Information injection-pump assembly
BOSCH
F 019 Z10 904
f019z10904
ZEXEL
101608-6444
1016086444
MITSUBISHI
ME441273
me441273
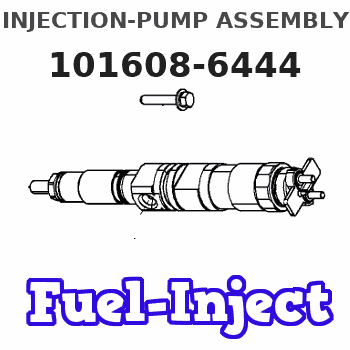
Rating:
Compare Prices: .
As an associate, we earn commssions on qualifying purchases through the links below
Fuel Pump 101608-6444 Engine Oil Pump
DFGUFG [OE NO. & Part NO] 101608-6444 || [Product Name and Model] Fuel Injection Pump || [Easy Installation] Standardized interface design, no additional modification required, simple and quick installation process, users can easily complete replacement and maintenance. || [Quality Assurance] Products undergo rigorous quality testing to ensure reliable performance and high-quality after-sales service, so you have no worries. || [Reliable Performance] Provides excellent fuel injection performance, optimizes engine operating efficiency, and helps equipment operate stably for a long time.
DFGUFG [OE NO. & Part NO] 101608-6444 || [Product Name and Model] Fuel Injection Pump || [Easy Installation] Standardized interface design, no additional modification required, simple and quick installation process, users can easily complete replacement and maintenance. || [Quality Assurance] Products undergo rigorous quality testing to ensure reliable performance and high-quality after-sales service, so you have no worries. || [Reliable Performance] Provides excellent fuel injection performance, optimizes engine operating efficiency, and helps equipment operate stably for a long time.
Service parts 101608-6444 INJECTION-PUMP ASSEMBLY:
1.
_
6.
COUPLING PLATE
7.
COUPLING PLATE
8.
_
9.
_
11.
Nozzle and Holder
ME440837
12.
Open Pre:MPa(Kqf/cm2)
21.6(220)
15.
NOZZLE SET
Include in #1:
101608-6444
as INJECTION-PUMP ASSEMBLY
Include in #2:
104761-0031
as _
Cross reference number
BOSCH
F 019 Z10 904
f019z10904
ZEXEL
101608-6444
1016086444
MITSUBISHI
ME441273
me441273
Zexel num
Bosch num
Firm num
Name
101608-6444
F 019 Z10 904
ME441273 MITSUBISHI
INJECTION-PUMP ASSEMBLY
6D34TL K 14BE INJECTION PUMP ASSY PE6A PE
6D34TL K 14BE INJECTION PUMP ASSY PE6A PE
Calibration Data:
Adjustment conditions
Test oil
1404 Test oil ISO4113 or {SAEJ967d}
1404 Test oil ISO4113 or {SAEJ967d}
Test oil temperature
degC
40
40
45
Nozzle and nozzle holder
105780-8140
Bosch type code
EF8511/9A
Nozzle
105780-0000
Bosch type code
DN12SD12T
Nozzle holder
105780-2080
Bosch type code
EF8511/9
Opening pressure
MPa
17.2
Opening pressure
kgf/cm2
175
Injection pipe
Outer diameter - inner diameter - length (mm) mm 6-2-600
Outer diameter - inner diameter - length (mm) mm 6-2-600
Overflow valve
131424-5520
Overflow valve opening pressure
kPa
255
221
289
Overflow valve opening pressure
kgf/cm2
2.6
2.25
2.95
Tester oil delivery pressure
kPa
255
255
255
Tester oil delivery pressure
kgf/cm2
2.6
2.6
2.6
Direction of rotation (viewed from drive side)
Right R
Right R
Injection timing adjustment
Direction of rotation (viewed from drive side)
Right R
Right R
Injection order
1-5-3-6-
2-4
Pre-stroke
mm
3.5
3.45
3.55
Beginning of injection position
Drive side NO.1
Drive side NO.1
Difference between angles 1
Cal 1-5 deg. 60 59.5 60.5
Cal 1-5 deg. 60 59.5 60.5
Difference between angles 2
Cal 1-3 deg. 120 119.5 120.5
Cal 1-3 deg. 120 119.5 120.5
Difference between angles 3
Cal 1-6 deg. 180 179.5 180.5
Cal 1-6 deg. 180 179.5 180.5
Difference between angles 4
Cyl.1-2 deg. 240 239.5 240.5
Cyl.1-2 deg. 240 239.5 240.5
Difference between angles 5
Cal 1-4 deg. 300 299.5 300.5
Cal 1-4 deg. 300 299.5 300.5
Injection quantity adjustment
Adjusting point
A
Rack position
10.3
Pump speed
r/min
1000
1000
1000
Average injection quantity
mm3/st.
85.5
84.5
86.5
Max. variation between cylinders
%
0
-2.5
2.5
Basic
*
Fixing the lever
*
Boost pressure
kPa
66
66
Boost pressure
mmHg
495
495
Injection quantity adjustment_02
Adjusting point
-
Rack position
7.9+-0.5
Pump speed
r/min
490
490
490
Average injection quantity
mm3/st.
