Information injection-pump assembly
BOSCH
9 400 615 775
9400615775
ZEXEL
101608-1100
1016081100
MITSUBISHI
ME075718
me075718
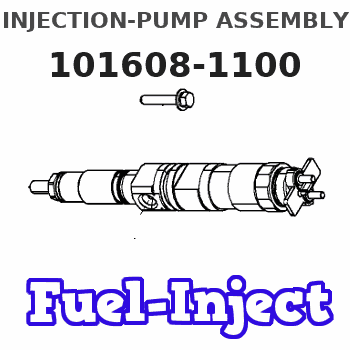
Rating:
Service parts 101608-1100 INJECTION-PUMP ASSEMBLY:
1.
_
6.
COUPLING PLATE
7.
COUPLING PLATE
8.
_
9.
_
11.
Nozzle and Holder
12.
Open Pre:MPa(Kqf/cm2)
15.7{160}/21.6{220}
14.
NOZZLE
Include in #1:
101608-1100
as INJECTION-PUMP ASSEMBLY
Include in #2:
104746-5570
as _
Cross reference number
BOSCH
9 400 615 775
9400615775
ZEXEL
101608-1100
1016081100
MITSUBISHI
ME075718
me075718
Zexel num
Bosch num
Firm num
Name
101608-1100
9 400 615 775
ME075718 MITSUBISHI
INJECTION-PUMP ASSEMBLY
6D17 K
6D17 K
Calibration Data:
Adjustment conditions
Test oil
1404 Test oil ISO4113 or {SAEJ967d}
1404 Test oil ISO4113 or {SAEJ967d}
Test oil temperature
degC
40
40
45
Nozzle and nozzle holder
105780-8140
Bosch type code
EF8511/9A
Nozzle
105780-0000
Bosch type code
DN12SD12T
Nozzle holder
105780-2080
Bosch type code
EF8511/9
Opening pressure
MPa
17.2
Opening pressure
kgf/cm2
175
Injection pipe
Outer diameter - inner diameter - length (mm) mm 6-2-600
Outer diameter - inner diameter - length (mm) mm 6-2-600
Overflow valve
131424-8420
Overflow valve opening pressure
kPa
255
221
289
Overflow valve opening pressure
kgf/cm2
2.6
2.25
2.95
Tester oil delivery pressure
kPa
157
157
157
Tester oil delivery pressure
kgf/cm2
1.6
1.6
1.6
Direction of rotation (viewed from drive side)
Left L
Left L
Injection timing adjustment
Direction of rotation (viewed from drive side)
Left L
Left L
Injection order
1-5-3-6-
2-4
Pre-stroke
mm
3.2
3.15
3.25
Beginning of injection position
Governor side NO.1
Governor side NO.1
Difference between angles 1
Cal 1-5 deg. 60 59.5 60.5
Cal 1-5 deg. 60 59.5 60.5
Difference between angles 2
Cal 1-3 deg. 120 119.5 120.5
Cal 1-3 deg. 120 119.5 120.5
Difference between angles 3
Cal 1-6 deg. 180 179.5 180.5
Cal 1-6 deg. 180 179.5 180.5
Difference between angles 4
Cyl.1-2 deg. 240 239.5 240.5
Cyl.1-2 deg. 240 239.5 240.5
Difference between angles 5
Cal 1-4 deg. 300 299.5 300.5
Cal 1-4 deg. 300 299.5 300.5
Injection quantity adjustment
Adjusting point
-
Rack position
12
Pump speed
r/min
850
850
850
Each cylinder's injection qty
mm3/st.
85.1
82.5
87.7
Basic
*
Fixing the rack
*
Standard for adjustment of the maximum variation between cylinders
*
Injection quantity adjustment_02
Adjusting point
Z
Rack position
9.5+-0.5
Pump speed
r/min
800
800
800
Each cylinder's injection qty
mm3/st.
10.8
9.2
12.4
Fixing the rack
*
Standard for adjustment of the maximum variation between cylinders
*
Injection quantity adjustment_03
Adjusting point
A
Rack position
R1(12)
Pump speed
r/min
850
850
850
Average injection quantity
mm3/st.
85.1
84.1
86.1
Basic
*
Fixing the lever
*
Injection quantity adjustment_04
Adjusting point
B
Rack position
R1+0.85
Pump speed
r/min
1450
1450
1450
Average injection quantity
mm3/st.
99.9
95.9
103.9
Fixing the lever
*
Injection quantity adjustment_05
Adjusting point
I
Rack position
-
Pump speed
r/min
100
100
100
Average injection quantity
mm3/st.
