Information injection-pump assembly
BOSCH
9 400 615 922
9400615922
ZEXEL
101609-9221
1016099221
MITSUBISHI-HEAV
3436501051
3436501051
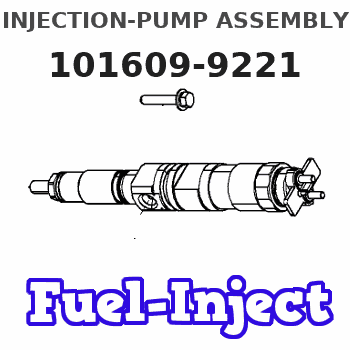
Rating:
Service parts 101609-9221 INJECTION-PUMP ASSEMBLY:
1.
_
5.
AUTOM. ADVANCE MECHANIS
6.
COUPLING PLATE
8.
_
9.
_
11.
Nozzle and Holder
12.
Open Pre:MPa(Kqf/cm2)
15.
NOZZLE SET
Include in #1:
101609-9221
as INJECTION-PUMP ASSEMBLY
Include in #2:
104132-6020
as _
Cross reference number
BOSCH
9 400 615 922
9400615922
ZEXEL
101609-9221
1016099221
MITSUBISHI-HEAV
3436501051
3436501051
Zexel num
Bosch num
Firm num
Name
9 400 615 922
3436501051 MITSUBISHI-HEAV
INJECTION-PUMP ASSEMBLY
S6K-T * K 14BE PE6A PE
S6K-T * K 14BE PE6A PE
Calibration Data:
Adjustment conditions
Test oil
1404 Test oil ISO4113 or {SAEJ967d}
1404 Test oil ISO4113 or {SAEJ967d}
Test oil temperature
degC
40
40
45
Nozzle and nozzle holder
105780-8140
Bosch type code
EF8511/9A
Nozzle
105780-0000
Bosch type code
DN12SD12T
Nozzle holder
105780-2080
Bosch type code
EF8511/9
Opening pressure
MPa
17.2
Opening pressure
kgf/cm2
175
Injection pipe
Outer diameter - inner diameter - length (mm) mm 6-2-600
Outer diameter - inner diameter - length (mm) mm 6-2-600
Overflow valve
131424-5720
Overflow valve opening pressure
kPa
255
221
289
Overflow valve opening pressure
kgf/cm2
2.6
2.25
2.95
Tester oil delivery pressure
kPa
255
255
255
Tester oil delivery pressure
kgf/cm2
2.6
2.6
2.6
Direction of rotation (viewed from drive side)
Right R
Right R
Injection timing adjustment
Direction of rotation (viewed from drive side)
Right R
Right R
Injection order
1-5-3-6-
2-4
Pre-stroke
mm
3.7
3.65
3.75
Rack position
After adjusting injection quantity. R=A
After adjusting injection quantity. R=A
Beginning of injection position
Drive side NO.1
Drive side NO.1
Difference between angles 1
Cal 1-5 deg. 60 59.5 60.5
Cal 1-5 deg. 60 59.5 60.5
Difference between angles 2
Cal 1-3 deg. 120 119.5 120.5
Cal 1-3 deg. 120 119.5 120.5
Difference between angles 3
Cal 1-6 deg. 180 179.5 180.5
Cal 1-6 deg. 180 179.5 180.5
Difference between angles 4
Cyl.1-2 deg. 240 239.5 240.5
Cyl.1-2 deg. 240 239.5 240.5
Difference between angles 5
Cal 1-4 deg. 300 299.5 300.5
Cal 1-4 deg. 300 299.5 300.5
Injection quantity adjustment
Adjusting point
A
Rack position
6.9
Pump speed
r/min
1100
1100
1100
Average injection quantity
mm3/st.
38.7
37.7
39.7
Max. variation between cylinders
%
0
-3.5
3.5
Basic
*
Fixing the lever
*
Injection quantity adjustment_02
Adjusting point
-
Rack position
6.4+-0.5
Pump speed
r/min
425
425
425
Average injection quantity
mm3/st.
