Information injection-pump assembly
BOSCH
9 400 611 710
9400611710
ZEXEL
101608-1990
1016081990
MITSUBISHI
ME170451
me170451
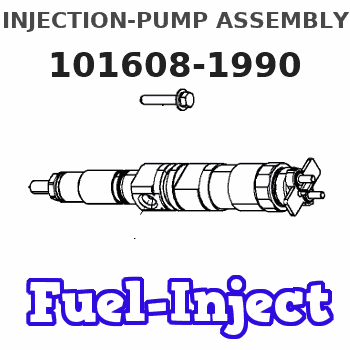
Rating:
Service parts 101608-1990 INJECTION-PUMP ASSEMBLY:
1.
_
6.
COUPLING PLATE
7.
COUPLING PLATE
8.
_
9.
_
11.
Nozzle and Holder
ME072745
12.
Open Pre:MPa(Kqf/cm2)
15.7{160}/21.6{220}
14.
NOZZLE
Cross reference number
BOSCH
9 400 611 710
9400611710
ZEXEL
101608-1990
1016081990
MITSUBISHI
ME170451
me170451
Zexel num
Bosch num
Firm num
Name
101608-1990
9 400 611 710
ME170451 MITSUBISHI
INJECTION-PUMP ASSEMBLY
6D16T2 K 14BF INJECTION PUMP ASSY PE6AD PE
6D16T2 K 14BF INJECTION PUMP ASSY PE6AD PE
Calibration Data:
Adjustment conditions
Test oil
1404 Test oil ISO4113 or {SAEJ967d}
1404 Test oil ISO4113 or {SAEJ967d}
Test oil temperature
degC
40
40
45
Nozzle and nozzle holder
105780-8260
Bosch type code
9 430 610 133
Nozzle
105780-0120
Bosch type code
1 688 901 990
Nozzle holder
105780-2190
Opening pressure
MPa
18
Opening pressure
kgf/cm2
184
Injection pipe
Outer diameter - inner diameter - length (mm) mm 6-2-600
Outer diameter - inner diameter - length (mm) mm 6-2-600
Overflow valve
131424-8420
Overflow valve opening pressure
kPa
255
221
289
Overflow valve opening pressure
kgf/cm2
2.6
2.25
2.95
Tester oil delivery pressure
kPa
255
255
255
Tester oil delivery pressure
kgf/cm2
2.6
2.6
2.6
Direction of rotation (viewed from drive side)
Left L
Left L
Injection timing adjustment
Direction of rotation (viewed from drive side)
Left L
Left L
Injection order
1-5-3-6-
2-4
Pre-stroke
mm
3.2
3.15
3.25
Beginning of injection position
Governor side NO.1
Governor side NO.1
Difference between angles 1
Cal 1-5 deg. 60 59.5 60.5
Cal 1-5 deg. 60 59.5 60.5
Difference between angles 2
Cal 1-3 deg. 120 119.5 120.5
Cal 1-3 deg. 120 119.5 120.5
Difference between angles 3
Cal 1-6 deg. 180 179.5 180.5
Cal 1-6 deg. 180 179.5 180.5
Difference between angles 4
Cyl.1-2 deg. 240 239.5 240.5
Cyl.1-2 deg. 240 239.5 240.5
Difference between angles 5
Cal 1-4 deg. 300 299.5 300.5
Cal 1-4 deg. 300 299.5 300.5
Injection quantity adjustment
Adjusting point
-
Rack position
11.8
Pump speed
r/min
700
700
700
Each cylinder's injection qty
mm3/st.
104.5
101.4
107.6
Basic
*
Fixing the rack
*
Standard for adjustment of the maximum variation between cylinders
*
Injection quantity adjustment_02
Adjusting point
Z
Rack position
9.5+-0.5
Pump speed
r/min
260
260
260
Each cylinder's injection qty
mm3/st.
11.5
9.8
13.2
Fixing the rack
*
Standard for adjustment of the maximum variation between cylinders
*
Injection quantity adjustment_03
Adjusting point
A
Rack position
R1(11.8)
Pump speed
r/min
700
700
700
Average injection quantity
mm3/st.
104.5
103.5
105.5
Basic
*
Fixing the lever
*
Boost pressure
kPa
26.7
26.7
Boost pressure
mmHg
200
200
Injection quantity adjustment_04
Adjusting point
B
Rack position
R1+0.7
Pump speed
r/min
1400
1400
1400
Average injection quantity
mm3/st.