8
6.7
9.3
Max. variation between cylinders
%
0
-14
14
Fixing the rack
*
Boost pressure
kPa
0
0
0
Boost pressure
mmHg
0
0
0
Remarks
Adjust only variation between cylinders; adjust governor according to governor specifications.
Adjust only variation between cylinders; adjust governor according to governor specifications.
Injection quantity adjustment_03
Adjusting point
E
Rack position
10.8++
Pump speed
r/min
100
100
100
Average injection quantity
mm3/st.
70
70
75
Fixing the lever
*
Boost pressure
kPa
0
0
0
Boost pressure
mmHg
0
0
0
Rack limit
*
Boost compensator adjustment
Pump speed
r/min
750
750
750
Rack position
R1-0.8
Boost pressure
kPa
28
21.3
34.7
Boost pressure
mmHg
210
160
260
Boost compensator adjustment_02
Pump speed
r/min
750
750
750
Rack position
R1(10.3)
Boost pressure
kPa
56.7
54
59.4
Boost pressure
mmHg
425
405
445
Timer adjustment
Pump speed
r/min
0
Advance angle
deg.
3
2
3
Load
0/4
Timer adjustment_02
Pump speed
r/min
650+-25
Advance angle
deg.
3
2
3
Load
0/4
Remarks
Start
Start
Timer adjustment_03
Pump speed
r/min
750+-25
Advance angle
deg.
0
0
0
Load
0/4
Remarks
Finish
Finish
Test data Ex:
Governor adjustment
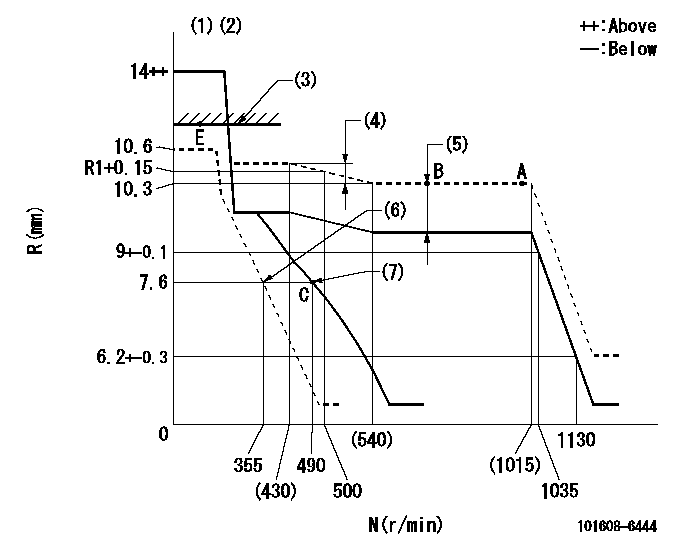
N:Pump speed
R:Rack position (mm)
(1)Target notch: K
(2)Tolerance for racks not indicated: +-0.05mm.
(3)RACK LIMIT
(4)Torque control stroke: L1 (N = N1 and N = N2 rack difference).
(5)Boost compensator stroke: BCL
(6)Set idle sub-spring
(7)Main spring setting
----------
K=9 L1=0.3+-0.1mm N1=750r/min N2=300r/min BCL=0.8+-0.1mm
----------
----------
K=9 L1=0.3+-0.1mm N1=750r/min N2=300r/min BCL=0.8+-0.1mm
----------
Speed control lever angle
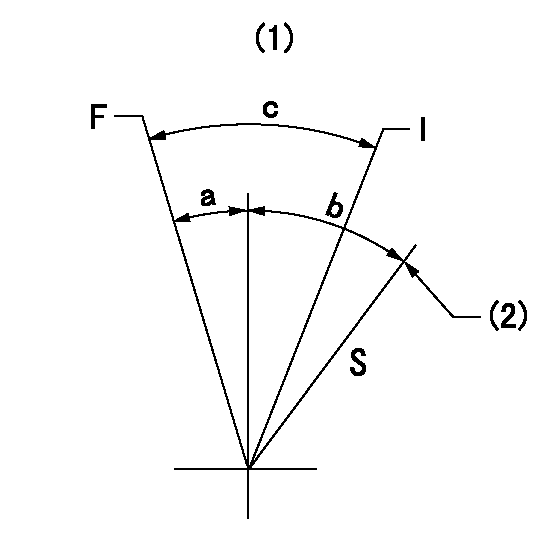
F:Full speed
I:Idle
S:Stop
(1)Base lever only
(2)Stopper bolt setting
----------
----------
a=3deg+-5deg b=35deg+-3deg c=15deg+-5deg
----------
----------
a=3deg+-5deg b=35deg+-3deg c=15deg+-5deg
Stop lever angle
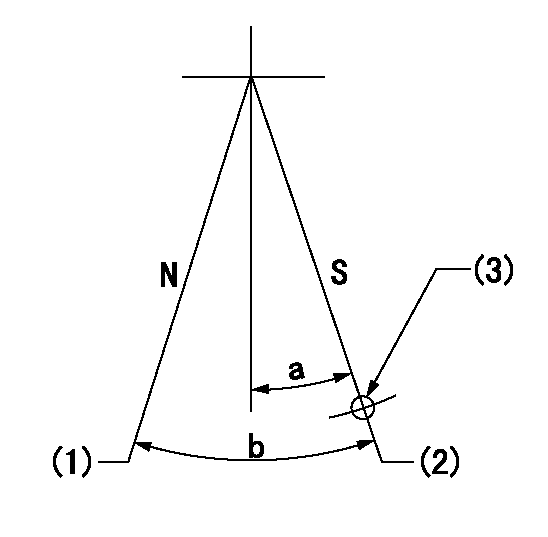
N:Pump normal
S:Stop the pump.
