Information injection-pump assembly
BOSCH
F 019 Z20 041
f019z20041
ZEXEL
101609-9223
1016099223
MITSUBISHI-HEAV
3436501053
3436501053
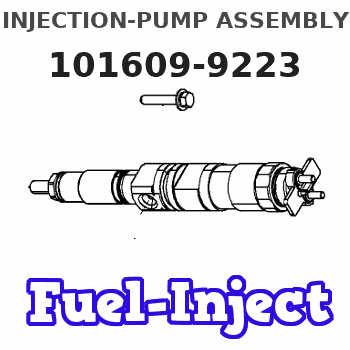
Rating:
Service parts 101609-9223 INJECTION-PUMP ASSEMBLY:
1.
_
5.
AUTOM. ADVANCE MECHANIS
6.
COUPLING PLATE
8.
_
9.
_
11.
Nozzle and Holder
12.
Open Pre:MPa(Kqf/cm2)
21.6(220)
15.
NOZZLE SET
Include in #1:
101609-9223
as INJECTION-PUMP ASSEMBLY
Include in #2:
104132-6040
as _
Cross reference number
BOSCH
F 019 Z20 041
f019z20041
ZEXEL
101609-9223
1016099223
MITSUBISHI-HEAV
3436501053
3436501053
Zexel num
Bosch num
Firm num
Name
F 019 Z20 041
3436501053 MITSUBISHI-HEAV
INJECTION-PUMP ASSEMBLY
S6K-T * K 14BE INJECTION PUMP ASSY PE6A PE
S6K-T * K 14BE INJECTION PUMP ASSY PE6A PE
Calibration Data:
Adjustment conditions
Test oil
1404 Test oil ISO4113 or {SAEJ967d}
1404 Test oil ISO4113 or {SAEJ967d}
Test oil temperature
degC
40
40
45
Nozzle and nozzle holder
105780-8140
Bosch type code
EF8511/9A
Nozzle
105780-0000
Bosch type code
DN12SD12T
Nozzle holder
105780-2080
Bosch type code
EF8511/9
Opening pressure
MPa
17.2
Opening pressure
kgf/cm2
175
Injection pipe
Outer diameter - inner diameter - length (mm) mm 6-2-600
Outer diameter - inner diameter - length (mm) mm 6-2-600
Overflow valve
131424-5720
Overflow valve opening pressure
kPa
255
221
289
Overflow valve opening pressure
kgf/cm2
2.6
2.25
2.95
Tester oil delivery pressure
kPa
255
255
255
Tester oil delivery pressure
kgf/cm2
2.6
2.6
2.6
Direction of rotation (viewed from drive side)
Right R
Right R
Injection timing adjustment
Direction of rotation (viewed from drive side)
Right R
Right R
Injection order
1-5-3-6-
2-4
Pre-stroke
mm
3.7
3.65
3.75
Rack position
After adjusting injection quantity. R=A
After adjusting injection quantity. R=A
Beginning of injection position
Drive side NO.1
Drive side NO.1
Difference between angles 1
Cal 1-5 deg. 60 59.5 60.5
Cal 1-5 deg. 60 59.5 60.5
Difference between angles 2
Cal 1-3 deg. 120 119.5 120.5
Cal 1-3 deg. 120 119.5 120.5
Difference between angles 3
Cal 1-6 deg. 180 179.5 180.5
Cal 1-6 deg. 180 179.5 180.5
Difference between angles 4
Cyl.1-2 deg. 240 239.5 240.5
Cyl.1-2 deg. 240 239.5 240.5
Difference between angles 5
Cal 1-4 deg. 300 299.5 300.5
Cal 1-4 deg. 300 299.5 300.5
Injection quantity adjustment
Adjusting point
A
Rack position
7.05
Pump speed
r/min
1100
1100
1100
Average injection quantity
mm3/st.
41.5
40.5
42.5
Max. variation between cylinders
%
0
-3.5
3.5
Basic
*
Fixing the lever
*
Injection quantity adjustment_02
Adjusting point
-
Rack position
6.4+-0.5
Pump speed
r/min
425
425
425
Average injection quantity
mm3/st.
8
6.7
9.3
Max. variation between cylinders
%
0
-10
10
Fixing the rack
*
Remarks
Adjust only variation between cylinders; adjust governor according to governor specifications.
Adjust only variation between cylinders; adjust governor according to governor specifications.
