Information injection-pump assembly
BOSCH
9 400 619 604
9400619604
ZEXEL
101608-6540
1016086540
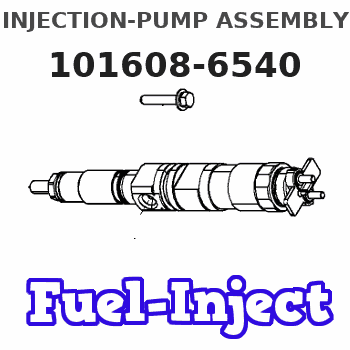
Rating:
Service parts 101608-6540 INJECTION-PUMP ASSEMBLY:
1.
_
6.
COUPLING PLATE
7.
COUPLING PLATE
8.
_
9.
_
11.
Nozzle and Holder
ME440837
12.
Open Pre:MPa(Kqf/cm2)
21.6{220}
15.
NOZZLE SET
Cross reference number
BOSCH
9 400 619 604
9400619604
ZEXEL
101608-6540
1016086540
Zexel num
Bosch num
Firm num
Name
Calibration Data:
Adjustment conditions
Test oil
1404 Test oil ISO4113 or {SAEJ967d}
1404 Test oil ISO4113 or {SAEJ967d}
Test oil temperature
degC
40
40
45
Nozzle and nozzle holder
105780-8140
Bosch type code
EF8511/9A
Nozzle
105780-0000
Bosch type code
DN12SD12T
Nozzle holder
105780-2080
Bosch type code
EF8511/9
Opening pressure
MPa
17.2
Opening pressure
kgf/cm2
175
Injection pipe
Outer diameter - inner diameter - length (mm) mm 6-2-600
Outer diameter - inner diameter - length (mm) mm 6-2-600
Overflow valve
131424-5520
Overflow valve opening pressure
kPa
255
221
289
Overflow valve opening pressure
kgf/cm2
2.6
2.25
2.95
Tester oil delivery pressure
kPa
255
255
255
Tester oil delivery pressure
kgf/cm2
2.6
2.6
2.6
Direction of rotation (viewed from drive side)
Right R
Right R
Injection timing adjustment
Direction of rotation (viewed from drive side)
Right R
Right R
Injection order
1-5-3-6-
2-4
Pre-stroke
mm
3.5
3.45
3.55
Beginning of injection position
Drive side NO.1
Drive side NO.1
Difference between angles 1
Cal 1-5 deg. 60 59.5 60.5
Cal 1-5 deg. 60 59.5 60.5
Difference between angles 2
Cal 1-3 deg. 120 119.5 120.5
Cal 1-3 deg. 120 119.5 120.5
Difference between angles 3
Cal 1-6 deg. 180 179.5 180.5
Cal 1-6 deg. 180 179.5 180.5
Difference between angles 4
Cyl.1-2 deg. 240 239.5 240.5
Cyl.1-2 deg. 240 239.5 240.5
Difference between angles 5
Cal 1-4 deg. 300 299.5 300.5
Cal 1-4 deg. 300 299.5 300.5
Injection quantity adjustment
Adjusting point
A
Rack position
8.3
Pump speed
r/min
1025
1025
1025
Average injection quantity
mm3/st.
84
83
85
Max. variation between cylinders
%
0
-2.5
2.5
Basic
*
Fixing the lever
*
Boost pressure
kPa
56
56
Boost pressure
mmHg
420
420
Injection quantity adjustment_02
Adjusting point
C
Rack position
6.4+-0.5
Pump speed
r/min
375
375
375
Average injection quantity
mm3/st.
8.5
7.2
9.8
Max. variation between cylinders
%
0
-14
14
Fixing the rack
*
Boost pressure
kPa
0
0
0
Boost pressure
mmHg
0
0
0
Injection quantity adjustment_03
Adjusting point
E
Rack position
8.5++
Pump speed
r/min
100
100
100
Average injection quantity
mm3/st.
65
65
70
Fixing the lever
*
Boost pressure
kPa
0
0
0
Boost pressure
mmHg
0
0
0
Rack limit
*
Boost compensator adjustment
Pump speed
r/min
800
800
800
Rack position
R1-0.7
Boost pressure
kPa
30.7
24
37.4
Boost pressure
mmHg
230
180
280
Boost compensator adjustment_02
Pump speed
r/min
800
800
800
Rack position
R1(8.3)
Boost pressure
kPa
46.7
44
49.4
Boost pressure
mmHg
350
330
370
Timer adjustment
Pump speed
r/min
0
Advance angle
deg.
3
2
3
Load
0/4
Timer adjustment_02
Pump speed
r/min
650+-25
Advance angle
deg.
3
2
3
Load
0/4
Remarks
Start
Start
Timer adjustment_03
Pump speed
r/min
750+-25
Advance angle
deg.
