Information injection-pump assembly
BOSCH
9 400 611 331
9400611331
ZEXEL
101608-6000
1016086000
MITSUBISHI
ME170452
me170452
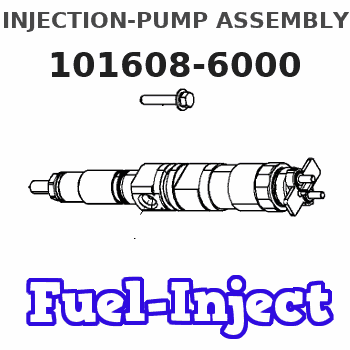
Rating:
Service parts 101608-6000 INJECTION-PUMP ASSEMBLY:
1.
_
6.
COUPLING PLATE
7.
COUPLING PLATE
8.
_
9.
_
11.
Nozzle and Holder
ME072745
12.
Open Pre:MPa(Kqf/cm2)
15.7{160}/21.6{220}
14.
NOZZLE
Cross reference number
BOSCH
9 400 611 331
9400611331
ZEXEL
101608-6000
1016086000
MITSUBISHI
ME170452
me170452
Zexel num
Bosch num
Firm num
Name
9 400 611 331
ME170452 MITSUBISHI
INJECTION-PUMP ASSEMBLY
6D16T7 * K 14BE INJECTION PUMP ASSY PE6A PE
6D16T7 * K 14BE INJECTION PUMP ASSY PE6A PE
Calibration Data:
Adjustment conditions
Test oil
1404 Test oil ISO4113 or {SAEJ967d}
1404 Test oil ISO4113 or {SAEJ967d}
Test oil temperature
degC
40
40
45
Nozzle and nozzle holder
105780-8260
Bosch type code
9 430 610 133
Nozzle
105780-0120
Bosch type code
1 688 901 990
Nozzle holder
105780-2190
Opening pressure
MPa
18
Opening pressure
kgf/cm2
184
Injection pipe
Outer diameter - inner diameter - length (mm) mm 6-2-600
Outer diameter - inner diameter - length (mm) mm 6-2-600
Overflow valve
131424-8420
Overflow valve opening pressure
kPa
255
221
289
Overflow valve opening pressure
kgf/cm2
2.6
2.25
2.95
Tester oil delivery pressure
kPa
255
255
255
Tester oil delivery pressure
kgf/cm2
2.6
2.6
2.6
Direction of rotation (viewed from drive side)
Left L
Left L
Injection timing adjustment
Direction of rotation (viewed from drive side)
Left L
Left L
Injection order
1-5-3-6-
2-4
Pre-stroke
mm
3.2
3.15
3.25
Beginning of injection position
Governor side NO.1
Governor side NO.1
Difference between angles 1
Cal 1-5 deg. 60 59.5 60.5
Cal 1-5 deg. 60 59.5 60.5
Difference between angles 2
Cal 1-3 deg. 120 119.5 120.5
Cal 1-3 deg. 120 119.5 120.5
Difference between angles 3
Cal 1-6 deg. 180 179.5 180.5
Cal 1-6 deg. 180 179.5 180.5
Difference between angles 4
Cyl.1-2 deg. 240 239.5 240.5
Cyl.1-2 deg. 240 239.5 240.5
Difference between angles 5
Cal 1-4 deg. 300 299.5 300.5
Cal 1-4 deg. 300 299.5 300.5
Injection quantity adjustment
Adjusting point
-
Rack position
12.4
Pump speed
r/min
900
900
900
Each cylinder's injection qty
mm3/st.
110.5
107.2
113.8
Basic
*
Fixing the rack
*
Standard for adjustment of the maximum variation between cylinders
*
Injection quantity adjustment_02
Adjusting point
Z
Rack position
9.5+-0.5
Pump speed
r/min
275
275
275
Each cylinder's injection qty
mm3/st.
12.5
10.6
14.4
Fixing the rack
*
Standard for adjustment of the maximum variation between cylinders
*
Injection quantity adjustment_03
Adjusting point
A
Rack position
R1(12.4)
Pump speed
r/min
900
900
900
Average injection quantity
mm3/st.
110.5
109.5
111.5
Basic
*
Fixing the lever
*
Boost pressure
kPa
70.6
70.6
Boost pressure
mmHg
530
530
Injection quantity adjustment_04
Adjusting point
B
Rack position
R1+0.8
Pump speed
r/min
1400
1400
1400
Average injection quantity
mm3/st.
115.5
111.5
119.5
Fixing the lever
*
Boost pressure
kPa
70.6
70.6
Boost pressure
mmHg
530
530
Injection quantity adjustment_05
Adjusting point
C
Rack position
(R1+0.1)
Pump speed
r/min
500
500
500
Average injection quantity
mm3/st.
