Information injection-pump assembly
BOSCH
F 01G 09U 05N
f01g09u05n
ZEXEL
101607-9330
1016079330
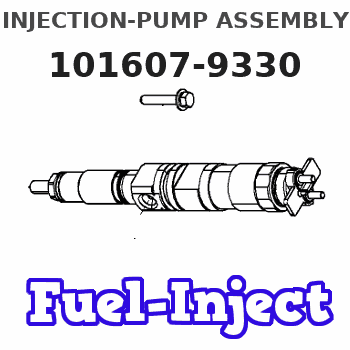
Rating:
Include in #2:
109341-1014
as _
Cross reference number
BOSCH
F 01G 09U 05N
f01g09u05n
ZEXEL
101607-9330
1016079330
Zexel num
Bosch num
Firm num
Name
Calibration Data:
Adjustment conditions
Test oil
1404 Test oil ISO4113 or {SAEJ967d}
1404 Test oil ISO4113 or {SAEJ967d}
Test oil temperature
degC
40
40
45
Nozzle and nozzle holder
105780-8140
Bosch type code
EF8511/9A
Nozzle
105780-0000
Bosch type code
DN12SD12T
Nozzle holder
105780-2080
Bosch type code
EF8511/9
Opening pressure
MPa
17.2
Opening pressure
kgf/cm2
175
Injection pipe
Outer diameter - inner diameter - length (mm) mm 6-2-600
Outer diameter - inner diameter - length (mm) mm 6-2-600
Overflow valve
131424-1520
Overflow valve opening pressure
kPa
157
123
191
Overflow valve opening pressure
kgf/cm2
1.6
1.25
1.95
Tester oil delivery pressure
kPa
157
157
157
Tester oil delivery pressure
kgf/cm2
1.6
1.6
1.6
Direction of rotation (viewed from drive side)
Right R
Right R
Injection timing adjustment
Direction of rotation (viewed from drive side)
Right R
Right R
Injection order
1-4-2-6-
3-5
Pre-stroke
mm
3.4
3.35
3.45
Beginning of injection position
Drive side NO.1
Drive side NO.1
Difference between angles 1
Cal 1-4 deg. 60 59.5 60.5
Cal 1-4 deg. 60 59.5 60.5
Difference between angles 2
Cyl.1-2 deg. 120 119.5 120.5
Cyl.1-2 deg. 120 119.5 120.5
Difference between angles 3
Cal 1-6 deg. 180 179.5 180.5
Cal 1-6 deg. 180 179.5 180.5
Difference between angles 4
Cal 1-3 deg. 240 239.5 240.5
Cal 1-3 deg. 240 239.5 240.5
Difference between angles 5
Cal 1-5 deg. 300 299.5 300.5
Cal 1-5 deg. 300 299.5 300.5
Injection quantity adjustment
Adjusting point
A
Rack position
9.8
Pump speed
r/min
600
600
600
Average injection quantity
mm3/st.
58.9
57.9
59.9
Max. variation between cylinders
%
0
-3.5
3.5
Basic
*
Fixing the lever
*
Injection quantity adjustment_02
Adjusting point
B
Rack position
R1(10)
Pump speed
r/min
1500
1500
1500
Average injection quantity
mm3/st.
80.6
79.6
81.6
Max. variation between cylinders
%
0
-5
5
Fixing the lever
*
Injection quantity adjustment_03
Adjusting point
C
Rack position
7.9+-0.5
Pump speed
r/min
300
300
300
Average injection quantity
mm3/st.
8.3
6.5
10.1
Max. variation between cylinders
%
0
-10
10
Fixing the rack
*
Injection quantity adjustment_04
Adjusting point
D
Rack position
-
Pump speed
r/min
100
100
100
Average injection quantity
mm3/st.
80
80
Fixing the lever
*
Remarks
After startup boost setting
After startup boost setting
Timer adjustment
Pump speed
r/min
850--
Advance angle
deg.
0
0
0
Remarks
Start
Start
Timer adjustment_02
Pump speed
r/min
800
Advance angle
deg.
0.5
Timer adjustment_03
Pump speed
r/min
1500
Advance angle
deg.
