Information injection-pump assembly
BOSCH
9 400 611 945
9400611945
ZEXEL
101608-6310
1016086310
MITSUBISHI
ME300222
me300222
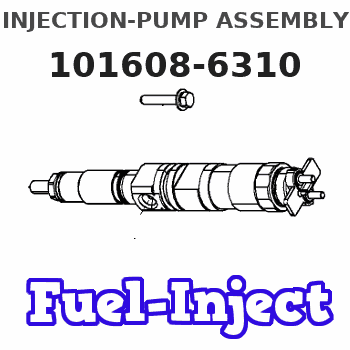
Rating:
Service parts 101608-6310 INJECTION-PUMP ASSEMBLY:
1.
_
6.
COUPLING PLATE
7.
COUPLING PLATE
8.
_
9.
_
11.
Nozzle and Holder
ME072662
12.
Open Pre:MPa(Kqf/cm2)
15.7{160}/21.6{220}
14.
NOZZLE
Include in #1:
101608-6310
as INJECTION-PUMP ASSEMBLY
Include in #2:
104748-0520
as _
Cross reference number
BOSCH
9 400 611 945
9400611945
ZEXEL
101608-6310
1016086310
MITSUBISHI
ME300222
me300222
Zexel num
Bosch num
Firm num
Name
101608-6310
9 400 611 945
ME300222 MITSUBISHI
INJECTION-PUMP ASSEMBLY
6D16 K 14BE INJECTION PUMP ASSY PE6A PE
6D16 K 14BE INJECTION PUMP ASSY PE6A PE
Calibration Data:
Adjustment conditions
Test oil
1404 Test oil ISO4113 or {SAEJ967d}
1404 Test oil ISO4113 or {SAEJ967d}
Test oil temperature
degC
40
40
45
Nozzle and nozzle holder
105780-8260
Bosch type code
9 430 610 133
Nozzle
105780-0120
Bosch type code
1 688 901 990
Nozzle holder
105780-2190
Opening pressure
MPa
18
Opening pressure
kgf/cm2
184
Injection pipe
Outer diameter - inner diameter - length (mm) mm 6-2-600
Outer diameter - inner diameter - length (mm) mm 6-2-600
Overflow valve
131424-8420
Overflow valve opening pressure
kPa
255
221
289
Overflow valve opening pressure
kgf/cm2
2.6
2.25
2.95
Tester oil delivery pressure
kPa
255
255
255
Tester oil delivery pressure
kgf/cm2
2.6
2.6
2.6
Direction of rotation (viewed from drive side)
Left L
Left L
Injection timing adjustment
Direction of rotation (viewed from drive side)
Left L
Left L
Injection order
1-5-3-6-
2-4
Pre-stroke
mm
3.2
3.15
3.25
Beginning of injection position
Governor side NO.1
Governor side NO.1
Difference between angles 1
Cal 1-5 deg. 60 59.5 60.5
Cal 1-5 deg. 60 59.5 60.5
Difference between angles 2
Cal 1-3 deg. 120 119.5 120.5
Cal 1-3 deg. 120 119.5 120.5
Difference between angles 3
Cal 1-6 deg. 180 179.5 180.5
Cal 1-6 deg. 180 179.5 180.5
Difference between angles 4
Cyl.1-2 deg. 240 239.5 240.5
Cyl.1-2 deg. 240 239.5 240.5
Difference between angles 5
Cal 1-4 deg. 300 299.5 300.5
Cal 1-4 deg. 300 299.5 300.5
Injection quantity adjustment
Adjusting point
-
Rack position
11.4
Pump speed
r/min
850
850
850
Each cylinder's injection qty
mm3/st.
84.5
82
87
Basic
*
Fixing the rack
*
Standard for adjustment of the maximum variation between cylinders
*
Injection quantity adjustment_02
Adjusting point
Z
Rack position
9.5+-0.5
Pump speed
r/min
310
310
310
Each cylinder's injection qty
mm3/st.
10.8
9.2
12.4
Fixing the rack
*
Standard for adjustment of the maximum variation between cylinders
*
Injection quantity adjustment_03
Adjusting point
A
Rack position
R1(11.4)
Pump speed
r/min
850
850
850
Average injection quantity
mm3/st.
