Information injection-pump assembly
BOSCH
9 400 612 457
9400612457
ZEXEL
101608-6350
1016086350
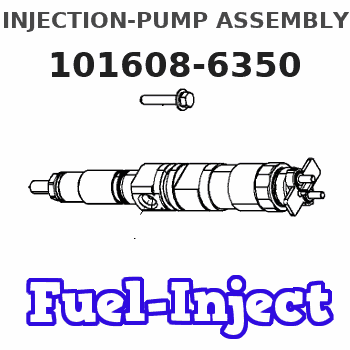
Rating:
Service parts 101608-6350 INJECTION-PUMP ASSEMBLY:
1.
_
7.
COUPLING PLATE
8.
_
9.
_
11.
Nozzle and Holder
ME440071
12.
Open Pre:MPa(Kqf/cm2)
17.7{180}
15.
NOZZLE SET
Include in #1:
101608-6350
as INJECTION-PUMP ASSEMBLY
Include in #2:
104749-0434
as _
Cross reference number
BOSCH
9 400 612 457
9400612457
ZEXEL
101608-6350
1016086350
Zexel num
Bosch num
Firm num
Name
Calibration Data:
Adjustment conditions
Test oil
1404 Test oil ISO4113 or {SAEJ967d}
1404 Test oil ISO4113 or {SAEJ967d}
Test oil temperature
degC
40
40
45
Nozzle and nozzle holder
105780-8140
Bosch type code
EF8511/9A
Nozzle
105780-0000
Bosch type code
DN12SD12T
Nozzle holder
105780-2080
Bosch type code
EF8511/9
Opening pressure
MPa
17.2
Opening pressure
kgf/cm2
175
Injection pipe
Outer diameter - inner diameter - length (mm) mm 6-2-600
Outer diameter - inner diameter - length (mm) mm 6-2-600
Overflow valve
131424-5520
Overflow valve opening pressure
kPa
255
221
289
Overflow valve opening pressure
kgf/cm2
2.6
2.25
2.95
Tester oil delivery pressure
kPa
255
255
255
Tester oil delivery pressure
kgf/cm2
2.6
2.6
2.6
RED4 control unit part number
407915-0
590
RED4 rack sensor specifications
mm
19
Direction of rotation (viewed from drive side)
Left L
Left L
Injection timing adjustment
Direction of rotation (viewed from drive side)
Left L
Left L
Injection order
1-5-3-6-
2-4
Pre-stroke
mm
4.2
4.15
4.25
Beginning of injection position
Governor side NO.1
Governor side NO.1
Difference between angles 1
Cal 1-5 deg. 60 59.5 60.5
Cal 1-5 deg. 60 59.5 60.5
Difference between angles 2
Cal 1-3 deg. 120 119.5 120.5
Cal 1-3 deg. 120 119.5 120.5
Difference between angles 3
Cal 1-6 deg. 180 179.5 180.5
Cal 1-6 deg. 180 179.5 180.5
Difference between angles 4
Cyl.1-2 deg. 240 239.5 240.5
Cyl.1-2 deg. 240 239.5 240.5
Difference between angles 5
Cal 1-4 deg. 300 299.5 300.5
Cal 1-4 deg. 300 299.5 300.5
Injection quantity adjustment
Rack position
(11.1)
PWM
%
50.4
Pump speed
r/min
900
900
900
Average injection quantity
mm3/st.
124.5
123.5
125.5
Max. variation between cylinders
%
0
-2.5
2.5
Basic
*
Injection quantity adjustment_02
Rack position
(7.3)
PWM
%
29.4+-2.
8
Pump speed
r/min
425
425
425
Average injection quantity
mm3/st.
11
9.5
12.5
Max. variation between cylinders
%
0
-15
15
Governor adjustment
Pump speed
r/min
600
Advance angle
deg.
3
2.5
3.5
Load
0/4
Remarks
Start
Start
Governor adjustment_02
Pump speed
r/min
-
Advance angle
deg.
0
0
0
Load
0/4
Remarks
Measure the actual speed.
