Information injection-pump assembly
BOSCH
9 400 615 888
9400615888
ZEXEL
101609-3080
1016093080
KOMATSU
6221711220
6221711220
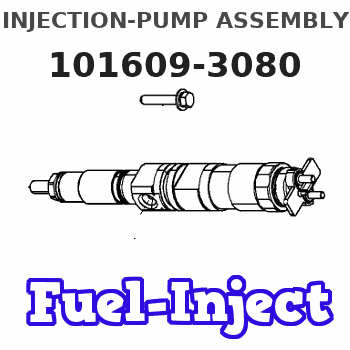
Rating:
Service parts 101609-3080 INJECTION-PUMP ASSEMBLY:
1.
_
5.
AUTOM. ADVANCE MECHANIS
6.
COUPLING PLATE
7.
COUPLING PLATE
8.
_
9.
_
11.
Nozzle and Holder
12.
Open Pre:MPa(Kqf/cm2)
23.0{235}
15.
NOZZLE SET
Include in #1:
101609-3080
as INJECTION-PUMP ASSEMBLY
Include in #2:
104242-8032
as _
Cross reference number
BOSCH
9 400 615 888
9400615888
ZEXEL
101609-3080
1016093080
KOMATSU
6221711220
6221711220
Zexel num
Bosch num
Firm num
Name
101609-3080
9 400 615 888
6221711220 KOMATSU
INJECTION-PUMP ASSEMBLY
S6D108 K 14BF INJECTION PUMP ASSY PE6AD PE
S6D108 K 14BF INJECTION PUMP ASSY PE6AD PE
Calibration Data:
Adjustment conditions
Test oil
1404 Test oil ISO4113 or {SAEJ967d}
1404 Test oil ISO4113 or {SAEJ967d}
Test oil temperature
degC
40
40
45
Nozzle and nozzle holder
105780-8140
Bosch type code
EF8511/9A
Nozzle
105780-0000
Bosch type code
DN12SD12T
Nozzle holder
105780-2080
Bosch type code
EF8511/9
Opening pressure
MPa
17.2
Opening pressure
kgf/cm2
175
Injection pipe
Outer diameter - inner diameter - length (mm) mm 6-2-600
Outer diameter - inner diameter - length (mm) mm 6-2-600
Overflow valve
131424-1520
Overflow valve opening pressure
kPa
157
123
191
Overflow valve opening pressure
kgf/cm2
1.6
1.25
1.95
Tester oil delivery pressure
kPa
157
157
157
Tester oil delivery pressure
kgf/cm2
1.6
1.6
1.6
RED3 control unit part number
407910-2
470
RED3 rack sensor specifications
mm
15
Direction of rotation (viewed from drive side)
Right R
Right R
Injection timing adjustment
Direction of rotation (viewed from drive side)
Right R
Right R
Injection order
1-5-3-6-
2-4
Pre-stroke
mm
3.6
3.55
3.65
Beginning of injection position
Drive side NO.1
Drive side NO.1
Difference between angles 1
Cal 1-5 deg. 60 59.5 60.5
Cal 1-5 deg. 60 59.5 60.5
Difference between angles 2
Cal 1-3 deg. 120 119.5 120.5
Cal 1-3 deg. 120 119.5 120.5
Difference between angles 3
Cal 1-6 deg. 180 179.5 180.5
Cal 1-6 deg. 180 179.5 180.5
Difference between angles 4
Cyl.1-2 deg. 240 239.5 240.5
Cyl.1-2 deg. 240 239.5 240.5
Difference between angles 5
Cal 1-4 deg. 300 299.5 300.5
Cal 1-4 deg. 300 299.5 300.5
Injection quantity adjustment
Rack position
(13.1)
Vist
V
1.38
1.38
1.38
Pump speed
r/min
1100
1100
1100
Average injection quantity
mm3/st.
135.5
134.5
136.5
Max. variation between cylinders
%
0
-2
2
Basic
*
Injection quantity adjustment_02
Rack position
(6.6)
Vist
V
2.7
2.6
2.8
Pump speed
r/min
350
350
350
Average injection quantity
mm3/st.