8
6.7
9.3
Max. variation between cylinders
%
0
-10
10
Fixing the rack
*
Remarks
Adjust only variation between cylinders; adjust governor according to governor specifications.
Adjust only variation between cylinders; adjust governor according to governor specifications.
Test data Ex:
Governor adjustment
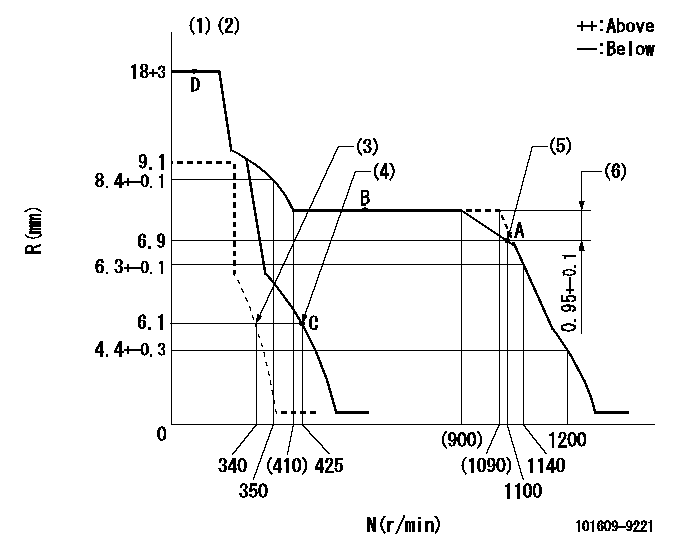
N:Pump speed
R:Rack position (mm)
(1)Target notch: K
(2)Tolerance for racks not indicated: +-0.05mm.
(3)Set idle sub-spring
(4)Main spring setting
(5)Set the torque spring.
(6)Rack difference between N = N1 and N = N2
----------
K=(15) N1=1100r/min N2=700r/min
----------
----------
K=(15) N1=1100r/min N2=700r/min
----------
Speed control lever angle
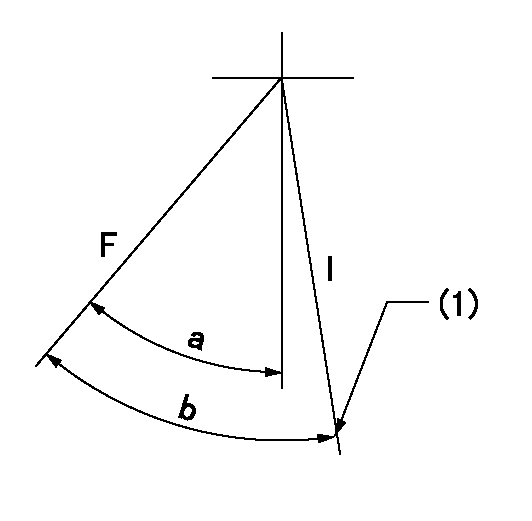
F:Full speed
I:Idle
(1)Stopper bolt setting
----------
----------
a=(21deg)+-5deg b=(22deg)+-5deg
----------
----------
a=(21deg)+-5deg b=(22deg)+-5deg
Stop lever angle
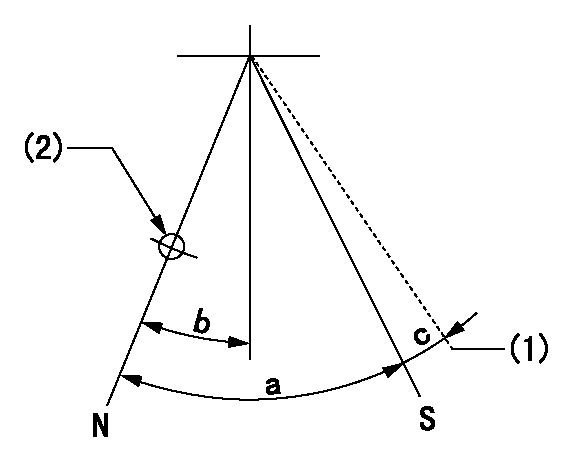
N:Pump normal
S:Stop the pump.