Measure the actual speed.
Governor adjustment_03
Pump speed
r/min
850
Advance angle
deg.
0.5
Load
4/4
Governor adjustment_04
Pump speed
r/min
1025
Advance angle
deg.
1.5
1
2
Load
4/4
Remarks
Finish
Finish
Test data Ex:
Speed control lever angle
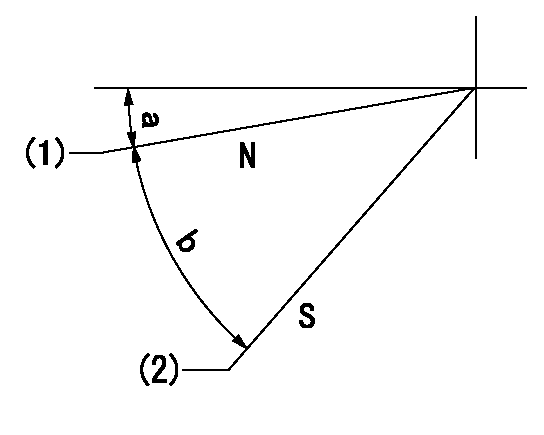
N:Pump normal
S:Stop the pump.
(1)Rack position = aa
(2)Rack position bb
----------
aa=20mm bb=1mm
----------
a=5deg+-5deg b=37deg+-5deg
----------
aa=20mm bb=1mm
----------
a=5deg+-5deg b=37deg+-5deg
0000000901

(1)Pump vertical direction
(2)Coupling's key groove position at No 1 cylinder's beginning of injection
(3)B.T.D.C.: aa
(4)-
----------
aa=8deg
----------
a=(0deg)
----------
aa=8deg
----------
a=(0deg)
Stop lever angle

(PWM) Pulse width modulation (%)
(R) Rack position (mm)
Rack sensor output characteristics
1. Rack limit adjustment
(1)Measure the rack position R2 for PWM a2%.
(2)Confirm that it is within the range R2 = 15+-1 mm.
(3)Measure the rack position R1 at PWM a %.
(4)Confirm that it is within the range R2 - R1 = 10+-0.1 mm.
2. Check the limp home operation.
(1)Move the switch box's limp home switch to the limp home side.
(2)Confirm rack position L1 (mm ) and L2 (mm) for PWM in the above table.
3. Check the pull down operation.
(1)Confirm that the rack position is 19 mm at PWM B%.
(2)In the conditions described in the above table, move the switch box's pull down switch to the pull down side and confirm that the rack position momentarily becomes 1 mm or less.
----------
a1=16.25% a2=72.5% L1=1--mm L2=19++mm A=5% B=95%
----------
----------
a1=16.25% a2=72.5% L1=1--mm L2=19++mm A=5% B=95%
----------
Information:
Center Bushing Check new bushings using the table below. Commutator and Drive End Bushing Specifications*I.D. of bushing ... 0.6693 to 0.6704 in.(17.000 to 17.028 mm)Oil clearance** ... 0.0036 to 0.0070 in.(0.091 to 0.178 mm)Maximum clearance** ... 0.016 in.(0.41 mm)Bushing depth ... 0.008 to 0.022 in.(0.20 to 0.56 mm)*Reaming may be necessary after installation. Center Bushing SpecificationsI.D. of bushing ... 1.182 to 1.184 in.(30.02 to 30.07 mm)Maximum clearance** ... 0.0236 in.(0.599 mm)Bushing depth ... 0.017 to 0.032 in.(0.43 to 0.81 mm)**The clearance is the difference between the shaft and the I.D. of the bushing.Armature
Check armature for straightness. Runout should not exceed 0.006 inch (0.15 mm). Maximum commutator runout is 0.016 inch (0.41 mm). If necessary, turn commutator and undercut insulation to 1/32-inch (0.794 mm). Undercut should never be less than 0.008 inch (0.20 mm) Commutator O.D. must be 1.77 inches (45.0 mm) or more. Clean copper dust from between the segments.Check armature for opens, shorts and grounds. Burned edge of commutator indicates an open circuit. Short Circuit TestPlace the armature in a growler and hold a hacksaw blade above each slot while slowly rotating the armature. If a coil is shorted, the blade will be attracted to and repelled from the slot.A short circuit most often occurs because of copper dust or filings between two commutator segments. A short of this nature can be corrected by removal of such material.
