Information injection-pump assembly
ZEXEL
101609-3270
1016093270
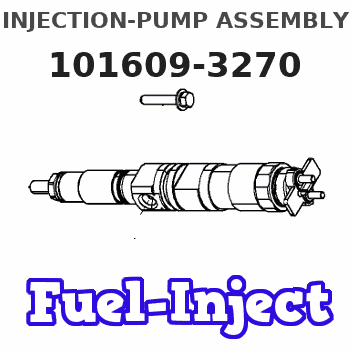
Rating:
Service parts 101609-3270 INJECTION-PUMP ASSEMBLY:
1.
_
5.
AUTOM. ADVANCE MECHANIS
6.
COUPLING PLATE
7.
COUPLING PLATE
8.
_
9.
_
10.
NOZZLE AND HOLDER ASSY
11.
Nozzle and Holder
12.
Open Pre:MPa(Kqf/cm2)
21.6{220}
13.
NOZZLE-HOLDER
14.
NOZZLE
15.
NOZZLE SET
Include in #1:
101609-3270
as INJECTION-PUMP ASSEMBLY
Include in #2:
104257-1080
as _
Cross reference number
ZEXEL
101609-3270
1016093270
Zexel num
Bosch num
Firm num
Name
101609-3270
INJECTION-PUMP ASSEMBLY
Calibration Data:
Adjustment conditions
Test oil
1404 Test oil ISO4113 or {SAEJ967d}
1404 Test oil ISO4113 or {SAEJ967d}
Test oil temperature
degC
40
40
45
Nozzle and nozzle holder
105780-8140
Bosch type code
EF8511/9A
Nozzle
105780-0000
Bosch type code
DN12SD12T
Nozzle holder
105780-2080
Bosch type code
EF8511/9
Opening pressure
MPa
17.2
Opening pressure
kgf/cm2
175
Injection pipe
Outer diameter - inner diameter - length (mm) mm 6-2-600
Outer diameter - inner diameter - length (mm) mm 6-2-600
Overflow valve
131424-3420
Overflow valve opening pressure
kPa
255
221
289
Overflow valve opening pressure
kgf/cm2
2.6
2.25
2.95
Tester oil delivery pressure
kPa
157
157
157
Tester oil delivery pressure
kgf/cm2
1.6
1.6
1.6
Direction of rotation (viewed from drive side)
Right R
Right R
Injection timing adjustment
Direction of rotation (viewed from drive side)
Right R
Right R
Injection order
1-5-3-6-
2-4
Pre-stroke
mm
2.5
2.45
2.55
Beginning of injection position
Drive side NO.1
Drive side NO.1
Difference between angles 1
Cal 1-5 deg. 60 59.5 60.5
Cal 1-5 deg. 60 59.5 60.5
Difference between angles 2
Cal 1-3 deg. 120 119.5 120.5
Cal 1-3 deg. 120 119.5 120.5
Difference between angles 3
Cal 1-6 deg. 180 179.5 180.5
Cal 1-6 deg. 180 179.5 180.5
Difference between angles 4
Cyl.1-2 deg. 240 239.5 240.5
Cyl.1-2 deg. 240 239.5 240.5
Difference between angles 5
Cal 1-4 deg. 300 299.5 300.5
Cal 1-4 deg. 300 299.5 300.5
Injection quantity adjustment
Adjusting point
A
Rack position
9.2
Pump speed
r/min
1000
1000
1000
Average injection quantity
mm3/st.
79.5
78.5
80.5
Max. variation between cylinders
%
0
-2.5
2.5
Basic
*
Fixing the lever
*
Injection quantity adjustment_02
Adjusting point
-
Rack position
7.1+-0.5
Pump speed
r/min
500
500
500
Average injection quantity
mm3/st.
15
14
16
Max. variation between cylinders
%
0
-15
15
Fixing the rack
*
Remarks
Adjust only variation between cylinders; adjust governor according to governor specifications.
Adjust only variation between cylinders; adjust governor according to governor specifications.
Injection quantity adjustment_03
Adjusting point
D
Rack position
-
Pump speed
r/min
100
100
100
Average injection quantity
mm3/st.
70
70
80
Fixing the lever
*
Rack limit
*
Test data Ex:
Governor adjustment
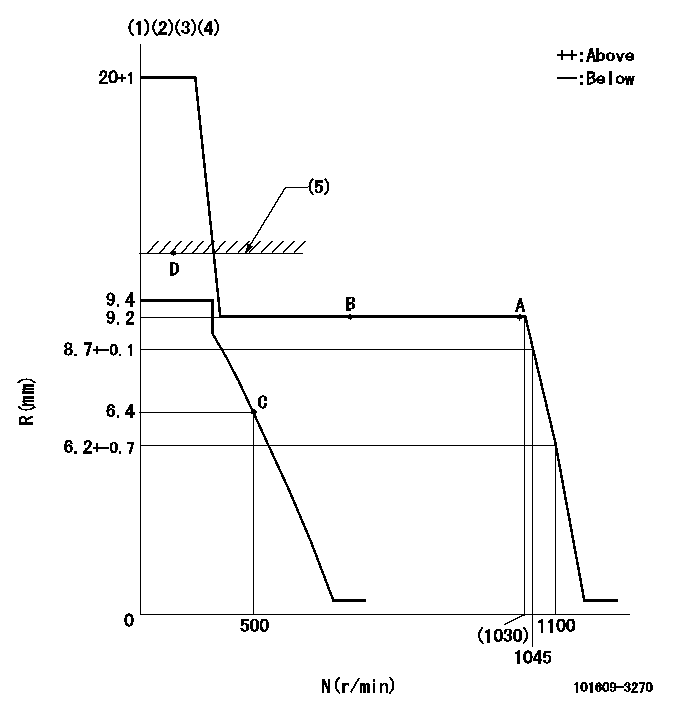
N:Pump speed
R:Rack position (mm)
(1)Target notch: K
(2)Tolerance for racks not indicated: +-0.05mm.