130.5
126.5
134.5
Fixing the lever
*
Boost pressure
kPa
70.6
70.6
Boost pressure
mmHg
530
530
Injection quantity adjustment_06
Adjusting point
D
Rack position
R2-1.35
Pump speed
r/min
400
400
400
Average injection quantity
mm3/st.
88
84
92
Fixing the lever
*
Boost pressure
kPa
0
0
0
Boost pressure
mmHg
0
0
0
Injection quantity adjustment_07
Adjusting point
I
Rack position
-
Pump speed
r/min
100
100
100
Average injection quantity
mm3/st.
160
160
170
Fixing the lever
*
Boost pressure
kPa
0
0
0
Boost pressure
mmHg
0
0
0
Rack limit
*
Boost compensator adjustment
Pump speed
r/min
400
400
400
Rack position
R2-1.35
Boost pressure
kPa
13.3
13.3
13.3
Boost pressure
mmHg
100
100
100
Boost compensator adjustment_02
Pump speed
r/min
400
400
400
Rack position
R2-0.55
Boost pressure
kPa
40
38.7
41.3
Boost pressure
mmHg
300
290
310
Boost compensator adjustment_03
Pump speed
r/min
400
400
400
Rack position
R2[R1+0.
1]
Boost pressure
kPa
57.3
57.3
57.3
Boost pressure
mmHg
430
430
430
Timer adjustment
Pump speed
r/min
[N1+50]-
-
Advance angle
deg.
0
0
0
Remarks
Start
Start
Timer adjustment_02
Pump speed
r/min
N1
Advance angle
deg.
0.5
Remarks
Measure the actual speed.
Measure the actual speed.
Timer adjustment_03
Pump speed
r/min
-
Advance angle
deg.
3.5
3.5
3.5
Remarks
Measure the actual speed, stop
Measure the actual speed, stop
Test data Ex:
Governor adjustment

N:Pump speed
R:Rack position (mm)
(1)Torque cam stamping: T1
(2)Tolerance for racks not indicated: +-0.05mm.
(3)RACK LIMIT
(4)Boost compensator stroke: BCL
----------
T1=N21 BCL=1.35+-0.1mm
----------
----------
T1=N21 BCL=1.35+-0.1mm
----------
Speed control lever angle
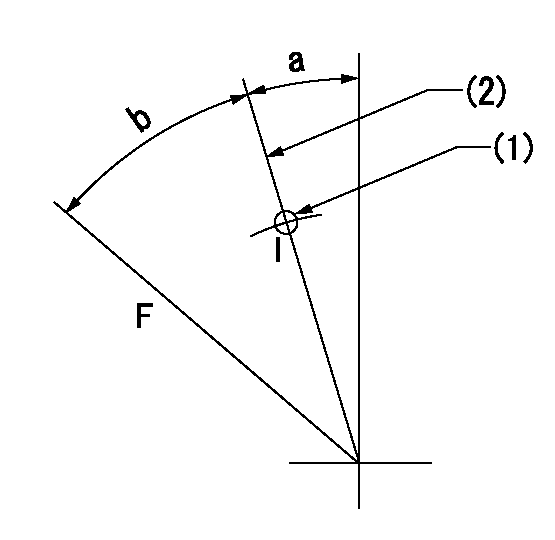
F:Full speed
I:Idle
(1)Use the hole at R = aa
(2)Stopper bolt setting
----------
aa=40mm
----------
a=19deg+-5deg b=41.5deg+-3deg
----------
aa=40mm
----------
a=19deg+-5deg b=41.5deg+-3deg
Stop lever angle
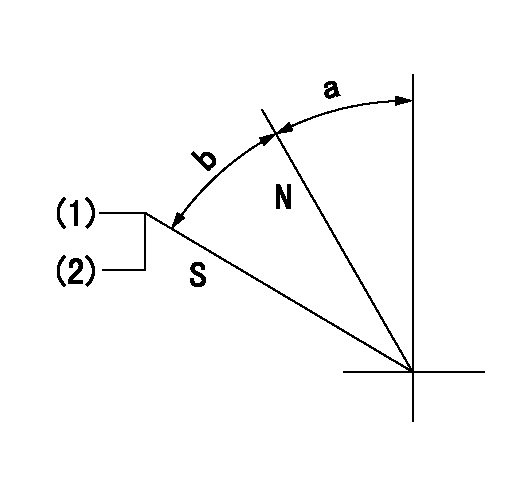
N:Pump normal
S:Stop the pump.
(1)Set the stopper bolt at speed = aa and rack position = bb and confirm non-injection (speed lever at full).
(2)Set the stopper bolt so that speed = cc and rack position = dd and confirm non-injection (with the speed lever at idle).
