Information injection-pump assembly
BOSCH
9 400 610 785
9400610785
ZEXEL
101681-9600
1016819600
NISSAN-DIESEL
16712Z5510
16712z5510
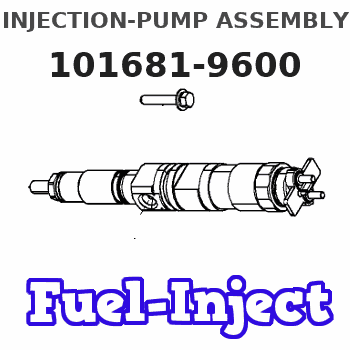
Rating:
Service parts 101681-9600 INJECTION-PUMP ASSEMBLY:
1.
_
6.
COUPLING PLATE
7.
COUPLING PLATE
8.
_
9.
_
11.
Nozzle and Holder
16600-Z5508
12.
Open Pre:MPa(Kqf/cm2)
21.6{220}
15.
NOZZLE SET
Include in #1:
101681-9600
as INJECTION-PUMP ASSEMBLY
Include in #2:
104745-3320
as _
Cross reference number
BOSCH
9 400 610 785
9400610785
ZEXEL
101681-9600
1016819600
NISSAN-DIESEL
16712Z5510
16712z5510
Zexel num
Bosch num
Firm num
Name
101681-9600
9 400 610 785
16712Z5510 NISSAN-DIESEL
INJECTION-PUMP ASSEMBLY
FD6T07 * K
FD6T07 * K
Calibration Data:
Adjustment conditions
Test oil
1404 Test oil ISO4113 or {SAEJ967d}
1404 Test oil ISO4113 or {SAEJ967d}
Test oil temperature
degC
40
40
45
Nozzle and nozzle holder
105780-8140
Bosch type code
EF8511/9A
Nozzle
105780-0000
Bosch type code
DN12SD12T
Nozzle holder
105780-2080
Bosch type code
EF8511/9
Opening pressure
MPa
17.2
Opening pressure
kgf/cm2
175
Injection pipe
Outer diameter - inner diameter - length (mm) mm 6-2-600
Outer diameter - inner diameter - length (mm) mm 6-2-600
Overflow valve
132424-0620
Overflow valve opening pressure
kPa
157
123
191
Overflow valve opening pressure
kgf/cm2
1.6
1.25
1.95
Tester oil delivery pressure
kPa
157
157
157
Tester oil delivery pressure
kgf/cm2
1.6
1.6
1.6
Direction of rotation (viewed from drive side)
Right R
Right R
Injection timing adjustment
Direction of rotation (viewed from drive side)
Right R
Right R
Injection order
1-4-2-6-
3-5
Pre-stroke
mm
2.4
2.35
2.45
Beginning of injection position
Drive side NO.1
Drive side NO.1
Difference between angles 1
Cal 1-4 deg. 60 59.5 60.5
Cal 1-4 deg. 60 59.5 60.5
Difference between angles 2
Cyl.1-2 deg. 120 119.5 120.5
Cyl.1-2 deg. 120 119.5 120.5
Difference between angles 3
Cal 1-6 deg. 180 179.5 180.5
Cal 1-6 deg. 180 179.5 180.5
Difference between angles 4
Cal 1-3 deg. 240 239.5 240.5
Cal 1-3 deg. 240 239.5 240.5
Difference between angles 5
Cal 1-5 deg. 300 299.5 300.5
Cal 1-5 deg. 300 299.5 300.5
Injection quantity adjustment
Adjusting point
A
Rack position
9.5
Pump speed
r/min
750
750
750
Average injection quantity
mm3/st.
59
58
60
Max. variation between cylinders
%
0
-2.5
2.5
Basic
*
Fixing the lever
*
Injection quantity adjustment_02
Adjusting point
C
Rack position
7+-0.5
Pump speed
r/min
300
300
300
Average injection quantity
mm3/st.
14.6
13.5
15.7
Max. variation between cylinders
%
0
-15
15
Fixing the rack
*
Injection quantity adjustment_03
Adjusting point
D
Rack position
13.9+-0.
1
Pump speed
r/min
100
100
100
Average injection quantity
mm3/st.
115
105
125
Fixing the lever
*
Rack limit
*
Timer adjustment
Pump speed
r/min
600
Advance angle
deg.
0.5
Timer adjustment_02
Pump speed
r/min
900
Advance angle
deg.
0.6
0.1
1.1
Timer adjustment_03
Pump speed
r/min
-
Advance angle
deg.
