Information injection-pump assembly
ZEXEL
101691-6200
1016916200
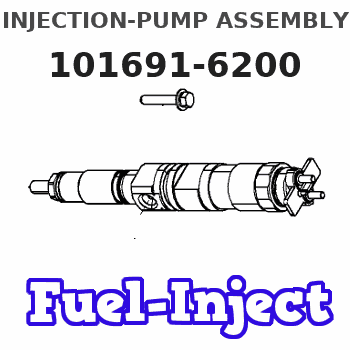
Rating:
Service parts 101691-6200 INJECTION-PUMP ASSEMBLY:
1.
_
6.
COUPLING PLATE
7.
COUPLING PLATE
8.
_
9.
_
11.
Nozzle and Holder
ME080371
12.
Open Pre:MPa(Kqf/cm2)
17.7{180}
15.
NOZZLE SET
Include in #1:
101691-6200
as INJECTION-PUMP ASSEMBLY
Cross reference number
ZEXEL
101691-6200
1016916200
Zexel num
Bosch num
Firm num
Name
101691-6200
INJECTION-PUMP ASSEMBLY
Calibration Data:
Adjustment conditions
Test oil
1404 Test oil ISO4113 or {SAEJ967d}
1404 Test oil ISO4113 or {SAEJ967d}
Test oil temperature
degC
40
40
45
Nozzle and nozzle holder
105780-8140
Bosch type code
EF8511/9A
Nozzle
105780-0000
Bosch type code
DN12SD12T
Nozzle holder
105780-2080
Bosch type code
EF8511/9
Opening pressure
MPa
17.2
Opening pressure
kgf/cm2
175
Injection pipe
Outer diameter - inner diameter - length (mm) mm 6-2-600
Outer diameter - inner diameter - length (mm) mm 6-2-600
Overflow valve
131424-5620
Overflow valve opening pressure
kPa
157
123
191
Overflow valve opening pressure
kgf/cm2
1.6
1.25
1.95
Tester oil delivery pressure
kPa
157
157
157
Tester oil delivery pressure
kgf/cm2
1.6
1.6
1.6
Direction of rotation (viewed from drive side)
Right R
Right R
Injection timing adjustment
Direction of rotation (viewed from drive side)
Right R
Right R
Injection order
1-5-3-6-
2-4
Pre-stroke
mm
3.5
3.45
3.55
Beginning of injection position
Drive side NO.1
Drive side NO.1
Difference between angles 1
Cal 1-5 deg. 60 59.5 60.5
Cal 1-5 deg. 60 59.5 60.5
Difference between angles 2
Cal 1-3 deg. 120 119.5 120.5
Cal 1-3 deg. 120 119.5 120.5
Difference between angles 3
Cal 1-6 deg. 180 179.5 180.5
Cal 1-6 deg. 180 179.5 180.5
Difference between angles 4
Cyl.1-2 deg. 240 239.5 240.5
Cyl.1-2 deg. 240 239.5 240.5
Difference between angles 5
Cal 1-4 deg. 300 299.5 300.5
Cal 1-4 deg. 300 299.5 300.5
Injection quantity adjustment
Adjusting point
A
Rack position
9.2
Pump speed
r/min
900
900
900
Average injection quantity
mm3/st.
54.8
53.8
55.8
Max. variation between cylinders
%
0
-2.5
2.5
Basic
*
Fixing the lever
*
Injection quantity adjustment_02
Adjusting point
B
Rack position
7.5+-0.5
Pump speed
r/min
300
300
300
Average injection quantity
mm3/st.
7.5
6.2
8.8
Max. variation between cylinders
%
0
-14
14
Fixing the rack
*
Injection quantity adjustment_03
Adjusting point
C
Rack position
-
Pump speed
r/min
100
100
100
Average injection quantity
mm3/st.
66
66
71
Fixing the lever
*
Rack limit
*
Timer adjustment
Pump speed
r/min
1000++
Advance angle
deg.
0
0
0
Remarks
Do not advance until starting N = 1000.
Do not advance until starting N = 1000.
Timer adjustment_02
Pump speed
r/min
1000
Advance angle
deg.
0.5
Timer adjustment_03
Pump speed
r/min
-
Advance angle
deg.