84.5
83.5
85.5
Basic
*
Fixing the lever
*
Injection quantity adjustment_04
Adjusting point
B
Rack position
R1+0.4
Pump speed
r/min
1450
1450
1450
Average injection quantity
mm3/st.
85.5
81.5
89.5
Fixing the lever
*
Injection quantity adjustment_05
Adjusting point
C
Rack position
R1-0.3
Pump speed
r/min
500
500
500
Average injection quantity
mm3/st.
82.5
78.5
86.5
Fixing the lever
*
Injection quantity adjustment_06
Adjusting point
I
Rack position
R1+0.5++
Pump speed
r/min
100
100
100
Average injection quantity
mm3/st.
155
155
165
Fixing the lever
*
Rack limit
*
Timer adjustment
Pump speed
r/min
1150--
Advance angle
deg.
0
0
0
Remarks
Start
Start
Timer adjustment_02
Pump speed
r/min
1100
Advance angle
deg.
0.5
Timer adjustment_03
Pump speed
r/min
1450
Advance angle
deg.
5
4.5
5.5
Remarks
Finish
Finish
Test data Ex:
Governor adjustment
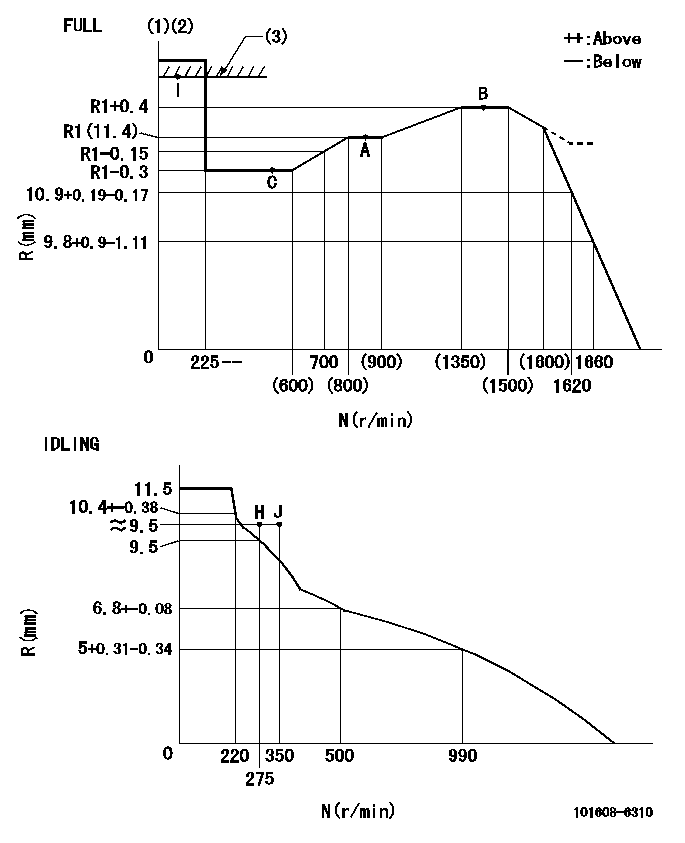
N:Pump speed
R:Rack position (mm)
(1)Torque cam stamping: T1
(2)Tolerance for racks not indicated: +-0.05mm.
