Information injection-pump assembly
BOSCH
9 400 612 921
9400612921
ZEXEL
101608-6441
1016086441
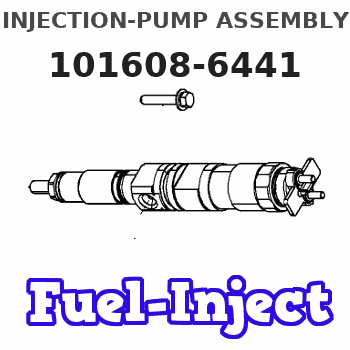
Rating:
Service parts 101608-6441 INJECTION-PUMP ASSEMBLY:
1.
_
6.
COUPLING PLATE
7.
COUPLING PLATE
8.
_
9.
_
11.
Nozzle and Holder
ME440837
12.
Open Pre:MPa(Kqf/cm2)
21.6{220}
15.
NOZZLE SET
Include in #1:
101608-6441
as INJECTION-PUMP ASSEMBLY
Include in #2:
104740-0852
as _
Cross reference number
BOSCH
9 400 612 921
9400612921
ZEXEL
101608-6441
1016086441
Zexel num
Bosch num
Firm num
Name
Calibration Data:
Adjustment conditions
Test oil
1404 Test oil ISO4113 or {SAEJ967d}
1404 Test oil ISO4113 or {SAEJ967d}
Test oil temperature
degC
40
40
45
Nozzle and nozzle holder
105780-8140
Bosch type code
EF8511/9A
Nozzle
105780-0000
Bosch type code
DN12SD12T
Nozzle holder
105780-2080
Bosch type code
EF8511/9
Opening pressure
MPa
17.2
Opening pressure
kgf/cm2
175
Injection pipe
Outer diameter - inner diameter - length (mm) mm 6-2-600
Outer diameter - inner diameter - length (mm) mm 6-2-600
Overflow valve
131424-5520
Overflow valve opening pressure
kPa
255
221
289
Overflow valve opening pressure
kgf/cm2
2.6
2.25
2.95
Tester oil delivery pressure
kPa
255
255
255
Tester oil delivery pressure
kgf/cm2
2.6
2.6
2.6
Direction of rotation (viewed from drive side)
Right R
Right R
Injection timing adjustment
Direction of rotation (viewed from drive side)
Right R
Right R
Injection order
1-5-3-6-
2-4
Pre-stroke
mm
3.5
3.45
3.55
Beginning of injection position
Drive side NO.1
Drive side NO.1
Difference between angles 1
Cal 1-5 deg. 60 59.5 60.5
Cal 1-5 deg. 60 59.5 60.5
Difference between angles 2
Cal 1-3 deg. 120 119.5 120.5
Cal 1-3 deg. 120 119.5 120.5
Difference between angles 3
Cal 1-6 deg. 180 179.5 180.5
Cal 1-6 deg. 180 179.5 180.5
Difference between angles 4
Cyl.1-2 deg. 240 239.5 240.5
Cyl.1-2 deg. 240 239.5 240.5
Difference between angles 5
Cal 1-4 deg. 300 299.5 300.5
Cal 1-4 deg. 300 299.5 300.5
Injection quantity adjustment
Adjusting point
A
Rack position
8.3
Pump speed
r/min
1000
1000
1000
Average injection quantity
mm3/st.
83.5
82.5
84.5
Max. variation between cylinders
%
0
-2.5
2.5
Basic
*
Fixing the lever
*
Boost pressure
kPa
69.3
69.3
Boost pressure
mmHg
520
520
Injection quantity adjustment_02
Adjusting point
-
Rack position
6+-0.5
Pump speed
r/min
475
475
475
Average injection quantity
mm3/st.
8
6.7
9.3
Max. variation between cylinders
%
0
-14
14
Fixing the rack
*
Boost pressure
kPa
0
0
0
Boost pressure
mmHg
0
0
0
Remarks
Adjust only variation between cylinders; adjust governor according to governor specifications.
Adjust only variation between cylinders; adjust governor according to governor specifications.
Injection quantity adjustment_03
Adjusting point
E
Rack position
8.5++
Pump speed
r/min
100
100
100
Average injection quantity
mm3/st.
