Information injection-pump assembly
ZEXEL
101608-1800
1016081800
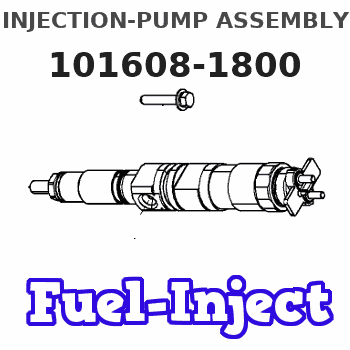
Rating:
Service parts 101608-1800 INJECTION-PUMP ASSEMBLY:
1.
_
6.
COUPLING PLATE
7.
COUPLING PLATE
8.
_
9.
_
11.
Nozzle and Holder
ME078067
12.
Open Pre:MPa(Kqf/cm2)
17.7{180}
15.
NOZZLE SET
Cross reference number
ZEXEL
101608-1800
1016081800
Zexel num
Bosch num
Firm num
Name
101608-1800
INJECTION-PUMP ASSEMBLY
6D16T 14BF PE6AD PE
6D16T 14BF PE6AD PE
Calibration Data:
Adjustment conditions
Test oil
1404 Test oil ISO4113 or {SAEJ967d}
1404 Test oil ISO4113 or {SAEJ967d}
Test oil temperature
degC
40
40
45
Nozzle and nozzle holder
105780-8140
Bosch type code
EF8511/9A
Nozzle
105780-0000
Bosch type code
DN12SD12T
Nozzle holder
105780-2080
Bosch type code
EF8511/9
Opening pressure
MPa
17.2
Opening pressure
kgf/cm2
175
Injection pipe
Outer diameter - inner diameter - length (mm) mm 6-2-600
Outer diameter - inner diameter - length (mm) mm 6-2-600
Overflow valve
131424-5520
Overflow valve opening pressure
kPa
255
221
289
Overflow valve opening pressure
kgf/cm2
2.6
2.25
2.95
Tester oil delivery pressure
kPa
157
157
157
Tester oil delivery pressure
kgf/cm2
1.6
1.6
1.6
Direction of rotation (viewed from drive side)
Left L
Left L
Injection timing adjustment
Direction of rotation (viewed from drive side)
Left L
Left L
Injection order
1-5-3-6-
2-4
Pre-stroke
mm
4.5
4.45
4.55
Beginning of injection position
Governor side NO.1
Governor side NO.1
Difference between angles 1
Cal 1-5 deg. 60 59.5 60.5
Cal 1-5 deg. 60 59.5 60.5
Difference between angles 2
Cal 1-3 deg. 120 119.5 120.5
Cal 1-3 deg. 120 119.5 120.5
Difference between angles 3
Cal 1-6 deg. 180 179.5 180.5
Cal 1-6 deg. 180 179.5 180.5
Difference between angles 4
Cyl.1-2 deg. 240 239.5 240.5
Cyl.1-2 deg. 240 239.5 240.5
Difference between angles 5
Cal 1-4 deg. 300 299.5 300.5
Cal 1-4 deg. 300 299.5 300.5
Injection quantity adjustment
Adjusting point
A
Rack position
10.6
Pump speed
r/min
1400
1400
1400
Average injection quantity
mm3/st.
106
105
107
Max. variation between cylinders
%
0
-2.5
2.5
Basic
*
Fixing the lever
*
Boost pressure
kPa
44
44
Boost pressure
mmHg
330
330
Injection quantity adjustment_02
Adjusting point
C
Rack position
8+-0.5
Pump speed
r/min
350
350
350
Average injection quantity
mm3/st.