4
3.5
4.5
Remarks
Finish
Finish
Test data Ex:
Governor adjustment
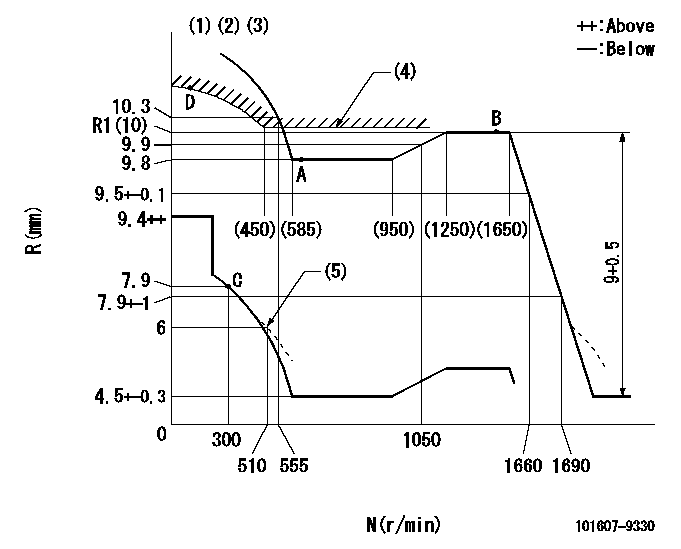
N:Pump speed
R:Rack position (mm)
(1)Lever ratio: RT
(2)Target shim dimension: TH
(3)Tolerance for racks not indicated: +-0.05mm.
(4)Excess fuel setting for starting: SXL (N = N1)
(5)Damper spring setting
----------
RT=1 TH=2.8mm SXL=R1+0.2mm N1=500r/min
----------
----------
RT=1 TH=2.8mm SXL=R1+0.2mm N1=500r/min
----------
0000000901

F:Full load
I:Idle
(1)Use the hole at R = aa
(2)Stopper bolt setting
----------
----------
a=17deg+-5deg b=19.5deg+-3deg
----------
----------
a=17deg+-5deg b=19.5deg+-3deg
Stop lever angle
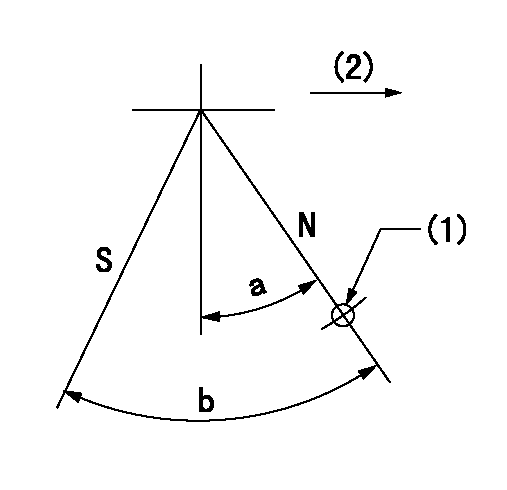
N:Pump normal
S:Stop the pump.
(1)Use the pin at R = aa
(2)Drive side
----------
aa=20mm
----------
a=40deg+-5deg b=71deg+-5deg
----------
aa=20mm
----------
a=40deg+-5deg b=71deg+-5deg
Timing setting
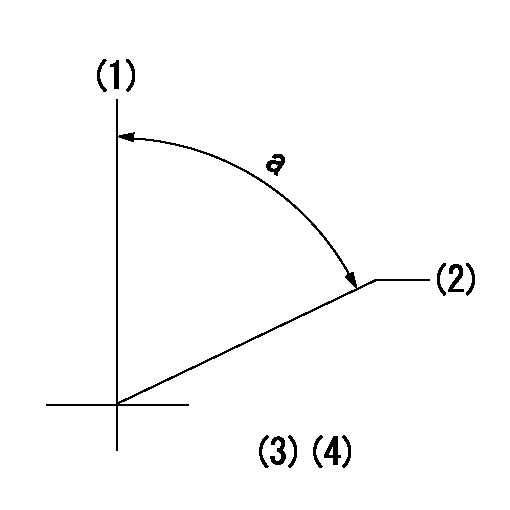
(1)Pump vertical direction
(2)Position of timer's threaded hole at No 1 cylinder's beginning of injection
(3)-
(4)-
----------
----------
a=(60deg)
----------
----------
a=(60deg)
Information:
Important Safety Information
Illustration 1 g02139237Work safely. Most accidents that involve product operation, maintenance, and repair are caused by failure to observe basic safety rules or precautions. An accident can often be avoided by recognizing potentially hazardous situations before an accident occurs. A person must be alert to potential hazards. This person should also have the necessary training, skills, and tools to perform these functions properly. Safety precautions and warnings are provided in this instruction and on the product. If these hazard warnings are not heeded, bodily injury or death could occur to you or to other persons. Caterpillar cannot anticipate every possible circumstance that might involve a potential hazard. Therefore, the warnings in this publication and the warnings that are on the product are not all inclusive. If a tool, a procedure, a work method, or operating technique that is not recommended by Caterpillar is used, ensure that it is safe for you and for other people to use. Ensure that the product will not be damaged or the product will not be made unsafe by the operation, lubrication, maintenance, or the repair procedures that are used.