65
65
70
Fixing the lever
*
Boost pressure
kPa
0
0
0
Boost pressure
mmHg
0
0
0
Rack limit
*
Boost compensator adjustment
Pump speed
r/min
800
800
800
Rack position
R1-0.9
Boost pressure
kPa
30.7
24
37.4
Boost pressure
mmHg
230
180
280
Boost compensator adjustment_02
Pump speed
r/min
800
800
800
Rack position
R1(8.3)
Boost pressure
kPa
60
57.3
62.7
Boost pressure
mmHg
450
430
470
Timer adjustment
Pump speed
r/min
0
Load
0/4
Remarks
Measure the actual advance angle.
Measure the actual advance angle.
Timer adjustment_02
Pump speed
r/min
650+-25
Load
0/4
Remarks
Measure the actual advance angle (beginning of advance).
Measure the actual advance angle (beginning of advance).
Timer adjustment_03
Pump speed
r/min
750+-25
Advance angle
deg.
0
0
0
Load
0/4
Remarks
Finish
Finish
Test data Ex:
Governor adjustment
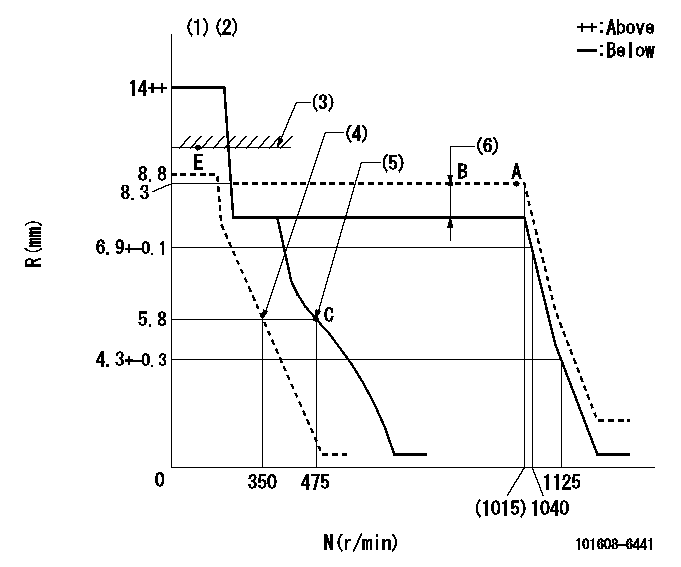
N:Pump speed
R:Rack position (mm)
(1)Target notch: K
(2)Tolerance for racks not indicated: +-0.05mm.
(3)RACK LIMIT
(4)Set idle sub-spring
(5)Main spring setting
(6)Boost compensator stroke: BCL
----------
K=14 BCL=0.9+-0.1mm
----------
----------
K=14 BCL=0.9+-0.1mm
----------
Speed control lever angle
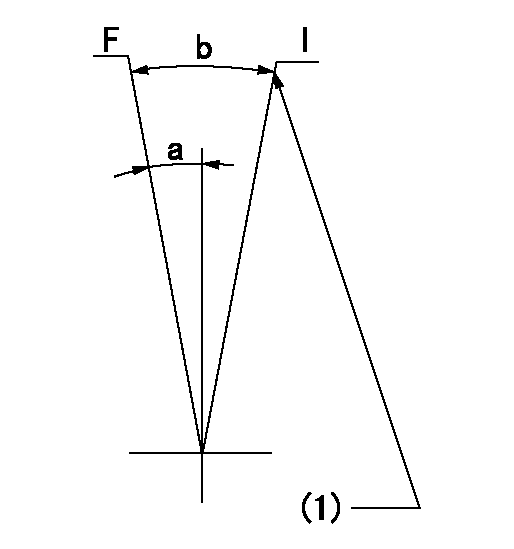
F:Full speed
I:Idle
(1)Stopper bolt setting
----------
----------
a=4deg+-5deg b=16deg+-5deg
----------
----------
a=4deg+-5deg b=16deg+-5deg
Stop lever angle
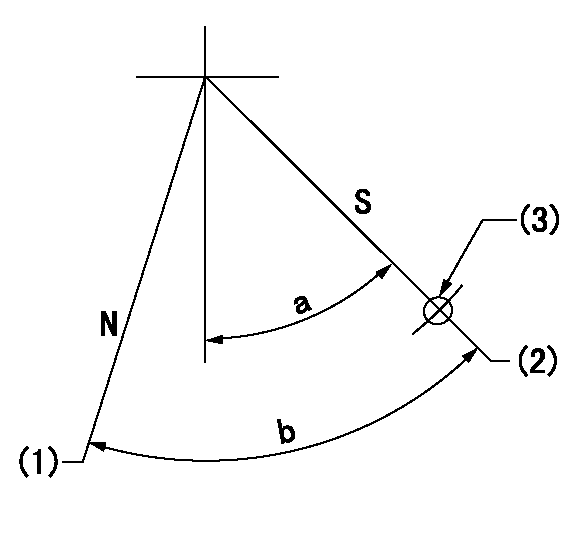
N:Pump normal
S:Stop the pump.
