Information injection-pump assembly
BOSCH
9 400 610 381
9400610381
ZEXEL
101641-9302
1016419302
NISSAN-DIESEL
1670006J61
1670006j61
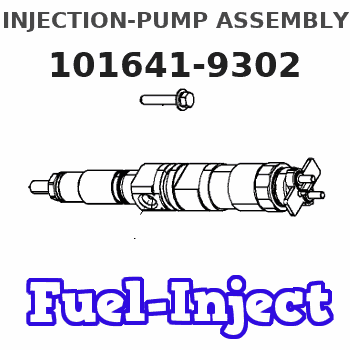
Rating:
Service parts 101641-9302 INJECTION-PUMP ASSEMBLY:
1.
_
6.
COUPLING PLATE
7.
COUPLING PLATE
8.
_
9.
_
11.
Nozzle and Holder
1660043G03
12.
Open Pre:MPa(Kqf/cm2)
9.8(100)
15.
NOZZLE SET
Include in #1:
101641-9302
as INJECTION-PUMP ASSEMBLY
Cross reference number
BOSCH
9 400 610 381
9400610381
ZEXEL
101641-9302
1016419302
NISSAN-DIESEL
1670006J61
1670006j61
Zexel num
Bosch num
Firm num
Name
9 400 610 381
1670006J61 NISSAN-DIESEL
INJECTION-PUMP ASSEMBLY
TD42 K 14BE INJECTION PUMP ASSY PE6A PE
TD42 K 14BE INJECTION PUMP ASSY PE6A PE
Calibration Data:
Adjustment conditions
Test oil
1404 Test oil ISO4113 or {SAEJ967d}
1404 Test oil ISO4113 or {SAEJ967d}
Test oil temperature
degC
40
40
45
Nozzle and nozzle holder
105780-8140
Bosch type code
EF8511/9A
Nozzle
105780-0000
Bosch type code
DN12SD12T
Nozzle holder
105780-2080
Bosch type code
EF8511/9
Opening pressure
MPa
17.2
Opening pressure
kgf/cm2
175
Injection pipe
Outer diameter - inner diameter - length (mm) mm 6-2-600
Outer diameter - inner diameter - length (mm) mm 6-2-600
Tester oil delivery pressure
kPa
157
157
157
Tester oil delivery pressure
kgf/cm2
1.6
1.6
1.6
Direction of rotation (viewed from drive side)
Right R
Right R
Injection timing adjustment
Direction of rotation (viewed from drive side)
Right R
Right R
Injection order
1-4-2-6-
3-5
Pre-stroke
mm
2.15
2.1
2.2
Beginning of injection position
Drive side NO.1
Drive side NO.1
Difference between angles 1
Cal 1-4 deg. 60 59.5 60.5
Cal 1-4 deg. 60 59.5 60.5
Difference between angles 2
Cyl.1-2 deg. 120 119.5 120.5
Cyl.1-2 deg. 120 119.5 120.5
Difference between angles 3
Cal 1-6 deg. 180 179.5 180.5
Cal 1-6 deg. 180 179.5 180.5
Difference between angles 4
Cal 1-3 deg. 240 239.5 240.5
Cal 1-3 deg. 240 239.5 240.5
Difference between angles 5
Cal 1-5 deg. 300 299.5 300.5
Cal 1-5 deg. 300 299.5 300.5
Injection quantity adjustment
Adjusting point
-
Rack position
13.8
Pump speed
r/min
1000
1000
1000
Average injection quantity
mm3/st.
46.5
45.5
47.5
Max. variation between cylinders
%
0
-2.5
2.5
Basic
*
Fixing the rack
*
Injection quantity adjustment_02
Adjusting point
-
Rack position
12.3
Pump speed
r/min
2000
2000
2000
Average injection quantity
mm3/st.
48
44.8
51.2
Fixing the rack
*
Injection quantity adjustment_03
Adjusting point
-
Rack position
9.3+-0.5
Pump speed
r/min
350
350
350
Average injection quantity
mm3/st.
