Information injection-pump assembly
BOSCH
9 400 616 001
9400616001
ZEXEL
101691-6271
1016916271
MITSUBISHI
ME088795
me088795
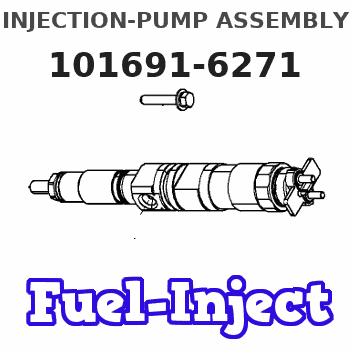
Rating:
Service parts 101691-6271 INJECTION-PUMP ASSEMBLY:
1.
_
6.
COUPLING PLATE
7.
COUPLING PLATE
8.
_
9.
_
11.
Nozzle and Holder
ME017801
12.
Open Pre:MPa(Kqf/cm2)
21.6{220}
15.
NOZZLE SET
Include in #1:
101691-6271
as INJECTION-PUMP ASSEMBLY
Cross reference number
BOSCH
9 400 616 001
9400616001
ZEXEL
101691-6271
1016916271
MITSUBISHI
ME088795
me088795
Zexel num
Bosch num
Firm num
Name
Calibration Data:
Adjustment conditions
Test oil
1404 Test oil ISO4113 or {SAEJ967d}
1404 Test oil ISO4113 or {SAEJ967d}
Test oil temperature
degC
40
40
45
Nozzle and nozzle holder
105780-8140
Bosch type code
EF8511/9A
Nozzle
105780-0000
Bosch type code
DN12SD12T
Nozzle holder
105780-2080
Bosch type code
EF8511/9
Opening pressure
MPa
17.2
Opening pressure
kgf/cm2
175
Injection pipe
Outer diameter - inner diameter - length (mm) mm 6-2-600
Outer diameter - inner diameter - length (mm) mm 6-2-600
Overflow valve
131424-5520
Overflow valve opening pressure
kPa
255
221
289
Overflow valve opening pressure
kgf/cm2
2.6
2.25
2.95
Tester oil delivery pressure
kPa
157
157
157
Tester oil delivery pressure
kgf/cm2
1.6
1.6
1.6
Direction of rotation (viewed from drive side)
Right R
Right R
Injection timing adjustment
Direction of rotation (viewed from drive side)
Right R
Right R
Injection order
1-5-3-6-
2-4
Pre-stroke
mm
3.5
3.45
3.55
Beginning of injection position
Drive side NO.1
Drive side NO.1
Difference between angles 1
Cal 1-5 deg. 60 59.5 60.5
Cal 1-5 deg. 60 59.5 60.5
Difference between angles 2
Cal 1-3 deg. 120 119.5 120.5
Cal 1-3 deg. 120 119.5 120.5
Difference between angles 3
Cal 1-6 deg. 180 179.5 180.5
Cal 1-6 deg. 180 179.5 180.5
Difference between angles 4
Cyl.1-2 deg. 240 239.5 240.5
Cyl.1-2 deg. 240 239.5 240.5
Difference between angles 5
Cal 1-4 deg. 300 299.5 300.5
Cal 1-4 deg. 300 299.5 300.5
Injection quantity adjustment
Adjusting point
A
Rack position
10.3
Pump speed
r/min
850
850
850
Average injection quantity
mm3/st.
72
71
73
Max. variation between cylinders
%
0
-2.5
2.5
Basic
*
Fixing the lever
*
Injection quantity adjustment_02
Adjusting point
B
Rack position
6.9+-0.5
Pump speed
r/min
425
425
425
Average injection quantity
mm3/st.
7.5
6.2
8.8
Max. variation between cylinders
%
0
-14
14
Fixing the rack
*
Injection quantity adjustment_03
Adjusting point
D
Rack position
-
Pump speed
r/min
100
100
100
Average injection quantity
mm3/st.
69
69
74
Fixing the lever
*
Rack limit
*
Timer adjustment
Pump speed
r/min
1100++
Advance angle
deg.
0
0
0
Remarks
Do not advance until starting N = 1100.
Do not advance until starting N = 1100.
Timer adjustment_02
Pump speed
r/min
1100
Advance angle
deg.
0.5
Timer adjustment_03
Pump speed
r/min
-
Advance angle
deg.
