Information injection-pump assembly
BOSCH
9 400 619 509
9400619509
ZEXEL
101608-6411
1016086411
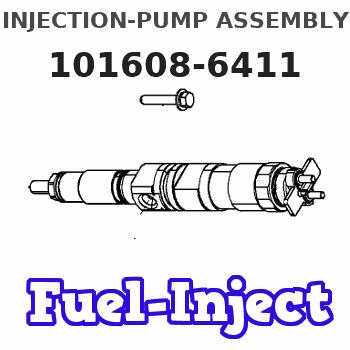
Rating:
Service parts 101608-6411 INJECTION-PUMP ASSEMBLY:
1.
_
6.
COUPLING PLATE
7.
COUPLING PLATE
8.
_
9.
_
11.
Nozzle and Holder
ME440837
12.
Open Pre:MPa(Kqf/cm2)
21.6{220}
15.
NOZZLE SET
Include in #1:
101608-6411
as INJECTION-PUMP ASSEMBLY
Include in #2:
104740-0810
as _
Cross reference number
BOSCH
9 400 619 509
9400619509
ZEXEL
101608-6411
1016086411
Zexel num
Bosch num
Firm num
Name
Calibration Data:
Adjustment conditions
Test oil
1404 Test oil ISO4113 or {SAEJ967d}
1404 Test oil ISO4113 or {SAEJ967d}
Test oil temperature
degC
40
40
45
Nozzle and nozzle holder
105780-8140
Bosch type code
EF8511/9A
Nozzle
105780-0000
Bosch type code
DN12SD12T
Nozzle holder
105780-2080
Bosch type code
EF8511/9
Opening pressure
MPa
17.2
Opening pressure
kgf/cm2
175
Injection pipe
Outer diameter - inner diameter - length (mm) mm 6-2-600
Outer diameter - inner diameter - length (mm) mm 6-2-600
Overflow valve
131424-5520
Overflow valve opening pressure
kPa
255
221
289
Overflow valve opening pressure
kgf/cm2
2.6
2.25
2.95
Tester oil delivery pressure
kPa
255
255
255
Tester oil delivery pressure
kgf/cm2
2.6
2.6
2.6
Direction of rotation (viewed from drive side)
Right R
Right R
Injection timing adjustment
Direction of rotation (viewed from drive side)
Right R
Right R
Injection order
1-5-3-6-
2-4
Pre-stroke
mm
3.2
3.15
3.25
Beginning of injection position
Drive side NO.1
Drive side NO.1
Difference between angles 1
Cal 1-5 deg. 60 59.5 60.5
Cal 1-5 deg. 60 59.5 60.5
Difference between angles 2
Cal 1-3 deg. 120 119.5 120.5
Cal 1-3 deg. 120 119.5 120.5
Difference between angles 3
Cal 1-6 deg. 180 179.5 180.5
Cal 1-6 deg. 180 179.5 180.5
Difference between angles 4
Cyl.1-2 deg. 240 239.5 240.5
Cyl.1-2 deg. 240 239.5 240.5
Difference between angles 5
Cal 1-4 deg. 300 299.5 300.5
Cal 1-4 deg. 300 299.5 300.5
Injection quantity adjustment
Adjusting point
A
Rack position
8.9
Pump speed
r/min
1075
1075
1075
Average injection quantity
mm3/st.
103
102
104
Max. variation between cylinders
%
0
-2.5
2.5
Basic
*
Fixing the lever
*
Boost pressure
kPa
66.7
66.7
Boost pressure
mmHg
500
500
Injection quantity adjustment_02
Adjusting point
-
Rack position
6.2+-0.5
Pump speed
r/min
475
475
475
Average injection quantity
mm3/st.
8
6.7
9.3
Max. variation between cylinders
%
0
-14
14
Fixing the rack
*
Boost pressure
kPa
0
0
0
Boost pressure
mmHg
0
0
0
Remarks
Adjust only variation between cylinders; adjust governor according to governor specifications.
Adjust only variation between cylinders; adjust governor according to governor specifications.
Injection quantity adjustment_03
Adjusting point
E
Rack position
9.1++
Pump speed
r/min
100
100
100
Average injection quantity
mm3/st.
65
65
70
Fixing the lever
*
Boost pressure
kPa
0
0
0
Boost pressure
mmHg
0
0
0
Rack limit
*
Boost compensator adjustment
Pump speed
r/min
750
750
750
Rack position
R1-1.3
Boost pressure
kPa
10.7
4
17.4
Boost pressure
mmHg
80
30
130
Boost compensator adjustment_02
Pump speed
r/min
750
750
750
Rack position
R1(8.9)
Boost pressure
kPa
57.3
54.6
60
Boost pressure
mmHg
430
410
450
Timer adjustment
Pump speed
r/min
0
Advance angle
deg.
3
2.5
3.5
Timer adjustment_02
Pump speed
r/min
-
Advance angle
deg.
3
2.5
3.5
Remarks
Measure speed (beginning of operation).
Measure speed (beginning of operation).
Timer adjustment_03
Pump speed
r/min
750+-25
Advance angle
deg.