9.8
8.7
10.9
Max. variation between cylinders
%
0
-15
15
Fixing the rack
*
Timer adjustment
Pump speed
r/min
550--
Advance angle
deg.
0
0
0
Remarks
Start
Start
Timer adjustment_02
Pump speed
r/min
500
Advance angle
deg.
0.5
Timer adjustment_03
Pump speed
r/min
2150
Advance angle
deg.
6
5.5
6.5
Remarks
Finish
Finish
Test data Ex:
Governor adjustment
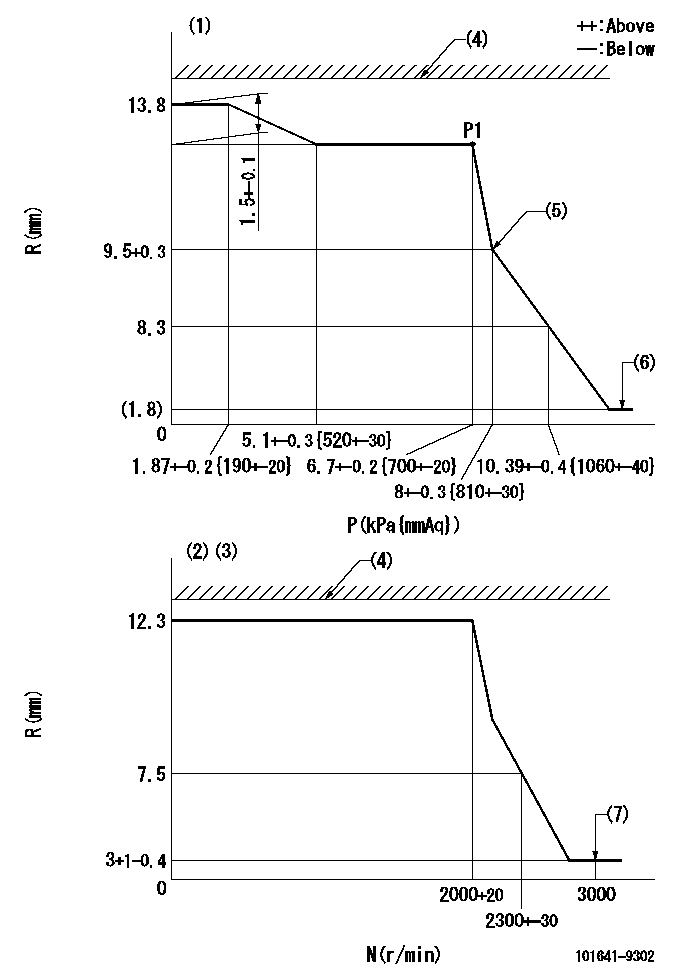
N:Pump speed
R:Rack position (mm)
P:Negative pressure
(1)Pneumatic governor
(2)Mechanical governor
(3)Acting negative pressure: P1
(4)RACK LIMIT: RAL
(5)Beginning of idle sub spring operation: L1
(6)With stopper disk.
