Information injection-pump assembly
BOSCH
9 400 619 513
9400619513
ZEXEL
101608-6450
1016086450
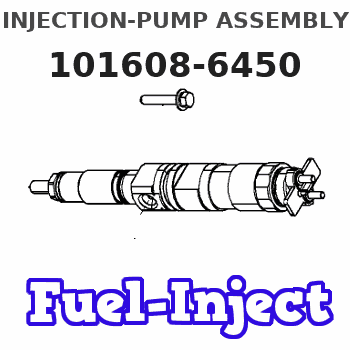
Rating:
Service parts 101608-6450 INJECTION-PUMP ASSEMBLY:
1.
_
7.
COUPLING PLATE
8.
_
9.
_
11.
Nozzle and Holder
12.
Open Pre:MPa(Kqf/cm2)
17.7{180}
15.
NOZZLE SET
Include in #1:
101608-6450
as INJECTION-PUMP ASSEMBLY
Include in #2:
104740-0860
as _
Cross reference number
BOSCH
9 400 619 513
9400619513
ZEXEL
101608-6450
1016086450
Zexel num
Bosch num
Firm num
Name
Calibration Data:
Adjustment conditions
Test oil
1404 Test oil ISO4113 or {SAEJ967d}
1404 Test oil ISO4113 or {SAEJ967d}
Test oil temperature
degC
40
40
45
Nozzle and nozzle holder
105780-8140
Bosch type code
EF8511/9A
Nozzle
105780-0000
Bosch type code
DN12SD12T
Nozzle holder
105780-2080
Bosch type code
EF8511/9
Opening pressure
MPa
17.2
Opening pressure
kgf/cm2
175
Injection pipe
Outer diameter - inner diameter - length (mm) mm 6-2-600
Outer diameter - inner diameter - length (mm) mm 6-2-600
Overflow valve
131424-5520
Overflow valve opening pressure
kPa
255
255
255
Overflow valve opening pressure
kgf/cm2
2.6
2.6
2.6
Tester oil delivery pressure
kPa
255
255
255
Tester oil delivery pressure
kgf/cm2
2.6
2.6
2.6
Direction of rotation (viewed from drive side)
Left L
Left L
Injection timing adjustment
Direction of rotation (viewed from drive side)
Left L
Left L
Injection order
1-5-3-6-
2-4
Pre-stroke
mm
4.5
4.45
4.55
Beginning of injection position
Governor side NO.1
Governor side NO.1
Difference between angles 1
Cal 1-5 deg. 60 59.5 60.5
Cal 1-5 deg. 60 59.5 60.5
Difference between angles 2
Cal 1-3 deg. 120 119.5 120.5
Cal 1-3 deg. 120 119.5 120.5
Difference between angles 3
Cal 1-6 deg. 180 179.5 180.5
Cal 1-6 deg. 180 179.5 180.5
Difference between angles 4
Cyl.1-2 deg. 240 239.5 240.5
Cyl.1-2 deg. 240 239.5 240.5
Difference between angles 5
Cal 1-4 deg. 300 299.5 300.5
Cal 1-4 deg. 300 299.5 300.5
Injection quantity adjustment
Adjusting point
A
Rack position
11.1
Pump speed
r/min
1050
1050
1050
Average injection quantity
mm3/st.
107.5
106.5
108.5
Max. variation between cylinders
%
0
-2.5
2.5
Basic
*
Fixing the lever
*
Boost pressure
kPa
65.3
65.3
Boost pressure
mmHg
490
490
Injection quantity adjustment_02
Adjusting point
-
Rack position
8+-0.5
Pump speed
r/min
495
495
495
Average injection quantity
mm3/st.
16.5
15
18
Max. variation between cylinders
%
0
-15
15
Fixing the rack
*
Boost pressure
kPa
0
0
0
Boost pressure
mmHg
0
0
0
Remarks
Adjust only variation between cylinders; adjust governor according to governor specifications.
