSU
INJECTION-PUMP ASSEMBLY
S6D95L K 14BE INJECTION PUMP ASSY PE6A PE
S6D95L K 14BE INJECTION PUMP ASSY PE6A PE
Calibration Data:
Adjustment conditions
Test oil
1404 Test oil ISO4113 or {SAEJ967d}
1404 Test oil ISO4113 or {SAEJ967d}
Test oil temperature
degC
40
40
45
Nozzle and nozzle holder
105780-8140
Bosch type code
EF8511/9A
Nozzle
105780-0000
Bosch type code
DN12SD12T
Nozzle holder
105780-2080
Bosch type code
EF8511/9
Opening pressure
MPa
17.2
Opening pressure
kgf/cm2
175
Injection pipe
Outer diameter - inner diameter - length (mm) mm 6-2-600
Outer diameter - inner diameter - length (mm) mm 6-2-600
Tester oil delivery pressure
kPa
157
157
157
Tester oil delivery pressure
kgf/cm2
1.6
1.6
1.6
Direction of rotation (viewed from drive side)
Right R
Right R
Injection timing adjustment
Direction of rotation (viewed from drive side)
Right R
Right R
Injection order
1-5-3-6-
2-4
Pre-stroke
mm
3.6
3.55
3.65
Beginning of injection position
Drive side NO.1
Drive side NO.1
Difference between angles 1
Cal 1-5 deg. 60 59.5 60.5
Cal 1-5 deg. 60 59.5 60.5
Difference between angles 2
Cal 1-3 deg. 120 119.5 120.5
Cal 1-3 deg. 120 119.5 120.5
Difference between angles 3
Cal 1-6 deg. 180 179.5 180.5
Cal 1-6 deg. 180 179.5 180.5
Difference between angles 4
Cyl.1-2 deg. 240 239.5 240.5
Cyl.1-2 deg. 240 239.5 240.5
Difference between angles 5
Cal 1-4 deg. 300 299.5 300.5
Cal 1-4 deg. 300 299.5 300.5
Injection quantity adjustment
Adjusting point
A
Rack position
10.8
Pump speed
r/min
1100
1100
1100
Average injection quantity
mm3/st.
42.5
41.5
43.5
Max. variation between cylinders
%
0
-2.5
2.5
Basic
*
Fixing the lever
*
Injection quantity adjustment_02
Adjusting point
-
Rack position
10.4+-0.
5
Pump speed
r/min
425
425
425
Average injection quantity
mm3/st.
12.5
11.5
13.5
Max. variation between cylinders
%
0
-15
15
Fixing the rack
*
Remarks
Adjust only variation between cylinders; adjust governor according to governor specifications.
Adjust only variation between cylinders; adjust governor according to governor specifications.
Test data Ex:
Governor adjustment
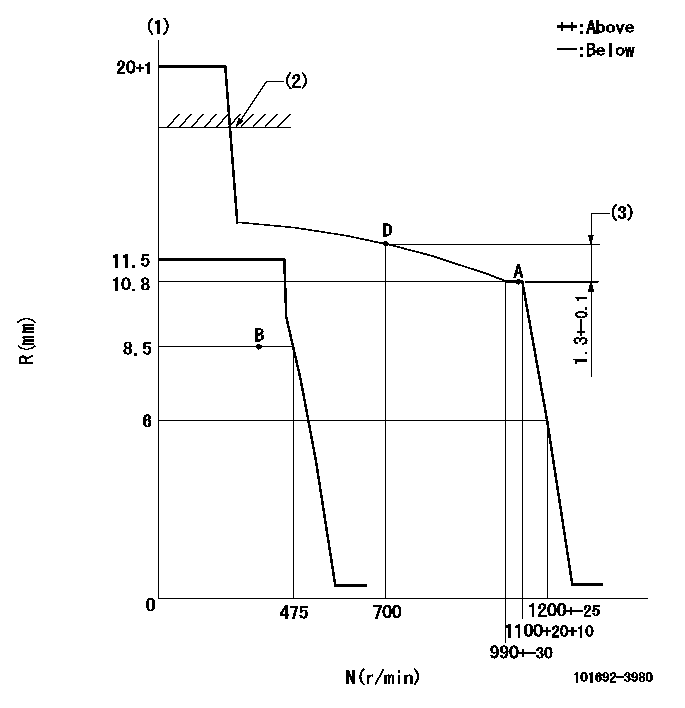
N:Pump speed
R:Rack position (mm)
(1)Target notch: K
(2)RACK LIMIT: RAL
(3)Rack difference between N = N1 and N = N2
----------
K=5 RAL=15+0.2mm N1=1100r/min N2=700r/min
----------
----------
K=5 RAL=15+0.2mm N1=1100r/min N2=700r/min
----------
Speed control lever angle
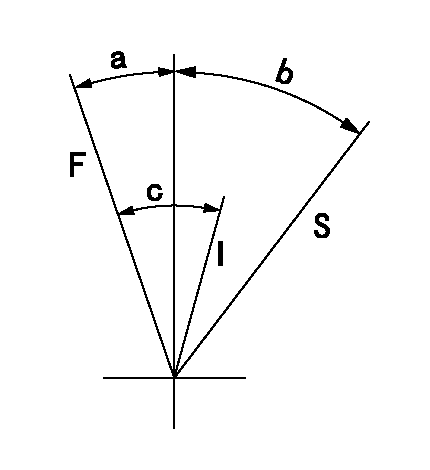