Test data Ex:
Governor adjustment
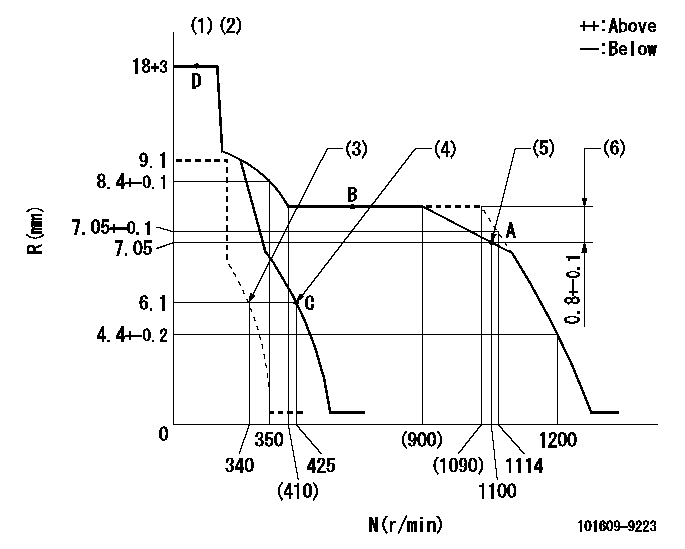
N:Pump speed
R:Rack position (mm)
(1)Target notch: K
(2)Tolerance for racks not indicated: +-0.05mm.
(3)Set idle sub-spring
(4)Main spring setting
(5)Set the torque spring.
(6)Rack difference between N = N1 and N = N2
----------
K=15 N1=1100r/min N2=700r/min
----------
----------
K=15 N1=1100r/min N2=700r/min
----------
Speed control lever angle
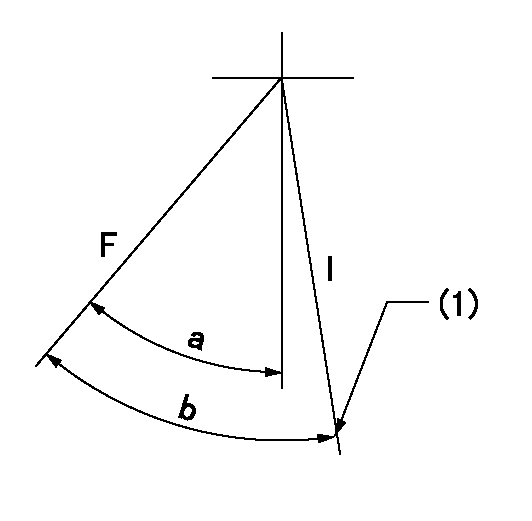
F:Full speed
I:Idle
(1)Stopper bolt setting
----------
----------
a=19deg+-5deg b=19deg+-5deg
----------
----------
a=19deg+-5deg b=19deg+-5deg
Stop lever angle
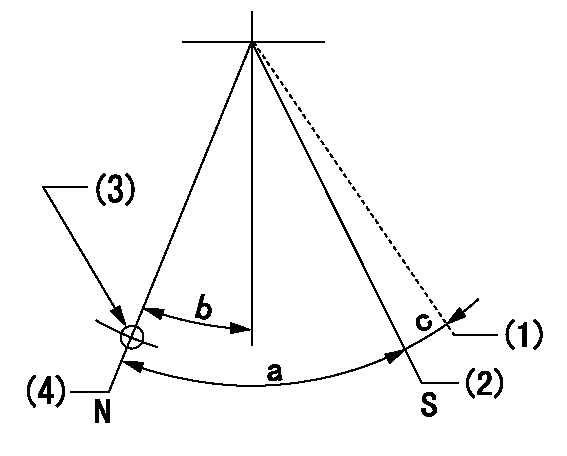
N:Pump normal
S:Stop the pump.
(1)Contacts outer boss.
(2)Contacts inner boss.
(3)Use the hole at R = aa
(4)Normal
----------
aa=60mm
----------
a=53deg+-5deg b=26.5deg+-5deg c=(9deg)
----------
aa=60mm
----------
a=53deg+-5deg b=26.5deg+-5deg c=(9deg)
0000001501 I/P WITH LOAD PLUNGER ADJ
Load plunger-equipped pump adjustment
1. Adjust the variation between cylinders and the injection quantity.
2. At Full point A, adjust the pre-stroke to the specified value.
3. After pre-stroke adjustment, reconfirm that the fuel injection quantity and the variation between cylinders is as specified.
----------
----------
----------
----------
Timing setting

(1)Pump vertical direction
(2)Position of gear mark '3' at No 1 cylinder's beginning of injection
(3)B.T.D.C.: aa
(4)After adjusting the injection quantity, adjust at rack position bb.