Adjust only variation between cylinders; adjust governor according to governor specifications.
Injection quantity adjustment_03
Adjusting point
E
Rack position
11.3++
Pump speed
r/min
100
100
100
Average injection quantity
mm3/st.
105
105
115
Fixing the lever
*
Boost pressure
kPa
0
0
0
Boost pressure
mmHg
0
0
0
Rack limit
*
Boost compensator adjustment
Pump speed
r/min
375
375
375
Rack position
9.35
Boost pressure
kPa
24
17.3
30.7
Boost pressure
mmHg
180
130
230
Boost compensator adjustment_02
Pump speed
r/min
375
375
375
Rack position
10.4
Boost pressure
kPa
56
53.3
58.7
Boost pressure
mmHg
420
400
440
Timer adjustment
Pump speed
r/min
0
Advance angle
deg.
3
2.5
3.5
Load
0/4
Timer adjustment_02
Pump speed
r/min
600
Advance angle
deg.
3
2.5
3.5
Load
0/4
Remarks
Start
Start
Timer adjustment_03
Pump speed
r/min
720
Advance angle
deg.
0.5
Load
0/4
Timer adjustment_04
Pump speed
r/min
(820)
Advance angle
deg.
0
0
0
Load
4/4
Timer adjustment_05
Pump speed
r/min
1000
Advance angle
deg.
1.5
1
2
Load
4/4
Remarks
Finish
Finish
Test data Ex:
Governor adjustment
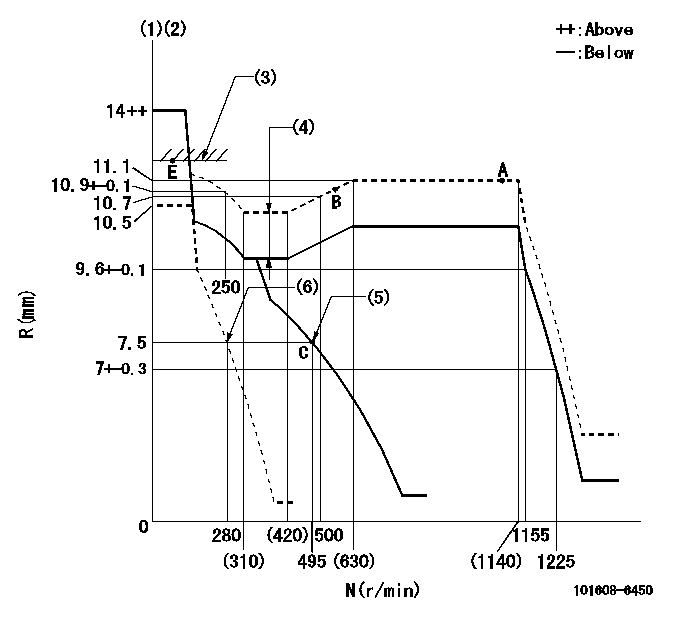
N:Pump speed
R:Rack position (mm)
(1)Target notch: K
(2)Tolerance for racks not indicated: +-0.05mm.
(3)RACK LIMIT
(4)Boost compensator stroke: BCL
(5)Main spring setting
(6)Set idle sub-spring
----------
K=9 BCL=1.05+-0.1mm
----------
----------
K=9 BCL=1.05+-0.1mm
----------
Speed control lever angle

F:Full speed
I:Idle
(1)Stopper bolt setting
----------
----------
a=18deg+-5deg b=4deg+-5deg
----------
----------
a=18deg+-5deg b=4deg+-5deg
Stop lever angle

N:Pump normal
S:Stop the pump.
(1)Normal
(2)Pump speed aa and rack position bb (to be sealed at delivery)
----------
aa=0r/min bb=1-0.5mm
----------
a=35deg+-5deg b=(55deg)
----------
aa=0r/min bb=1-0.5mm
----------
a=35deg+-5deg b=(55deg)
0000001501 TAMPER PROOF

Tamperproofing-equipped boost compensator cover installation procedure
(A) After adjusting the boost compensator, tighten the bolts to remove the heads.
