Information injection-pump assembly
BOSCH
9 400 616 039
9400616039
ZEXEL
101692-3541
1016923541
KOMATSU
6206711370
6206711370
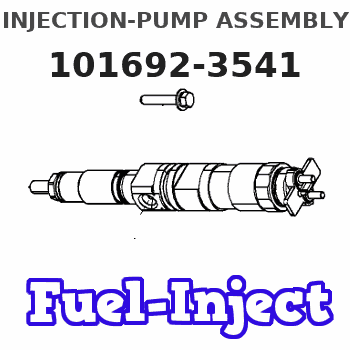
Rating:
Service parts 101692-3541 INJECTION-PUMP ASSEMBLY:
1.
_
5.
AUTOM. ADVANCE MECHANIS
6.
COUPLING PLATE
7.
COUPLING PLATE
8.
_
9.
_
11.
Nozzle and Holder
6207-11-3100
12.
Open Pre:MPa(Kqf/cm2)
19.6{200}
15.
NOZZLE SET
Cross reference number
BOSCH
9 400 616 039
9400616039
ZEXEL
101692-3541
1016923541
KOMATSU
6206711370
6206711370
Zexel num
Bosch num
Firm num
Name
9 400 616 039
6206711370 KOMATSU
INJECTION-PUMP ASSEMBLY
6D95L K 14BE INJECTION PUMP ASSY PE6A PE
6D95L K 14BE INJECTION PUMP ASSY PE6A PE
Calibration Data:
Adjustment conditions
Test oil
1404 Test oil ISO4113 or {SAEJ967d}
1404 Test oil ISO4113 or {SAEJ967d}
Test oil temperature
degC
40
40
45
Nozzle and nozzle holder
105780-8140
Bosch type code
EF8511/9A
Nozzle
105780-0000
Bosch type code
DN12SD12T
Nozzle holder
105780-2080
Bosch type code
EF8511/9
Opening pressure
MPa
17.2
Opening pressure
kgf/cm2
175
Injection pipe
Outer diameter - inner diameter - length (mm) mm 6-2-600
Outer diameter - inner diameter - length (mm) mm 6-2-600
Overflow valve opening pressure
kPa
157
123
191
Overflow valve opening pressure
kgf/cm2
1.6
1.25
1.95
Tester oil delivery pressure
kPa
157
157
157
Tester oil delivery pressure
kgf/cm2
1.6
1.6
1.6
Direction of rotation (viewed from drive side)
Right R
Right R
Injection timing adjustment
Direction of rotation (viewed from drive side)
Right R
Right R
Injection order
1-5-3-6-
2-4
Pre-stroke
mm
3.6
3.55
3.65
Rack position
Point A R=A
Point A R=A
Beginning of injection position
Drive side NO.1
Drive side NO.1
Difference between angles 1
Cal 1-5 deg. 60 59.5 60.5
Cal 1-5 deg. 60 59.5 60.5
Difference between angles 2
Cal 1-3 deg. 120 119.5 120.5
Cal 1-3 deg. 120 119.5 120.5
Difference between angles 3
Cal 1-6 deg. 180 179.5 180.5
Cal 1-6 deg. 180 179.5 180.5
Difference between angles 4
Cyl.1-2 deg. 240 239.5 240.5
Cyl.1-2 deg. 240 239.5 240.5
Difference between angles 5
Cal 1-4 deg. 300 299.5 300.5
Cal 1-4 deg. 300 299.5 300.5
Injection quantity adjustment
Adjusting point
A
Rack position
10
Pump speed
r/min
1175
1175
1175
Average injection quantity
mm3/st.
35.6
34.6
36.6
Max. variation between cylinders
%
0
-2.5
2.5
Basic
*
Fixing the lever
*
Injection quantity adjustment_02
Adjusting point
-
Rack position
10.3+-0.
5
Pump speed
r/min
350
350
350
Average injection quantity
mm3/st.
10.5
9.5
11.5
Max. variation between cylinders
%
0
-15
15
Fixing the rack
*
Remarks
Adjust only variation between cylinders; adjust governor according to governor specifications.
Adjust only variation between cylinders; adjust governor according to governor specifications.
