Information injection-pump assembly
BOSCH
9 400 613 054
9400613054
ZEXEL
101608-6203
1016086203
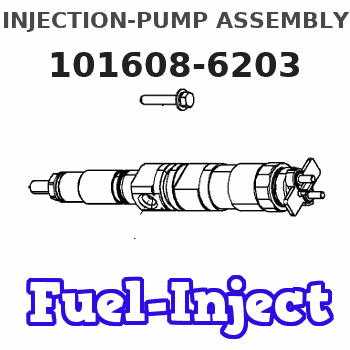
Rating:
Service parts 101608-6203 INJECTION-PUMP ASSEMBLY:
1.
_
7.
COUPLING PLATE
8.
_
9.
_
11.
Nozzle and Holder
ME440071
12.
Open Pre:MPa(Kqf/cm2)
17.7{180}
15.
NOZZLE SET
Include in #1:
101608-6203
as INJECTION-PUMP ASSEMBLY
Include in #2:
104740-0694
as _
Cross reference number
BOSCH
9 400 613 054
9400613054
ZEXEL
101608-6203
1016086203
Zexel num
Bosch num
Firm num
Name
Calibration Data:
Adjustment conditions
Test oil
1404 Test oil ISO4113 or {SAEJ967d}
1404 Test oil ISO4113 or {SAEJ967d}
Test oil temperature
degC
40
40
45
Nozzle and nozzle holder
105780-8140
Bosch type code
EF8511/9A
Nozzle
105780-0000
Bosch type code
DN12SD12T
Nozzle holder
105780-2080
Bosch type code
EF8511/9
Opening pressure
MPa
17.2
Opening pressure
kgf/cm2
175
Injection pipe
Outer diameter - inner diameter - length (mm) mm 6-2-600
Outer diameter - inner diameter - length (mm) mm 6-2-600
Overflow valve
131424-5520
Overflow valve opening pressure
kPa
255
221
289
Overflow valve opening pressure
kgf/cm2
2.6
2.25
2.95
Tester oil delivery pressure
kPa
255
255
255
Tester oil delivery pressure
kgf/cm2
2.6
2.6
2.6
Direction of rotation (viewed from drive side)
Left L
Left L
Injection timing adjustment
Direction of rotation (viewed from drive side)
Left L
Left L
Injection order
1-5-3-6-
2-4
Pre-stroke
mm
4.5
4.45
4.55
Beginning of injection position
Governor side NO.1
Governor side NO.1
Difference between angles 1
Cal 1-5 deg. 60 59.5 60.5
Cal 1-5 deg. 60 59.5 60.5
Difference between angles 2
Cal 1-3 deg. 120 119.5 120.5
Cal 1-3 deg. 120 119.5 120.5
Difference between angles 3
Cal 1-6 deg. 180 179.5 180.5
Cal 1-6 deg. 180 179.5 180.5
Difference between angles 4
Cyl.1-2 deg. 240 239.5 240.5
Cyl.1-2 deg. 240 239.5 240.5
Difference between angles 5
Cal 1-4 deg. 300 299.5 300.5
Cal 1-4 deg. 300 299.5 300.5
Injection quantity adjustment
Adjusting point
A
Rack position
11.9
Pump speed
r/min
1100
1100
1100
Average injection quantity
mm3/st.
143.5
142.5
144.5
Max. variation between cylinders
%
0
-2.5
2.5
Basic
*
Fixing the lever
*
Boost pressure
kPa
66.7
66.7
Boost pressure
mmHg
500
500
Injection quantity adjustment_02
Adjusting point
-
Rack position
7.8+-0.5
Pump speed
r/min
425
425
425
Average injection quantity
mm3/st.
16.5
15
18
Max. variation between cylinders
%
0
-15
15
Fixing the rack
*
Boost pressure
kPa
0
0
0
Boost pressure
mmHg
0
0
0
Remarks
Adjust only variation between cylinders; adjust governor according to governor specifications.
Adjust only variation between cylinders; adjust governor according to governor specifications.