0
0
0
Load
0/4
Remarks
Finish
Finish
Test data Ex:
Governor adjustment
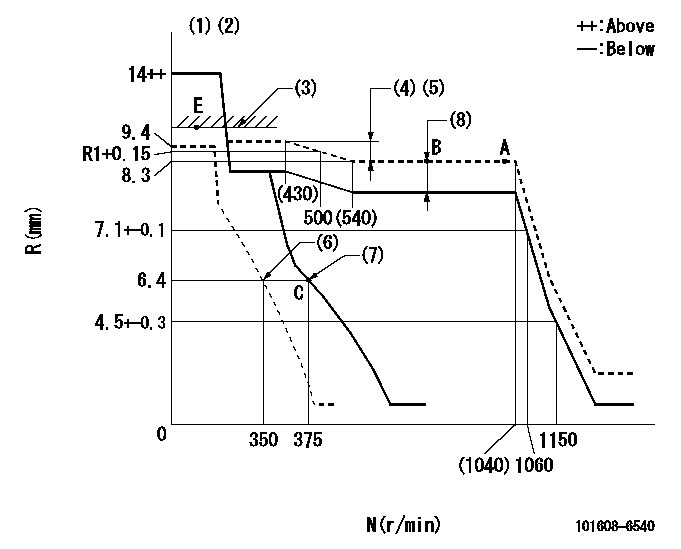
N:Pump speed
R:Rack position (mm)
(1)Target notch: K
(2)Tolerance for racks not indicated: +-0.05mm.
(3)RACK LIMIT
(4)Torque control stroke: L1
(5)Rack difference between N = N1 and N = N2
(6)Set idle sub-spring
(7)Main spring setting
(8)Boost compensator stroke: BCL
----------
K=12 L1=0.3+-0.1mm N1=800r/min N2=300r/min BCL=0.7+-0.1mm
----------
----------
K=12 L1=0.3+-0.1mm N1=800r/min N2=300r/min BCL=0.7+-0.1mm
----------
Speed control lever angle

F:Full speed
I:Idle
(1)Stopper bolt setting
(2)Base lever only
----------
----------
a=3deg+-5deg b=18deg+-5deg
----------
----------
a=3deg+-5deg b=18deg+-5deg
Stop lever angle
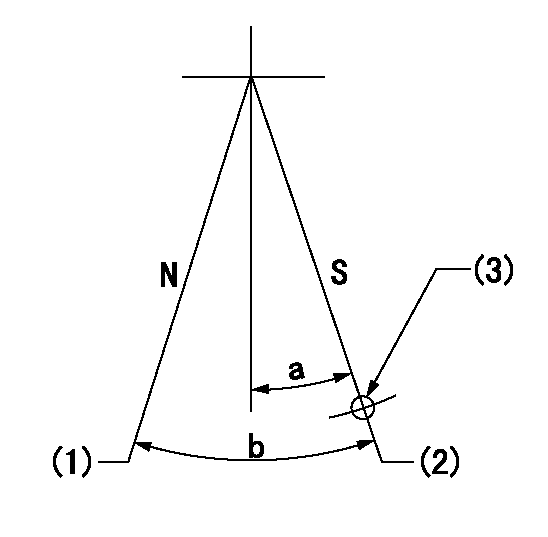
N:Pump normal
S:Stop the pump.
(1)Normal
(2)Rack position = aa, speed = bb (stamp at delivery)
(3)Use the hole above R = cc
----------
aa=1-0.5mm bb=0r/min cc=25mm
----------
a=21deg+-5deg b=(55deg)
----------
aa=1-0.5mm bb=0r/min cc=25mm
----------
a=21deg+-5deg b=(55deg)
Timing setting

(1)Pump vertical direction
(2)Position of gear mark '3' at No 1 cylinder's beginning of injection
(3)B.T.D.C.: aa
(4)-
----------
aa=10deg
----------
a=(130deg)
----------
aa=10deg
----------
a=(130deg)
Information:
Water Pump
Disassembly of Water Pump
Inspection of Water Pump
If the inspection of the impeller and shaft finds abnormal noise or rough rotation, replace the assembly.
Inspection of impeller and shaft rotation conditionThermostat
Disassembly of Thermostat
Inspection of Thermostat
To test the thermostat operation, immerse the thermostat in a container filled with water, and heat the water while measuring the water temperature. Record the temperature at which the valve starts to open and the temperature at which the valve lift becomes 8 mm [0.3 in.] or more. (a) Stir the water in the container to ensure uniform temperature distribution.(b) When installing the thermostat, be sure to check the valve opening temperature indication stamped on the upper face of the thermostat mounting flange.
Inspection of thermostatThermo Switch
Inspection of Thermo Switch
Immerse the temperature sensor in oil, and measure the resistance while increasing the oil temperature. If the temperature measurement exceeds the standard value significantly, replace the thermo switch.
Since the inspection requires heating of oil to high temperatures, be careful not to get burns or start a fire.
Inspection of thermo switch
Disassembly of Water Pump
Inspection of Water Pump
If the inspection of the impeller and shaft finds abnormal noise or rough rotation, replace the assembly.
Inspection of impeller and shaft rotation conditionThermostat
Disassembly of Thermostat
Inspection of Thermostat
To test the thermostat operation, immerse the thermostat in a container filled with water, and heat the water while measuring the water temperature. Record the temperature at which the valve starts to open and the temperature at which the valve lift becomes 8 mm [0.3 in.] or more. (a) Stir the water in the container to ensure uniform temperature distribution.(b) When installing the thermostat, be sure to check the valve opening temperature indication stamped on the upper face of the thermostat mounting flange.
Inspection of thermostatThermo Switch
Inspection of Thermo Switch
Immerse the temperature sensor in oil, and measure the resistance while increasing the oil temperature. If the temperature measurement exceeds the standard value significantly, replace the thermo switch.
Since the inspection requires heating of oil to high temperatures, be careful not to get burns or start a fire.
Inspection of thermo switch