Information injection-pump assembly
ZEXEL
101607-6824
1016076824
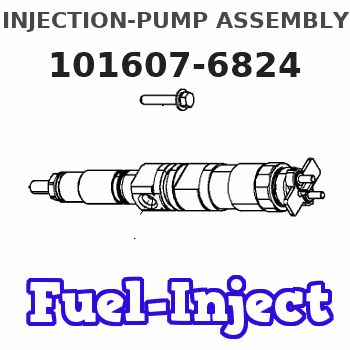
Rating:
Service parts 101607-6824 INJECTION-PUMP ASSEMBLY:
1.
_
6.
COUPLING PLATE
7.
COUPLING PLATE
8.
_
9.
_
11.
Nozzle and Holder
ME075761
12.
Open Pre:MPa(Kqf/cm2)
15.7{160}/21.6{220}
14.
NOZZLE
Include in #1:
101607-6824
as INJECTION-PUMP ASSEMBLY
Include in #2:
104746-5080
as _
Cross reference number
ZEXEL
101607-6824
1016076824
Zexel num
Bosch num
Firm num
Name
101607-6824
INJECTION-PUMP ASSEMBLY
Calibration Data:
Adjustment conditions
Test oil
1404 Test oil ISO4113 or {SAEJ967d}
1404 Test oil ISO4113 or {SAEJ967d}
Test oil temperature
degC
40
40
45
Nozzle and nozzle holder
105780-8140
Bosch type code
EF8511/9A
Nozzle
105780-0000
Bosch type code
DN12SD12T
Nozzle holder
105780-2080
Bosch type code
EF8511/9
Opening pressure
MPa
17.2
Opening pressure
kgf/cm2
175
Injection pipe
Outer diameter - inner diameter - length (mm) mm 6-2-600
Outer diameter - inner diameter - length (mm) mm 6-2-600
Overflow valve
131424-8420
Overflow valve opening pressure
kPa
255
221
289
Overflow valve opening pressure
kgf/cm2
2.6
2.25
2.95
Tester oil delivery pressure
kPa
157
157
157
Tester oil delivery pressure
kgf/cm2
1.6
1.6
1.6
Direction of rotation (viewed from drive side)
Left L
Left L
Injection timing adjustment
Direction of rotation (viewed from drive side)
Left L
Left L
Injection order
1-5-3-6-
2-4
Pre-stroke
mm
3.2
3.15
3.25
Beginning of injection position
Governor side NO.1
Governor side NO.1
Difference between angles 1
Cal 1-5 deg. 60 59.5 60.5
Cal 1-5 deg. 60 59.5 60.5
Difference between angles 2
Cal 1-3 deg. 120 119.5 120.5
Cal 1-3 deg. 120 119.5 120.5
Difference between angles 3
Cal 1-6 deg. 180 179.5 180.5
Cal 1-6 deg. 180 179.5 180.5
Difference between angles 4
Cyl.1-2 deg. 240 239.5 240.5
Cyl.1-2 deg. 240 239.5 240.5
Difference between angles 5
Cal 1-4 deg. 300 299.5 300.5
Cal 1-4 deg. 300 299.5 300.5
Injection quantity adjustment
Adjusting point
-
Rack position
11.8
Pump speed
r/min
850
850
850
Each cylinder's injection qty
mm3/st.
80
77.6
82.4
Basic
*
Fixing the rack
*
Standard for adjustment of the maximum variation between cylinders
*
Injection quantity adjustment_02
Adjusting point
Z
Rack position
9.5+-0.5
Pump speed
r/min
600
600
600
Each cylinder's injection qty
mm3/st.
10.8
9.2
12.4
Fixing the rack
*
Standard for adjustment of the maximum variation between cylinders
*
Injection quantity adjustment_03
Adjusting point
A
Rack position
R1(11.8)
Pump speed
r/min
850
850
850
Average injection quantity
mm3/st.
80
79
81
Basic
*
Fixing the lever
*
Injection quantity adjustment_04
Adjusting point
B
Rack position
R1+0.35
Pump speed
r/min
1450
1450
1450
Average injection quantity
mm3/st.
85
81
89
Fixing the lever
*
Injection quantity adjustment_05
Adjusting point
C
Rack position
R1-0.4
Pump speed
r/min
500
500
500
Average injection quantity
mm3/st.
58.5
54.5
62.5
Fixing the lever
*
Injection quantity adjustment_06
Adjusting point
I
Rack position
-
Pump speed
r/min
100
100
100
Average injection quantity
mm3/st.