105.5
101.5
109.5
Fixing the lever
*
Boost pressure
kPa
26.7
26.7
Boost pressure
mmHg
200
200
Injection quantity adjustment_05
Adjusting point
C
Rack position
R2(R1-0.
2)
Pump speed
r/min
400
400
400
Average injection quantity
mm3/st.
109.5
105.5
113.5
Fixing the lever
*
Boost pressure
kPa
26.7
26.7
Boost pressure
mmHg
200
200
Injection quantity adjustment_06
Adjusting point
E
Rack position
R1+0.55
Pump speed
r/min
1100
1100
1100
Average injection quantity
mm3/st.
106.5
102.5
110.5
Fixing the lever
*
Boost pressure
kPa
26.7
26.7
Boost pressure
mmHg
200
200
Boost compensator adjustment
Pump speed
r/min
400
400
400
Rack position
R2-0.5
Boost pressure
kPa
7.3
6
8.6
Boost pressure
mmHg
55
45
65
Boost compensator adjustment_02
Pump speed
r/min
400
400
400
Rack position
R2(R1-0.
2)
Boost pressure
kPa
13.3
13.3
13.3
Boost pressure
mmHg
100
100
100
Timer adjustment
Pump speed
r/min
1000--
Advance angle
deg.
0
0
0
Remarks
Start
Start
Timer adjustment_02
Pump speed
r/min
950
Advance angle
deg.
0.5
Timer adjustment_03
Pump speed
r/min
1400
Advance angle
deg.
3.5
3
4
Remarks
Finish
Finish
Test data Ex:
Governor adjustment
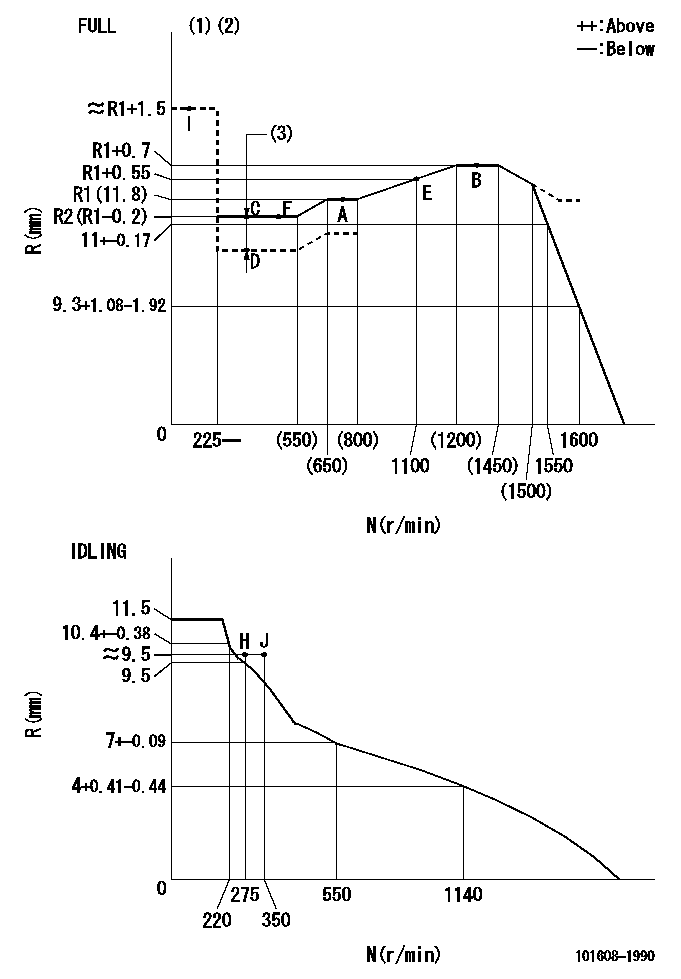
N:Pump speed
R:Rack position (mm)
(1)Torque cam stamping: T1
(2)Tolerance for racks not indicated: +-0.05mm.
