Information injection-pump assembly
ZEXEL
101607-9170
1016079170
NISSAN-DIESEL
16713Z6379
16713z6379
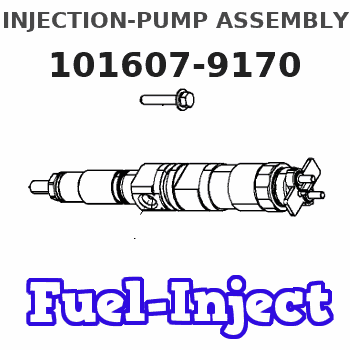
Rating:
Service parts 101607-9170 INJECTION-PUMP ASSEMBLY:
1.
_
7.
COUPLING PLATE
8.
_
9.
_
11.
Nozzle and Holder
16600-Z6003
12.
Open Pre:MPa(Kqf/cm2)
17.7{180}/22.6{230}
14.
NOZZLE
Include in #1:
101607-9170
as INJECTION-PUMP ASSEMBLY
Cross reference number
ZEXEL
101607-9170
1016079170
NISSAN-DIESEL
16713Z6379
16713z6379
Zexel num
Bosch num
Firm num
Name
Calibration Data:
Adjustment conditions
Test oil
1404 Test oil ISO4113 or {SAEJ967d}
1404 Test oil ISO4113 or {SAEJ967d}
Test oil temperature
degC
40
40
45
Nozzle and nozzle holder
105780-8250
Bosch type code
1 688 901 101
Nozzle
105780-0120
Bosch type code
1 688 901 990
Nozzle holder
105780-2190
Opening pressure
MPa
20.7
Opening pressure
kgf/cm2
211
Injection pipe
Outer diameter - inner diameter - length (mm) mm 6-2-600
Outer diameter - inner diameter - length (mm) mm 6-2-600
Overflow valve
131424-8921
Overflow valve opening pressure
kPa
157
123
191
Overflow valve opening pressure
kgf/cm2
1.6
1.25
1.95
Tester oil delivery pressure
kPa
255
255
255
Tester oil delivery pressure
kgf/cm2
2.6
2.6
2.6
Direction of rotation (viewed from drive side)
Left L
Left L
Injection timing adjustment
Direction of rotation (viewed from drive side)
Left L
Left L
Injection order
1-4-2-6-
3-5
Pre-stroke
mm
3.7
3.65
3.75
Beginning of injection position
Governor side NO.1
Governor side NO.1
Difference between angles 1
Cal 1-4 deg. 60 59.5 60.5
Cal 1-4 deg. 60 59.5 60.5
Difference between angles 2
Cyl.1-2 deg. 120 119.5 120.5
Cyl.1-2 deg. 120 119.5 120.5
Difference between angles 3
Cal 1-6 deg. 180 179.5 180.5
Cal 1-6 deg. 180 179.5 180.5
Difference between angles 4
Cal 1-3 deg. 240 239.5 240.5
Cal 1-3 deg. 240 239.5 240.5
Difference between angles 5
Cal 1-5 deg. 300 299.5 300.5
Cal 1-5 deg. 300 299.5 300.5
Injection quantity adjustment
Adjusting point
-
Rack position
11.9
Pump speed
r/min
800
800
800
Average injection quantity
mm3/st.
87.5
85.9
89.1
Max. variation between cylinders
%
0
-3.5
3.5
Basic
*
Fixing the rack
*
Standard for adjustment of the maximum variation between cylinders
*
Injection quantity adjustment_02
Adjusting point
Z
Rack position
9.5+-0.5
Pump speed
r/min
420
420
420
Average injection quantity
mm3/st.
9.5
7.7
11.3
Max. variation between cylinders
%
0
-10
10
Fixing the rack
*
Standard for adjustment of the maximum variation between cylinders
*
Injection quantity adjustment_03
Adjusting point
A
Rack position
R1(11.9)
Pump speed
r/min
800
800
800
Average injection quantity
mm3/st.
87.5
86.5
88.5
Basic
*
Fixing the lever
*
Injection quantity adjustment_04
Adjusting point
B
Rack position
R1+1.15
Pump speed
r/min
1450
1450
1450
Average injection quantity
mm3/st.
98
94
102
Fixing the lever
*
Injection quantity adjustment_05
Adjusting point
I
Rack position
-
Pump speed
r/min
100
100
100
Average injection quantity
mm3/st.
