Information injection-pump assembly
BOSCH
9 400 616 031
9400616031
ZEXEL
101692-3302
1016923302
KOMATSU
6207711280
6207711280
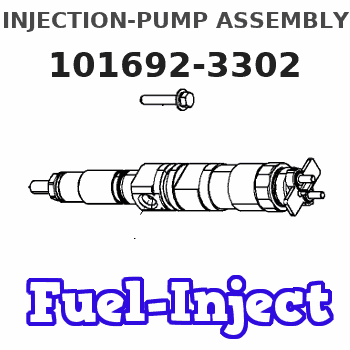
Rating:
Service parts 101692-3302 INJECTION-PUMP ASSEMBLY:
1.
_
5.
AUTOM. ADVANCE MECHANIS
6.
COUPLING PLATE
7.
COUPLING PLATE
8.
_
9.
_
11.
Nozzle and Holder
12.
Open Pre:MPa(Kqf/cm2)
19.6(200)
15.
NOZZLE SET
Cross reference number
BOSCH
9 400 616 031
9400616031
ZEXEL
101692-3302
1016923302
KOMATSU
6207711280
6207711280
Zexel num
Bosch num
Firm num
Name
Calibration Data:
Adjustment conditions
Test oil
1404 Test oil ISO4113 or {SAEJ967d}
1404 Test oil ISO4113 or {SAEJ967d}
Test oil temperature
degC
40
40
45
Nozzle and nozzle holder
105780-8140
Bosch type code
EF8511/9A
Nozzle
105780-0000
Bosch type code
DN12SD12T
Nozzle holder
105780-2080
Bosch type code
EF8511/9
Opening pressure
MPa
17.2
Opening pressure
kgf/cm2
175
Injection pipe
Outer diameter - inner diameter - length (mm) mm 6-2-600
Outer diameter - inner diameter - length (mm) mm 6-2-600
Tester oil delivery pressure
kPa
157
157
157
Tester oil delivery pressure
kgf/cm2
1.6
1.6
1.6
Direction of rotation (viewed from drive side)
Right R
Right R
Injection timing adjustment
Direction of rotation (viewed from drive side)
Right R
Right R
Injection order
1-5-3-6-
2-4
Pre-stroke
mm
3.6
3.55
3.65
Rack position
Point A R=A
Point A R=A
Beginning of injection position
Drive side NO.1
Drive side NO.1
Difference between angles 1
Cal 1-5 deg. 60 59.5 60.5
Cal 1-5 deg. 60 59.5 60.5
Difference between angles 2
Cal 1-3 deg. 120 119.5 120.5
Cal 1-3 deg. 120 119.5 120.5
Difference between angles 3
Cal 1-6 deg. 180 179.5 180.5
Cal 1-6 deg. 180 179.5 180.5
Difference between angles 4
Cyl.1-2 deg. 240 239.5 240.5
Cyl.1-2 deg. 240 239.5 240.5
Difference between angles 5
Cal 1-4 deg. 300 299.5 300.5
Cal 1-4 deg. 300 299.5 300.5
Injection quantity adjustment
Adjusting point
A
Rack position
10.8
Pump speed
r/min
1100
1100
1100
Average injection quantity
mm3/st.
42.5
41.5
43.5
Max. variation between cylinders
%
0
-2.5
2.5
Basic
*
Fixing the lever
*
Injection quantity adjustment_02
Adjusting point
-
Rack position
10.4+-0.
5
Pump speed
r/min
425
425
425
Average injection quantity
mm3/st.
12.5
11.5
13.5
Max. variation between cylinders
%
0
-15
15
Fixing the rack
*
Remarks
Adjust only variation between cylinders; adjust governor according to governor specifications.
Adjust only variation between cylinders; adjust governor according to governor specifications.