8
6.5
9.5
Max. variation between cylinders
%
0
-15
15
Fixing the rack
*
Boost pressure
kPa
0
0
0
Boost pressure
mmHg
0
0
0
Boost compensator adjustment
Pump speed
r/min
650
650
650
Rack position
R1-0.9
Boost pressure
kPa
20
17.3
22.7
Boost pressure
mmHg
150
130
170
Boost compensator adjustment_02
Pump speed
r/min
650
650
650
Rack position
R1(10.6)
Boost pressure
kPa
30.7
24
37.4
Boost pressure
mmHg
230
180
280
Timer adjustment
Pump speed
r/min
1150--
Advance angle
deg.
0
0
0
Load
4/4
Remarks
Beginning of advance.
Beginning of advance.
Timer adjustment_02
Pump speed
r/min
450
Advance angle
deg.
2
1.5
2.5
Load
0/4
Remarks
Start
Start
Timer adjustment_03
Pump speed
r/min
(550)
Advance angle
deg.
0
0
0
Load
0/4
Remarks
Measure the actual speed.
Measure the actual speed.
Timer adjustment_04
Pump speed
r/min
1100
Advance angle
deg.
0.5
Load
4/4
Timer adjustment_05
Pump speed
r/min
1400
Advance angle
deg.
2.5
2
3
Load
4/4
Remarks
Finish
Finish
Test data Ex:
Governor adjustment
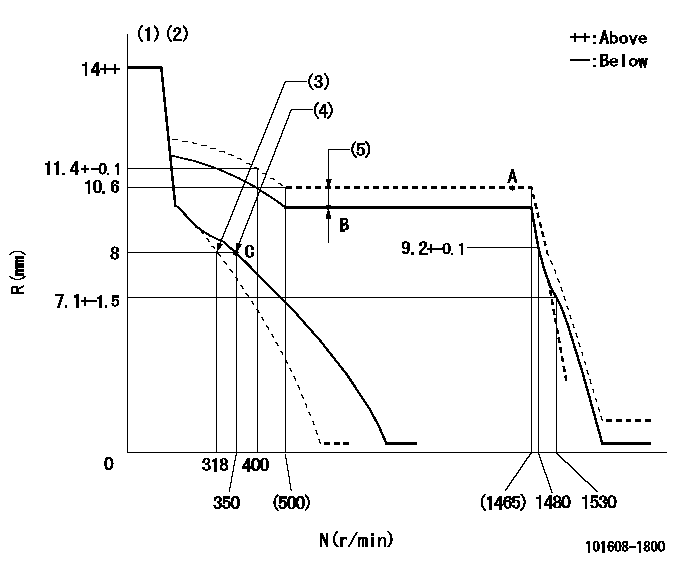
N:Pump speed
R:Rack position (mm)
(1)Target notch: K
(2)Tolerance for racks not indicated: +-0.05mm.
(3)Main spring setting
(4)Set idle sub-spring
(5)Boost compensator stroke: BCL
----------
K=13 BCL=0.9+-0.1mm
----------
----------
K=13 BCL=0.9+-0.1mm
----------
Speed control lever angle

F:Full speed
I:Idle
(1)Stopper bolt setting
----------
----------
a=(30deg)+-5deg b=(20deg)+-5deg
----------
----------
a=(30deg)+-5deg b=(20deg)+-5deg
Stop lever angle
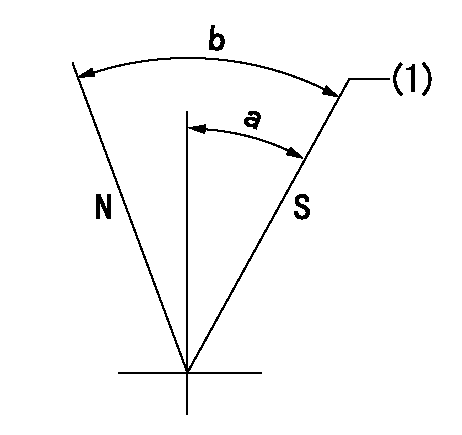
N:Pump normal
S:Stop the pump.