F:Full speed
I:Idle
S:Stop
----------
----------
a=9deg+-5deg b=32deg+-3deg c=33deg+-5deg
----------
----------
a=9deg+-5deg b=32deg+-3deg c=33deg+-5deg
Timing setting
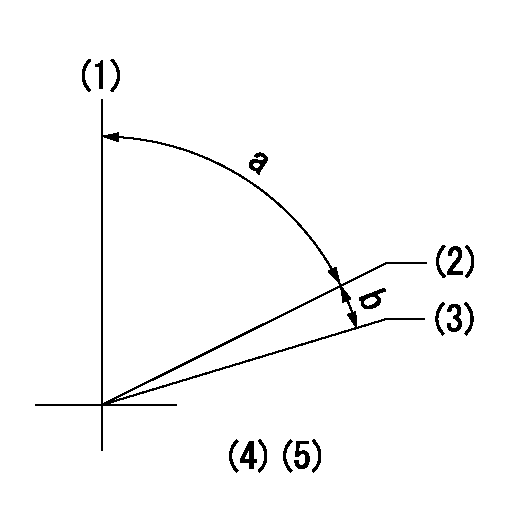
(1)Pump vertical direction
(2)Position of key groove at No 1 cylinder's beginning of injection
(3)Stamp aligning marks on the pump housing flange.
(4)-
(5)-
----------
----------
a=59deg36min+-3deg b=0deg24min+-30min
----------
----------
a=59deg36min+-3deg b=0deg24min+-30min
Information:
Engine Mounts
Inspect
Inspect the engine mounts for deterioration and proper bolt torque. Engine vibration may be caused by improper engine mounting and/or engine mount deterioration. Any engine mount showing deterioration should be replaced. Refer to the Torque Specifications section of this publication for recommended bolt torque values. See the Marine Engine Application and Installation Guide for more information.Crankshaft Vibration Damper
Inspect
Damage to, or failure of, the crankshaft vibration damper will increase torsional vibrations and result in damage to the crankshaft and other engine components. A deteriorating damper will cause excessive gear train noise at variable points in the speed range.The damper is mounted to the crankshaft, located behind the belt guard on the front of the engine.Removal and Installation
Refer to the Service Manual for the damper removal procedure and for the damper installation procedure.Visconic Damper
The visconic damper has a weight, located inside a fluid filled case. The weight moves in the case to limit torsional vibration. Inspect the damper for evidence of dents, cracks or leaks of the fluid.Replace the damper if the damper is dented, cracked, or leaking. Refer to the Service Manual or contact your Caterpillar dealer for damper replacement.Valve Lash
Check/Adjust
Initial valve lash adjustment on new, rebuilt or remanufactured engines is recommended at the first scheduled oil change interval due to initial wear and seating of valve train components.Subsequent adjustments should be made at Every 3000 Hour interval.This maintenance is recommended by Caterpillar as part of a lubrication and preventive maintenance schedule to provide maximum engine life.
Only qualified service personnel should perform this maintenance. Refer to the Service Manual or your Caterpillar dealer for the complete valve lash adjustment procedure.
