Information injection-pump assembly
ZEXEL
101631-9761
1016319761
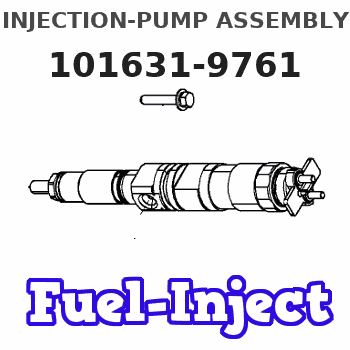
Rating:
Service parts 101631-9761 INJECTION-PUMP ASSEMBLY:
1.
_
6.
COUPLING PLATE
7.
COUPLING PLATE
8.
_
9.
_
11.
Nozzle and Holder
16600-20053
12.
Open Pre:MPa(Kqf/cm2)
9.8{100}
15.
NOZZLE SET
Include in #1:
101631-9761
as INJECTION-PUMP ASSEMBLY
Include in #2:
104740-3280
as _
Cross reference number
ZEXEL
101631-9761
1016319761
Zexel num
Bosch num
Firm num
Name
Calibration Data:
Adjustment conditions
Test oil
1404 Test oil ISO4113 or {SAEJ967d}
1404 Test oil ISO4113 or {SAEJ967d}
Test oil temperature
degC
40
40
45
Nozzle and nozzle holder
105780-8140
Bosch type code
EF8511/9A
Nozzle
105780-0000
Bosch type code
DN12SD12T
Nozzle holder
105780-2080
Bosch type code
EF8511/9
Opening pressure
MPa
17.2
Opening pressure
kgf/cm2
175
Injection pipe
Outer diameter - inner diameter - length (mm) mm 6-2-600
Outer diameter - inner diameter - length (mm) mm 6-2-600
Tester oil delivery pressure
kPa
157
157
157
Tester oil delivery pressure
kgf/cm2
1.6
1.6
1.6
Direction of rotation (viewed from drive side)
Right R
Right R
Injection timing adjustment
Direction of rotation (viewed from drive side)
Right R
Right R
Injection order
1-4-2-6-
3-5
Pre-stroke
mm
2.15
2.1
2.2
Rack position
R=11.7
Beginning of injection position
Drive side NO.1
Drive side NO.1
Difference between angles 1
Cal 1-4 deg. 60 59.5 60.5
Cal 1-4 deg. 60 59.5 60.5
Difference between angles 2
Cyl.1-2 deg. 120 119.5 120.5
Cyl.1-2 deg. 120 119.5 120.5
Difference between angles 3
Cal 1-6 deg. 180 179.5 180.5
Cal 1-6 deg. 180 179.5 180.5
Difference between angles 4
Cal 1-3 deg. 240 239.5 240.5
Cal 1-3 deg. 240 239.5 240.5
Difference between angles 5
Cal 1-5 deg. 300 299.5 300.5
Cal 1-5 deg. 300 299.5 300.5
Injection quantity adjustment
Adjusting point
-
Rack position
12.2
Pump speed
r/min
800
800
800
Average injection quantity
mm3/st.
32.1
31.1
33.1
Max. variation between cylinders
%
0
-2.5
2.5
Basic
*
Fixing the rack
*
Injection quantity adjustment_02
Adjusting point
-
Rack position
11.7
Pump speed
r/min
1900
1900
1900
Average injection quantity
mm3/st.
36.1
34.5
37.7
Max. variation between cylinders
%
0
-4
4
Fixing the rack
*
Injection quantity adjustment_03
Adjusting point
-
Rack position
8.6+-0.5
Pump speed
r/min
300
300
300
Average injection quantity
mm3/st.
7.5
6.5
8.5
Max. variation between cylinders
%
0
-15
15
Fixing the rack
*
Injection quantity adjustment_04
Adjusting point
-
Rack position
-
Pump speed
r/min
800
800
800
Average injection quantity
mm3/st.
32.1
31.6
32.6
Remarks
Set full load.
Set full load.
Timer adjustment
Pump speed
r/min
550--
Advance angle
deg.
0
0
0
Remarks
Start
Start
Timer adjustment_02
Pump speed
r/min
500
Advance angle
deg.
