Information injection-pump assembly
BOSCH
9 400 610 729
9400610729
ZEXEL
101607-9440
1016079440
NISSAN-DIESEL
16713Z6505
16713z6505
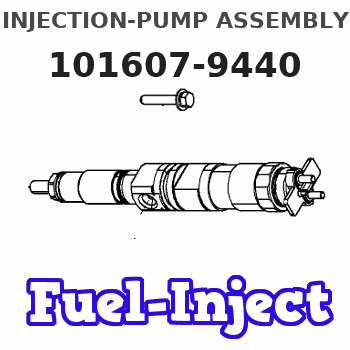
Rating:
Service parts 101607-9440 INJECTION-PUMP ASSEMBLY:
1.
_
7.
COUPLING PLATE
8.
_
9.
_
11.
Nozzle and Holder
16600-Z5663
12.
Open Pre:MPa(Kqf/cm2)
17.7{180}/20.6{210}
14.
NOZZLE
Cross reference number
BOSCH
9 400 610 729
9400610729
ZEXEL
101607-9440
1016079440
NISSAN-DIESEL
16713Z6505
16713z6505
Zexel num
Bosch num
Firm num
Name
9 400 610 729
16713Z6505 NISSAN-DIESEL
INJECTION-PUMP ASSEMBLY
FE6E * K 14BF PE6AD PE
FE6E * K 14BF PE6AD PE
Calibration Data:
Adjustment conditions
Test oil
1404 Test oil ISO4113 or {SAEJ967d}
1404 Test oil ISO4113 or {SAEJ967d}
Test oil temperature
degC
40
40
45
Nozzle and nozzle holder
105780-8260
Bosch type code
9 430 610 133
Nozzle
105780-0120
Bosch type code
1 688 901 990
Nozzle holder
105780-2190
Opening pressure
MPa
18
Opening pressure
kgf/cm2
184
Injection pipe
Outer diameter - inner diameter - length (mm) mm 6-2-600
Outer diameter - inner diameter - length (mm) mm 6-2-600
Overflow valve
131425-0420
Overflow valve opening pressure
kPa
157
123
191
Overflow valve opening pressure
kgf/cm2
1.6
1.25
1.95
Tester oil delivery pressure
kPa
255
255
255
Tester oil delivery pressure
kgf/cm2
2.6
2.6
2.6
Direction of rotation (viewed from drive side)
Right R
Right R
Injection timing adjustment
Direction of rotation (viewed from drive side)
Right R
Right R
Injection order
1-4-2-6-
3-5
Pre-stroke
mm
3.7
3.65
3.75
Beginning of injection position
Drive side NO.1
Drive side NO.1
Difference between angles 1
Cal 1-4 deg. 60 59.5 60.5
Cal 1-4 deg. 60 59.5 60.5
Difference between angles 2
Cyl.1-2 deg. 120 119.5 120.5
Cyl.1-2 deg. 120 119.5 120.5
Difference between angles 3
Cal 1-6 deg. 180 179.5 180.5
Cal 1-6 deg. 180 179.5 180.5
Difference between angles 4
Cal 1-3 deg. 240 239.5 240.5
Cal 1-3 deg. 240 239.5 240.5
Difference between angles 5
Cal 1-5 deg. 300 299.5 300.5
Cal 1-5 deg. 300 299.5 300.5
Injection quantity adjustment
Adjusting point
-
Rack position
12.1
Pump speed
r/min
800
800
800
Average injection quantity
mm3/st.
99
97.4
100.6
Max. variation between cylinders
%
0
-3.5
3.5
Basic
*
Fixing the rack
*
Standard for adjustment of the maximum variation between cylinders
*
Injection quantity adjustment_02
Adjusting point
Z
Rack position
9.5+-0.5
Pump speed
r/min
265
265
265
Average injection quantity
mm3/st.
9
7.2
10.8
Max. variation between cylinders
%
0
-10
10
Fixing the rack
*
Standard for adjustment of the maximum variation between cylinders
*
Injection quantity adjustment_03
Adjusting point
A
Rack position
R1(12.1)
Pump speed
r/min
800
800
800
Average injection quantity
mm3/st.
99
98
100
Basic
*
Fixing the lever
*
Injection quantity adjustment_04
Adjusting point
B
Rack position
R1+1
Pump speed
r/min
1500
1500
1500
Average injection quantity
mm3/st.