(3)The torque control spring does not operate.
(4)Adjust the secondary timing before adjusting the governor.
(5)RACK LIMIT
----------
K=18
----------
----------
K=18
----------
Speed control lever angle

F:Full speed
I:Idle
S:Stop
----------
----------
a=15deg+-5deg b=27deg+-5deg c=32deg+-3deg
----------
----------
a=15deg+-5deg b=27deg+-5deg c=32deg+-3deg
Stop lever angle
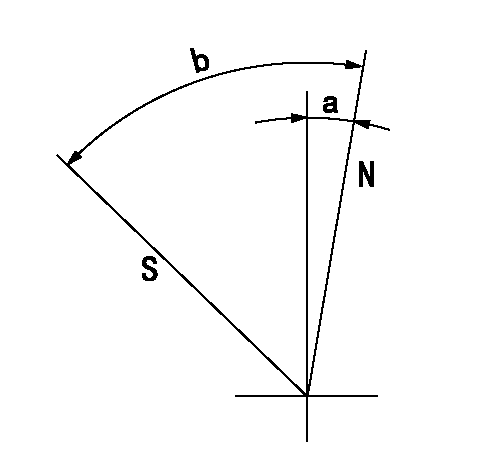
N:Pump normal
S:Stop the pump.
----------
----------
a=0deg+-5deg b=53deg+-5deg
----------
----------
a=0deg+-5deg b=53deg+-5deg
Timing setting

(1)Pump vertical direction
(2)Key groove position at No. 1 cylinder's beginning of injection position (at BTDC: aa).
(3)Position of the key groove of the No. 1 cylinder at B.T.D.C. bb (fix the governor flyweight at this position for delivery).
(4)B.T.D.C.: aa
(5)At second timing adjustment, set the camshaft at the * position and tighten the flyweight locknut.
(6)Align the flyweight's timing gear position with the lockpin groove and then fully tighten the flyweight to the camshaft.
(7)Remove the lock pin and adjust the governor. Reinstall the lock pin to fix the flyweight for delivery.
----------
aa=17deg bb=0deg
----------
a=54deg54min+-3deg b=8deg30min+-30min
----------
aa=17deg bb=0deg
----------
a=54deg54min+-3deg b=8deg30min+-30min
Information:
This Revised Service Letter replaces the 05Dec2012 (Revised 31Jan2013) Service Letter. Changes have been made to the Affected Product and Action Required.
TERMINATION DATE
31Dec2013
PROBLEM
The existing fuel injector has a 150 degree spray pattern. During the combustion stroke (process), the current end of injection timing maps can allow the 150 degree spray pattern to temporarily impinge upon the exposed wall of the cylinder liner as the piston moves downward in the bore.
Depending on engine speed and load factors, the fuel making contact with the liner can dilute the oil film or cause excessive soot. The excessive soot can build up to form carbon deposits at the piston lands and grooves, resulting in uneven top ring and groove wear, which may cause ring breakage. This situation is aggravated by contamination within the air and lubrication systems.
AFFECTED PRODUCT
Model Identification Number
793D FDB00105-01737, 1739
PARTS NEEDED
Qty
Part Number Description
16 20R2296 INJECTOR GP-FUEL
1 4264383 SOFTWARE GP-ELEK
In order to allow equitable parts availability to all participating dealers, please limit your initial parts order to not exceed 7% of dealership population. This is an initial order recommendation only, and the ultimate responsibility for ordering the total number of parts needed to satisfy the program lies with the dealer.
ACTION REQUIRED
This program does not apply to 793D Off-Highway Trucks equipped with high altitude engine arrangements.
If a 793D Off-Highway Truck that is listed in the Affected Product already has 423-7547 Fuel Injectors or 20R-2296 Fuel Injectors installed, do not apply this Service Letter.
Refer to the service manual if/as necessary.
Install a full set of sixteen 145 degree fuel injectors along with the software.
NOTE 1: Do not mix the 145 degree fuel injectors with the former 150 degree fuel injectors in the same engine.
NOTE 2: Do not install the software that is listed in the Parts Needed unless all sixteen fuel injectors have been replaced by the 145 degree spray pattern fuel injectors that is listed in the Parts Needed.
SERVICE CLAIM ALLOWANCES
Product smu/age whichever comes first Caterpillar Dealer Suggested Customer Suggested
Parts % Labor Hrs% Parts % Labor Hrs% Parts % Labor Hrs%
0-1000 hrs,
0-6 mo 100.0% 100.0% 0.0% 0.0% 0.0% 0.0%
This is a 8.0-hour job
If there has been a previous repair, part age/hours will apply. Retain a copy of the previous repair invoice in the dealer's records for audit purposes, and specify repair date and machine hours in the "Additional Comments" section of the warranty claim.
If the engine is out of chassis for Planned Component Rebuild (PCR), the software and injectors should be installed. However, the costs for the software and injector update are not covered under this program.
PARTS DISPOSITION
Handle the parts in accordance with your Warranty Bulletin on warranty parts handling.
Have questions with 101609-3270?
Group cross 101609-3270 ZEXEL
101609-3270
INJECTION-PUMP ASSEMBLY