0.5
Timer adjustment_03
Pump speed
r/min
1100
Advance angle
deg.
1.7
1.2
2.2
Timer adjustment_04
Pump speed
r/min
1900
Advance angle
deg.
6
5.5
6.5
Remarks
Finish
Finish
Test data Ex:
Governor adjustment
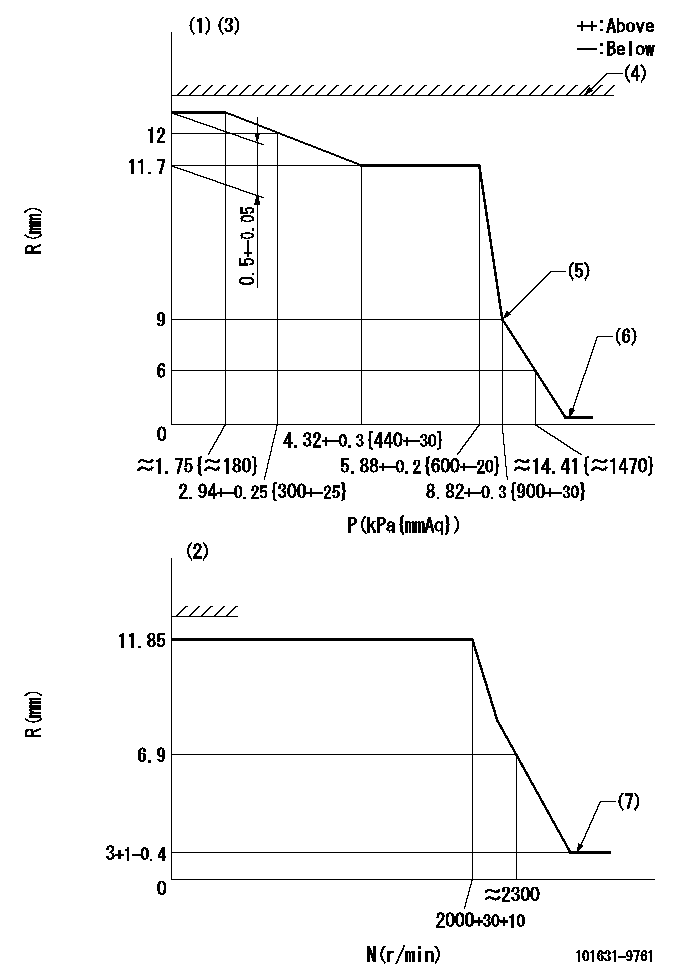
N:Pump speed
R:Rack position (mm)
P:Negative pressure
(1)Pneumatic governor
(2)Mechanical governor
(3)Acting negative pressure: P1
(4)RACK LIMIT: RAL
(5)Beginning of idle sub spring operation: L1
(6)With stopper disk.
(7)Injection quantity Q = Q1 or less
----------
P1=3.63+-0.2kPa(370+-20mmAq) RAL=17-0.3mm L1=9+0.3mm Q1=3mm3/st
----------
----------
P1=3.63+-0.2kPa(370+-20mmAq) RAL=17-0.3mm L1=9+0.3mm Q1=3mm3/st
----------
Speed control lever angle
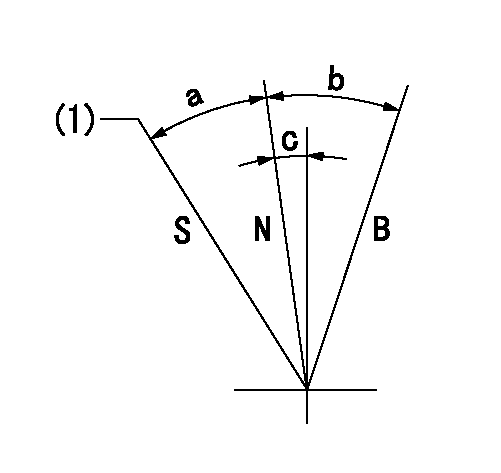
N:Normal
B:When boosted
S:Stop
(1)Rack position = aa
----------
aa=(1.8)mm
----------
a=20.5deg+-3deg b=8deg+-5deg c=0.5deg+-5deg
----------
aa=(1.8)mm
----------
a=20.5deg+-3deg b=8deg+-5deg c=0.5deg+-5deg
Timing setting
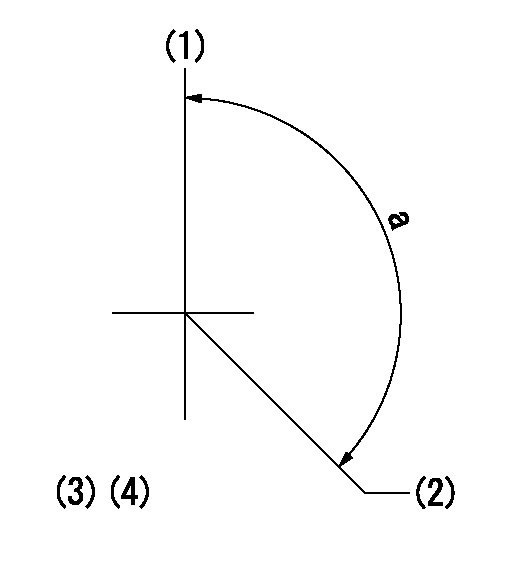
(1)Pump vertical direction
(2)Position of gear mark 'Y' at No 1 cylinder's beginning of injection
(3)B.T.D.C.: aa
(4)-
----------
aa=20deg
----------
a=(130deg)
----------
aa=20deg
----------
a=(130deg)
Information:
Start By:a. remove exhaust manifoldb. remove inlet manifoldc. remove fuel injection nozzle assembliesd. remove fuel filtere. remove water temperature regulatorf. remove cylinder head assembly 1. Put cylinder head assembly (1) in position on tool group (A). 2. Put compression on valve spring (2) with tool (C). 3. Remove spring locks (3). 4. Remove tool (C). Remove valve spring cap (2) and valve springs (4). 5. Remove washer (5) and O-ring seal (8) from valve (7).6. Remove seal (6). Remove valve (7). 7. Check the valve spring tension with tool (B). The outer spring force must be 180 9 N (40 2 lb.). The length of the spring under test force must be 27.4 mm (1.08 in.). The free length after test must be 45.2 mm (1.78 in.). The inner spring force must be 68.5 9 N (15.4 2 lb.). The length of the spring under test force must be 23.88 mm (.940 in.). The length after test must be 39.6 mm (1.56 in.).8. Do Steps 1 through 8 again for the remainder of the valves. If the cylinder head is equipped with removable valve guides, refer to module SENB8082-06, System Operating Testing And Adjusting Specifications, 4.236 And 4.2482 Diesel Engines For Lift Trucks.Install Valves