----------
aa=1400r/min bb=7-0.5mm cc=285r/min dd=(7.3)mm
----------
a=11.5deg+-5deg b=28deg+-5deg
----------
aa=1400r/min bb=7-0.5mm cc=285r/min dd=(7.3)mm
----------
a=11.5deg+-5deg b=28deg+-5deg
0000001501 LEVER
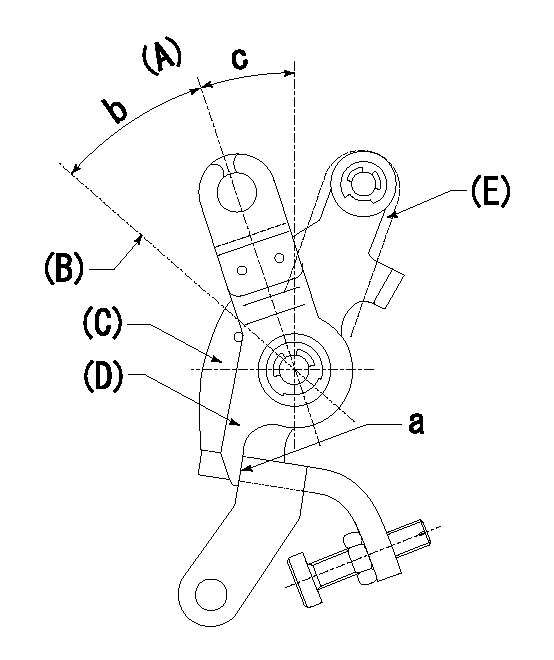
(A) Idle
(B) Full speed
(C) Base lever
(D) Accelerator lever
(E) Accelerator lever delivery position
1. Measure speed lever angle
(1)Measure the angle when the accelerator lever (D) contacted the base lever (C) at a.
----------
----------
b=41.5deg+-3deg c=19deg+-5deg
----------
----------
b=41.5deg+-3deg c=19deg+-5deg
Timing setting

(1)Pump vertical direction
(2)Position of timer's tooth at No 1 cylinder's beginning of injection
(3)B.T.D.C.: aa
(4)-
----------
aa=12deg
----------
a=(1deg)
----------
aa=12deg
----------
a=(1deg)
Information:
Features and Benefits
Reman short blocks expand the repair options available. When used with other
remanufactured products and reusable components from the core engine, short blocks help
lower dealer repair/rebuild cost and shorten turnaround time.
The 3500B short block is a fully assembled cylinder block with sequence valves, crankshaft,
cylinder pack groups, piston jets, camshaft bearings, and lifting eyes.
The short block does not include camshaft, cam access covers, or block side covers. The
short block may contain a remanufactured cylinder block, crankshaft, connecting rods, and
pistons. The cylinder liners, piston rings, camshaft bearings, and crankshaft bearings are
100% new components. The remanufactured components are remanufactured to factory
specifications using factory precision machine tools and proven processes.
Core Acceptance
Short blocks from 3500B diesel series machine and commercial engines that were built with
101-0829 Piston ? Rod Gp. are acceptable as core. Reference SELD0026 for the latest Short
Block Core Acceptance Criteria.
Core Management
Please refer to the Caterpillar Core Management Information System (CMIS 2) Parts
Information application describing all reman part/CAF and related information. Also refer to
other CMIS 2 inquiry applications such as Customer Profiles, Inspection Reason Codes,
Inspection Line Inquiry, Add Charge Information, Entitlement Activity, Entitlement Inquiry,
CCR Inquiry, CCR Entry, Shipment Processing; Process Packaging Grief; and Reporting to
properly manage core returns and monitor inspection performance. This information will be
available to all dealers worldwide after your CMIS 2 conversion date. In the meantime,
please continue to use the current CMIS Entitlement Parts Inquiry Screen describing the list
of parts in a Core Acceptability Family (CAF) and related part number detail.
For the latest updates of Reman Policies and Core Management (SELD0122), Core
Management Systems & Operations Procedures (SELD0040), and Shipping Instructions
(SELD0039), go to the Reman website and click on Procedures and Policies (listed under
Reman Program Information).
Please note that 3500B short block core will be shipped to Lafayette address:
Caterpillar Inc.
3701 State Road 26 East
Lafayette, Indiana, 47905
U.S.A.
See "SHIPPING INSTRUCTIONS" (SELD0039) for more information.
If you have any questions regarding core return processing, feel free to call Corinth toll free
at (800) 537-2928. For assistance with technical questions, call the Peoria Reman
Customer Satisfaction Hot Line also toll free at (888) 88-REMAN or use our E-mail
address--Reman_Help.
James E. Reynolds
Dept: 3500 Reman Engines
Location: 88-B21L
Phone: 765-448-2295
Fax: 765-448-5897