13.5
12.3
14.7
Max. variation between cylinders
%
0
-10
10
Injection quantity adjustment_03
Remarks
Rack limit setting V = 0.9-0.04
Rack limit setting V = 0.9-0.04
Test data Ex:
Speed control lever angle
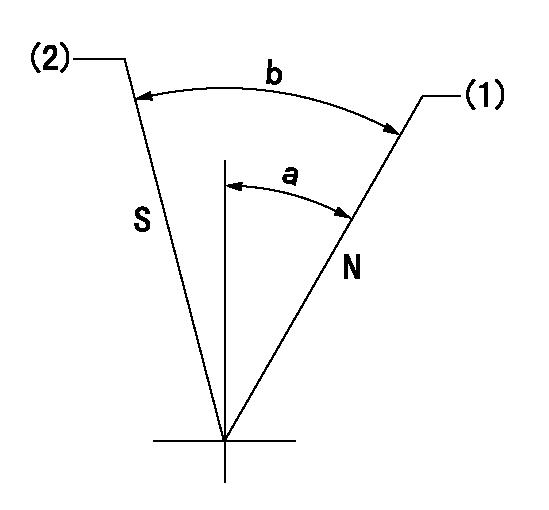
N:Pump normal
S:Stop the pump.
(1)Vist = aa, (rack position = bb)
(2)Rack position = cc
----------
aa=0.8V bb=16mm cc=1mm
----------
a=19deg+-5deg b=29deg+-5deg
----------
aa=0.8V bb=16mm cc=1mm
----------
a=19deg+-5deg b=29deg+-5deg
0000000901
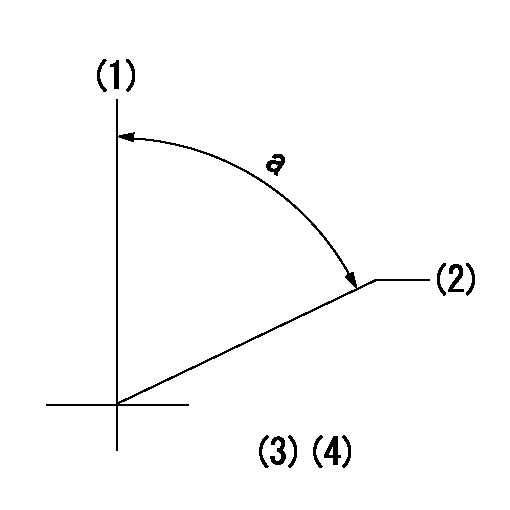
(1)Pump vertical direction
(2)Position of camshaft's key groove at No 1 cylinder's beginning of injection
(3)-
(4)-
----------
----------
a=(50deg)
----------
----------
a=(50deg)
Stop lever angle

(Rs) rack sensor specifications
(C/U) control unit part number
(V) Rack sensor output voltage
(R) Rack position (mm)
1. Confirming governor output characteristics (rack 15 mm, span 6 mm)
(1)When the output voltages of the rack sensor are V1 and V2, check that the rack positions R1 and R2 in the table above are satisfied.
----------
----------
----------
----------
Information:
Always use a wrench to hold the hex fitting on top of the master nozzle, when assembling or disassembling lines. If a wrench is not used, the master nozzle and manifold it is installed into may be damaged.
Check fuel line for "Close-in" Do NOT use fuel lines with an ID (inside diameter) LESS than 1.191 mm (0.0469 in). The fuel line ID can be checked using a 1.2 mm (.047 in) drill.If the drill bit can NOT be inserted into the fuel line high pressure hole, either drill out the line using a 1.6 mm (.063 in) drill or replace the fuel line with a new line. Use the same length and internal diameter lines each time the reference pump is tested.
If the fuel lines are not completely and thoroughly cleaned out after the drilling procedure, metal particles or foreign debris in the line will damage the master nozzles and contaminate the calibration fluid in the test stand.
After the hole has been drilled to the correct size, clean the line with solvent and remove any metal particles. Blow compressed air through the lines, after cleaning, to remove any solvent.
When using pressure air, wear a protective face shield and protective clothing. The maximum air pressure at the nozzle must be less than 205 kPa (30 psi) for cleaning purposes.
9. Identify fuel lines and nozzles in the same order as the reference pump plunger and barrels (1-6 or 1-12) and use the same lines and nozzles each time the reference pump is run on the test bench.10. Select two test points (speeds and shot settings) that will cover the delivery range realized in a dealer's shop.Always set up the test points using only the pump rack zero pin. Do not set the rack full load or idle stops.11. The test stand and reference pump should be run for ten minutes.Make sure test stand pressures and temperatures are within published specifications and that they are stable.12. Set the first test point.Take five samples (draws) and record the individual pump and barrel deliveries for each sample (draw).13. Examine pump and barrel sample data:* Are the samples consistent?The MAXIMUM allowable difference between the HIGH and LOW delivery pump and barrel in the reference pump should be three cc's.If there is NOT a three cc difference, swap pump and barrels in the pump housing (or check master nozzles for damage) and re-test UNTIL the maximum HIGH to LOW
Have questions with 101609-3080?
Group cross 101609-3080 ZEXEL
Komatsu
Komatsu
Komatsu
Komatsu
101609-3080
9 400 615 888
6221711220
INJECTION-PUMP ASSEMBLY
S6D108
S6D108