Injection quantity adjustment_03
Adjusting point
E
Rack position
12.1++
Pump speed
r/min
100
100
100
Average injection quantity
mm3/st.
130
130
140
Fixing the lever
*
Boost pressure
kPa
0
0
0
Boost pressure
mmHg
0
0
0
Rack limit
*
Boost compensator adjustment
Pump speed
r/min
500
500
500
Rack position
R1-1.2
Boost pressure
kPa
18.7
12
25.4
Boost pressure
mmHg
140
90
190
Boost compensator adjustment_02
Pump speed
r/min
500
500
500
Rack position
R1(11.15
)
Boost pressure
kPa
57.3
54.6
60
Boost pressure
mmHg
430
410
450
Timer adjustment
Pump speed
r/min
1100++
Advance angle
deg.
0
0
0
Remarks
Do not advance until starting N = 1100.
Do not advance until starting N = 1100.
Timer adjustment_02
Pump speed
r/min
-
Advance angle
deg.
4
4
4
Remarks
Measure the actual speed, stop
Measure the actual speed, stop
Test data Ex:
Governor adjustment
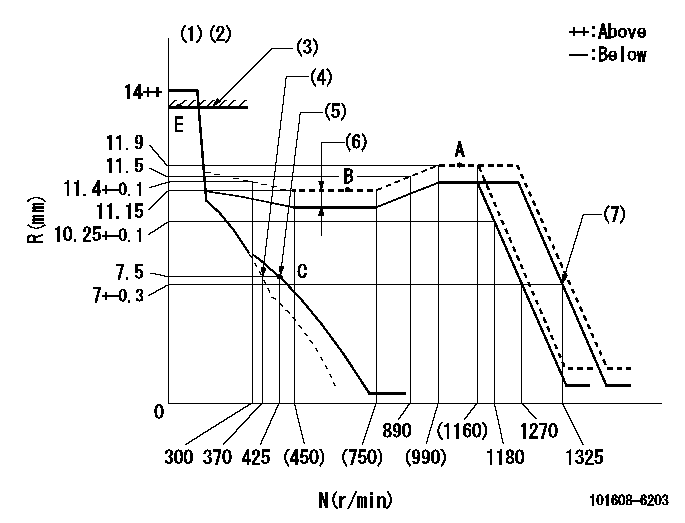
N:Pump speed
R:Rack position (mm)
(1)Target notch: K
(2)Tolerance for racks not indicated: +-0.05mm.
(3)RACK LIMIT
(4)Main spring setting
(5)Set idle sub-spring
(6)Boost compensator stroke: BCL
(7)At delivery
----------
K=8 BCL=1.2+-0.1mm
----------
----------
K=8 BCL=1.2+-0.1mm
----------
Speed control lever angle
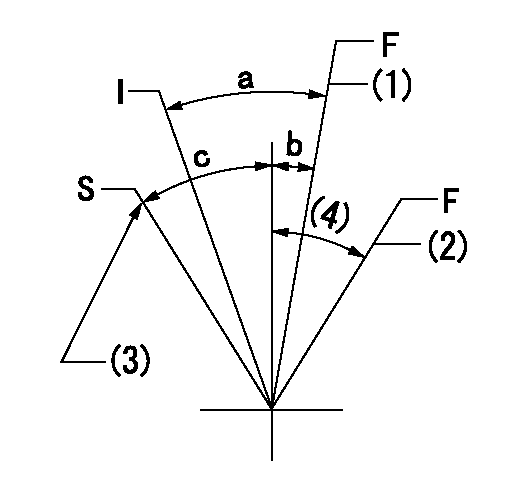
F:Full speed
I:Idle
S:Stop
(1)Set the pump speed at aa
(2)Speed = bb (set position for delivery)
(3)Stopper bolt setting
(4)Actual measurement
----------
aa=1270r/min bb=1325r/min
----------
a=(23deg)+-5deg b=(4deg)+-5deg c=31deg+-3deg
----------
aa=1270r/min bb=1325r/min
----------
a=(23deg)+-5deg b=(4deg)+-5deg c=31deg+-3deg
Stop lever angle

N:Pump normal
S:Stop the pump.