----------
aa=6deg bb=7.05mm
----------
a=(110deg)
----------
aa=6deg bb=7.05mm
----------
a=(110deg)
Information:
6. Coat the seal of the element with a thin film of clean engine oil or antifreeze. 7. Install the element. Tighten it until the seal contacts the base, then tighten it an additional 3/4 turn. 8. Open the inlet valve and the outlet valve. 9. Maintain the coolant level above the low level plate. 10. Clean and install the radiator cap.11. Start the engine and check for leaks.Brakes
Inspect - Adjust
The machine must be level, the bowl lowered, and the parking brake applied.1. Block the wheels securely.2. Start the engine. 3. When the air pressure reaches the NORMAL range, stop the engine. 4. Release the parking/emergency brake. 5. Measure the distance from the rotochamber to the slack adjuster clevis retaining pin. 6. Apply the service brake and measure the amount of travel of the rod. If the travel is 76 mm (3 inches) or more, adjust the brake.7. Measure the brake rotochamber rod travel of all four wheel brakes. Scraper rotochambers are located inside the push frame.To Adjust
1. Loosen the adjustment locking bolt. 2. Turn the adjusting bolt, as required, until the travel is 41 mm (1.62 inches). 3. Tighten the locking bolt. 4. Apply and release the brakes, watching the rotochamber rod for binding.5. Observe the diaphragm for leaks. 6. Start the engine and allow air pressure to reach 690 kPa (100 psi) or in the green range on the air pressure gauge.7. Apply the parking brake.8. Stop the engine.9. Remove the blocking from the wheels.Check the Air System for Leaks
1. Start the engine and allow air pressure to reach 690 kPa (100 psi) or in the green range on the air pressure gauge. 2. Apply the service brakes and hold them in the applied condition.3. Stop the engine.4. With the brakes applied, watch the air pressure gauge.5. The pressure should drop no more than 35 kPa (5 psi) in 10 minutes.6. If the air pressure loss is greater than 35 kPa (5 psi), inspect the air lines and connections. Make any necessary repairs.To Test Brakes
Be sure the area around the vehicle is clear of personnel and obstructions.Fasten the seat belt before operating the vehicle.Test the brakes on a dry, level surface.
The vehicle must be on a dry, level surface, the bowl lowered and the parking brake applied.The following tests are to determine if the service brake or parking/emergency brake is functional. These tests are not intended to measure maximum brake holding effort.Brake holding effort required to hold a vehicle at a specific engine rpm will vary from vehicle to vehicle due to differences in engine setting, power train efficiency, etc., as well as differences in brake holding ability.Engine rpm at beginning of vehicle movement, with service or parking/emergency brake applied, should be compared against the engine rpm your specific vehicle was able to hold on a prior test, as an indication of system deterioration.Service Brake
1. Start the engine. Allow the engine to reach the normal operating temperature.2. When air pressure registers 690 kPa (100 psi) or
Inspect - Adjust
The machine must be level, the bowl lowered, and the parking brake applied.1. Block the wheels securely.2. Start the engine. 3. When the air pressure reaches the NORMAL range, stop the engine. 4. Release the parking/emergency brake. 5. Measure the distance from the rotochamber to the slack adjuster clevis retaining pin. 6. Apply the service brake and measure the amount of travel of the rod. If the travel is 76 mm (3 inches) or more, adjust the brake.7. Measure the brake rotochamber rod travel of all four wheel brakes. Scraper rotochambers are located inside the push frame.To Adjust
1. Loosen the adjustment locking bolt. 2. Turn the adjusting bolt, as required, until the travel is 41 mm (1.62 inches). 3. Tighten the locking bolt. 4. Apply and release the brakes, watching the rotochamber rod for binding.5. Observe the diaphragm for leaks. 6. Start the engine and allow air pressure to reach 690 kPa (100 psi) or in the green range on the air pressure gauge.7. Apply the parking brake.8. Stop the engine.9. Remove the blocking from the wheels.Check the Air System for Leaks
1. Start the engine and allow air pressure to reach 690 kPa (100 psi) or in the green range on the air pressure gauge. 2. Apply the service brakes and hold them in the applied condition.3. Stop the engine.4. With the brakes applied, watch the air pressure gauge.5. The pressure should drop no more than 35 kPa (5 psi) in 10 minutes.6. If the air pressure loss is greater than 35 kPa (5 psi), inspect the air lines and connections. Make any necessary repairs.To Test Brakes
Be sure the area around the vehicle is clear of personnel and obstructions.Fasten the seat belt before operating the vehicle.Test the brakes on a dry, level surface.
The vehicle must be on a dry, level surface, the bowl lowered and the parking brake applied.The following tests are to determine if the service brake or parking/emergency brake is functional. These tests are not intended to measure maximum brake holding effort.Brake holding effort required to hold a vehicle at a specific engine rpm will vary from vehicle to vehicle due to differences in engine setting, power train efficiency, etc., as well as differences in brake holding ability.Engine rpm at beginning of vehicle movement, with service or parking/emergency brake applied, should be compared against the engine rpm your specific vehicle was able to hold on a prior test, as an indication of system deterioration.Service Brake
1. Start the engine. Allow the engine to reach the normal operating temperature.2. When air pressure registers 690 kPa (100 psi) or