105.5
101.5
109.5
Fixing the lever
*
Injection quantity adjustment_05
Adjusting point
C
Rack position
(R1-0.45
)
Pump speed
r/min
600
600
600
Average injection quantity
mm3/st.
94.5
90.5
98.5
Fixing the lever
*
Injection quantity adjustment_06
Adjusting point
I
Rack position
-
Pump speed
r/min
100
100
100
Average injection quantity
mm3/st.
105
105
115
Fixing the lever
*
Rack limit
*
Timer adjustment
Pump speed
r/min
(900)
Advance angle
deg.
0
0
0
Remarks
Start
Start
Timer adjustment_02
Pump speed
r/min
1080
Advance angle
deg.
2
1.5
2.5
Timer adjustment_03
Pump speed
r/min
1225
Advance angle
deg.
2
1.5
2.5
Timer adjustment_04
Pump speed
r/min
1425
Advance angle
deg.
6
5.5
6.5
Remarks
Finish
Finish
Test data Ex:
Governor adjustment
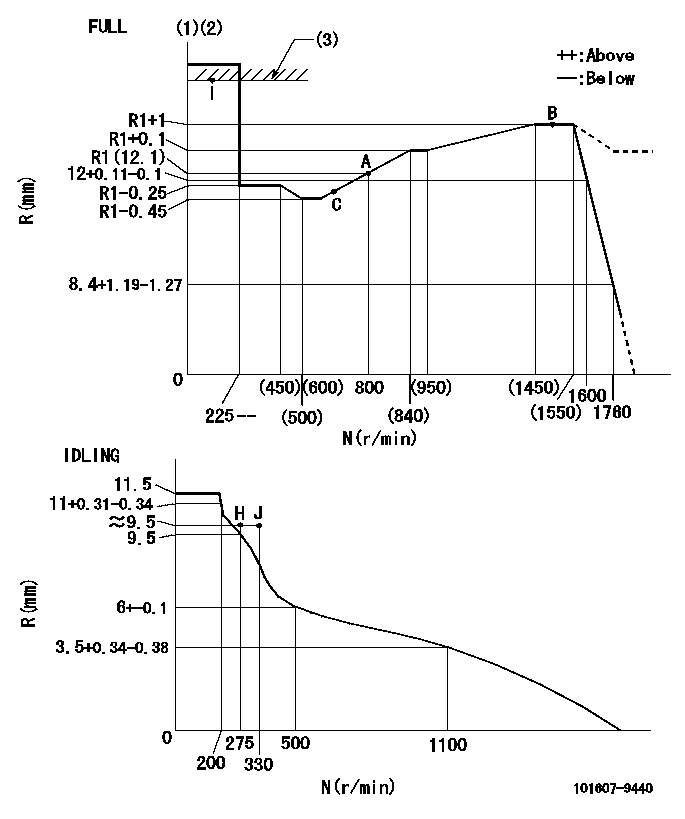
N:Pump speed
R:Rack position (mm)
(1)Torque cam stamping: T1
(2)Tolerance for racks not indicated: +-0.05mm.
(3)RACK LIMIT
----------
T1=K89
----------
----------
T1=K89
----------
Speed control lever angle

F:Full speed
I:Idle
(1)Use the hole at R = aa
(2)Stopper bolt set position 'H'
----------
aa=36mm
----------
a=25deg+-5deg b=42deg+-3deg
----------
aa=36mm
----------
a=25deg+-5deg b=42deg+-3deg
Stop lever angle
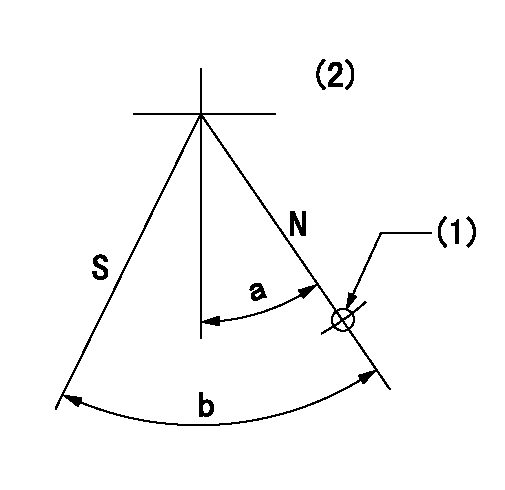
N:Pump normal
S:Stop the pump.