(3)RACK LIMIT
----------
T1=M16
----------
----------
T1=M16
----------
Speed control lever angle
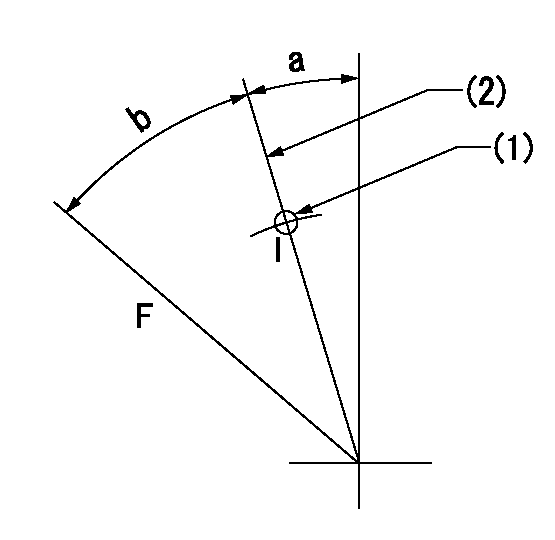
F:Full speed
I:Idle
(1)Use the hole at R = aa
(2)Stopper bolt set position 'H'
----------
aa=40mm
----------
a=18.5deg+-5deg b=42deg+-3deg
----------
aa=40mm
----------
a=18.5deg+-5deg b=42deg+-3deg
Stop lever angle
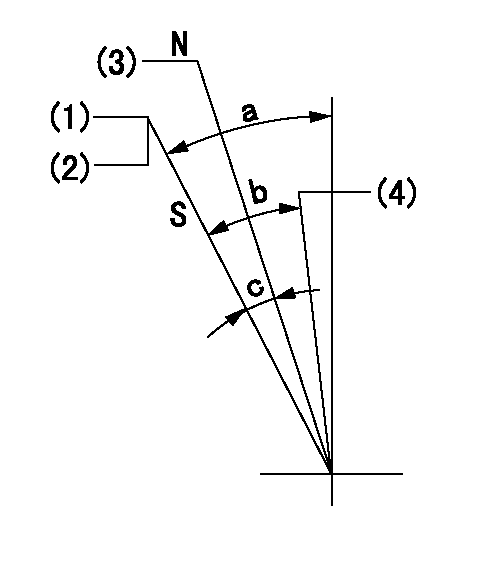
N:Engine manufacturer's normal use
S:Stop the pump.
(1)Confirm that speed = aa, rack position = bb and the stopper bolt is set at non-injection at the speed lever's full setting.
(2)After setting the stopper bolt, confirm non-injection at speed = cc and rack position = dd.
(3)Rack position = approximately ee (speed lever full, speed = ff).
(4)Free (at delivery)
----------
aa=1450r/min bb=7.2-0.5mm cc=275r/min dd=(8)mm ee=15mm ff=0r/min
----------
a=36.5deg+-5deg b=(25deg) c=13deg+-5deg
----------
aa=1450r/min bb=7.2-0.5mm cc=275r/min dd=(8)mm ee=15mm ff=0r/min
----------
a=36.5deg+-5deg b=(25deg) c=13deg+-5deg
0000001501 LEVER
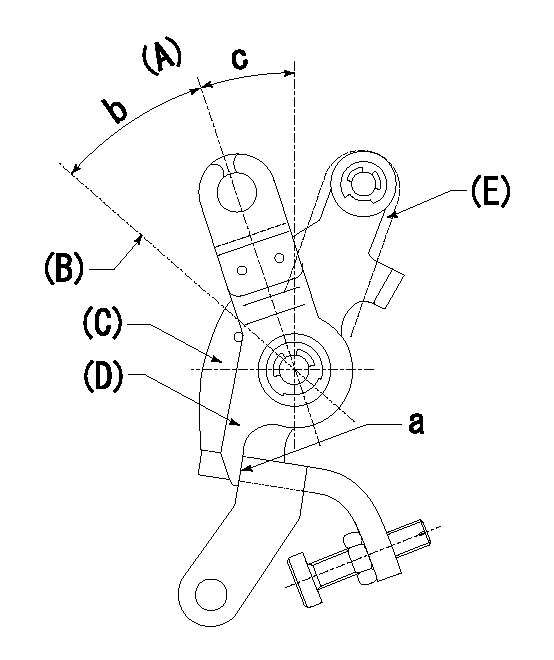
(A) Idle
(B) Full speed
(C) Base lever
(D) Accelerator lever
(E) Accelerator lever delivery position
1. Measure speed lever angle
(1)Measure the angle when the accelerator lever (D) contacted the base lever (C) at a.
----------
----------
b=42deg+-3deg c=18.5deg+-5deg
----------
----------
b=42deg+-3deg c=18.5deg+-5deg
0000001601 ACS

(A) Housing
(B) Snap ring
(C) adjusting screw
(D) Set screw
(E): Push rod
(F) Spacer
1. Adjustment of the aneroid compensator
(1)Adjust with the (D) set screw so that the clearance between the (A) housing and (B) snap ring is L1.
(2)Select the push rod (E) so that the distance from the end surface of the (F) spacer becomes L2.
(3)Turn adjusting screw (C) to adjust the start of aneroid compensator operation.
2. Adjustment when mounting the governor.
(1)Set the speed of the pump to N1 r/min and fix the control lever at the full set position.
(2)Turn adjusting screw (C) to obtain the performance shown in the graph above.