3
3
3
Remarks
Measure the actual speed, stop
Measure the actual speed, stop
Test data Ex:
Governor adjustment
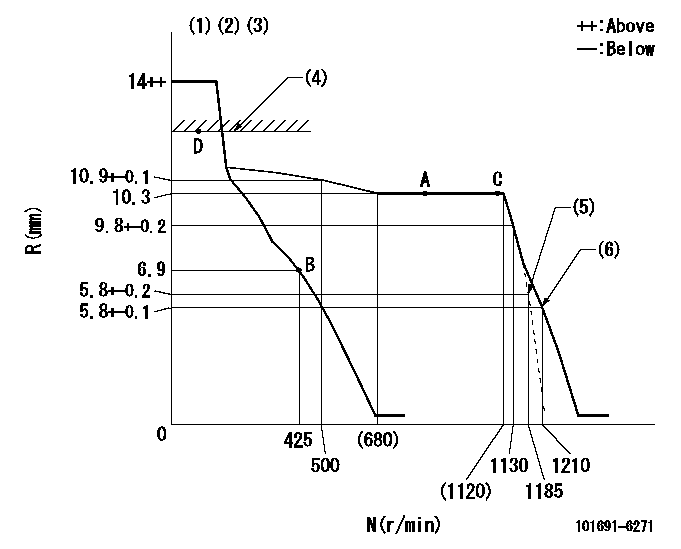
N:Pump speed
R:Rack position (mm)
(1)Target notch: K
(2)Tolerance for racks not indicated: +-0.05mm.
(3)Supplied with torque spring not set.
(4)RACK LIMIT
(5)Main spring setting
(6)Set idle sub-spring
----------
K=10
----------
----------
K=10
----------
Speed control lever angle
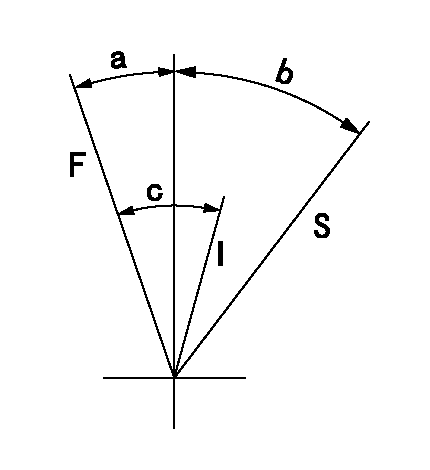
F:Full speed
I:Idle
S:Stop
----------
----------
a=9deg+-5deg b=35deg+-3deg c=24deg+-5deg
----------
----------
a=9deg+-5deg b=35deg+-3deg c=24deg+-5deg
Stop lever angle

N:Pump normal
S:Stop the pump.
----------
----------
a=26.5deg+-5deg b=53deg+-5deg
----------
----------
a=26.5deg+-5deg b=53deg+-5deg
Timing setting

(1)Pump vertical direction
(2)Position of gear mark '3' at No 1 cylinder's beginning of injection
(3)B.T.D.C.: aa
(4)-
----------
aa=14deg
----------
a=(130deg)
----------
aa=14deg
----------
a=(130deg)
Information:
Keep all parts clean from contaminants. Contaminants put into the system may cause rapid wear and shortened component life.
1. Bend the lock tab and remove bolt (1).
The oil pump idler gear (3) can fall off the pump when the pump is removed. Injury can be the result. To prevent injury, always hold idler gear on the pump when the pump is removed.
2. Bend the two tabs on locks (4) on the left hand side of the engine. Remove the four bolts (2) and (5) and remove the oil pump and suction bell as a unit. Be sure the idler gear (3) is engaged with the crankshaft gear and tabs on locks (4) on bolts (5) are not next to the oil pan gasket surface when bolts (2) and (5) are tightened. Install in reverse order.End By:a. install oil panDisassemble Oil Pump
Start By:a. remove oil pump
Keep all parts clean from contaminants. Contaminants put into the system may cause rapid wear and shortened component life.
1. Remove idler gear (2). Remove the bearing from the idler gear with tooling (B).2. Remove suction bell (1) and the bolt and the washer from the oil pump drive gear. 3. Remove the drive gear from the shaft with tooling (A).4. Remove the key from the pump shaft and bolts (3). 5. Remove body (8), two gears (7), the keys and spacer (4).6. Remove two shafts (5) and the gears.7. Remove bolts (6), the cover and the pressure relief valve. 8. Remove the bearings from the oil pump body assembly and the scavenge pump body assembly with tooling (B).Assemble Oil Pump
1. Install the bearings in the scavenge pump body assembly with tooling (B) and a press as follows:a. Put bearings (9) in position on the inside of the scavenge pump body assembly with the chamfer on the bearing toward the outside of the pump body. Install the bearing until it is 1.52 mm (.060 in) below the inside machined surface of the scavenge pump body assembly. Make sure the joints in the bearings are at an angle of 30° 15° from the center line through the bores in the scavenge pump body and toward the outlet passage of the pump. The outlet passage has a cavity between the bearing bores. 2. Install the bearings in oil pump body assembly with tooling (B) and a press as follows.a. Put bearings (10) in position on the inside of the oil pump body assembly with the chamfer on the bearings toward the outside of the pump body. Install the bearings until they are even with the outside of the pump at an angle of 30° 15° from the centerline through the bearing bores and toward the outlet passage of the pump. The outlet passage has a cavity between the bearing bores.3. Check the condition of the relief valve. Check the condition and specifications for all the parts of the oil pump before it is assembled. See the topic, Oil Pump, in the Specifications module.4. Put clean