Test data Ex:
Governor adjustment
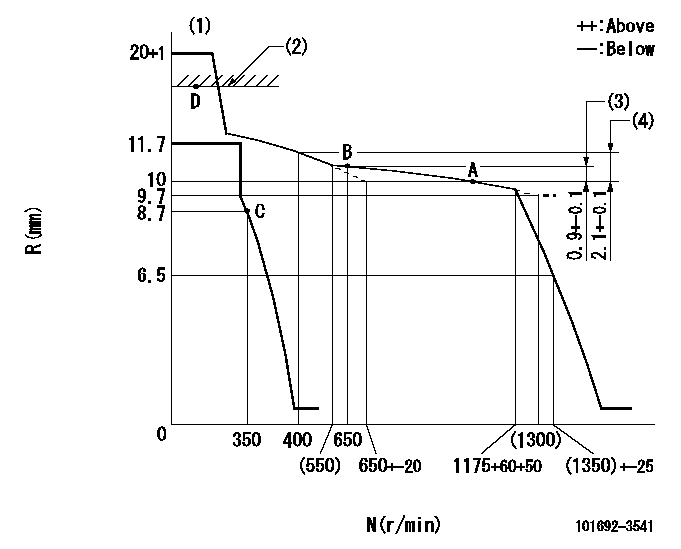
N:Pump speed
R:Rack position (mm)
(1)Notch fixed: K
(2)RACK CAP: R1
(3)Rack difference between N = N1 and N = N2
(4)Rack difference between N = N3 and N = N4
----------
K=20 R1=(17.5)mm N1=1175r/min N2=650r/min N3=1175r/min N4=400r/min
----------
----------
K=20 R1=(17.5)mm N1=1175r/min N2=650r/min N3=1175r/min N4=400r/min
----------
Speed control lever angle
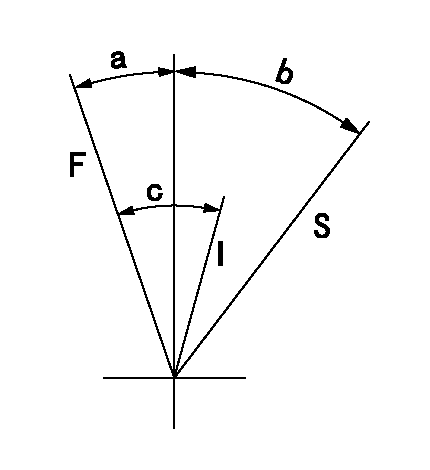
F:Full speed
I:Idle
S:Stop
----------
----------
a=(27deg)+-5deg b=32deg+-3deg c=(28deg)+-5deg
----------
----------
a=(27deg)+-5deg b=32deg+-3deg c=(28deg)+-5deg
Timing setting
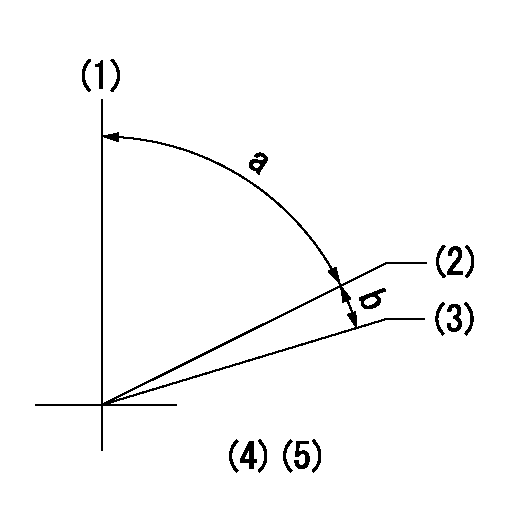
(1)Pump vertical direction
(2)Position of key groove at No 1 cylinder's beginning of injection
(3)Stamp aligning marks on the pump housing flange.
(4)-
(5)-
----------
----------
a=59deg36min+-3deg b=0deg24min+-30min
----------
----------
a=59deg36min+-3deg b=0deg24min+-30min
Information:
Crankshaft Vibration Damper
Inspect/Check
Damage to, or failure of, the damper will increase torsional vibrations and result in damage to the crankshaft and other engine components. A deteriorating vibration damper will cause excessive gear train noise at variable points in the speed range.Visconic Damper (If Equipped)
The vibration damper weight is located inside a fluid filled case. The weight moves in the case to limit torsional vibration. Inspect the dampers for evidence of dents, cracks or leaks of the fluid.Rubber Damper (If Equipped)
The vibration damper can have a visual wobble (movement to the front and rear when in rotation) on the outer ring. This does not mean a replacement is necessary since some wobble of the outer ring is normal. To see if the amount of wobble is acceptable, or replacement is necessary, check the damper with the procedure in the Testing and Adjusting section of the Service Manual.The vibration damper has marks on the hub and ring. These marks will indicate the condition of the vibration damper. If the marks are not in alignment, the rubber seal between the ring and the hub has separated from the ring and/or hub. If the marks are not in alignment, install a new vibration damper. Refer to the Service Manual for the necessary replacement procedure.Air Compressor
Inspect/Check
Do not disconnect the air line from the air compressor governor without purging the air brake and auxiliary air systems.Failure to purge the air brake and auxiliary air systems before removing the air compressor could cause personal injury.