(3)After final adjustment, confirm that the gap between housing (A) and snapring (B) is L3.
----------
N1=1450r/min L1=1.4~1.7mm L2=0.5+-0.5mm L3=(0.1~0.5)mm
----------
Ra=R1+0.4mm Rb=[R1+0.2]+-0.1mm Rc=R1-0.1mm Pa=(89.8)+4kPa((674)+30mmHg) Pb=79.4kPa(596mmHg) Pc=61.6kPa(462mmHg) Q1=85.5+-4cm3/1000st Q2=- Q3=74.5+-4cm3/1000st
----------
N1=1450r/min L1=1.4~1.7mm L2=0.5+-0.5mm L3=(0.1~0.5)mm
----------
Ra=R1+0.4mm Rb=[R1+0.2]+-0.1mm Rc=R1-0.1mm Pa=(89.8)+4kPa((674)+30mmHg) Pb=79.4kPa(596mmHg) Pc=61.6kPa(462mmHg) Q1=85.5+-4cm3/1000st Q2=- Q3=74.5+-4cm3/1000st
Timing setting

(1)Pump vertical direction
(2)Position of timer's tooth at No 1 cylinder's beginning of injection
(3)B.T.D.C.: aa
(4)-
----------
aa=12deg
----------
a=(1deg)
----------
aa=12deg
----------
a=(1deg)
Information:
Repair
Measure crankshaft main journal to main bearing clearance.
Fig. 5-Main Bearing ClearanceMain bearing journal O.D. (new) (1, Fig. 5) ... 3.123 to 3.124 inch(79.32 to 79.35 mm)Assembled Main bearing I.D. (new) (2) ... 3.126 to 3.128 inch(79.39 to 79.45 mm)Main bearing clearance (new) (3) ... 0.0016 to 0.0046 inch(0.041 to 0.117 mm)Main bearing clearance (maximum) ... 0.006 inch(0.15 mm)Main bearing bore I.D. (4) ... 3.325 to 3.326 inch(84.46 to 84.48 mm)Measure crankshaft main journal taper and roundness.
Fig. 6-Main Bearing MeasurementJournal taper (maximum) (1, Fig. 6) ... 0.001 inch per 1.00 inch(0.03 mm per 25.4 mm)Journal out-of-round (maximum) (2, Fig. 6) ... 0.003 inch(0.08 mm)If wear is even, but out of specifications, dress crankshaft main journals and select proper undersize bearing inserts.If journals are out-of-round or tapered, grind crankshaft and select proper undersize bearing inserts.If crankshaft end play is excessive, replace worn thrust bearings or grind crankshaft thrust surfaces and select proper oversize thrust bearing.Installation
Fig. 7-Main Bearing Insert InstallationPosition bearing inserts in cylinder block and main bearing caps with the tang on the insert engaged in the slot in the cylinder block and main bearing caps (Fig. 7).Apply a coat of clean engine oil to the bearing surface of the inserts.Position crankshaft in cylinder block. Tangs on main bearing halves in main bearing caps must be positioned to the same side of the crankshaft as the tangs on main bearing halves in cylinder block.
Fig. 8-Main Bearing Cap PositionsInstall main bearing caps with numbers (1, Fig. 8) corresponding to numbers in oil pan rail (2). If there is no arrow (3) machined on main bearing cap, install cap with number to same side as numbers in oil pan rail. If there is an arrow machined on main bearing cap, arrow must point toward camshaft side.Dip main bearing cap screws in clean engine oil and position them in the main bearing caps. IMPORTANT: Do not use pneumatic wrench to install main bearing cap screws.Before tightening cap screws on main bearing caps, align upper and lower thrust flanges on main thrust bearings. Using a soft-face hammer, tap crankshaft to the rear and then to the front to line up thrust bearing flanges.Rotate crankshaft by hand. Crankshaft should rotate with little effort.
Fig. 9-Main Bearing Cap ScrewTighten main bearing cap screws (Fig. 9)Main bearing cap screw torque ... 85 lb-ft(115 N m) (12 kg-m)Turn crankshaft by hand. If it does not turn easily, disassemble parts and determine the cause.Pull piston and connecting rods into position against the crankshaft.Install connecting rod caps (Group 0403).Install engine front plate (Group 0404).Install camshaft (Group 0402).Install timing gear train (Group 0402).Install timing gear cover (Group 0402).Install vibration damper (Group 0401).Install fan belt and alternator belt (Group 0429).Install flywheel housing (Group 0433).Install flywheel (Group 0433).Install oil pan (Group 0407).Install pushrods and rocker arm assembly (Group 0402).Install rocker arm cover (Group 0402).Install fuel transfer pump (Group 0421).Crankshaft Gear
Removal
Remove crankshaft from engine (Group 0401).