(7)Injection quantity Q = Q1 or less
----------
RAL=16.1-0.3mm L1=9.5+0.3mm Q1=3mm3/st
----------
----------
RAL=16.1-0.3mm L1=9.5+0.3mm Q1=3mm3/st
----------
0000001101
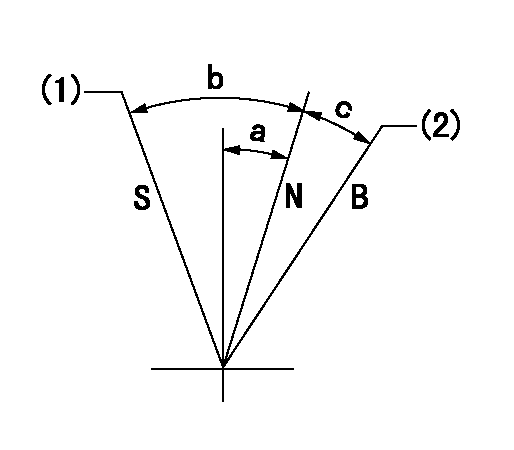
N:Normal
B:When boosted
S:Stop
(1)Rack position = aa
(2)Rack position corresponding to cc
----------
aa=(1.8)mm bb=15mm
----------
a=2.5deg+-5deg b=24.5deg+-3deg c=2deg+-5deg
----------
aa=(1.8)mm bb=15mm
----------
a=2.5deg+-5deg b=24.5deg+-3deg c=2deg+-5deg
0000001501 ACS
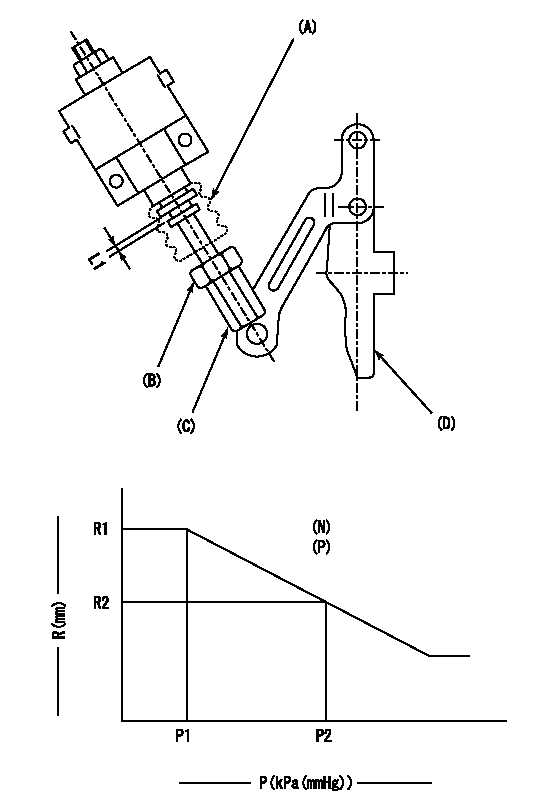
(N): Speed of the pump
(P): aneroid compensator negative pressure
(A) rubber boot
(B) Nut
(c) Nut
(D) Lever
1. Aneroid compensator installation
(1)Turn nut (C) to adjust gap to L1.
(2)Lock using nut (B).
(3)Move the lever to the excess fuel supply side and confirm that it moves smoothly.
----------
L1=0.1~0.5mm
----------
N=1000r/min P=0.98kPa(100mmAq) R1=13.8mm R2=13mm Pa1=5.9+-2.7kPa(44+-20mmHg) Pa2=21.9kPa(164mmHg) Q1=46.5+-1cm3/1000st Q2=(40.6)cm3/1000st
----------
L1=0.1~0.5mm
----------
N=1000r/min P=0.98kPa(100mmAq) R1=13.8mm R2=13mm Pa1=5.9+-2.7kPa(44+-20mmHg) Pa2=21.9kPa(164mmHg) Q1=46.5+-1cm3/1000st Q2=(40.6)cm3/1000st
Timing setting

(1)Pump vertical direction
(2)Position of gear mark 'ZZ' at No 1 cylinder's beginning of injection
(3)B.T.D.C.: aa
(4)-
----------
aa=16deg
----------
a=(110deg)
----------
aa=16deg
----------
a=(110deg)
Information:
Air Shutoff Solenoid (If Equipped)
This optional solenoid is located on top of the engine in the air inlet system. When the solenoid is activated, the solenoid mechanically shuts off inlet air to the engine. The solenoid can only be activated by the overspeed switch or the emergency stop switch.Fuel Shutoff Solenoid
This solenoid is located on the governor or on the fuel injection pump. When the solenoid is activated, the solenoid moves the fuel rack (either directly or through the governor) to the Fuel Off position.Overspeed Shutoffs
Magnetic pickup (1), mounted in the flywheel housing (2).A magnetic pickup mounted in the flywheel housing senses the passage of the flywheel ring gear teeth. Should the engine speed increase above the overspeed setting of the Electronic Speed Switch (118 percent of rated engine speed), the magnetic pickup will sense the overspeed. The overspeed condition activates both the air (if equipped) and fuel shutoff solenoids.The shutoffs must be reset before the engine will restart. A reset button on the Electronic Speed Switch (in the junction box) must be pushed to open the overspeed switch. The air shutoff lever (at the top of the air inlet housing) must be manually reset.If equipped with a Caterpillar Generator Set Control Panel, the devices on the panel must be reset after an overspeed shutoff. Turn the Engine Control Switch to the OFF/RESET position.Oil Pressure Switches
Typical example of oil pressure switches, mounted in the rear of the junction box.An oil pressure switch has wires connected to the electrical system for alarm or shutoff functions. The oil pressure switch senses oil pressure at the bearing oil gallery. If sufficient oil pressure is not achieved after engine starting, or if the engine has been running normally and then loses oil pressure, the fuel shutoff solenoid is energized to shut the engine off. No resetting procedure is required.Engine Step Oil Pressure
This is an adjustable engine speed setting that protects the engine from a failure caused by too little oil pressure for a specified speed range. This option requires two different oil pressure switches. One switch has a high pressure rating- when the engine is running above the speed setting, the engine must maintain oil pressure higher than the switch rating. The other switch has a low pressure rating- an engine running below the speed setting must maintain oil pressure above the low switch rating.In an automatic start/stop system, an automatic reset switch is used. Manually operated systems require the switch to be reset before the engine will start.