95
85
105
Fixing the lever
*
Rack limit
*
Timer adjustment
Pump speed
r/min
950--
Advance angle
deg.
0
0
0
Remarks
Start
Start
Timer adjustment_02
Pump speed
r/min
900
Advance angle
deg.
0.5
Timer adjustment_03
Pump speed
r/min
-
Advance angle
deg.
1
0.5
1.5
Remarks
Measure the actual speed.
Measure the actual speed.
Timer adjustment_04
Pump speed
r/min
1100
Advance angle
deg.
1
0.5
1.5
Timer adjustment_05
Pump speed
r/min
1400
Advance angle
deg.
7
6.5
7.5
Remarks
Finish
Finish
Test data Ex:
Governor adjustment
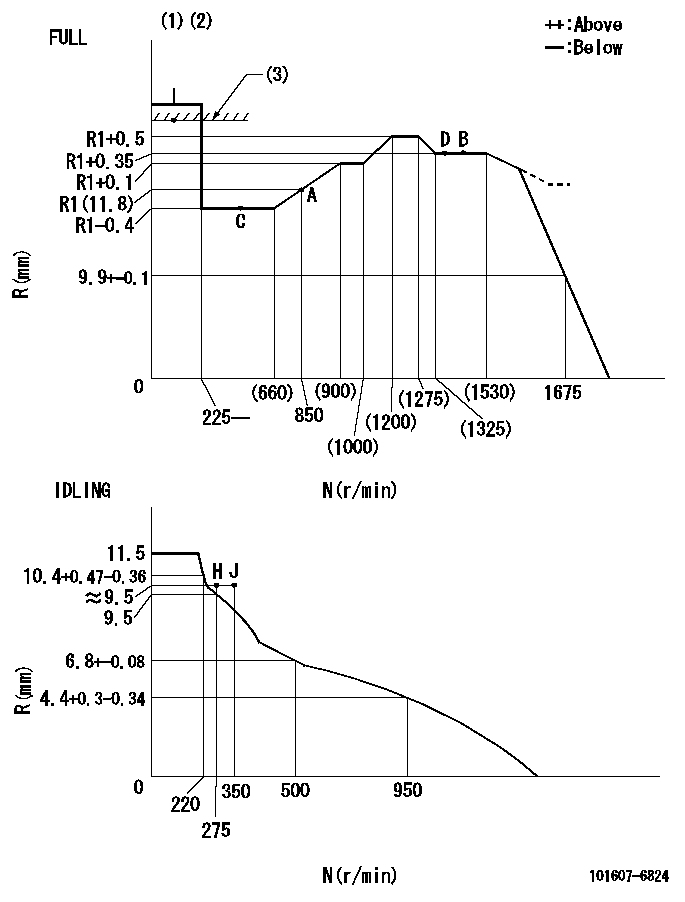
N:Pump speed
R:Rack position (mm)
(1)Torque cam stamping: T1
(2)Tolerance for racks not indicated: +-0.05mm.
(3)RACK LIMIT
----------
T1=K61
----------
----------
T1=K61
----------
Speed control lever angle

F:Full speed
I:Idle
(1)Stopper bolt set position 'H'
----------
----------
a=24deg+-5deg b=(47.5deg)+-3deg
----------
----------
a=24deg+-5deg b=(47.5deg)+-3deg
Stop lever angle
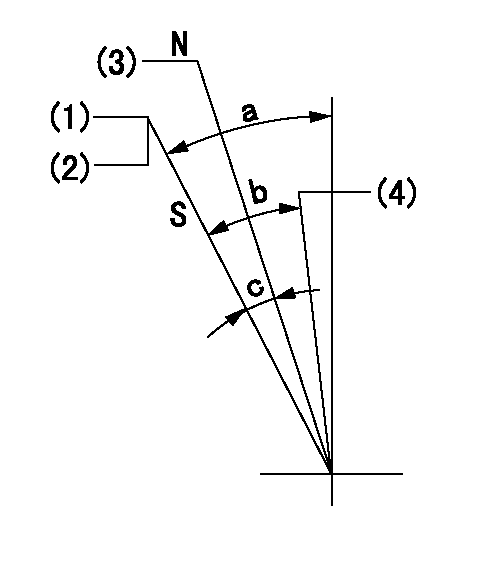
N:Engine manufacturer's normal use
S:Stop the pump.
(1)Set the stopper bolt at pump speed = aa and rack position = bb (non-injection rack position). Confirm non-injection.
(2)After setting the stopper bolt, confirm non-injection at speed cc. Rack position = dd (non-injection rack position).
(3)Rack position = approximately ee (speed lever full, speed = ff).