3
3
3
Remarks
Measure the actual speed, stop
Measure the actual speed, stop
Test data Ex:
Governor adjustment
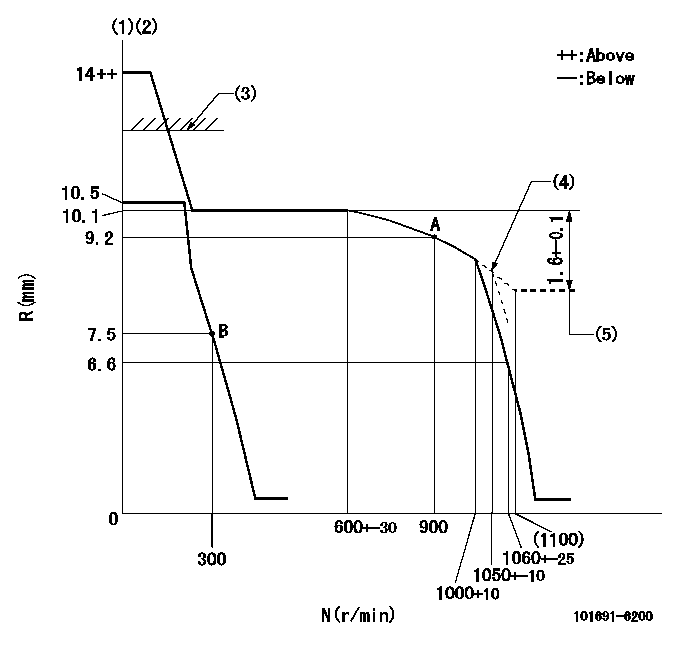
N:Pump speed
R:Rack position (mm)
(1)Target notch: K
(2)Supplied with torque spring not set.
(3)RACK LIMIT
(4)Set at delivery
(5)Rack difference between N = N1 and N = N2
----------
K=13 N1=1200r/min N2=500r/min
----------
----------
K=13 N1=1200r/min N2=500r/min
----------
Speed control lever angle

F:Full speed
I:Idle
(1)Stopper bolt setting
(2)At delivery
----------
----------
a=6deg+-5deg b=23deg+-5deg c=(2deg)
----------
----------
a=6deg+-5deg b=23deg+-5deg c=(2deg)
Stop lever angle
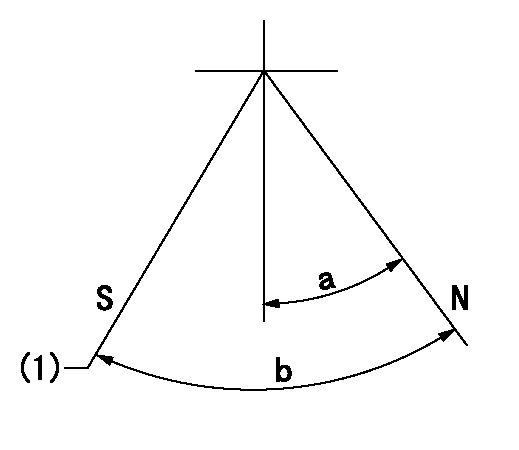
N:Pump normal
S:Stop the pump.
(1)At delivery
----------
----------
a=43deg+-5deg b=53deg+-5deg
----------
----------
a=43deg+-5deg b=53deg+-5deg
Timing setting

(1)Pump vertical direction
(2)Position of gear mark '3' at No 1 cylinder's beginning of injection
(3)B.T.D.C.: aa
(4)-
----------
aa=16deg
----------
a=(130deg)
----------
aa=16deg
----------
a=(130deg)
Information:
Start By:a. disassemble governorb. remove fuel injection pumps
Keep all parts clean from contaminants. Contaminants put into the system may cause rapid wear and shortened component life.
1. Remove cover (1) and gasket. 2. Remove rack (2).
If the original lifters are to be installed in the fuel injection pump housing, put identification marks on them as to their location in the housing.