Improper operation, lubrication, maintenance or repair of this product can be dangerous and could result in injury or death.Do not operate or perform any lubrication, maintenance or repair on this product, until you have read and understood the operation, lubrication, maintenance and repair information.
Safety precautions and warnings are provided in this manual and on the product. If these hazard warnings are not heeded, bodily injury or death could occur to you or to other persons.The hazards are identified by the safety alert symbol which is followed by a signal word such as danger, warning, or caution. The "" safety alert symbol is shown below.
Illustration 2 g00008666This safety alert symbol means:Pay attention!Become alert!Your safety is involved.The message that appears under the safety alert symbol explains the hazard.Operations that may cause product damage are identified by "" labels on the product and in this publication.Caterpillar cannot anticipate every possible circumstance that might involve a potential hazard. The safety information in this document and the safety information on the machine are not all inclusive. Determine that the tools, procedures, work methods, and operating techniques are safe. Determine that the operation, lubrication, maintenance, and repair procedures will not damage the machine. Also, you must determine that the operation, lubrication, maintenance, and repair procedures will not make the machine unsafe.The information, the specifications, and the illustrations that exist in this guideline are based on information which was available at the time of publication. The specifications, torques, pressures, measurements, adjustments, illustrations, and other items can change at any time. These changes can affect the service that is given to the product. Obtain the complete, most current information before you start any job. Caterpillar dealers can supply the most current information.Summary
The information included in this guideline should serve as an aid in fuel injection pump housing test procedure.Service Letters and Technical Information Bulletins
The most recent Service Letters and Technical Information Bulletins
Illustration 1 g02139237Work safely. Most accidents that involve product operation, maintenance, and repair are caused by failure to observe basic safety rules or precautions. An accident can often be avoided by recognizing potentially hazardous situations before an accident occurs. A person must be alert to potential hazards. This person should also have the necessary training, skills, and tools to perform these functions properly. Safety precautions and warnings are provided in this instruction and on the product. If these hazard warnings are not heeded, bodily injury or death could occur to you or to other persons. Caterpillar cannot anticipate every possible circumstance that might involve a potential hazard. Therefore, the warnings in this publication and the warnings that are on the product are not all inclusive. If a tool, a procedure, a work method, or operating technique that is not recommended by Caterpillar is used, ensure that it is safe for you and for other people to use. Ensure that the product will not be damaged or the product will not be made unsafe by the operation, lubrication, maintenance, or the repair procedures that are used.
Improper operation, lubrication, maintenance or repair of this product can be dangerous and could result in injury or death.Do not operate or perform any lubrication, maintenance or repair on this product, until you have read and understood the operation, lubrication, maintenance and repair information.
Safety precautions and warnings are provided in this manual and on the product. If these hazard warnings are not heeded, bodily injury or death could occur to you or to other persons.The hazards are identified by the safety alert symbol which is followed by a signal word such as danger, warning, or caution. The "" safety alert symbol is shown below.
Illustration 2 g00008666This safety alert symbol means:Pay attention!Become alert!Your safety is involved.The message that appears under the safety alert symbol explains the hazard.Operations that may cause product damage are identified by "" labels on the product and in this publication.Caterpillar cannot anticipate every possible circumstance that might involve a potential hazard. The safety information in this document and the safety information on the machine are not all inclusive. Determine that the tools, procedures, work methods, and operating techniques are safe. Determine that the operation, lubrication, maintenance, and repair procedures will not damage the machine. Also, you must determine that the operation, lubrication, maintenance, and repair procedures will not make the machine unsafe.The information, the specifications, and the illustrations that exist in this guideline are based on information which was available at the time of publication. The specifications, torques, pressures, measurements, adjustments, illustrations, and other items can change at any time. These changes can affect the service that is given to the product. Obtain the complete, most current information before you start any job. Caterpillar dealers can supply the most current information.Summary
The information included in this guideline should serve as an aid in fuel injection pump housing test procedure.Service Letters and Technical Information Bulletins
The most recent Service Letters and Technical Information Bulletins