Information injection-pump assembly
BOSCH
9 400 619 850
9400619850
ZEXEL
101608-1010
1016081010
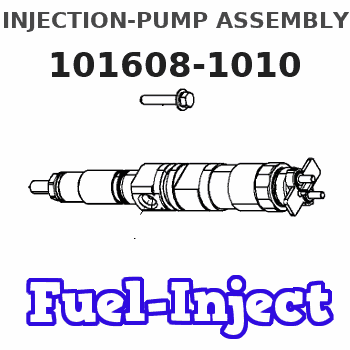
Rating:
Service parts 101608-1010 INJECTION-PUMP ASSEMBLY:
1.
_
6.
COUPLING PLATE
7.
COUPLING PLATE
8.
_
9.
_
11.
Nozzle and Holder
12.
Open Pre:MPa(Kqf/cm2)
15.7{160}/21.6{220}
14.
NOZZLE
Include in #1:
101608-1010
as INJECTION-PUMP ASSEMBLY
Include in #2:
104746-5472
as _
Cross reference number
BOSCH
9 400 619 850
9400619850
ZEXEL
101608-1010
1016081010
Zexel num
Bosch num
Firm num
Name
Calibration Data:
Adjustment conditions
Test oil
1404 Test oil ISO4113 or {SAEJ967d}
1404 Test oil ISO4113 or {SAEJ967d}
Test oil temperature
degC
40
40
45
Nozzle and nozzle holder
105780-8140
Bosch type code
EF8511/9A
Nozzle
105780-0000
Bosch type code
DN12SD12T
Nozzle holder
105780-2080
Bosch type code
EF8511/9
Opening pressure
MPa
17.2
Opening pressure
kgf/cm2
175
Injection pipe
Outer diameter - inner diameter - length (mm) mm 6-2-600
Outer diameter - inner diameter - length (mm) mm 6-2-600
Overflow valve
131424-8420
Overflow valve opening pressure
kPa
255
221
289
Overflow valve opening pressure
kgf/cm2
2.6
2.25
2.95
Tester oil delivery pressure
kPa
157
157
157
Tester oil delivery pressure
kgf/cm2
1.6
1.6
1.6
Direction of rotation (viewed from drive side)
Left L
Left L
Injection timing adjustment
Direction of rotation (viewed from drive side)
Left L
Left L
Injection order
1-5-3-6-
2-4
Pre-stroke
mm
3.2
3.15
3.25
Beginning of injection position
Governor side NO.1
Governor side NO.1
Difference between angles 1
Cal 1-5 deg. 60 59.5 60.5
Cal 1-5 deg. 60 59.5 60.5
Difference between angles 2
Cal 1-3 deg. 120 119.5 120.5
Cal 1-3 deg. 120 119.5 120.5
Difference between angles 3
Cal 1-6 deg. 180 179.5 180.5
Cal 1-6 deg. 180 179.5 180.5
Difference between angles 4
Cyl.1-2 deg. 240 239.5 240.5
Cyl.1-2 deg. 240 239.5 240.5
Difference between angles 5
Cal 1-4 deg. 300 299.5 300.5
Cal 1-4 deg. 300 299.5 300.5
Injection quantity adjustment
Adjusting point
-
Rack position
11.9
Pump speed
r/min
850
850
850
Each cylinder's injection qty
mm3/st.
86.5
83.9
89.1
Basic
*
Fixing the rack
*
Standard for adjustment of the maximum variation between cylinders
*
Injection quantity adjustment_02
Adjusting point
Z
Rack position
9.5+-0.5
Pump speed
r/min
600
600
600
Each cylinder's injection qty
mm3/st.
10.8
9.2
12.4
Fixing the rack
*
Standard for adjustment of the maximum variation between cylinders
*
Injection quantity adjustment_03
Adjusting point
A
Rack position
R1(11.9)
Pump speed
r/min
850
850
850
Average injection quantity
mm3/st.
86.5
85.5
87.5
Basic
*
Fixing the lever
*
Injection quantity adjustment_04
Adjusting point
B
Rack position
R1+0.35
Pump speed
r/min
1450
1450
1450
Average injection quantity
mm3/st.
90.5
86.5
94.5
Fixing the lever
*
Injection quantity adjustment_05
Adjusting point
C
Rack position
R1-0.4
Pump speed
r/min
500
500
500
Average injection quantity
mm3/st.
71.5
67.5
75.5
Fixing the lever
*
Injection quantity adjustment_06
Adjusting point
I
Rack position
-
Pump speed
r/min
100
100
100
Average injection quantity
mm3/st.
95
85
105
Fixing the lever
*
Rack limit
*
Timer adjustment
Pump speed
r/min
1150--
Advance angle
deg.