91
81
101
Fixing the lever
*
Rack limit
*
Timer adjustment
Pump speed
r/min
1150--
Advance angle
deg.
0
0
0
Remarks
Start
Start
Timer adjustment_02
Pump speed
r/min
1100
Advance angle
deg.
0.5
Timer adjustment_03
Pump speed
r/min
1450
Advance angle
deg.
6
5.5
6.5
Remarks
Finish
Finish
Test data Ex:
Governor adjustment

N:Pump speed
R:Rack position (mm)
(1)Torque cam stamping: T1
(2)Tolerance for racks not indicated: +-0.05mm.
(3)RACK LIMIT
----------
T1=H28
----------
----------
T1=H28
----------
Speed control lever angle

F:Full speed
I:Idle
(1)Use the hole at R = aa
(2)Stopper bolt set position 'H'
----------
aa=29mm
----------
a=10deg+-5deg b=(47.5deg)+-3deg
----------
aa=29mm
----------
a=10deg+-5deg b=(47.5deg)+-3deg
Stop lever angle
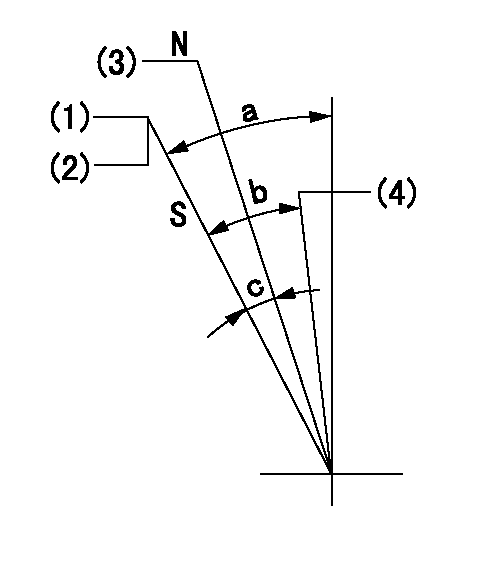
N:Engine manufacturer's normal use
S:Stop the pump.
(1)Set the stopper bolt at pump speed = aa and rack position = bb (non-injection rack position). Confirm non-injection.
(2)After setting the stopper bolt, confirm non-injection at speed cc. Rack position = dd (non-injection rack position).
(3)Rack position = approximately ee (speed lever full, speed = ff).
(4)Free (at delivery)
----------
aa=1450r/min bb=7.2-0.5mm cc=275r/min dd=(8.8)mm ee=15mm ff=0r/min
----------
a=36.5deg+-5deg b=(25deg) c=13deg+-5deg
----------
aa=1450r/min bb=7.2-0.5mm cc=275r/min dd=(8.8)mm ee=15mm ff=0r/min
----------
a=36.5deg+-5deg b=(25deg) c=13deg+-5deg
0000001201

F:At operation, hold it in the full speed position.
I:Idle
(1)At rack position aa and pump speed bb, set the stopper bolt. (After setting it, apply red paint.)
(2)Actual measurement
----------
aa=9.9+-0.1mm bb=1575r/min
----------
a=15deg+-5deg
----------
aa=9.9+-0.1mm bb=1575r/min
----------
a=15deg+-5deg
Timing setting

(1)Pump vertical direction
(2)Position of timer's tooth at No 1 cylinder's beginning of injection
(3)B.T.D.C.: aa
(4)-
----------
aa=10deg
----------
a=(2deg)
----------
aa=10deg
----------
a=(2deg)
Information:
Cleaning the DPF
Because the sections of the DPF are replaceable, a small stock of filter sections can be maintained. Filter sections from a small on-hand stock can be used to replace filters in service at the next scheduled cleaning. The removed filters can be cleaned and returned for installation in the next vehicle. This process of maintaining a stock of filter sections can significantly reduce the amount of down time that will occur.Note: Check State and Local air pollution regulations pertaining to record keeping of serviced filters. Some governmental entities may require filter tracking. Note: Perform a back pressure test prior to cleaning the DPF and record the results. After cleaning the DPF, run the engine at high idle for 5 to 15 minutes to bring the engine and exhaust system to operating temperature. Perform another back pressure test and record the results on the DPF cleaning records form.
Weigh and record the filter unit prior to baking.