(1)Pump speed aa and rack position bb (to be sealed at delivery)
----------
aa=0r/min bb=1-0.5mm
----------
a=35deg+-5deg b=(55deg)
----------
aa=0r/min bb=1-0.5mm
----------
a=35deg+-5deg b=(55deg)
0000001501 TAMPER PROOF

Tamperproofing-equipped boost compensator cover installation procedure
(A) After adjusting the boost compensator, tighten the bolts to remove the heads.
(1)Before adjusting the governor and the boost compensator, tighten the screw to the specified torque.
(Tightening torque T = T1 maximum)
(2)After adjusting the governor and the boost compensator, tighten to the specified torque to break off the bolt heads.
(Tightening torque T = T2)
----------
T1=2.5N-m(0.25kgf-m) T2=2.9~4.4N-m(0.3~0.45kgf-m)
----------
----------
T1=2.5N-m(0.25kgf-m) T2=2.9~4.4N-m(0.3~0.45kgf-m)
----------
Timing setting

(1)Pump vertical direction
(2)Position of timer's tooth at No 1 cylinder's beginning of injection
(3)B.T.D.C.: aa
(4)-
----------
aa=10deg
----------
a=(1deg)
----------
aa=10deg
----------
a=(1deg)
Information:
6. Full-load Quantity for Starting a warmed-up Engine
When the engine is warmed-up, it is not necessary to operate the lever (9) for additional fuel.7. Stopping the Engine
For stopping the engine, the starting and stopping lever (9) must be pulled beyond the starting position until it rests firmly against the stop. When pulling the lever slowly, the engine will speed up again before stopping.8. Operating the Tractor
The hydraulic governor of the distributor-type pump functions in the same manner as a mechanical governor (RSV governor) of an in-line pump. It is, however, more sensitive to response than the mechanical governor.Pump Illustrations
Fuel Circuit Of Distributor - Type Pump
Checking The Fuel-Injection Pump Drive And Replacing Components (as from 3 cylinder engine)
1. Check the gearwheel and hub or injection timer. If necessary, dismantle the gearwheel from the hub or from the injection timer.2. Renew the defective component.
7-492.1 Assemble the gearwheel and hub so that the punch mark registers with the groove in the hub.Fig. 7-49, right2.2 Assemble the gearwhell to the injection timer so that the recess in the former registers with the groove in the hub.Fig. 7-49, left Important:As from 1975, the hub was modified in the case of rigid drive.
7-502.3 In the case of in-line injection pump, mount gearwheel onto steel hub.Fig. 7-50, right2.4 In the case of distributor injection pump, mount gearwheel reversed onto the hub.Fig. 7-50 left Observe markings and angular degrees.Dismantling And Installing Injectors
Dismantling:
1. Dismantle leak-off line to injector. Disconnect injection delivery line on injection.2. Dismantle stirrup and remove thrust piece.
7-513. Remove injector using extracting device No. 150800.Fig. 7-51, Attention:In addition, use threaded piece No. 110050 in case of lateral connection of injection delivery line.Fig. 7-51, leftUse extractor No. 110030 in case of top connection of injection delivery line.Fig. 7-51, right
7-52On FL 912 W remove injector by special wrench No. 110010 plus insert No. 110020.Fig. 7-52
7-534. Remove joint washer from injector or from cylinder head, as the case may be. (Extractor No. 120630)Fig. 7-53, leftIn case of FL 912 W, remove heat insulating plate (using, for example, bent wire).Fig. 7-53, rightInstalling:
7-541. Stick new joint washer with grease (graphited side facing towards injector).Fig. 7-54 On FL 912 install heat guard as shown.Fig. 7-53, right2. Install injector.
7-553. Install thrust piece and place stirrup in position.Fig. 7-55, left4. Place washer with convex side facing stirrup and screw on nut.(See Specification Data)5. On FL 912 W align injector to injection pipe.Fig. 7-55, right
7-566. Tighten injector by special wrench No. 110010 plus insert No. 110020.Fig. 7-567. Tighten injector and fit leak-oil line with new sealing rings.Removing And Refitting Injector On Engine Provided With Exhaust Air Heating
Preliminary work:
Injector is removed.1. Stick by means of grease sealing ring to injector and insert the latter in the cylinder head.