(1)Hold the boss against the stop side
(2)Use the hole at R = aa
----------
aa=60mm
----------
a=53deg+-5deg b=26.5deg+-5deg c=(9deg)
----------
aa=60mm
----------
a=53deg+-5deg b=26.5deg+-5deg c=(9deg)
0000001501 I/P WITH LOAD PLUNGER ADJ
Load plunger-equipped pump adjustment
1. Adjust the variation between cylinders and the injection quantity.
2. At Full point A, adjust the pre-stroke to the specified value.
3. After pre-stroke adjustment, reconfirm that the fuel injection quantity and the variation between cylinders is as specified.
----------
----------
----------
----------
Timing setting

(1)Pump vertical direction
(2)Position of gear mark '3' at No 1 cylinder's beginning of injection
(3)B.T.D.C.: aa
(4)After adjusting the injection quantity, adjust at rack position bb.
----------
aa=6deg bb=6.9mm
----------
a=(110deg)
----------
aa=6deg bb=6.9mm
----------
a=(110deg)
Information:
Changing Ether Cylinders
Ether is poisonous and flammable.Do not store replacement ether cylinders in living areas or in the operator's compartment.Do not smoke while changing ether cylinders.Use ether only in well ventilated areas.Use it with care to avoid fires.Keep the cylinders out of the reach of children.Avoid breathing ether vapors or repeated contact of ether with the skin.Do not store cylinders in direct sunlight.Do not puncture or burn the cylinders.Discard the cylinders in a safe place.
The ether cylinder is located at the right front of the machine, inside the guard. 1. Remove the two bolts to open the guard. 2. Loosen the clamp (1). Unscrew the cylinder (2). 3. Remove the used gasket and replace it with the new one provided with each new cylinder. 4. Install a new cylinder and tighten it hand tight. Tighten the clamp.5. Close the guard and install the retaining bolts.
Remove the ether cylinder before shipping the machine.
Draft Frame Arms
(631, 633, 637, 639)
Adjust
The draft frame arms and the scraper bowl can be in contact, but there must be no wear between them. Install wear shoe and shims, as needed, on the inside of draft frame arm. The clearance between the draft frame arm and the scraper bowl must not exceed .00 + 3.0 - .00 mm (.00 + .12 - .00 in).Refer to the Service Manual for your machine or contact your Caterpillar dealer for the correct adjustment procedures.
Ether is poisonous and flammable.Do not store replacement ether cylinders in living areas or in the operator's compartment.Do not smoke while changing ether cylinders.Use ether only in well ventilated areas.Use it with care to avoid fires.Keep the cylinders out of the reach of children.Avoid breathing ether vapors or repeated contact of ether with the skin.Do not store cylinders in direct sunlight.Do not puncture or burn the cylinders.Discard the cylinders in a safe place.
The ether cylinder is located at the right front of the machine, inside the guard. 1. Remove the two bolts to open the guard. 2. Loosen the clamp (1). Unscrew the cylinder (2). 3. Remove the used gasket and replace it with the new one provided with each new cylinder. 4. Install a new cylinder and tighten it hand tight. Tighten the clamp.5. Close the guard and install the retaining bolts.
Remove the ether cylinder before shipping the machine.
Draft Frame Arms
(631, 633, 637, 639)
Adjust
The draft frame arms and the scraper bowl can be in contact, but there must be no wear between them. Install wear shoe and shims, as needed, on the inside of draft frame arm. The clearance between the draft frame arm and the scraper bowl must not exceed .00 + 3.0 - .00 mm (.00 + .12 - .00 in).Refer to the Service Manual for your machine or contact your Caterpillar dealer for the correct adjustment procedures.