0
0
0
Remarks
Finish
Finish
Test data Ex:
Governor adjustment
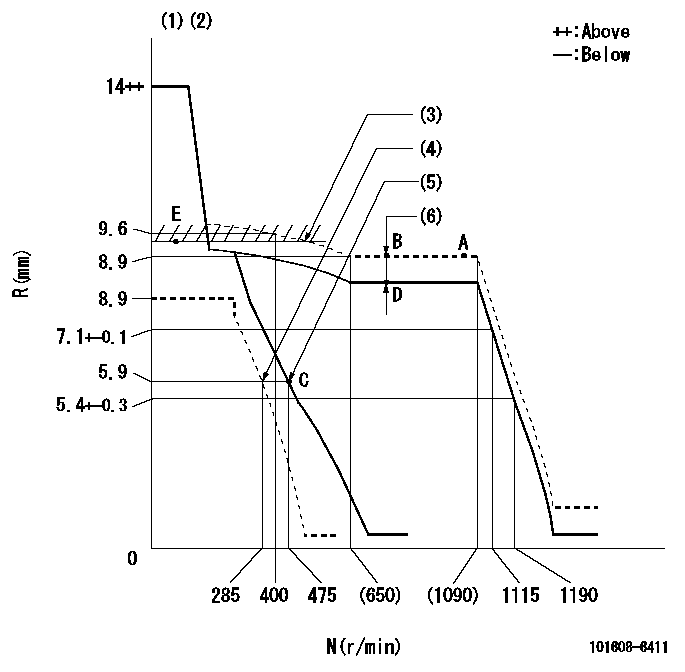
N:Pump speed
R:Rack position (mm)
(1)Target notch: K
(2)Tolerance for racks not indicated: +-0.05mm.
(3)RACK LIMIT
(4)Set idle sub-spring
(5)Main spring setting
(6)Boost compensator stroke: BCL
----------
K=19 BCL=1.3+-0.1mm
----------
----------
K=19 BCL=1.3+-0.1mm
----------
Speed control lever angle
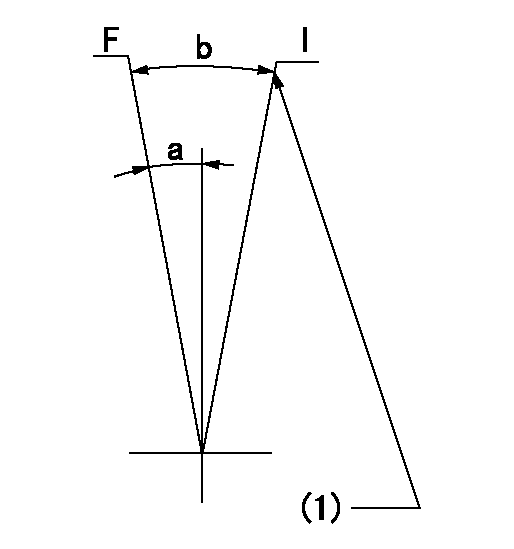
F:Full speed
I:Idle
(1)Stopper bolt setting
----------
----------
a=12deg+-5deg b=19deg+-5deg
----------
----------
a=12deg+-5deg b=19deg+-5deg
Stop lever angle

N:Pump normal
S:Stop the pump.
(1)Pump speed aa and rack position bb (to be sealed at delivery)
(2)Normal
----------
aa=0r/min bb=1-0.5mm
----------
a=21deg+-5deg b=(55deg)
----------
aa=0r/min bb=1-0.5mm
----------
a=21deg+-5deg b=(55deg)
Timing setting

(1)Pump vertical direction
(2)Position of gear mark '3' at No 1 cylinder's beginning of injection
(3)B.T.D.C.: aa
(4)-
----------
aa=8deg
----------
a=(130deg)
----------
aa=8deg
----------
a=(130deg)
Information:
GENERAL
1. Schematic
Schematic2. Specifications (standard) INSPECTION
Inspection points1. Water pump Check the impeller and shaft for rotation. If they do not rotate freely or have noise, replace the water pump assembly.
Checking water pump2. Thermostat (standard) Hang the thermostat in the pan of water as shown in the illustration. The thermostat must be below the surface of the water and its must be away from the sides of the pan. Heat the water uniformly in the pan and measure a temperature at which the valve starts opening and a temperature at which the valve lift (distance) is 8 mm (0.3 in.). Replace the thermostat if defective.
Water in the pan is hot. Any contact can cause severe burns.
Testing thermostat3. Thermoswitch (standard) Hang the thermoswitch in the pan of oil with its temperature sensing end below the surface of oil and measure the resistance while heating the oil as shown in the illustration. If the resistance is incorrect, replace the thermoswitch.
Oil in the pan is hot. Any contact can cause severe burns.
Testing thermoswitch4. Thermounit (standard) Hang the thermounit in the pan of antifreeze with its temperature sensing end below the surface of antifreeze and measure the resistance while heating the antifreeze as shown in the illustration. If the resistance is incorrect, replace the thermounit.
Antifreeze in the pan is hot. Any contact can cause severe burns.
Testing thermounit
1. Schematic
Schematic2. Specifications (standard) INSPECTION
Inspection points1. Water pump Check the impeller and shaft for rotation. If they do not rotate freely or have noise, replace the water pump assembly.
Checking water pump2. Thermostat (standard) Hang the thermostat in the pan of water as shown in the illustration. The thermostat must be below the surface of the water and its must be away from the sides of the pan. Heat the water uniformly in the pan and measure a temperature at which the valve starts opening and a temperature at which the valve lift (distance) is 8 mm (0.3 in.). Replace the thermostat if defective.
Water in the pan is hot. Any contact can cause severe burns.
Testing thermostat3. Thermoswitch (standard) Hang the thermoswitch in the pan of oil with its temperature sensing end below the surface of oil and measure the resistance while heating the oil as shown in the illustration. If the resistance is incorrect, replace the thermoswitch.
Oil in the pan is hot. Any contact can cause severe burns.
Testing thermoswitch4. Thermounit (standard) Hang the thermounit in the pan of antifreeze with its temperature sensing end below the surface of antifreeze and measure the resistance while heating the antifreeze as shown in the illustration. If the resistance is incorrect, replace the thermounit.
Antifreeze in the pan is hot. Any contact can cause severe burns.
Testing thermounit