(3)Boost compensator stroke: BCL
----------
T1=M18 BCL=0.5+-0.1mm
----------
----------
T1=M18 BCL=0.5+-0.1mm
----------
Speed control lever angle
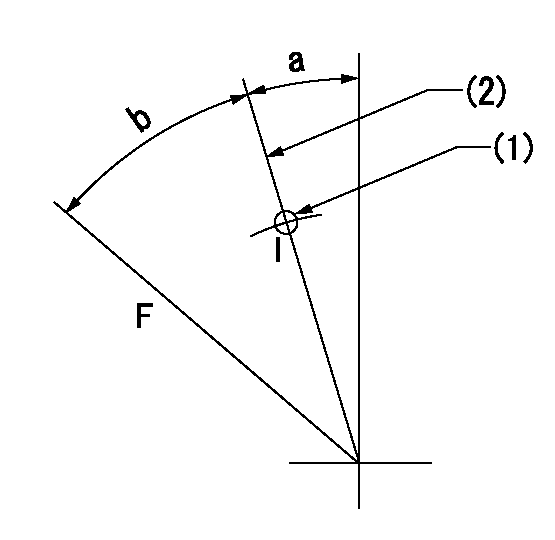
F:Full speed
I:Idle
(1)Use the hole at R = aa
(2)Stopper bolt set position 'H'
----------
aa=40mm
----------
a=18.5deg+-5deg b=42deg+-3deg
----------
aa=40mm
----------
a=18.5deg+-5deg b=42deg+-3deg
Stop lever angle

N:Pump normal
S:Stop the pump.
(1)With the speed lever at Full, set the stopper bolt so that speed = aa and rack position = bb (non-injection rack position). Confirm non-injection.
(2)With the speed lever at idle and after setting the stopper bolt, confirm non-injection at speed = cc. Rack position = dd (non-injection rack position)
----------
aa=1400r/min bb=7-0.5mm cc=275r/min dd=(7.5)mm
----------
a=11.5deg+-5deg b=28deg+-5deg
----------
aa=1400r/min bb=7-0.5mm cc=275r/min dd=(7.5)mm
----------
a=11.5deg+-5deg b=28deg+-5deg
0000001501 LEVER
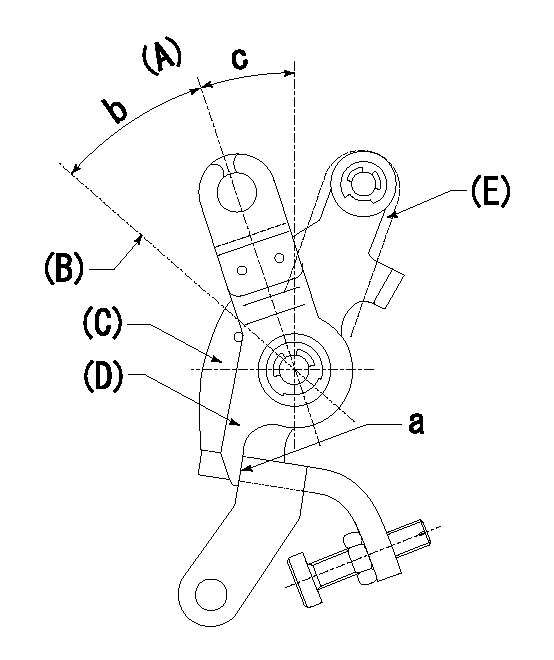
(A) Idle
(B) Full speed
(C) Base lever
(D) Accelerator lever
(E) Accelerator lever delivery position
1. Measure speed lever angle
(1)Measure the angle when the accelerator lever (D) contacted the base lever (C) at a.
----------
----------
b=42deg+-3deg c=18.5deg+-5deg
----------
----------
b=42deg+-3deg c=18.5deg+-5deg
Timing setting

(1)Pump vertical direction
(2)Position of timer's tooth at No 1 cylinder's beginning of injection
(3)B.T.D.C.: aa
(4)-
----------
aa=12deg
----------
a=(1deg)
----------
aa=12deg
----------
a=(1deg)
Information:
1. If necessary, remove the injector clamp bolt and clamp.
Illustration 1. Remove Clamp Bolt And Clamp.2. Remove jumper tube by removing two socket head cap screws on one end and loosening the tube nut on the other end. Refer to Illustrations 2 and 3.
Illustration 2. Remove Two Cap Screws.
Illustration 3. Loosen Tube Nut.
Make sure the small seat, shown in Illustration 4, is removed. Do not allow the seat to fall into any engine cavity, which could result in damage if unintentionally left inside the engine.Also, make sure the jumper tube is kept clean at all times. Dirt or other debris can get into the engine with this tube removed and cause possible damage.
Illustration 4. Do Not Lose Or Misplace Tube Seat.3. Remove four bolts and rocker arm assembly.
Illustration 5. Remove Rocker Arm Assembly.4. Remove inlet manifold bolt, as shown in Illustration 6.
Illustration 6. Remove Manifold Bolt.5. Remove the unit injector.6. Install a new injector brass sleeve or inspect and ream the existing sleeves as outlined in Tool Operating Manual NEHS0675. It is not necessary to ream new sleeves when using this procedure.7. Install the unit injector.