3
2.5
3.5
Remarks
Measure the actual speed, stop
Measure the actual speed, stop
Test data Ex:
Governor adjustment
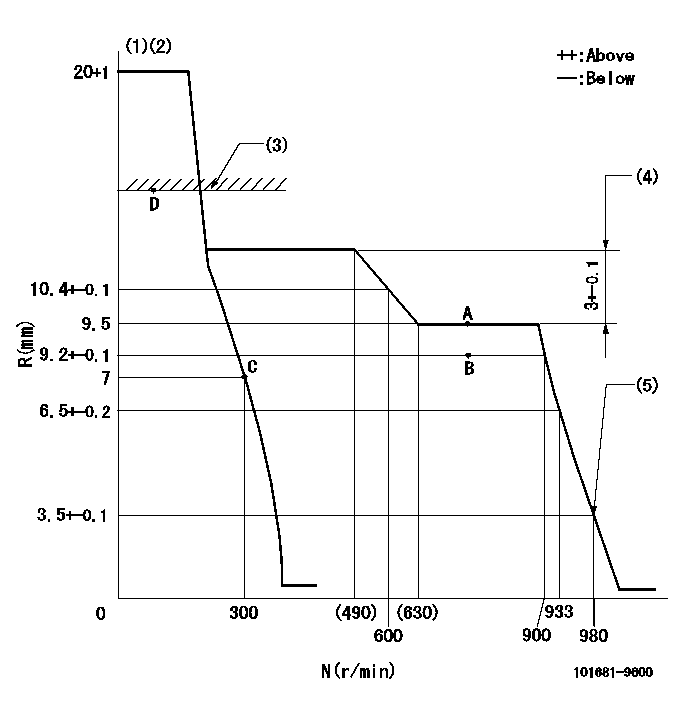
N:Pump speed
R:Rack position (mm)
(1)Target notch: K
(2)Tolerance for racks not indicated: +-0.05mm.
(3)RACK LIMIT
(4)Rack difference between N = N1 and N = N2
(5)Set idle sub-spring
----------
K=17 N1=750r/min N2=450r/min
----------
----------
K=17 N1=750r/min N2=450r/min
----------
Speed control lever angle
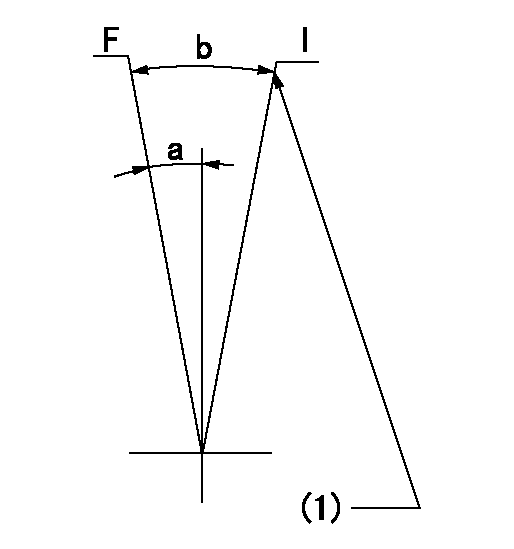
F:Full speed
I:Idle
(1)Stopper bolt setting
----------
----------
a=10deg+-5deg b=25deg+-5deg
----------
----------
a=10deg+-5deg b=25deg+-5deg
Stop lever angle

N:Pump normal
S:Stop the pump.
----------
----------
a=26.5deg+-5deg b=53deg+-5deg
----------
----------
a=26.5deg+-5deg b=53deg+-5deg
0000001501 GOV FULL LOAD ADJUSTMENT
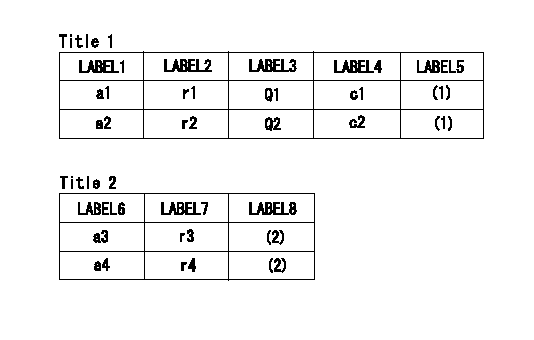
Title1:Full load stopper adjustment
Title2:Governor set speed
LABEL1:Distinguishing
LABEL2:Pump speed (r/min)
LABEL3:Ave. injection quantity (mm3/st)
LABEL4:Max. var. bet. cyl.
LABEL5:Remarks
LABEL6:Distinguishing
LABEL7:Governor set speed (r/min)
LABEL8:Remarks
(1)Adjustment conditions are the same as those for measuring injection quantity.
