Information injection-pump assembly
BOSCH
F 019 Z20 477
f019z20477
ZEXEL
101607-9210
1016079210
NISSAN-DIESEL
1671395275
1671395275
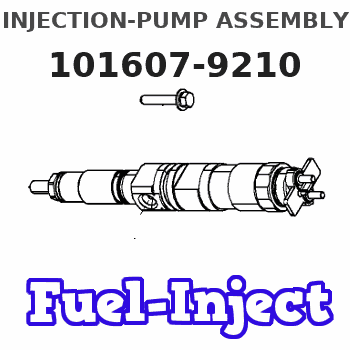
Rating:
Service parts 101607-9210 INJECTION-PUMP ASSEMBLY:
1.
_
7.
COUPLING PLATE
8.
_
9.
_
11.
Nozzle and Holder
16600-95019
12.
Open Pre:MPa(Kqf/cm2)
19.6{200}
15.
NOZZLE SET
Include in #1:
101607-9210
as INJECTION-PUMP ASSEMBLY
Include in #2:
104746-5171
as _
Cross reference number
BOSCH
F 019 Z20 477
f019z20477
ZEXEL
101607-9210
1016079210
NISSAN-DIESEL
1671395275
1671395275
Zexel num
Bosch num
Firm num
Name
F 019 Z20 477
1671395275 NISSAN-DIESEL
INJECTION-PUMP ASSEMBLY
NE6TA * K 14BF PE6AD PE
NE6TA * K 14BF PE6AD PE
Calibration Data:
Adjustment conditions
Test oil
1404 Test oil ISO4113 or {SAEJ967d}
1404 Test oil ISO4113 or {SAEJ967d}
Test oil temperature
degC
40
40
45
Nozzle and nozzle holder
105780-8140
Bosch type code
EF8511/9
Nozzle
105780-0000
Bosch type code
DN12SD12T
Nozzle holder
105780-2080
Bosch type code
EF8511/9
Opening pressure
MPa
17.2
Opening pressure
kgf/cm2
175
Injection pipe
Outer diameter - inner diameter - length (mm) mm 6-2-600
Outer diameter - inner diameter - length (mm) mm 6-2-600
Overflow valve
131424-1520
Overflow valve opening pressure
kPa
157
123
191
Overflow valve opening pressure
kgf/cm2
1.6
1.25
1.95
Tester oil delivery pressure
kPa
157
157
157
Tester oil delivery pressure
kgf/cm2
1.6
1.6
1.6
Direction of rotation (viewed from drive side)
Right R
Right R
Injection timing adjustment
Direction of rotation (viewed from drive side)
Right R
Right R
Injection order
1-4-2-6-
3-5
Pre-stroke
mm
3.9
3.85
3.95
Beginning of injection position
Drive side NO.1
Drive side NO.1
Difference between angles 1
Cal 1-4 deg. 60 59.5 60.5
Cal 1-4 deg. 60 59.5 60.5
Difference between angles 2
Cyl.1-2 deg. 120 119.5 120.5
Cyl.1-2 deg. 120 119.5 120.5
Difference between angles 3
Cal 1-6 deg. 180 179.5 180.5
Cal 1-6 deg. 180 179.5 180.5
Difference between angles 4
Cal 1-3 deg. 240 239.5 240.5
Cal 1-3 deg. 240 239.5 240.5
Difference between angles 5
Cal 1-5 deg. 300 299.5 300.5
Cal 1-5 deg. 300 299.5 300.5
Injection quantity adjustment
Adjusting point
-
Rack position
13.8
Pump speed
r/min
1400
1400
1400
Average injection quantity
mm3/st.
118
116.4
119.6
Max. variation between cylinders
%
0
-3.5
3.5
Basic
*
Fixing the rack
*
Standard for adjustment of the maximum variation between cylinders
*
Injection quantity adjustment_02
Adjusting point
-
Rack position
9.6+-0.5
Pump speed
r/min
275
275
275
Average injection quantity
mm3/st.
9
7.2
10.8
Max. variation between cylinders
%
0
-10
10
Fixing the rack
*
Standard for adjustment of the maximum variation between cylinders
*
Remarks
Adjust only variation between cylinders; adjust governor according to governor specifications.
Adjust only variation between cylinders; adjust governor according to governor specifications.
Injection quantity adjustment_03
Adjusting point
A
Rack position
R1(13.8)
Pump speed
r/min
1400
1400
1400
Average injection quantity
mm3/st.
118
117
119
Basic
*
Fixing the lever
*
Boost pressure
kPa
33.3
33.3
Boost pressure
mmHg
250
250
Injection quantity adjustment_04
Adjusting point
B
Rack position
R1-0.8
Pump speed
r/min
900
900
900
Average injection quantity
mm3/st.
94.5
91.3
97.7
Fixing the lever
*
Boost pressure
kPa
33.3
33.3
Boost pressure
mmHg
250
250
Injection quantity adjustment_05
Adjusting point
C
Rack position
R2-0.55
Pump speed
r/min
600
600
600
Average injection quantity
mm3/st.