105
105
115
Fixing the lever
*
Rack limit
*
Timer adjustment
Pump speed
r/min
970--
Advance angle
deg.
0
0
0
Remarks
Start
Start
Timer adjustment_02
Pump speed
r/min
920
Advance angle
deg.
0.5
Timer adjustment_03
Pump speed
r/min
(1000)
Advance angle
deg.
1.5
1
2
Timer adjustment_04
Pump speed
r/min
1160
Advance angle
deg.
1.5
1
2
Timer adjustment_05
Pump speed
r/min
1450
Advance angle
deg.
7
6.5
7.5
Remarks
Finish
Finish
Test data Ex:
Governor adjustment
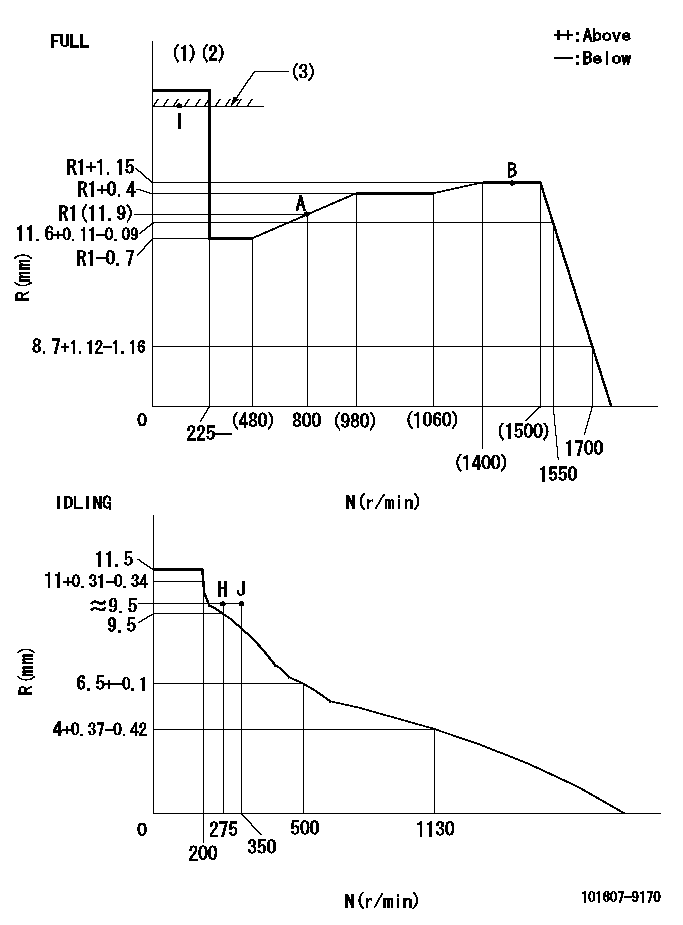
N:Pump speed
R:Rack position (mm)
(1)Torque cam stamping: T1
(2)Tolerance for racks not indicated: +-0.05mm.
(3)RACK LIMIT
----------
T1=J92
----------
----------
T1=J92
----------
Speed control lever angle
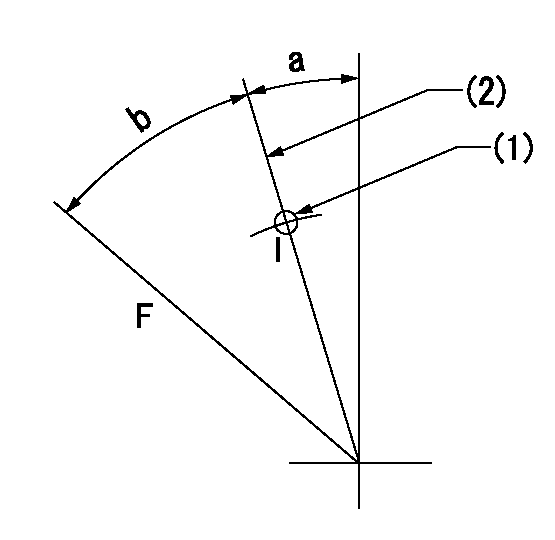
F:Full speed
I:Idle
(1)Use the hole at R = aa
(2)Stopper bolt set position 'H'
----------
aa=38mm
----------
a=5deg+-5deg b=37.5deg+-3deg
----------
aa=38mm
----------
a=5deg+-5deg b=37.5deg+-3deg
Stop lever angle
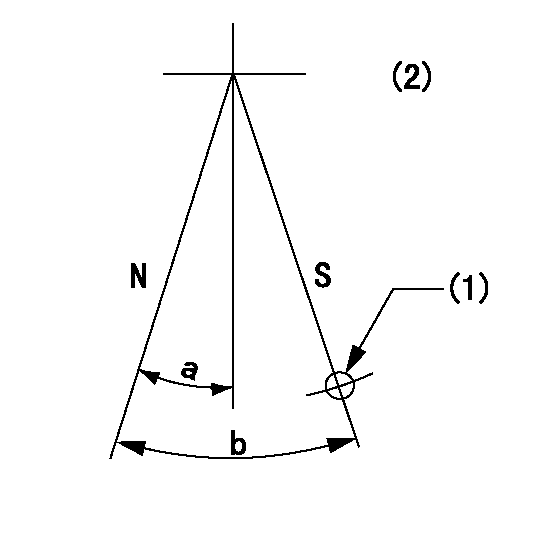
N:Pump normal
S:Stop the pump.