(2)-
----------
----------
a1=B a2=E r1=750r/min r2=750r/min Q1=59+-1mm3/st Q2=- c1=+-2.5% c2=+-2.5% a3=18 a4=- r3=900r/min r4=-
----------
----------
a1=B a2=E r1=750r/min r2=750r/min Q1=59+-1mm3/st Q2=- c1=+-2.5% c2=+-2.5% a3=18 a4=- r3=900r/min r4=-
Timing setting
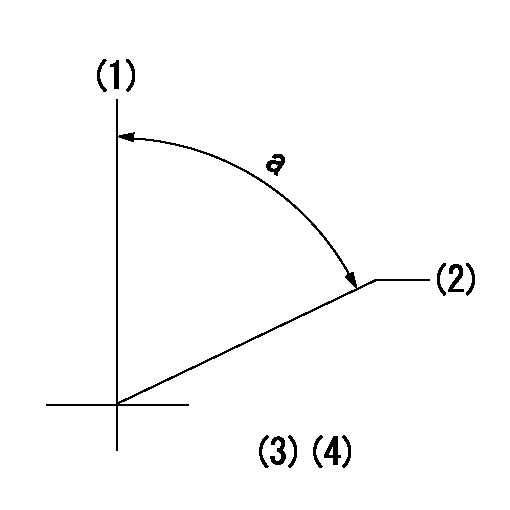
(1)Pump vertical direction
(2)Position of gear mark 'P' at No 1 cylinder's beginning of injection
(3)-
(4)-
----------
----------
a=(50deg)
----------
----------
a=(50deg)
Information:
Crankcase Lubricating Oil
The Lubrication and Maintenance Charts list the normal oil change periods as determined by fuel sulphur content. (Make an initial oil change after the first 500 miles of operation for reconditioned engines.)Use oils which meet Engine Service classification CD or MIL-L-2104C. These are additive-type oils that have been approved for use in Caterpillar Diesel Engines. Diesel Engine Crankcase
Check oil level daily before starting engine and when refueling. Check with the engine either running or stopped as indicated on the oil level gauge. Add oil when the level drops to the add oil mark. Drain the crankcase every 10,000 miles while engine is warm and stopped. If equipped with a 13 qt. supplemental filter system the normal interval can be extended to 15,000 miles. Install drain plug. Diesel Engine Crankcase Lubricating Oil Filter
Change filter element every 10,000 miles. Drain the filter housing by removing drain plug. Loosen bolt on the cover and remove the housing and filter element. Inspect seal and install a new one if necessary. Wash the inside of the filter housing and install a new Caterpillar filter element. After draining crankcase remove filter cap and refill. See page 15 for quantity. Start engine and check for oil leaks at drain plug and filter housing. Diesel Engine Crankcase Breather
Remove breather tube cover and element. Wash with clean solvent or diesel fuel at each oil change period. Inspect seal and replace if necessary. Lubricating Grease
Use Multipurpose-type Grease which contains both 3 to 5% molybdenum disulfide conforming to MIL-M-7866, and a suitable corrosion inhibitor. NLGI No. 2 Grade is suitable for most temperatures. NLGI No. 1 or No. 0 are suitable for extremely low temperatures.Always clean fittings before lubricating.Fan Pulley Bearing
Lubricate every 10,000 miles. Lubricate through fitting until grease appears at relief fitting on front of fan hub. Wipe off excess grease. Water Pump Bearing
Lubricate every 10,000 miles. Lubricate through fitting until lubricant appears at relief fitting. Earlier engines have no relief fitting. Excess lubricant will appear at end of water pump shaft. Tachometer Drive
Lubricate every 10,000 miles. Remove plug. Install grease fitting and apply one stroke of lubricant through fitting.
The Lubrication and Maintenance Charts list the normal oil change periods as determined by fuel sulphur content. (Make an initial oil change after the first 500 miles of operation for reconditioned engines.)Use oils which meet Engine Service classification CD or MIL-L-2104C. These are additive-type oils that have been approved for use in Caterpillar Diesel Engines. Diesel Engine Crankcase
Check oil level daily before starting engine and when refueling. Check with the engine either running or stopped as indicated on the oil level gauge. Add oil when the level drops to the add oil mark. Drain the crankcase every 10,000 miles while engine is warm and stopped. If equipped with a 13 qt. supplemental filter system the normal interval can be extended to 15,000 miles. Install drain plug. Diesel Engine Crankcase Lubricating Oil Filter
Change filter element every 10,000 miles. Drain the filter housing by removing drain plug. Loosen bolt on the cover and remove the housing and filter element. Inspect seal and install a new one if necessary. Wash the inside of the filter housing and install a new Caterpillar filter element. After draining crankcase remove filter cap and refill. See page 15 for quantity. Start engine and check for oil leaks at drain plug and filter housing. Diesel Engine Crankcase Breather
Remove breather tube cover and element. Wash with clean solvent or diesel fuel at each oil change period. Inspect seal and replace if necessary. Lubricating Grease
Use Multipurpose-type Grease which contains both 3 to 5% molybdenum disulfide conforming to MIL-M-7866, and a suitable corrosion inhibitor. NLGI No. 2 Grade is suitable for most temperatures. NLGI No. 1 or No. 0 are suitable for extremely low temperatures.Always clean fittings before lubricating.Fan Pulley Bearing
Lubricate every 10,000 miles. Lubricate through fitting until grease appears at relief fitting on front of fan hub. Wipe off excess grease. Water Pump Bearing
Lubricate every 10,000 miles. Lubricate through fitting until lubricant appears at relief fitting. Earlier engines have no relief fitting. Excess lubricant will appear at end of water pump shaft. Tachometer Drive
Lubricate every 10,000 miles. Remove plug. Install grease fitting and apply one stroke of lubricant through fitting.
Have questions with 101681-9600?
Group cross 101681-9600 ZEXEL
Nissan-Diesel
101681-9600
9 400 610 785
16712Z5510
INJECTION-PUMP ASSEMBLY
FD6T07
FD6T07