(1)Normal
(2)Rack position = aa, speed = bb (stamp at delivery)
(3)Use the hole above R = cc
----------
aa=4-0.5mm bb=0r/min cc=25mm
----------
a=14deg+-5deg b=(48deg)
----------
aa=4-0.5mm bb=0r/min cc=25mm
----------
a=14deg+-5deg b=(48deg)
0000001501 TAMPER PROOF

Tamperproofing-equipped boost compensator cover installation procedure
(A) After adjusting the boost compensator, tighten the bolts to remove the heads.
(1)Before adjusting the governor and the boost compensator, tighten the screw to the specified torque.
(Tightening torque T = T1 maximum)
(2)After adjusting the governor and the boost compensator, tighten to the specified torque to break off the bolt heads.
(Tightening torque T = T2)
----------
T1=2.5N-m(0.25kgf-m) T2=2.9~4.4N-m(0.3~0.45kgf-m)
----------
----------
T1=2.5N-m(0.25kgf-m) T2=2.9~4.4N-m(0.3~0.45kgf-m)
----------
Timing setting

(1)Pump vertical direction
(2)Position of gear mark '3' at No 1 cylinder's beginning of injection
(3)B.T.D.C.: aa
(4)-
----------
aa=10deg
----------
a=(130deg)
----------
aa=10deg
----------
a=(130deg)
Information:
Injection timing adjustment shim
Adjusting injection timing(3) Alternative Adjustment/Inspection ProcedureThe injection timing adjustment/inspection procedure in which the delivery valve is removed allows the flow of fuel to be verified clearly, but removing the delivery valve can allow dirt to enter the fuel system. With the procedure described below, it is possible to check the injection timing without removing the delivery valve.(a) Disconnect injection pipe No. 1 from the nozzle holder.
Disconnecting injection pipe No. 1(b) Slowly turn the crankshaft clockwise, and note the position of the IT mark at the point in time when fuel emerges from the end of the pipe. The timing indicated by the IT mark is retarded by approximately 1° relative to the actual injection timing, so this 1° difference must be taken into account in the shim selection. Air-bleed the fuel system before turning the crankshaft. 4. Injectors
4.1 Removal
Removing and installing injectors1 Fuel injection pipe2 Injector holder3 Injector4 Gasket
The fuel injection pipe nut should be tightened to the specified torque using a tool specially designed for the purpose.
4.2 Inspection and AdjustmentCheck each injector for the following points. If the result is not satisfactory, either repair or replace it according to conditions.(1) Injector Valve Opening Pressure(a) Install an injector on an injector tester. Move the handle up and down repeatedly to remove air from the injector.(b) While observing the pressure gauge, operate the handle at a rate of approximately one stroke per second. Record the reading.
Testing injector valve opening pressure The needle of the gauge moves slowly toward the higher pressure side and then wobbles while injection is taking place. Injector valve opening pressure corresponds to a pressure at which the gauge needle starts wobbling.(c) If the reading on the gauge does not correspond to the specified injector valve opening pressure of 21.6+10 MPa {220+100kgf/cm2} (3130+1420 psi), disassemble the injector and replace the washer with one of proper thickness.(d) A change of 0.1 mm (0.004 in.) in the washer thickness yields a change of 1.5 MPa {15 kgf/cm2} (213 psi).
Never expose any part of your body to the spray of fuel injected from the injector.
Adjusting injector valve opening pressure(2) Spray Condition(a) Operate the injector tester handle at a rate of approximately one stroke per second.(b) The spray pattern A in the drawing on the right is normal while all the other patterns are abnormal. The spray may be coarse and narrow, and some fuel may remain on the nozzle hole after injection. However, these conditions are typically observed during tests on a tester and thus do not indicate abnormal operation of the injector.(c) Operate the tester handle at a rate of approximately four to six strokes per second. The injector can be considered normal if fuel is injected evenly and at correct angles (see drawing) from all the four nozzle holes and fine atomization of fuel is observed in all sprays.
Inspecting spray condition(3) Leakage from InjectorsUse the injector tester to maintain a pressure 1-2 MPa {10-20 kgf/cm2} (142-285 psi) lower than the specified injector valve opening
Have questions with 101608-6444?
Group cross 101608-6444 ZEXEL
Mitsubishi
101608-6444
F 019 Z10 904
ME441273
INJECTION-PUMP ASSEMBLY
6D34TL
6D34TL