By baking the filter under a controlled procedure, the remaining soot on the DPF will burn off and leave a smaller quantity of ash. Failure to observe this procedure can result to damage or cracking to the DPF substrate. A commercial programmable oven is required for this procedure. Careful adherence to this procedure is imperative. Deviation from this procedure may lead to thermal shock and cracking of the DPF substrate or melting at high temperatures.
Place filter into a programmable commercial oven designed for this purpose. Center the filter as much as possible on a rack with 2 inches of spacing below and above for best results.
Program the oven as follows:
Ramp oven temperature to 200° C (392° F)
Hold oven temperature at 200° C (392° F)
Ramp oven temperature to 450° C (842° F)
Hold oven temperature at 450° C (842° F)
Cool down to ambient temperature at natural rate within the oven with the doors closed. Do not use fans.
Place filter in cleaning machine and clean as per machine instructions.
Replace the filter in the oven. Ramp to 650° C (1202° F) in 60 minutes.
Hold oven temperature at 650° C (1202° F) for 240 minutes.
Cool to ambient temperature at a natural rate. Do not use fans.Note: Allow the filter to cool in the oven with the door closed until the filter can be handled with bare hands.Cleaning Procedure
Ash and soot should be removed from the DPF utilizing the Cat 319-2189 Diesel Particulate Filter Cleaner Gp. Using the cleaner without following baking procedure, results in lower efficiency cleaning and will reduce the life of the HEPA filters in the machine. The tool uses pulsed air to flush the ash and soot.Note: Other cleaning methods can release significant quantities of airborne ash and soot. Airborne ash and soot should not be inhaled and may be regulated as a hazardous substance by local regulations.Cleaned Filter Specification
The following steps determine if the DPF was properly cleaned:Note: This specification applies to filters that were cleaned of ash only. This specification is only valid subsequent to the recommend
Because the sections of the DPF are replaceable, a small stock of filter sections can be maintained. Filter sections from a small on-hand stock can be used to replace filters in service at the next scheduled cleaning. The removed filters can be cleaned and returned for installation in the next vehicle. This process of maintaining a stock of filter sections can significantly reduce the amount of down time that will occur.Note: Check State and Local air pollution regulations pertaining to record keeping of serviced filters. Some governmental entities may require filter tracking. Note: Perform a back pressure test prior to cleaning the DPF and record the results. After cleaning the DPF, run the engine at high idle for 5 to 15 minutes to bring the engine and exhaust system to operating temperature. Perform another back pressure test and record the results on the DPF cleaning records form.
Weigh and record the filter unit prior to baking.
By baking the filter under a controlled procedure, the remaining soot on the DPF will burn off and leave a smaller quantity of ash. Failure to observe this procedure can result to damage or cracking to the DPF substrate. A commercial programmable oven is required for this procedure. Careful adherence to this procedure is imperative. Deviation from this procedure may lead to thermal shock and cracking of the DPF substrate or melting at high temperatures.
Place filter into a programmable commercial oven designed for this purpose. Center the filter as much as possible on a rack with 2 inches of spacing below and above for best results.
Program the oven as follows:
Ramp oven temperature to 200° C (392° F)
Hold oven temperature at 200° C (392° F)
Ramp oven temperature to 450° C (842° F)
Hold oven temperature at 450° C (842° F)
Cool down to ambient temperature at natural rate within the oven with the doors closed. Do not use fans.
Place filter in cleaning machine and clean as per machine instructions.
Replace the filter in the oven. Ramp to 650° C (1202° F) in 60 minutes.
Hold oven temperature at 650° C (1202° F) for 240 minutes.
Cool to ambient temperature at a natural rate. Do not use fans.Note: Allow the filter to cool in the oven with the door closed until the filter can be handled with bare hands.Cleaning Procedure
Ash and soot should be removed from the DPF utilizing the Cat 319-2189 Diesel Particulate Filter Cleaner Gp. Using the cleaner without following baking procedure, results in lower efficiency cleaning and will reduce the life of the HEPA filters in the machine. The tool uses pulsed air to flush the ash and soot.Note: Other cleaning methods can release significant quantities of airborne ash and soot. Airborne ash and soot should not be inhaled and may be regulated as a hazardous substance by local regulations.Cleaned Filter Specification
The following steps determine if the DPF was properly cleaned:Note: This specification applies to filters that were cleaned of ash only. This specification is only valid subsequent to the recommend
Have questions with 101608-1100?
Group cross 101608-1100 ZEXEL
Mitsubishi
101608-1100
9 400 615 775
ME075718
INJECTION-PUMP ASSEMBLY
6D17
6D17