(4)Free (at delivery)
----------
aa=1450r/min bb=7.2-0.5mm cc=275r/min dd=(8.8)mm ee=15mm ff=0r/min
----------
a=36.5deg+-5deg b=(25deg) c=13deg+-5deg
----------
aa=1450r/min bb=7.2-0.5mm cc=275r/min dd=(8.8)mm ee=15mm ff=0r/min
----------
a=36.5deg+-5deg b=(25deg) c=13deg+-5deg
0000001501 LEVER
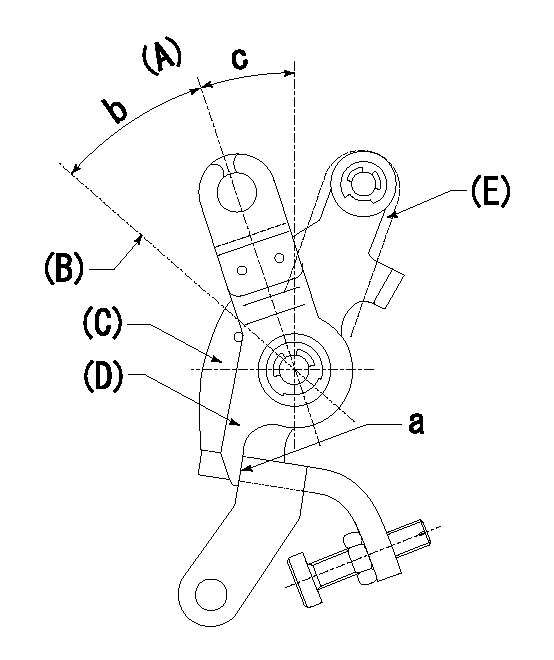
(A) Idle
(B) Full speed
(C) Base lever
(D) Accelerator lever
(E) Accelerator lever delivery position
1. Measure speed lever angle
(1)Measure the angle when the accelerator lever (D) contacted the base lever (C) at a.
----------
----------
b=(47.5deg)+-3deg c=24deg+-5deg
----------
----------
b=(47.5deg)+-3deg c=24deg+-5deg
Timing setting

(1)Pump vertical direction
(2)Position of timer's tooth at No 1 cylinder's beginning of injection
(3)B.T.D.C.: aa
(4)-
----------
aa=7deg
----------
a=(4deg)
----------
aa=7deg
----------
a=(4deg)
Information:
Reassemble Motor to Pump
Thoroughly clean the motor shaft and the hollow pump shaft. Remove the tape from the key (5) and keyway.
Apply a liberal amount of Loctite Nickel Anti-Seize No. 77164 to the pump shaft.
Install the shaft key (5) into the keyway.
Slide the motor shaft into the hollow pump shaft.
Reinstall the four washers (2) and nuts (1).Primary Strainer Removal and Installation
Primary Strainer Removal
Illustration 34 g06272994
(1) Primary Strainer
(2) Drain Plug
(3) Nut
(4) Strainer Cover
(5) Compression Ring
(6) Seal
(7) Strainer Housing
(8) Strainer Screens
Place a suitable drain pan underneath the primary strainer (1) to capture DEF fluid.
Remove and store the drain plug (2) from the bottom of the strainer cover (4). Allow DEF fluid to drain.
Inspect drain plug (1) and any seals, replace if damaged.
Install drain plug (2) into the bottom of the strainer cover (4).
Remove and store eight nuts (3) and the compression flange (5) located around the bottom of the strainer cover (4).
Remove and store the strainer cover (4) of the primary strainer (1).
Remove and inspect seal (6), replace if damaged.
Remove and discard the primary strainer screens (8) from the screen housing (7).Primary Strainer Installation
Install new primary strainer screens (8) into the screen housing (7).
Install screen housing (7) into the primary strainer (1).
Install the seal (6) onto the bottom of the strainer cover (4).
Install the strainer cover (4), compression flange (5), and eight nuts (3).
Open primary valve, operate DEF Transfer Pump and check for leaks around the bottom of the primary strainer (1).
Remove drain pan and dispose of DEF fluid.Secondary Strainer Removal and Installation
Secondary Strainer Removal
Illustration 35 g06272975
(1) Secondary Strainer
(2) Strainer Element
(3) Seal
(4) Strainer Cover
(5) Bolt
Place a suitable drain pan underneath the secondary strainer (1) to capture DEF fluid.
Remove and store the bolts (5).
Remove and store strainer cover (4).
Remove and inspect seal (3), replace if damaged.