64.5
60.5
68.5
Fixing the lever
*
Boost pressure
kPa
0
0
0
Boost pressure
mmHg
0
0
0
Injection quantity adjustment_06
Adjusting point
I
Rack position
-
Pump speed
r/min
150
150
150
Average injection quantity
mm3/st.
80
80
100
Fixing the lever
*
Boost pressure
kPa
0
0
0
Boost pressure
mmHg
0
0
0
Rack limit
*
Boost compensator adjustment
Pump speed
r/min
600
600
600
Rack position
R2-0.55
Boost pressure
kPa
10.7
9.4
12
Boost pressure
mmHg
80
70
90
Boost compensator adjustment_02
Pump speed
r/min
600
600
600
Rack position
R2(R1-1.
2)
Boost pressure
kPa
20
20
20
Boost pressure
mmHg
150
150
150
Timer adjustment
Pump speed
r/min
920--
Advance angle
deg.
0
0
0
Remarks
Start
Start
Timer adjustment_02
Pump speed
r/min
870
Advance angle
deg.
0.5
Timer adjustment_03
Pump speed
r/min
1400
Advance angle
deg.
2
1.5
2.5
Remarks
Finish
Finish
Test data Ex:
Governor adjustment
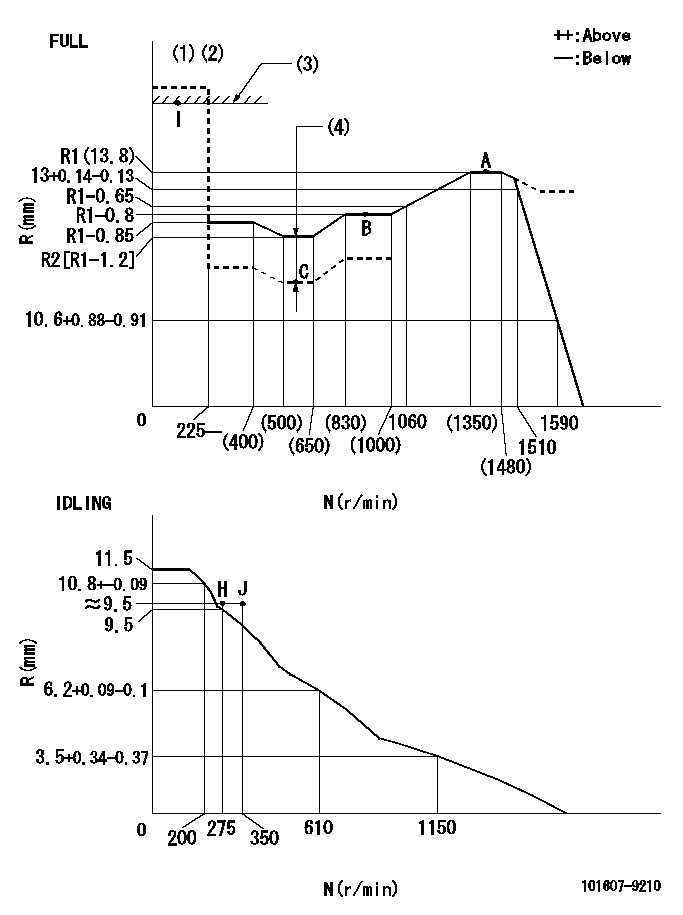
N:Pump speed
R:Rack position (mm)
(1)Torque cam stamping: T1
(2)Tolerance for racks not indicated: +-0.05mm.
(3)RACK LIMIT
(4)Boost compensator stroke: BCL
----------
T1=J98 BCL=0.55+-0.1mm
----------
----------
T1=J98 BCL=0.55+-0.1mm
----------
Speed control lever angle

F:Full speed
I:Idle
(1)Use the hole at R = aa
(2)Stopper bolt set position 'H'
----------
aa=100mm
----------
a=26.5deg+-5deg b=42deg+-3deg
----------
aa=100mm
----------
a=26.5deg+-5deg b=42deg+-3deg
Stop lever angle

N:Pump normal
S:Stop the pump.