7-572. Slip rubber seal on injector and the vertical pin (see arrow) for fixture.Fig. 7-57
7-583. Apply leak oil pan (arrow). Slip spring and spacer sleeve on pin for fixture.Fig. 7-584. Apply clamping piece and fixture.5. Apply washer the curved side of which must show towards fixture; screw on
When the engine is warmed-up, it is not necessary to operate the lever (9) for additional fuel.7. Stopping the Engine
For stopping the engine, the starting and stopping lever (9) must be pulled beyond the starting position until it rests firmly against the stop. When pulling the lever slowly, the engine will speed up again before stopping.8. Operating the Tractor
The hydraulic governor of the distributor-type pump functions in the same manner as a mechanical governor (RSV governor) of an in-line pump. It is, however, more sensitive to response than the mechanical governor.Pump Illustrations
Fuel Circuit Of Distributor - Type Pump
Checking The Fuel-Injection Pump Drive And Replacing Components (as from 3 cylinder engine)
1. Check the gearwheel and hub or injection timer. If necessary, dismantle the gearwheel from the hub or from the injection timer.2. Renew the defective component.
7-492.1 Assemble the gearwheel and hub so that the punch mark registers with the groove in the hub.Fig. 7-49, right2.2 Assemble the gearwhell to the injection timer so that the recess in the former registers with the groove in the hub.Fig. 7-49, left Important:As from 1975, the hub was modified in the case of rigid drive.
7-502.3 In the case of in-line injection pump, mount gearwheel onto steel hub.Fig. 7-50, right2.4 In the case of distributor injection pump, mount gearwheel reversed onto the hub.Fig. 7-50 left Observe markings and angular degrees.Dismantling And Installing Injectors
Dismantling:
1. Dismantle leak-off line to injector. Disconnect injection delivery line on injection.2. Dismantle stirrup and remove thrust piece.
7-513. Remove injector using extracting device No. 150800.Fig. 7-51, Attention:In addition, use threaded piece No. 110050 in case of lateral connection of injection delivery line.Fig. 7-51, leftUse extractor No. 110030 in case of top connection of injection delivery line.Fig. 7-51, right
7-52On FL 912 W remove injector by special wrench No. 110010 plus insert No. 110020.Fig. 7-52
7-534. Remove joint washer from injector or from cylinder head, as the case may be. (Extractor No. 120630)Fig. 7-53, leftIn case of FL 912 W, remove heat insulating plate (using, for example, bent wire).Fig. 7-53, rightInstalling:
7-541. Stick new joint washer with grease (graphited side facing towards injector).Fig. 7-54 On FL 912 install heat guard as shown.Fig. 7-53, right2. Install injector.
7-553. Install thrust piece and place stirrup in position.Fig. 7-55, left4. Place washer with convex side facing stirrup and screw on nut.(See Specification Data)5. On FL 912 W align injector to injection pipe.Fig. 7-55, right
7-566. Tighten injector by special wrench No. 110010 plus insert No. 110020.Fig. 7-567. Tighten injector and fit leak-oil line with new sealing rings.Removing And Refitting Injector On Engine Provided With Exhaust Air Heating
Preliminary work:
Injector is removed.1. Stick by means of grease sealing ring to injector and insert the latter in the cylinder head.
7-572. Slip rubber seal on injector and the vertical pin (see arrow) for fixture.Fig. 7-57
7-583. Apply leak oil pan (arrow). Slip spring and spacer sleeve on pin for fixture.Fig. 7-584. Apply clamping piece and fixture.5. Apply washer the curved side of which must show towards fixture; screw on
Have questions with 101608-1800?
Group cross 101608-1800 ZEXEL
101608-1800
INJECTION-PUMP ASSEMBLY
6D16T
6D16T