(1)Use the hole at R = aa
(2)No return spring
----------
aa=28mm
----------
a=20deg+-5deg b=40deg+-5deg
----------
aa=28mm
----------
a=20deg+-5deg b=40deg+-5deg
Timing setting
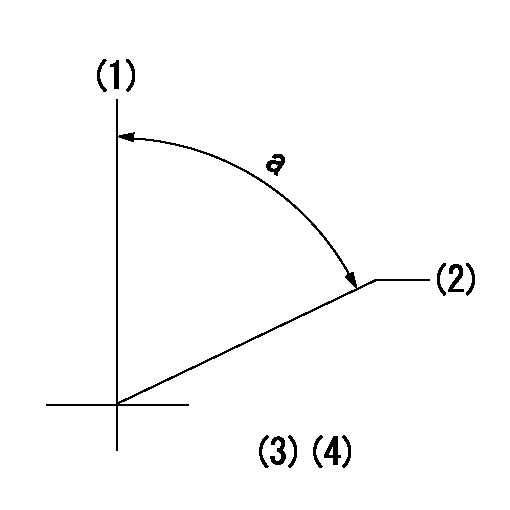
(1)Pump vertical direction
(2)Position of timer's threaded hole at No 1 cylinder's beginning of injection
(3)-
(4)-
----------
----------
a=(60deg)
----------
----------
a=(60deg)
Information:
Illustration 6 g06613192
Gray locking wedge removed from ECM connector
Remove gray locking wedge from 86-pin connector to provide access to release the DT Pins.Note: Circuit U937 to be removed from pin location number 24 and transferred to pin location 73.Note: Cloth tape will need to be removed to the split in the harness main bundle.Note: The U937 wire can then be routed into the opposite branch to gain enough free length to make the connection.Note: The U939 wire removed from pin location 73 has adequate length to be loaded into location 16.
Transfer and relocate the wires as detailed in Table 2.
Reinstall the locking wedge (B) when all wires have been transferred and relocated.
Illustration 7 g06613197
View of back of ECM connector with connector cover (D) removed
Apply cloth tape to both wire branches from the main bundle of wires up the branches to the harness strain relief strap location.
Illustration 8 g06613199
Connector cover (D) reinstalled with harness secured
(1) 3S-2093 Cable Strap
(D) Connector cover
Reinstall connector cover (D) and secure the harness branches using two cable straps (1).
Use caution when re-engaging the connector with the ECM.
Tighten allen head screw (A).Note: In certain cases, U937 may require lengthening to provide adequate strain relief when relocated in pin 73.Note: Refer to "Soldered Splice","Deutsch connector", or "Sealed Mechanical Splice" for the proper way to extend circuit U937.Soldered Splice
A soldered spliced can be made to extend the wire. Soldered connection will need to be insulated using an appropriately sized adhesive head shrink sleeve.
Illustration 9 g06613210
U937 removed
Remove U937 from ECM connector.
Cut pin off end of wire.
Strip wire 7.5 mm (0.30 inch).
Illustration 10 g06613213
Additional wire soldered to circuit U937
Solder to additional wire to extend U937 and install appropriate sized adhesive head shrink sleeve.
Install pin on end of U937.
Insert U937 into pin 73.
Refer to "Procedure to Change Connector Plug Assembly Pins" for the proper method to reinstall ECM connector.Deutsch connector
Table 3
Required Parts
Qty Part Number Part Name
1 115-8109 Wire Splice Note: The deutsch connector is a field serviceable alternative to permanent splices. It is made from the same high-quality silicone elastomer as used for the Deutsch connector seals and grommets. The splice body houses a contact retention system that secures a mated pair of contacts in a compact environmentally sealed unit. This splice can also be serviced with standard deutsch connector tools.
Illustration 11 g06613218
Deutsch connector section view
Illustration 12 g06613221
Deutsch connector splice installed
Illustration 13 g06613224
Sufficient strain relief for deutsch connector
Refer to "Procedure to Change Connector Plug Assembly Pins" for the proper method to reinstall ECM connectorSealed Mechanical Splice
Table 4
Required Parts
Qty Part Number Part Name
1 136-4877 Wire Splice Note: Sealed mechanical splices have head-shrinkable, environmentally sealed sleeves.
Illustration 14 g06613205
Sealed mechanical splice
Select appropriate splice size.
Strip wire 7.5 mm (0.3 inch).
Insert stripped wire into sealed mechanical splice.
Crimp sealed mechanical splice.
Apply heat to the crimped splice until tubing re-covers and adhesive flows.
Refer to "Procedure to Change Connector Plug Assembly Pins" for the proper method to reinstall ECM connector