(1)Before adjusting the governor and the boost compensator, tighten the screw to the specified torque.
(Tightening torque T = T1 maximum)
(2)After adjusting the governor and the boost compensator, tighten to the specified torque to break off the bolt heads.
(Tightening torque T = T2 maximum)
----------
T1=2.5N-m(0.25kgf-m) T2=2.9~4.4N-m(0.3~0.45kgf-m)
----------
----------
T1=2.5N-m(0.25kgf-m) T2=2.9~4.4N-m(0.3~0.45kgf-m)
----------
Timing setting

(1)Pump vertical direction
(2)Coupling's key groove position at No 1 cylinder's beginning of injection
(3)B.T.D.C.: aa
(4)-
----------
aa=8deg
----------
a=(0deg)
----------
aa=8deg
----------
a=(0deg)
Information:
Disassembling alternator(2) Removing Pulley(a) Wrap cloth around the rotor, then clamp the rotor in a vise. Remove the pulley nut and then the pulley and spacer.(b) Pull the rotor out of the front bracket.
Removing pulley(3) Removing Stator and Rectifier(a) Unsolder from the rectifier the leads that connect the rectifier to the stator coils. Then, remove the stator.
Unsolder the leads quickly to prevent heat from damaging the diodes.
(b) Remove the rectifier's mounting screws, then remove the rectifier.
Removing stator3.4 Inspection KEY POINTS FOR INSPECTION(1) Inspecting RectifierWith each diode, measure the resistance between the diode terminal and the heat sink. Measure the resistance with the tester's (+) probe applied to the diode terminal and with the tester's (-) probe applied to the diode terminal. If the resistance is infinite in both cases, there is an open circuit. If the resistance is close to zero in both cases, there is a short circuit. An open circuit or short circuit indicates a diode fault. Replace the rectifier if any diode is faulty.Next, measure the resistance between the terminals of the leads that connect the rectifier to the stator coil for each of the diodes. If any measurement reveals an open circuit (infinite resistance) or a short circuit (near-zero resistance), replace the rectifier.
Inspecting rectifier(2) Inspecting Field Coil(a) Check whether continuity exists between the rotor's slip rings. If continuity does not exist, the field coil is open-circuited and the rotor must be replaced.
Field coil continuity test(b) Check whether continuity exists between each slip ring and the rotor shaft (or core). If continuity exists, the field coil is grounded and the rotor must be replaced.
Field coil ground test(3) Inspecting Stator Coils(a) Check whether continuity exists between the leads at the ends of each stator coil. If continuity does not exist between any coil's leads, there is an open circuit and the stator must be replaced.
Stator coil continuity test(b) Check whether continuity exists between each stator coil lead and the stator core. If continuity exists, the stator coil is grounded and the stator must be replaced.
Stator coil ground test(4) Inspecting Brushes(a) Replace the brush if it is worn down to the wear limit line.
Inspecting brush(b) To replace the brush, remove the cover (see the drawing) then unsolder and take out the brush set.
Replacing brush3.5 AssemblyPerform assembly by following the disassembly sequence in reverse. KEY POINTS FOR ASSEMBLY(1) Heat the rear bracket before press-fitting the rear bearing into it. Do not apply oil or grease to the outer or inner surface of the bearing.(2) Before fitting the rotor in the rear bracket, insert a thin metal rod into the small hole in the rear bracket to keep the brushes raised. Remove the metal rod when assembly is complete.
Assembling alternator3.6 InstallationPerform installation by following the removal sequence in reverse. KEY POINTS FOR INSTALLATION Insertion of spacer and clearance adjustmentInstallation of the support bolt is accompanied by insertion of a spacer. Install the spacer as follows:(a) Insert the support bolt into pinion. (Do not install the nut.)(b) Install the alternator