Fig. 10-Crankshaft Gear RemovalUse knife-edge puller (1, Fig. 10) to remove crankshaft gear (2) from
Measure crankshaft main journal to main bearing clearance.
Fig. 5-Main Bearing ClearanceMain bearing journal O.D. (new) (1, Fig. 5) ... 3.123 to 3.124 inch(79.32 to 79.35 mm)Assembled Main bearing I.D. (new) (2) ... 3.126 to 3.128 inch(79.39 to 79.45 mm)Main bearing clearance (new) (3) ... 0.0016 to 0.0046 inch(0.041 to 0.117 mm)Main bearing clearance (maximum) ... 0.006 inch(0.15 mm)Main bearing bore I.D. (4) ... 3.325 to 3.326 inch(84.46 to 84.48 mm)Measure crankshaft main journal taper and roundness.
Fig. 6-Main Bearing MeasurementJournal taper (maximum) (1, Fig. 6) ... 0.001 inch per 1.00 inch(0.03 mm per 25.4 mm)Journal out-of-round (maximum) (2, Fig. 6) ... 0.003 inch(0.08 mm)If wear is even, but out of specifications, dress crankshaft main journals and select proper undersize bearing inserts.If journals are out-of-round or tapered, grind crankshaft and select proper undersize bearing inserts.If crankshaft end play is excessive, replace worn thrust bearings or grind crankshaft thrust surfaces and select proper oversize thrust bearing.Installation
Fig. 7-Main Bearing Insert InstallationPosition bearing inserts in cylinder block and main bearing caps with the tang on the insert engaged in the slot in the cylinder block and main bearing caps (Fig. 7).Apply a coat of clean engine oil to the bearing surface of the inserts.Position crankshaft in cylinder block. Tangs on main bearing halves in main bearing caps must be positioned to the same side of the crankshaft as the tangs on main bearing halves in cylinder block.
Fig. 8-Main Bearing Cap PositionsInstall main bearing caps with numbers (1, Fig. 8) corresponding to numbers in oil pan rail (2). If there is no arrow (3) machined on main bearing cap, install cap with number to same side as numbers in oil pan rail. If there is an arrow machined on main bearing cap, arrow must point toward camshaft side.Dip main bearing cap screws in clean engine oil and position them in the main bearing caps. IMPORTANT: Do not use pneumatic wrench to install main bearing cap screws.Before tightening cap screws on main bearing caps, align upper and lower thrust flanges on main thrust bearings. Using a soft-face hammer, tap crankshaft to the rear and then to the front to line up thrust bearing flanges.Rotate crankshaft by hand. Crankshaft should rotate with little effort.
Fig. 9-Main Bearing Cap ScrewTighten main bearing cap screws (Fig. 9)Main bearing cap screw torque ... 85 lb-ft(115 N m) (12 kg-m)Turn crankshaft by hand. If it does not turn easily, disassemble parts and determine the cause.Pull piston and connecting rods into position against the crankshaft.Install connecting rod caps (Group 0403).Install engine front plate (Group 0404).Install camshaft (Group 0402).Install timing gear train (Group 0402).Install timing gear cover (Group 0402).Install vibration damper (Group 0401).Install fan belt and alternator belt (Group 0429).Install flywheel housing (Group 0433).Install flywheel (Group 0433).Install oil pan (Group 0407).Install pushrods and rocker arm assembly (Group 0402).Install rocker arm cover (Group 0402).Install fuel transfer pump (Group 0421).Crankshaft Gear
Removal
Remove crankshaft from engine (Group 0401).
Fig. 10-Crankshaft Gear RemovalUse knife-edge puller (1, Fig. 10) to remove crankshaft gear (2) from
Have questions with 101608-6310?
Group cross 101608-6310 ZEXEL
Mitsubishi
101608-6310
9 400 611 945
ME300222
INJECTION-PUMP ASSEMBLY
6D16
6D16