(1)Normal
(2)Rack position = aa, speed = bb (stamp at delivery)
(3)Use the hole above R = cc
----------
aa=1-0.5mm bb=0r/min cc=25mm
----------
a=21deg+-5deg b=(55deg)
----------
aa=1-0.5mm bb=0r/min cc=25mm
----------
a=21deg+-5deg b=(55deg)
0000001501 TAMPER PROOF

Tamperproofing-equipped boost compensator cover installation procedure
(A) After adjusting the boost compensator, tighten the bolts to remove the heads.
(1)Before adjusting the governor and the boost compensator, tighten the screw to the specified torque.
(Tightening torque T = T1 maximum)
(2)After adjusting the governor and the boost compensator, tighten to the specified torque to break off the bolt heads.
(Tightening torque T = T2)
----------
T1=2.5N-m(0.25kgf-m) T2=2.9~4.4N-m(0.3~0.45kgf-m)
----------
----------
T1=2.5N-m(0.25kgf-m) T2=2.9~4.4N-m(0.3~0.45kgf-m)
----------
Timing setting

(1)Pump vertical direction
(2)Position of gear mark '3' at No 1 cylinder's beginning of injection
(3)B.T.D.C.: aa
(4)-
----------
aa=10deg
----------
a=(130deg)
----------
aa=10deg
----------
a=(130deg)
Information:
5.3 Assembly
Assembly sequence: piston and connecting rod assemblies and crankshaftThe assembly sequence is indicated by the numbers in the drawing above. KEY POINTS FOR ASSEMBLY(1) Installing Main Bearings(a) Press the main bearings (upper and lower) into the cylinder block and main bearing caps, respectively, such that the bearings' lugs fit into the grooves.
Installing main bearings(b) Fit the flanged main bearing in the No. 3 journal position.(c) Smear a little engine oil on the inner surface of each bearing.
Installing flanged main bearing(2) Installing Crankshaft(a) Wash the crankshaft thoroughly in cleaning solvent, then dry it with compressed air.(b) Keeping the crankshaft horizontal, gently lower it into the cylinder block.(c) Smear a little engine oil on each crankshaft journal.
Installing crankshaft(3) Installing Main Bearing Caps(a) Before installing the main bearing caps, apply sealant to the mating surfaces of the frontmost and rearmost caps and to the corresponding surfaces in the cylinder block.
Installing main bearing caps(b) Referring to the cap numbers, fit the main bearing caps sequentially starting at the front of the engine. The arrow on each cap must point toward the front of the engine.
Make sure the frontmost and rearmost caps fit flush against the cylinder block.
Front marks and cap numbers(4) Tightening Bearing Cap BoltsTighten the bearing cap bolts alternately a little at a time, then torque each bolt to specification.
Tightening bearing cap bolts(5) Checking Crankshaft RotationConfirm that the crankshaft turns smoothly.
Checking crankshaft rotation(6) Measuring End Play of CrankshaftApply a dial gauge to the end of the crankshaft and measure the end play. If the measurement exceeds the specified limit, replace the No. 3 flanged bearing.
Unit: mm (in.)
Measuring end play of crankshaft(7) Inserting Side Seals(a) Apply sealant to the mating surfaces of each side seal. (b) With the radius of each side seal facing the outside, push the side seals part-way into the frontmost and rearmost caps by hand.