Be sure the engine cannot be started while this maintenance is being performed. To prevent possible injury, do not use the starting motor to turn the flywheel.Hot engine components can cause burns. Allow additional time for the engine to cool before measuring/adjusting valve lash clearance.
Operation of Caterpillar engines with improper valve adjustments will reduce engine efficiency. This reduced efficiency could result in excessive fuel usage and/or shortened engine component life.
Valve Rotators
When inspecting the valve rotators, protective glasses or face shield and protective clothing must be worn, to prevent being burned by hot oil or spray.
A valve rotator which does not operate properly will accelerate valve face wear and valve seat wear and shorten valve life. If a damaged rotator is not replaced, valve face guttering could result and cause pieces of the valve to fall into the cylinder. This can cause piston and cylinder head damage.
After setting the valve lash and before installing the valve covers:1. Start the engine. Follow the engine starting procedure in this manual. Operate the engine at low idle.2. Observe the top surface of each valve rotator. Each valve rotator should turn slightly each time the valve closes.If a valve fails to rotate, contact your Caterpillar dealer.Fuel Ratio Control, Set Point, and Low Idle
Check/Adjust
The fuel ratio control limits the amount of fuel to the cylinders during acceleration. This affects the amount of exhaust smoke. The
Inspect
Inspect the engine mounts for deterioration and proper bolt torque. Engine vibration may be caused by improper engine mounting and/or engine mount deterioration. Any engine mount showing deterioration should be replaced. Refer to the Torque Specifications section of this publication for recommended bolt torque values. See the Marine Engine Application and Installation Guide for more information.Crankshaft Vibration Damper
Inspect
Damage to, or failure of, the crankshaft vibration damper will increase torsional vibrations and result in damage to the crankshaft and other engine components. A deteriorating damper will cause excessive gear train noise at variable points in the speed range.The damper is mounted to the crankshaft, located behind the belt guard on the front of the engine.Removal and Installation
Refer to the Service Manual for the damper removal procedure and for the damper installation procedure.Visconic Damper
The visconic damper has a weight, located inside a fluid filled case. The weight moves in the case to limit torsional vibration. Inspect the damper for evidence of dents, cracks or leaks of the fluid.Replace the damper if the damper is dented, cracked, or leaking. Refer to the Service Manual or contact your Caterpillar dealer for damper replacement.Valve Lash
Check/Adjust
Initial valve lash adjustment on new, rebuilt or remanufactured engines is recommended at the first scheduled oil change interval due to initial wear and seating of valve train components.Subsequent adjustments should be made at Every 3000 Hour interval.This maintenance is recommended by Caterpillar as part of a lubrication and preventive maintenance schedule to provide maximum engine life.
Only qualified service personnel should perform this maintenance. Refer to the Service Manual or your Caterpillar dealer for the complete valve lash adjustment procedure.
Be sure the engine cannot be started while this maintenance is being performed. To prevent possible injury, do not use the starting motor to turn the flywheel.Hot engine components can cause burns. Allow additional time for the engine to cool before measuring/adjusting valve lash clearance.
Operation of Caterpillar engines with improper valve adjustments will reduce engine efficiency. This reduced efficiency could result in excessive fuel usage and/or shortened engine component life.
Valve Rotators
When inspecting the valve rotators, protective glasses or face shield and protective clothing must be worn, to prevent being burned by hot oil or spray.
A valve rotator which does not operate properly will accelerate valve face wear and valve seat wear and shorten valve life. If a damaged rotator is not replaced, valve face guttering could result and cause pieces of the valve to fall into the cylinder. This can cause piston and cylinder head damage.
After setting the valve lash and before installing the valve covers:1. Start the engine. Follow the engine starting procedure in this manual. Operate the engine at low idle.2. Observe the top surface of each valve rotator. Each valve rotator should turn slightly each time the valve closes.If a valve fails to rotate, contact your Caterpillar dealer.Fuel Ratio Control, Set Point, and Low Idle
Check/Adjust
The fuel ratio control limits the amount of fuel to the cylinders during acceleration. This affects the amount of exhaust smoke. The
Have questions with 101692-3980?
Group cross 101692-3980 ZEXEL
Komatsu
Komatsu
101692-3980
9 400 616 060
6207711281
INJECTION-PUMP ASSEMBLY
S6D95L
S6D95L