(1)Normal
(2)Pump speed aa and rack position bb (to be sealed at delivery)
----------
aa=0r/min bb=1-0.5mm
----------
a=35deg+-5deg b=(55deg)
----------
aa=0r/min bb=1-0.5mm
----------
a=35deg+-5deg b=(55deg)
0000001501 TAMPER PROOF

Tamperproofing-equipped boost compensator cover installation procedure
(A) After adjusting the boost compensator, tighten the bolts to remove the heads.
(1)Before adjusting the governor and the boost compensator, tighten the screw to the specified torque.
(Tightening torque T = T1 maximum)
(2)After adjusting the governor and the boost compensator, tighten to the specified torque to break off the bolt heads.
(Tightening torque T = T2)
----------
T1=2.5N-m(0.25kgf-m) T2=2.9~4.4N-m(0.3~0.45kgf-m)
----------
----------
T1=2.5N-m(0.25kgf-m) T2=2.9~4.4N-m(0.3~0.45kgf-m)
----------
Timing setting

(1)Pump vertical direction
(2)Coupling's key groove position at No 1 cylinder's beginning of injection
(3)B.T.D.C.: aa
(4)-
----------
aa=14deg
----------
a=(7deg)
----------
aa=14deg
----------
a=(7deg)
Information:
PARTS NEEDED
Qty
Part Number Description
1 2744962 PUMP GP-F INJ -B
In order to allow equitable parts availability to all participating dealers, please limit your initial parts order to not exceed 2% of dealership population. This is an initial order recommendation only, and the ultimate responsibility for ordering the total number of parts needed to satisfy the program lies with the dealer.
ACTION REQUIRED
Replace the failed fuel injection pump. Refer to the engine's Disassembly and Assembly.
While carrying out "Fuel Injection Pump - Remove", please ensure that the fuel injection pump gear backlash is removed and the fuel injection pump locking bolt is tightened to a torque of 17 N.m (13 lb ft).
Fuel injection pumps that have not been locked correctly will have the claim rejected or debited.
After the new fuel injection pump has been installed, carry out checks for air in the fuel. Refer to the engine's Testing and Adjusting, "Air in Fuel - Test".
To ensure correct priming of the fuel system on first start-up, follow the procedure below.
1. Ensure that all low pressure fuel connections and high pressure fuel lines are installed correctly.
2. Set the throttle to the low idle position and ensure the parking brake is engaged
3. Crank the engine for 1 second to initiate the fuel priming sequence (do not start the engine)
4. Return ignition switch to the RUN position & listen for the fuel priming pump running
5. Leave the ignition key in the RUN position for three minutes.
6. Crank the engine with the throttle lever in the CLOSED position until the engine starts.
7. Run the engine at low idle for one minute.
8. Cycle the throttle lever from the low idle position to the high idle position three times. The cycle time for the throttle lever is one second to six seconds for one complete cycle.
9. Check for leaks in the fuel system.
Documentation Procedure
Please ensure that when submitting the claim the following documentation is provided.
1. Full details of the customer?s complaint and the symptoms witnessed.
2. Test work and diagnostic checks carried out to diagnose that the fuel injection pump is the part causing failure.
3. Results from the Testing and Adjusting, "Air in Fuel - Test". Please include photos of any air seen in the SIMS entry.
If the requested documentation is not provided, the claim may be rejected or debited.
SERVICE CLAIM ALLOWANCES
Product smu/age whichever comes first Caterpillar Dealer Suggested Customer Suggested
Parts % Labor Hrs% Parts % Labor Hrs% Parts % Labor Hrs%
0-3000 hrs,
0-36 mo 100.0% 100.0% 0.0% 0.0% 0.0% 0.0%
This is a 4.0-hour job
Refer to the Documentation Procedure in the Action Required for the Service Claim.
PARTS DISPOSITION
***** NACD *****
Hold all failed fuel injection pumps for a Parts Return Request (PRR). A PRR will be issued to you through the Send-It-Back process after the claim is submitted. Make