Alignment of side seals for installation(c) Press each side seal completely into position using a flat implement. Be careful not to bend the side seals.
Inserting side seals(8) Preparation for Installation of Piston and Connecting Rod Assemblies(a) Clean each cylinder's inner surface with a rag, then smear each with engine oil.(b) Press the connecting rod bearings (upper and lower) into the connecting rods and caps such that the bearings' lugs fit into the grooves.(c) Smear the connecting rod bearings with engine oil.(d) Turn the cylinder block onto its side.
Preparation for installation of piston and connecting rod assemblies(9) Preparation for Installation of Piston and Connecting Rod Assemblies(a) Smear the pistons' sliding surfaces and piston rings with engine oil.(b) Position the piston ring gaps as shown in the drawing. Do not align any ring gap with the piston pin or at 90° to the piston pin.
Piston ring positions(c) Turn the crankshaft until the crank pin onto which the connecting rod is to be fitted reaches its TDC position.(d) Align the piston such that its front mark (this is stamped on the piston crown) points toward the timing gear case mounting surface (the front of the engine).(e)
Assembly sequence: piston and connecting rod assemblies and crankshaftThe assembly sequence is indicated by the numbers in the drawing above. KEY POINTS FOR ASSEMBLY(1) Installing Main Bearings(a) Press the main bearings (upper and lower) into the cylinder block and main bearing caps, respectively, such that the bearings' lugs fit into the grooves.
Installing main bearings(b) Fit the flanged main bearing in the No. 3 journal position.(c) Smear a little engine oil on the inner surface of each bearing.
Installing flanged main bearing(2) Installing Crankshaft(a) Wash the crankshaft thoroughly in cleaning solvent, then dry it with compressed air.(b) Keeping the crankshaft horizontal, gently lower it into the cylinder block.(c) Smear a little engine oil on each crankshaft journal.
Installing crankshaft(3) Installing Main Bearing Caps(a) Before installing the main bearing caps, apply sealant to the mating surfaces of the frontmost and rearmost caps and to the corresponding surfaces in the cylinder block.
Installing main bearing caps(b) Referring to the cap numbers, fit the main bearing caps sequentially starting at the front of the engine. The arrow on each cap must point toward the front of the engine.
Make sure the frontmost and rearmost caps fit flush against the cylinder block.
Front marks and cap numbers(4) Tightening Bearing Cap BoltsTighten the bearing cap bolts alternately a little at a time, then torque each bolt to specification.
Tightening bearing cap bolts(5) Checking Crankshaft RotationConfirm that the crankshaft turns smoothly.
Checking crankshaft rotation(6) Measuring End Play of CrankshaftApply a dial gauge to the end of the crankshaft and measure the end play. If the measurement exceeds the specified limit, replace the No. 3 flanged bearing.
Unit: mm (in.)
Measuring end play of crankshaft(7) Inserting Side Seals(a) Apply sealant to the mating surfaces of each side seal. (b) With the radius of each side seal facing the outside, push the side seals part-way into the frontmost and rearmost caps by hand.
Alignment of side seals for installation(c) Press each side seal completely into position using a flat implement. Be careful not to bend the side seals.
Inserting side seals(8) Preparation for Installation of Piston and Connecting Rod Assemblies(a) Clean each cylinder's inner surface with a rag, then smear each with engine oil.(b) Press the connecting rod bearings (upper and lower) into the connecting rods and caps such that the bearings' lugs fit into the grooves.(c) Smear the connecting rod bearings with engine oil.(d) Turn the cylinder block onto its side.
Preparation for installation of piston and connecting rod assemblies(9) Preparation for Installation of Piston and Connecting Rod Assemblies(a) Smear the pistons' sliding surfaces and piston rings with engine oil.(b) Position the piston ring gaps as shown in the drawing. Do not align any ring gap with the piston pin or at 90° to the piston pin.
Piston ring positions(c) Turn the crankshaft until the crank pin onto which the connecting rod is to be fitted reaches its TDC position.(d) Align the piston such that its front mark (this is stamped on the piston crown) points toward the timing gear case mounting surface (the front of the engine).(e)