Remove and discard strainer element (2).Secondary Strainer Installation
Install new secondary strainer element (2) into the secondary strainer (1).
Install the seal (3) onto the bottom of the strainer cover (4).
Install the strainer cover (4) with bolts (5).
Open secondary valve, operate DEF Transfer Pump and check for leaks around the bottom of the secondary strainer (1).
Remove drain pan and dispose of DEF fluid.Product Description
Extended Warranties and Service Contracts
A wide variety of protection plans are available for Cat Engines. Consult your Caterpillardealer for detailed information on the specific programs and coverages that are available.DEF Transfer Pump is an optional attachment to an engine system. Refer to the warranty information for your engine or consult your Caterpillar dealer.Customer Assistance
USA and Canada
When a problem arises concerning the operation or the service of a Marine engine, the problem will normally be managed by the dealer in your area.Your satisfaction is a primary concern to Caterpillar and to Caterpillar dealers. If you have a problem that has not been handled to your complete satisfaction, follow these steps:
Discuss your problem with a manager from the dealership.
If your problem cannot be resolved at the dealer level, use the phone number that is listed below to talk with a Field Service Coordinator:877-228-9900
The normal hours are from 7:00 AM
Thoroughly clean the motor shaft and the hollow pump shaft. Remove the tape from the key (5) and keyway.
Apply a liberal amount of Loctite Nickel Anti-Seize No. 77164 to the pump shaft.
Install the shaft key (5) into the keyway.
Slide the motor shaft into the hollow pump shaft.
Reinstall the four washers (2) and nuts (1).Primary Strainer Removal and Installation
Primary Strainer Removal
Illustration 34 g06272994
(1) Primary Strainer
(2) Drain Plug
(3) Nut
(4) Strainer Cover
(5) Compression Ring
(6) Seal
(7) Strainer Housing
(8) Strainer Screens
Place a suitable drain pan underneath the primary strainer (1) to capture DEF fluid.
Remove and store the drain plug (2) from the bottom of the strainer cover (4). Allow DEF fluid to drain.
Inspect drain plug (1) and any seals, replace if damaged.
Install drain plug (2) into the bottom of the strainer cover (4).
Remove and store eight nuts (3) and the compression flange (5) located around the bottom of the strainer cover (4).
Remove and store the strainer cover (4) of the primary strainer (1).
Remove and inspect seal (6), replace if damaged.
Remove and discard the primary strainer screens (8) from the screen housing (7).Primary Strainer Installation
Install new primary strainer screens (8) into the screen housing (7).
Install screen housing (7) into the primary strainer (1).
Install the seal (6) onto the bottom of the strainer cover (4).
Install the strainer cover (4), compression flange (5), and eight nuts (3).
Open primary valve, operate DEF Transfer Pump and check for leaks around the bottom of the primary strainer (1).
Remove drain pan and dispose of DEF fluid.Secondary Strainer Removal and Installation
Secondary Strainer Removal
Illustration 35 g06272975
(1) Secondary Strainer
(2) Strainer Element
(3) Seal
(4) Strainer Cover
(5) Bolt
Place a suitable drain pan underneath the secondary strainer (1) to capture DEF fluid.
Remove and store the bolts (5).
Remove and store strainer cover (4).
Remove and inspect seal (3), replace if damaged.
Remove and discard strainer element (2).Secondary Strainer Installation
Install new secondary strainer element (2) into the secondary strainer (1).
Install the seal (3) onto the bottom of the strainer cover (4).
Install the strainer cover (4) with bolts (5).
Open secondary valve, operate DEF Transfer Pump and check for leaks around the bottom of the secondary strainer (1).
Remove drain pan and dispose of DEF fluid.Product Description
Extended Warranties and Service Contracts
A wide variety of protection plans are available for Cat Engines. Consult your Caterpillardealer for detailed information on the specific programs and coverages that are available.DEF Transfer Pump is an optional attachment to an engine system. Refer to the warranty information for your engine or consult your Caterpillar dealer.Customer Assistance
USA and Canada
When a problem arises concerning the operation or the service of a Marine engine, the problem will normally be managed by the dealer in your area.Your satisfaction is a primary concern to Caterpillar and to Caterpillar dealers. If you have a problem that has not been handled to your complete satisfaction, follow these steps:
Discuss your problem with a manager from the dealership.
If your problem cannot be resolved at the dealer level, use the phone number that is listed below to talk with a Field Service Coordinator:877-228-9900
The normal hours are from 7:00 AM
Have questions with 101607-6824?
Group cross 101607-6824 ZEXEL
101607-6824
INJECTION-PUMP ASSEMBLY