0
0
0
Remarks
Start
Start
Timer adjustment_02
Pump speed
r/min
1100
Advance angle
deg.
0.5
Timer adjustment_03
Pump speed
r/min
1450
Advance angle
deg.
5
4.5
5.5
Remarks
Finish
Finish
Test data Ex:
Governor adjustment

N:Pump speed
R:Rack position (mm)
(1)Torque cam stamping: T1
(2)Tolerance for racks not indicated: +-0.05mm.
(3)RACK LIMIT
----------
T1=K60
----------
----------
T1=K60
----------
Speed control lever angle
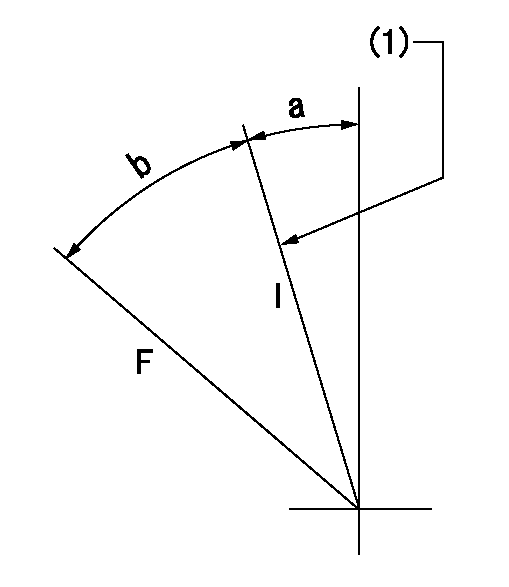
F:Full speed
I:Idle
(1)Stopper bolt set position 'H'
----------
----------
a=18.5deg+-5deg b=42deg+-3deg
----------
----------
a=18.5deg+-5deg b=42deg+-3deg
Stop lever angle
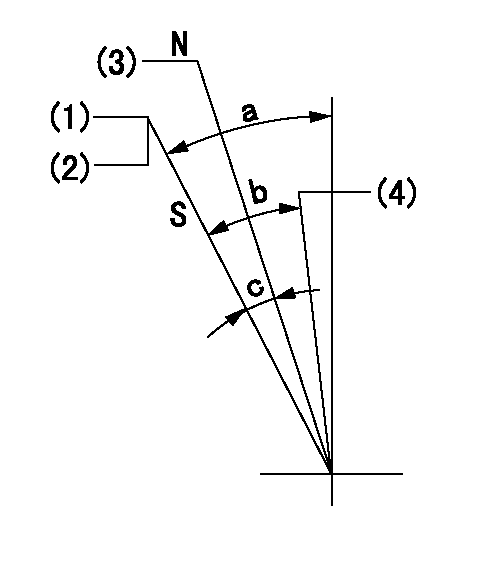
N:Engine manufacturer's normal use
S:Stop the pump.
(1)Set the stopper bolt at pump speed = aa and rack position = bb (non-injection rack position). Confirm non-injection.
(2)After setting the stopper bolt, confirm non-injection at speed cc. Rack position = dd (non-injection rack position).
(3)Rack position = approximately ee (speed lever full, speed = ff).
(4)Free (at delivery)
----------
aa=1450r/min bb=7.2-0.5mm cc=275r/min dd=(8.8)mm ee=15mm ff=0r/min
----------
a=36.5deg+-5deg b=(25deg) c=13deg+-5deg
----------
aa=1450r/min bb=7.2-0.5mm cc=275r/min dd=(8.8)mm ee=15mm ff=0r/min
----------
a=36.5deg+-5deg b=(25deg) c=13deg+-5deg
0000001501 LEVER
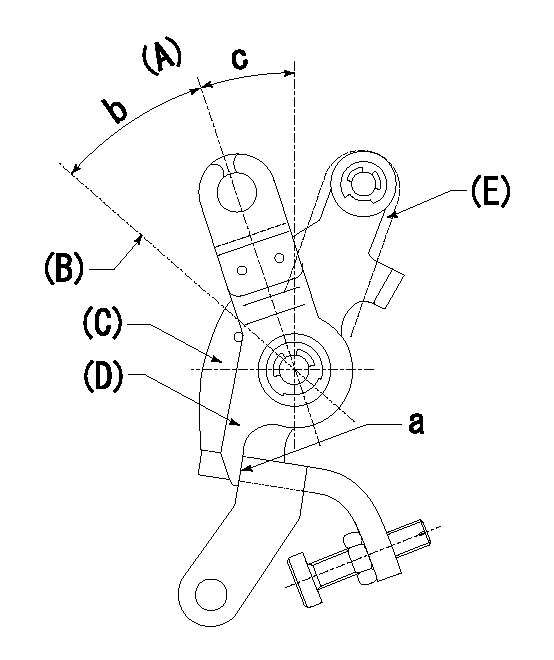
(A) Idle
(B) Full speed
(C) Base lever
(D) Accelerator lever
(E) Accelerator lever delivery position
1. Measure speed lever angle
(1)Measure the angle when the accelerator lever (D) contacted the base lever (C) at a.