Fig. 22-Armature Ground TestWith the ohmmeter set to read on its highest scale, place one test lead on the commutator and the other lead on the armature core or shaft (Fig. 22). If the test meter indicator swings towards zero, the armature is grounded. Replace armature.
Fig. 23-Open Circuit TestWith the ohmmeter set to read on its lowest scale, place one test lead on the commutator segment and the other test lead on an adjacent segment (Fig. 23). Repeat this operation for all segments by moving one lead at a time. If the test meter indicator does not swing to zero and remains stationary, the armature coil between these two segements is open. Replace armature.Burned commutator segments are usually an indication of an open circuited coil.Overrunning Clutch and Pinion
Do not immerse the overrunning clutch and pinion 4, Fig. 21 in a cleaning solvent. The unit has been prelubricated and solvent will wash lubricant away. It may be cleaned with a cloth moistened with a cleaning solvent and wiped dry.Rotate the pinion. Pinion gear should rotate smoothly (but not necessarily easily) in one direction, and should not rotate in the opposite direction.If the pinion gear does not rotate smoothly, or if it is worn, chipped, or burred, it should be replaced.Field Windings and Shunt Windings
Grounded Circuit Test (Fig. 24)
Fig. 24-Grounded Circuit TestRemove the screw and hang the eyelet terminal in the air. Using an ohmmeter set to read on its highest scale, place one test lead on the copper terminal bolt and the other lead on a clean spot of the field frame (Fig. 24). If the ohmmeter
Check armature for straightness. Runout should not exceed 0.006 inch (0.15 mm). Maximum commutator runout is 0.016 inch (0.41 mm). If necessary, turn commutator and undercut insulation to 1/32-inch (0.794 mm). Undercut should never be less than 0.008 inch (0.20 mm) Commutator O.D. must be 1.77 inches (45.0 mm) or more. Clean copper dust from between the segments.Check armature for opens, shorts and grounds. Burned edge of commutator indicates an open circuit. Short Circuit TestPlace the armature in a growler and hold a hacksaw blade above each slot while slowly rotating the armature. If a coil is shorted, the blade will be attracted to and repelled from the slot.A short circuit most often occurs because of copper dust or filings between two commutator segments. A short of this nature can be corrected by removal of such material.
Fig. 22-Armature Ground TestWith the ohmmeter set to read on its highest scale, place one test lead on the commutator and the other lead on the armature core or shaft (Fig. 22). If the test meter indicator swings towards zero, the armature is grounded. Replace armature.
Fig. 23-Open Circuit TestWith the ohmmeter set to read on its lowest scale, place one test lead on the commutator segment and the other test lead on an adjacent segment (Fig. 23). Repeat this operation for all segments by moving one lead at a time. If the test meter indicator does not swing to zero and remains stationary, the armature coil between these two segements is open. Replace armature.Burned commutator segments are usually an indication of an open circuited coil.Overrunning Clutch and Pinion
Do not immerse the overrunning clutch and pinion 4, Fig. 21 in a cleaning solvent. The unit has been prelubricated and solvent will wash lubricant away. It may be cleaned with a cloth moistened with a cleaning solvent and wiped dry.Rotate the pinion. Pinion gear should rotate smoothly (but not necessarily easily) in one direction, and should not rotate in the opposite direction.If the pinion gear does not rotate smoothly, or if it is worn, chipped, or burred, it should be replaced.Field Windings and Shunt Windings
Grounded Circuit Test (Fig. 24)
Fig. 24-Grounded Circuit TestRemove the screw and hang the eyelet terminal in the air. Using an ohmmeter set to read on its highest scale, place one test lead on the copper terminal bolt and the other lead on a clean spot of the field frame (Fig. 24). If the ohmmeter