Do not install the injectors "off-engine" because the injector tip will protrude from the head and be subject to damage. If the injectors are installed off-engine, make sure the bottom surface of the head is raised off the surface of the work bench.
8. Install the injector forcing cover (8). Make sure the extending portion (small dowel) is in the oil supply hole of the injector. Also make sure wear button (10) is in place.
Illustration 7. Install Injector Forcing Cover (8) With Wear Button (10).9. Place a small amount of 4C-5591 Thread Lubricant on top of the injector forcing cover's wear button (10) and on the threads of forcing bolt (4).
Complete lubrication of the wear button and forcing bolt must be maintained for each injector seating procedure. Failure to relubricate each part before seating the next injector may cause premature wear or tool damage. Also, make sure the forcing bolt turns freely and does not have any damaged threads.
Illustration 8. Put A Small Amount Of Thread Lubricant On Wear Button.10. Install the forcing bridge with three 7X-0457 Bolts (5) and three 9M-1974 Hard Washers (6). Put the two long legs of the forcing bridge in the two rocker arm shaft support holes closest to the injector. The short leg of the forcing bridge sits on the intake manifold bolt boss.
Illustration 9. Install Forcing Bridge.11. Tighten forcing bridge mounting bolts (5) to 28 7 N m, 2.9 0.7 meter kg, (21 5 lb. ft.).
Damage to the head could occur if bridge mounting bolts (5) are not tightened to the specified torque.
Illustration 10. Tighten Forcing Bridge Bolts.12. Tighten the forcing bolt finger tight.13. Use a 9U-5019 Torque Wrench and tighten the forcing bolts to 34 1.4 N m, 3.5
Illustration 1. Remove Clamp Bolt And Clamp.2. Remove jumper tube by removing two socket head cap screws on one end and loosening the tube nut on the other end. Refer to Illustrations 2 and 3.
Illustration 2. Remove Two Cap Screws.
Illustration 3. Loosen Tube Nut.
Make sure the small seat, shown in Illustration 4, is removed. Do not allow the seat to fall into any engine cavity, which could result in damage if unintentionally left inside the engine.Also, make sure the jumper tube is kept clean at all times. Dirt or other debris can get into the engine with this tube removed and cause possible damage.
Illustration 4. Do Not Lose Or Misplace Tube Seat.3. Remove four bolts and rocker arm assembly.
Illustration 5. Remove Rocker Arm Assembly.4. Remove inlet manifold bolt, as shown in Illustration 6.
Illustration 6. Remove Manifold Bolt.5. Remove the unit injector.6. Install a new injector brass sleeve or inspect and ream the existing sleeves as outlined in Tool Operating Manual NEHS0675. It is not necessary to ream new sleeves when using this procedure.7. Install the unit injector.
Do not install the injectors "off-engine" because the injector tip will protrude from the head and be subject to damage. If the injectors are installed off-engine, make sure the bottom surface of the head is raised off the surface of the work bench.
8. Install the injector forcing cover (8). Make sure the extending portion (small dowel) is in the oil supply hole of the injector. Also make sure wear button (10) is in place.
Illustration 7. Install Injector Forcing Cover (8) With Wear Button (10).9. Place a small amount of 4C-5591 Thread Lubricant on top of the injector forcing cover's wear button (10) and on the threads of forcing bolt (4).
Complete lubrication of the wear button and forcing bolt must be maintained for each injector seating procedure. Failure to relubricate each part before seating the next injector may cause premature wear or tool damage. Also, make sure the forcing bolt turns freely and does not have any damaged threads.
Illustration 8. Put A Small Amount Of Thread Lubricant On Wear Button.10. Install the forcing bridge with three 7X-0457 Bolts (5) and three 9M-1974 Hard Washers (6). Put the two long legs of the forcing bridge in the two rocker arm shaft support holes closest to the injector. The short leg of the forcing bridge sits on the intake manifold bolt boss.
Illustration 9. Install Forcing Bridge.11. Tighten forcing bridge mounting bolts (5) to 28 7 N m, 2.9 0.7 meter kg, (21 5 lb. ft.).
Damage to the head could occur if bridge mounting bolts (5) are not tightened to the specified torque.
Illustration 10. Tighten Forcing Bridge Bolts.12. Tighten the forcing bolt finger tight.13. Use a 9U-5019 Torque Wrench and tighten the forcing bolts to 34 1.4 N m, 3.5
Have questions with 101608-1990?
Group cross 101608-1990 ZEXEL
Mitsubishi
101608-1990
9 400 611 710
ME170451
INJECTION-PUMP ASSEMBLY
6D16T2
6D16T2