(1)Use the hole at R = aa
(2)No return spring
----------
aa=32mm
----------
a=10deg+-5deg b=40deg+-5deg
----------
aa=32mm
----------
a=10deg+-5deg b=40deg+-5deg
Timing setting
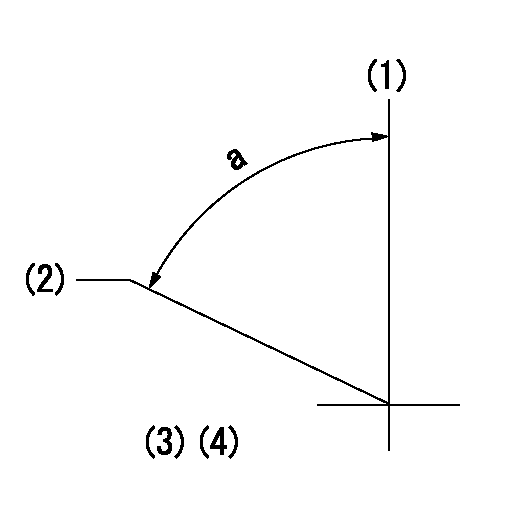
(1)Pump vertical direction
(2)Position of timer's threaded hole at No 1 cylinder's beginning of injection
(3)-
(4)-
----------
----------
a=(80deg)
----------
----------
a=(80deg)
Information:
Introduction
The problem that is identified below does not have a known permanent solution. Until a permanent solution is known, use the solution that is identified below.Problem
The fuel fill nozzle is being deactivated before the tank is full. The early deactivation causes the technician to hold the nozzle active in order to fill the fuel tank completely.Solution
Illustration 1 g03818479
773G / 775G (1) 308-0415 Vent As (2) 8J-6875 Shuttle Valve Gp (3) 252-5806 Shutoff Valve Assembly (4) 376-1308 Receiver As (5) 376-6616 Hose As
Illustration 2 g03818481
777G (1) 308-0415 Vent As (2) 8J-6875 Shuttle Valve Gp (3) 252-5806 Shutoff Valve Assembly (4) 376-1308 Receiver As (5) 376-6616 Hose As Perform the procedure in Troubleshooting, UENR2276, "Fluids Service System Troubleshooting". Report all failures through the DSN and replace with current parts as needed.
The problem that is identified below does not have a known permanent solution. Until a permanent solution is known, use the solution that is identified below.Problem
The fuel fill nozzle is being deactivated before the tank is full. The early deactivation causes the technician to hold the nozzle active in order to fill the fuel tank completely.Solution
Illustration 1 g03818479
773G / 775G (1) 308-0415 Vent As (2) 8J-6875 Shuttle Valve Gp (3) 252-5806 Shutoff Valve Assembly (4) 376-1308 Receiver As (5) 376-6616 Hose As
Illustration 2 g03818481
777G (1) 308-0415 Vent As (2) 8J-6875 Shuttle Valve Gp (3) 252-5806 Shutoff Valve Assembly (4) 376-1308 Receiver As (5) 376-6616 Hose As Perform the procedure in Troubleshooting, UENR2276, "Fluids Service System Troubleshooting". Report all failures through the DSN and replace with current parts as needed.