3. Remove lifters (3). 4. Put the fuel injection pump housing on end on blocks. Use tool (A) to remove snap ring (4). 5. Use a soft hammer to push the camshaft toward the governor end of the fuel injection pump housing to loosen washer (5). Remove washer (5). 6. Remove camshaft (6). 7. Remove bearings (7) from the drive end of the fuel injection pump housing. 8. Remove bearings (8) from the governor end of the fuel injection pump housing.Assemble Fuel Injection Pump Housing
Be sure all oil passages are clear, and put clean oil on all parts before assembly. 1. Use tooling (B) to install bearing (10) in the governor end of the fuel injection pump housing with junction (joint) (11) toward the top of the fuel injection pump housing. Install the bearing so it is 0.25 0.20 mm (0.10 0.008 in) below the surface of the housing.2. Use tooling (B) to install bearing (9) in the governor end of the fuel injection pump housing so it is 7.16 0.13 mm (0.282 0.005 in) below the surface of the housing. 3. Use tooling (B) to install bearing (12) in the drive end of the fuel injection pump housing with the junction (joint) in the bearing toward the top of the fuel injection pump housing. Install the bearing so it is 1.00 0.25 mm (9.039 0.010 in) below the surface of the housing. 4. Install plate (13) of tooling (C) on the drive end of the fuel injection pump housing to install the bearing for the rack. Use clean grease to hold the new rack bearing on driver (14) of tooling (C). Install the driver and bearing in plate (13) with the groove in the driver in alignment with the pin in the plate and use a hammer to push the bearing into position. The bearing will be installed to the correct depth when the shoulder of the driver is against plate (13).5. Remove tooling (C) from the fuel injection pump housing. The rack bearing must be installed so it is 0.25 0.25 mm (0.010 0.010 in) below the surface of the housing. 6. Install camshaft (6).7. Put the fuel injection pump housing on end, and place a block under the camshaft. 8. Put washer (5) over the end of the camshaft and use tooling (B) and a spacer (15) that has an inside diameter of 38.1 mm (1.5 in) and a length of 31.75 mm (1.25 in) to push the washer against its seat on the camshaft. Camshaft must have 0.285 0.235 mm (0.0112 0.0093 in) end play
Keep all parts clean from contaminants. Contaminants put into the system may cause rapid wear and shortened component life.
1. Remove cover (1) and gasket. 2. Remove rack (2).
If the original lifters are to be installed in the fuel injection pump housing, put identification marks on them as to their location in the housing.
3. Remove lifters (3). 4. Put the fuel injection pump housing on end on blocks. Use tool (A) to remove snap ring (4). 5. Use a soft hammer to push the camshaft toward the governor end of the fuel injection pump housing to loosen washer (5). Remove washer (5). 6. Remove camshaft (6). 7. Remove bearings (7) from the drive end of the fuel injection pump housing. 8. Remove bearings (8) from the governor end of the fuel injection pump housing.Assemble Fuel Injection Pump Housing
Be sure all oil passages are clear, and put clean oil on all parts before assembly. 1. Use tooling (B) to install bearing (10) in the governor end of the fuel injection pump housing with junction (joint) (11) toward the top of the fuel injection pump housing. Install the bearing so it is 0.25 0.20 mm (0.10 0.008 in) below the surface of the housing.2. Use tooling (B) to install bearing (9) in the governor end of the fuel injection pump housing so it is 7.16 0.13 mm (0.282 0.005 in) below the surface of the housing. 3. Use tooling (B) to install bearing (12) in the drive end of the fuel injection pump housing with the junction (joint) in the bearing toward the top of the fuel injection pump housing. Install the bearing so it is 1.00 0.25 mm (9.039 0.010 in) below the surface of the housing. 4. Install plate (13) of tooling (C) on the drive end of the fuel injection pump housing to install the bearing for the rack. Use clean grease to hold the new rack bearing on driver (14) of tooling (C). Install the driver and bearing in plate (13) with the groove in the driver in alignment with the pin in the plate and use a hammer to push the bearing into position. The bearing will be installed to the correct depth when the shoulder of the driver is against plate (13).5. Remove tooling (C) from the fuel injection pump housing. The rack bearing must be installed so it is 0.25 0.25 mm (0.010 0.010 in) below the surface of the housing. 6. Install camshaft (6).7. Put the fuel injection pump housing on end, and place a block under the camshaft. 8. Put washer (5) over the end of the camshaft and use tooling (B) and a spacer (15) that has an inside diameter of 38.1 mm (1.5 in) and a length of 31.75 mm (1.25 in) to push the washer against its seat on the camshaft. Camshaft must have 0.285 0.235 mm (0.0112 0.0093 in) end play
Have questions with 101691-6200?
Group cross 101691-6200 ZEXEL
101691-6200
INJECTION-PUMP ASSEMBLY