Inspect the air compressor as instructed by the OEM truck manufacturers' instructions or for more information on how to check your air compressor, refer to the Service Manual for this engine.If you decide to inspect your air compressor, be sure to observe the following actions. Visually check for fluid leaks and listen for air leaks. Release the air pressure in the air tank until the air pressure is zero. Visually check for fluid leaks. Remove discharge fittings and inspect compressor discharge port and discharge line for excessive carbon deposits. The discharge line must be cleaned or replaced and the compressor checked more thoroughly if there is excessive carbon build-up in either the discharge line or compressor discharge port.For more information on how to check your air compressor, refer to the OEM truck manufacturer's instructions or engine Service Manual.Engine Valve Lash
The procedures for engine valve lash should be performed according to the information in the Service Manual.
Check/Adjust
Be sure the engine cannot be started while this maintenance is being performed. To prevent possible injury, do not use the starting motor to turn the flywheel.Hot engine components can cause burns. Allow additional time for the engine to cool before measuring/adjusting valve lash.The 3176 uses high voltage to the unit injectors. Disconnect injector enable circuit connector J5/P5 to prevent personal injury. Do not come in contact with the injector terminals while the engine is running.
Adjust the valve lash to the setting given in the chart above.Refer to the Service Manual or your Caterpillar dealer for
Inspect/Check
Damage to, or failure of, the damper will increase torsional vibrations and result in damage to the crankshaft and other engine components. A deteriorating vibration damper will cause excessive gear train noise at variable points in the speed range.Visconic Damper (If Equipped)
The vibration damper weight is located inside a fluid filled case. The weight moves in the case to limit torsional vibration. Inspect the dampers for evidence of dents, cracks or leaks of the fluid.Rubber Damper (If Equipped)
The vibration damper can have a visual wobble (movement to the front and rear when in rotation) on the outer ring. This does not mean a replacement is necessary since some wobble of the outer ring is normal. To see if the amount of wobble is acceptable, or replacement is necessary, check the damper with the procedure in the Testing and Adjusting section of the Service Manual.The vibration damper has marks on the hub and ring. These marks will indicate the condition of the vibration damper. If the marks are not in alignment, the rubber seal between the ring and the hub has separated from the ring and/or hub. If the marks are not in alignment, install a new vibration damper. Refer to the Service Manual for the necessary replacement procedure.Air Compressor
Inspect/Check
Do not disconnect the air line from the air compressor governor without purging the air brake and auxiliary air systems.Failure to purge the air brake and auxiliary air systems before removing the air compressor could cause personal injury.
Inspect the air compressor as instructed by the OEM truck manufacturers' instructions or for more information on how to check your air compressor, refer to the Service Manual for this engine.If you decide to inspect your air compressor, be sure to observe the following actions. Visually check for fluid leaks and listen for air leaks. Release the air pressure in the air tank until the air pressure is zero. Visually check for fluid leaks. Remove discharge fittings and inspect compressor discharge port and discharge line for excessive carbon deposits. The discharge line must be cleaned or replaced and the compressor checked more thoroughly if there is excessive carbon build-up in either the discharge line or compressor discharge port.For more information on how to check your air compressor, refer to the OEM truck manufacturer's instructions or engine Service Manual.Engine Valve Lash
The procedures for engine valve lash should be performed according to the information in the Service Manual.
Check/Adjust
Be sure the engine cannot be started while this maintenance is being performed. To prevent possible injury, do not use the starting motor to turn the flywheel.Hot engine components can cause burns. Allow additional time for the engine to cool before measuring/adjusting valve lash.The 3176 uses high voltage to the unit injectors. Disconnect injector enable circuit connector J5/P5 to prevent personal injury. Do not come in contact with the injector terminals while the engine is running.
Adjust the valve lash to the setting given in the chart above.Refer to the Service Manual or your Caterpillar dealer for