Test data Ex:
Governor adjustment
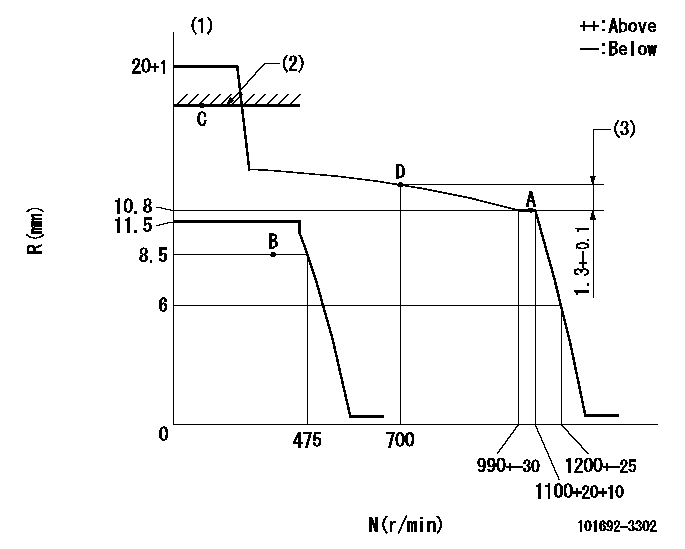
N:Pump speed
R:Rack position (mm)
(1)Target notch: K
(2)RACK CAP: R1
(3)Rack difference between N = N1 and N = N2
----------
K=5 R1=(17.5)mm N1=1100r/min N2=700r/min
----------
----------
K=5 R1=(17.5)mm N1=1100r/min N2=700r/min
----------
Speed control lever angle
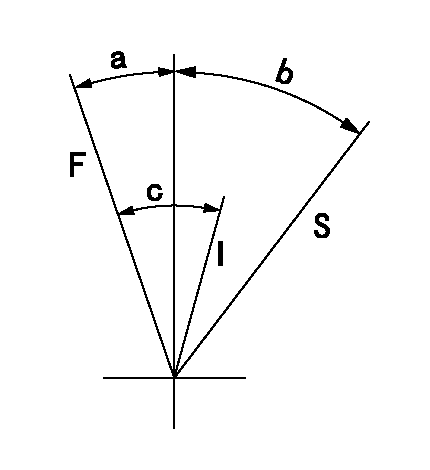
F:Full speed
I:Idle
S:Stop
----------
----------
a=9deg+-5deg b=32deg+-3deg c=33deg+-5deg
----------
----------
a=9deg+-5deg b=32deg+-3deg c=33deg+-5deg
Timing setting
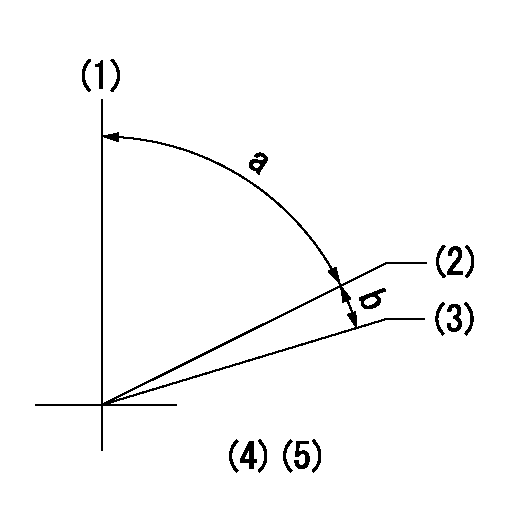
(1)Pump vertical direction
(2)Position of key groove at No 1 cylinder's beginning of injection
(3)Stamp aligning marks on the pump housing flange.
(4)-
(5)-
----------
----------
a=59deg36min+-3deg b=0deg24min+-30min
----------
----------
a=59deg36min+-3deg b=0deg24min+-30min
Information:
Fuel line clamps should not be over torqued. Over torqueing causes the clamps to butterfly, which results in low clamping force and fuel line vibration and eventual failure.
Tighten fuel line clamps as required using 6V4980 Torque Screwdriver Tool Group. The standard torque for these fasteners (#10 screw) is 20 lb inch (2.26 N m).* Inspect engine wiring and electronic wiring harnesses for loose connections and worn or frayed wires. Inspect:
* Air intake system hoses and elbows for cracks and loose clamps.All guards must be in place.Check condition of batteries and the level of electrolyte, unless equipped with a maintenance free battery.Refer to OEM truck owner manual or manufacturers' recommendations for battery maintenance.Engine Crankcase
Make sure you read and understand the information in the Lubricant Specifications section of this manual before you proceed with maintenance of the crankcase lube oil system.
Check Oil Level
The vehicle must be parked on a level surface to perform this maintenance procedure.
1. Check the oil level with the engine stopped.Ensure that the engine when the oil level is not above the FULL RANGE zone on the dipstick. 2. Maintain the oil level between the ADD and FULL marks in the FULL RANGE zone on the ENGINE STOPPED side of the dipstick. Do not fill the crankcase above the FULL RANGE zone. Operating your engine when the oil level is above the FULL RANGE zone could cause your crankshaft to dip into the oil. If this happens, the air bubbles created from the crankshaft dipping into the oil will reduce the lubricating characteristics of your oil and also result in the loss of power.If the dipstick does not have a FULL mark in the FULL RANGE zone, refer to Dipstick Calibration in this manual or consult your Caterpillar dealer before changing oil and operating the engine. 3. Remove the oil filler cap and add oil if necessary. See Refill Capacities and Lubricant Specifications for the size of your engine crankcase and recommended oil to use. Remote mounted filter or auxiliary filters require additional oil than what the Refill Capacities chart states. For all information pertaining to auxiliary oil filters, refer to the truck OEM or filter manufacturer's instructions.Cooling System
Make sure you read and understand the information in the Cooling System Specifications section of this manual before you proceed with maintenance of the cooling system.
Check Coolant Level
1. Check the coolant level with the engine stopped and cool.2. Remove the filler cap slowly to relieve any pressure.3. Maintain the coolant level within 1/2 inch (13 mm) below the bottom of the fill pipe or to the proper level on the sight glass, if equipped.4. Inspect the filler cap. Replace the cap if gaskets are damaged. Install the filler cap.5. Inspect and clean the radiator fins.Air Cleaner Indicator (If Equipped)
Check Air Cleaner Service Indicator
Typical air cleaner indicator shown.Your engine may be equipped with a different indicator.A service indicator (if equipped) may be mounted on your dashboard or in the engine compartment. A colored piston showing in the window indicates the