----------
----------
b=42deg+-3deg c=18.5deg+-5deg
----------
----------
b=42deg+-3deg c=18.5deg+-5deg
Timing setting

(1)Pump vertical direction
(2)Position of timer's tooth at No 1 cylinder's beginning of injection
(3)B.T.D.C.: aa
(4)-
----------
aa=7deg
----------
a=(3deg)
----------
aa=7deg
----------
a=(3deg)
Information:
Introduction
The problem that is identified below does not have a known permanent solution. Until a permanent solution is known, use the solution that is identified below.Problem
Fuel Injectors in 797F powered Off-Highway Trucks engines are not reaching expected mid-life target. The typical failure mode is a "-2" or a "-7" code on the fuel injectors.Solution
This will be an interim troubleshooting procedure to follow for trucks running with a special test software. Prior to executing this procedure, utilize Cat ® Electronic Technician (Cat ET) or Advisor to verify if any logged codes have been logged. Certain injector diagnostics do not notify the operator or light the check engine light upon activation."Fuel system verification-Test" procedure applies to trucks running with following software versions only.
Engine - LRC 3655600-31 (Test)
Engine - Tier II 5297866-05 (Test)
Engine - HAA (4x2) 3253178-39 (Test)
Engine - Tier II Custom 4727209-12 (Test)Troubleshooting Procedure
Table 1
Troubleshooting Test Steps Values Results
1. Check for Diagnostic Codes
A. Establish communication between Cat® (Electronic Technician) ET and the engine ECM. Cat ET must be configured for Dual Data Link Communications to perform this procedure. Refer to Troubleshooting, "Electronic Service Tools", if necessary.
B. Determine the diagnostic code that relates to an injector. Codes
Result: A -2 code is present.
Repair: Perform the following procedure:
1. Do not clear the diagnostic code.
Access the Fuel System Verification Test by accessing the following display screens:
- Diagnostics
- Diagnostic Tests
- Fuel System Verification Test
3. Perform the Fuel System Verification Test.
If the injector passes the test, the injector is "OK". Cat ET will clear the code.
Result: If the injector fails the test, perform the following procedure:
a. Replace the injector.
b. Flash program the trim file for the new injector into the ECM. Refer to Troubleshooting, "Injector Trim File - Install", if necessary.
c. Perform the Fuel System Verification Test again. This test will clear the active diagnostic code for the new injector. Verify that the original condition has been resolved.
Result: If the test
The problem that is identified below does not have a known permanent solution. Until a permanent solution is known, use the solution that is identified below.Problem
Fuel Injectors in 797F powered Off-Highway Trucks engines are not reaching expected mid-life target. The typical failure mode is a "-2" or a "-7" code on the fuel injectors.Solution
This will be an interim troubleshooting procedure to follow for trucks running with a special test software. Prior to executing this procedure, utilize Cat ® Electronic Technician (Cat ET) or Advisor to verify if any logged codes have been logged. Certain injector diagnostics do not notify the operator or light the check engine light upon activation."Fuel system verification-Test" procedure applies to trucks running with following software versions only.
Engine - LRC 3655600-31 (Test)
Engine - Tier II 5297866-05 (Test)
Engine - HAA (4x2) 3253178-39 (Test)
Engine - Tier II Custom 4727209-12 (Test)Troubleshooting Procedure
Table 1
Troubleshooting Test Steps Values Results
1. Check for Diagnostic Codes
A. Establish communication between Cat® (Electronic Technician) ET and the engine ECM. Cat ET must be configured for Dual Data Link Communications to perform this procedure. Refer to Troubleshooting, "Electronic Service Tools", if necessary.
B. Determine the diagnostic code that relates to an injector. Codes
Result: A -2 code is present.
Repair: Perform the following procedure:
1. Do not clear the diagnostic code.
Access the Fuel System Verification Test by accessing the following display screens:
- Diagnostics
- Diagnostic Tests
- Fuel System Verification Test
3. Perform the Fuel System Verification Test.
If the injector passes the test, the injector is "OK". Cat ET will clear the code.
Result: If the injector fails the test, perform the following procedure:
a. Replace the injector.
b. Flash program the trim file for the new injector into the ECM. Refer to Troubleshooting, "Injector Trim File - Install", if necessary.
c. Perform the Fuel System Verification Test again. This test will clear the active diagnostic code for the new injector. Verify that the original condition has been resolved.
Result: If the test