If the RESET button does not move to the extended position after the engine starts, the engine will NOT be protected by this particular switch.If the RESET button remains in the reset position, the engine oil pump will not develop normal oil pressure. An inspection should be made to correct the problem.
In order to reset the switch, push the RESET button until the button latches. After the engine starts and develops oil pressure, the button will move to the extended (running) position.
The button must
This optional solenoid is located on top of the engine in the air inlet system. When the solenoid is activated, the solenoid mechanically shuts off inlet air to the engine. The solenoid can only be activated by the overspeed switch or the emergency stop switch.Fuel Shutoff Solenoid
This solenoid is located on the governor or on the fuel injection pump. When the solenoid is activated, the solenoid moves the fuel rack (either directly or through the governor) to the Fuel Off position.Overspeed Shutoffs
Magnetic pickup (1), mounted in the flywheel housing (2).A magnetic pickup mounted in the flywheel housing senses the passage of the flywheel ring gear teeth. Should the engine speed increase above the overspeed setting of the Electronic Speed Switch (118 percent of rated engine speed), the magnetic pickup will sense the overspeed. The overspeed condition activates both the air (if equipped) and fuel shutoff solenoids.The shutoffs must be reset before the engine will restart. A reset button on the Electronic Speed Switch (in the junction box) must be pushed to open the overspeed switch. The air shutoff lever (at the top of the air inlet housing) must be manually reset.If equipped with a Caterpillar Generator Set Control Panel, the devices on the panel must be reset after an overspeed shutoff. Turn the Engine Control Switch to the OFF/RESET position.Oil Pressure Switches
Typical example of oil pressure switches, mounted in the rear of the junction box.An oil pressure switch has wires connected to the electrical system for alarm or shutoff functions. The oil pressure switch senses oil pressure at the bearing oil gallery. If sufficient oil pressure is not achieved after engine starting, or if the engine has been running normally and then loses oil pressure, the fuel shutoff solenoid is energized to shut the engine off. No resetting procedure is required.Engine Step Oil Pressure
This is an adjustable engine speed setting that protects the engine from a failure caused by too little oil pressure for a specified speed range. This option requires two different oil pressure switches. One switch has a high pressure rating- when the engine is running above the speed setting, the engine must maintain oil pressure higher than the switch rating. The other switch has a low pressure rating- an engine running below the speed setting must maintain oil pressure above the low switch rating.In an automatic start/stop system, an automatic reset switch is used. Manually operated systems require the switch to be reset before the engine will start.
If the RESET button does not move to the extended position after the engine starts, the engine will NOT be protected by this particular switch.If the RESET button remains in the reset position, the engine oil pump will not develop normal oil pressure. An inspection should be made to correct the problem.
In order to reset the switch, push the RESET button until the button latches. After the engine starts and develops oil pressure, the button will move to the extended (running) position.
The button must