(1)Use the hole at R = aa
----------
aa=36mm
----------
a=20deg+-5deg b=40deg+-5deg
----------
aa=36mm
----------
a=20deg+-5deg b=40deg+-5deg
Timing setting

(1)Pump vertical direction
(2)Coupling's key groove position at No 1 cylinder's beginning of injection
(3)-
(4)-
----------
----------
a=(30deg)
----------
----------
a=(30deg)
Information:
Unit Injector Mechanism
Illustration 2 g01430766
Typical unit injector mechanism (17) Unit injector (18) Adjusting nut (19) Rocker arm assembly (20) CamshaftThe unit injector mechanism provides the downward force that is required to pressurize the fuel in the unit injector. When a signal is received from the ECM, the unit injector (17) injects the pressurized fuel into the combustion chamber. The camshaft gear is driven by an idler gear which is driven through the front gear train by the crankshaft gear. The gears of the front gear train that are timed must be aligned in order to provide the correct relationship between the piston and valve movement. During assembly of the front gear train, care must be taken in order to correctly align the timing marks of the gears. The camshaft has three camshaft lobes for each cylinder. Two lobes operate the inlet and exhaust valves, and one operates the unit injector mechanism. Force is transferred from the unit injector lobe on camshaft (20) through rocker arm assembly (19) to the top of the unit injector. The adjusting nut (18) allows setting of the unit injector adjustment. Refer to the Testing and Adjusting, "Electronic Unit Injector - Adjust" for the proper setting of the unit injector.Unit Injector
Illustration 3 g01332439
(21) Solenoid (22) Tappet (23) Plunger (24) Barrel (25) Nozzle assemblyOperation of the Electronic Unit Injector
The operation of the Electronic Control Unit (EUI) consists of the following four stages: Pre-injection, Injection, End of injection and Fill. Unit injectors use a plunger and barrel to pump high pressure fuel into the combustion chamber. Components of the injector include the tappet, the plunger, the barrel and nozzle assembly. Components of the nozzle assembly include the spring, the nozzle check, and a nozzle tip. The cartridge valve is made up of the following components: solenoid, armature, poppet valve and poppet spring.The injector is mounted in an injector bore in the cylinder head which has an integral fuel supply passage. The injector sleeve separates the injector from the engine coolant in the water jacket. Some engines use a stainless steel sleeve. The stainless steel sleeve fits into the cylinder head with a light press fit.
Illustration 4 g00942799
Pre-injection (A) Fuel supply pressure (B) Injection pressure (C) Moving parts (D) Mechanical movement (E) Fuel movement.Pre-injection metering starts with the injector plunger and the injector tappet at the top of the fuel injection stroke. When the plunger cavity is full of fuel, the poppet valve is in the open position and the nozzle check is in the open position. Fuel leaves the plunger cavity when the rocker arm pushes down on the tappet and the plunger. Fuel flow that is blocked by the closed nozzle check valve flows past the open poppet valve to the fuel supply passage in the cylinder head. If the solenoid is energized, the poppet valve remains open and the fuel from the plunger cavity continues flowing into the fuel supply passage.
Illustration 5 g00942798
Injection (A) Fuel supply pressure. (B) Injection pressure (C) Moving parts (D) Mechanical movement (E)
Illustration 2 g01430766
Typical unit injector mechanism (17) Unit injector (18) Adjusting nut (19) Rocker arm assembly (20) CamshaftThe unit injector mechanism provides the downward force that is required to pressurize the fuel in the unit injector. When a signal is received from the ECM, the unit injector (17) injects the pressurized fuel into the combustion chamber. The camshaft gear is driven by an idler gear which is driven through the front gear train by the crankshaft gear. The gears of the front gear train that are timed must be aligned in order to provide the correct relationship between the piston and valve movement. During assembly of the front gear train, care must be taken in order to correctly align the timing marks of the gears. The camshaft has three camshaft lobes for each cylinder. Two lobes operate the inlet and exhaust valves, and one operates the unit injector mechanism. Force is transferred from the unit injector lobe on camshaft (20) through rocker arm assembly (19) to the top of the unit injector. The adjusting nut (18) allows setting of the unit injector adjustment. Refer to the Testing and Adjusting, "Electronic Unit Injector - Adjust" for the proper setting of the unit injector.Unit Injector
Illustration 3 g01332439
(21) Solenoid (22) Tappet (23) Plunger (24) Barrel (25) Nozzle assemblyOperation of the Electronic Unit Injector
The operation of the Electronic Control Unit (EUI) consists of the following four stages: Pre-injection, Injection, End of injection and Fill. Unit injectors use a plunger and barrel to pump high pressure fuel into the combustion chamber. Components of the injector include the tappet, the plunger, the barrel and nozzle assembly. Components of the nozzle assembly include the spring, the nozzle check, and a nozzle tip. The cartridge valve is made up of the following components: solenoid, armature, poppet valve and poppet spring.The injector is mounted in an injector bore in the cylinder head which has an integral fuel supply passage. The injector sleeve separates the injector from the engine coolant in the water jacket. Some engines use a stainless steel sleeve. The stainless steel sleeve fits into the cylinder head with a light press fit.
Illustration 4 g00942799
Pre-injection (A) Fuel supply pressure (B) Injection pressure (C) Moving parts (D) Mechanical movement (E) Fuel movement.Pre-injection metering starts with the injector plunger and the injector tappet at the top of the fuel injection stroke. When the plunger cavity is full of fuel, the poppet valve is in the open position and the nozzle check is in the open position. Fuel leaves the plunger cavity when the rocker arm pushes down on the tappet and the plunger. Fuel flow that is blocked by the closed nozzle check valve flows past the open poppet valve to the fuel supply passage in the cylinder head. If the solenoid is energized, the poppet valve remains open and the fuel from the plunger cavity continues flowing into the fuel supply passage.
Illustration 5 g00942798
Injection (A) Fuel supply pressure. (B) Injection pressure (C) Moving parts (D) Mechanical movement (E)