1. Put clean engine oil on the valve stems.2. Install valve (3), washer (2) and seal (1).
The closed coil of the spring must be toward the cylinder head.
3. Install springs (5) and valve spring cap (4). 4. Use tool (A), and put springs under compression, and install O-ring seal on the valve. Exhaust valves have an extra O-ring seal on them.
Locks (6) can be thrown from the valve when tool (A) is released if they are not in their correct position on the valve stem.
5. Use tool (B), and install locks (6) that hold the springs in place.6. Remove tool (A), and hit the top of the valve with a plastic hammer to be sure the locks are in their correct position on the valve.7. Do Steps 1 through 6 again for the remainder of the valves.End By:a. install cylinder head assemblyb. install water temperature regulatorc. install fuel filterd. install fuel injection nozzle assembliese. install inlet manifold
1. Put clean engine oil on the valve stems.2. Install valve (3), washer (2) and seal (1).
The closed coil of the spring must be toward the cylinder head.
3. Install springs (5) and valve spring cap (4). 4. Use tool (A), and put springs under compression, and install O-ring seal on the valve. Exhaust valves have an extra O-ring seal on them.
Locks (6) can be thrown from the valve when tool (A) is released if they are not in their correct position on the valve stem.
5. Use tool (B), and install locks (6) that hold the springs in place.6. Remove tool (A), and hit the top of the valve with a plastic hammer to be sure the locks are in their correct position on the valve.7. Do Steps 1 through 6 again for the remainder of the valves.End By:a. install cylinder head assemblyb. install water temperature regulatorc. install fuel filterd. install fuel injection nozzle assembliese. install inlet manifold