Information injection-pump assembly
ZEXEL
101607-6822
1016076822
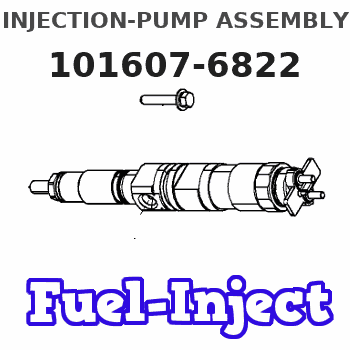
Rating:
Service parts 101607-6822 INJECTION-PUMP ASSEMBLY:
1.
_
6.
COUPLING PLATE
7.
COUPLING PLATE
8.
_
9.
_
11.
Nozzle and Holder
ME075761
12.
Open Pre:MPa(Kqf/cm2)
15.7{160}/21.6{220}
14.
NOZZLE
Cross reference number
ZEXEL
101607-6822
1016076822
Zexel num
Bosch num
Firm num
Name
101607-6822
INJECTION-PUMP ASSEMBLY
Calibration Data:
Adjustment conditions
Test oil
1404 Test oil ISO4113 or {SAEJ967d}
1404 Test oil ISO4113 or {SAEJ967d}
Test oil temperature
degC
40
40
45
Nozzle and nozzle holder
105780-8140
Bosch type code
EF8511/9A
Nozzle
105780-0000
Bosch type code
DN12SD12T
Nozzle holder
105780-2080
Bosch type code
EF8511/9
Opening pressure
MPa
17.2
Opening pressure
kgf/cm2
175
Injection pipe
Outer diameter - inner diameter - length (mm) mm 6-2-600
Outer diameter - inner diameter - length (mm) mm 6-2-600
Overflow valve
131424-8420
Overflow valve opening pressure
kPa
255
221
289
Overflow valve opening pressure
kgf/cm2
2.6
2.25
2.95
Tester oil delivery pressure
kPa
157
157
157
Tester oil delivery pressure
kgf/cm2
1.6
1.6
1.6
Direction of rotation (viewed from drive side)
Left L
Left L
Injection timing adjustment
Direction of rotation (viewed from drive side)
Left L
Left L
Injection order
1-5-3-6-
2-4
Pre-stroke
mm
3.2
3.15
3.25
Beginning of injection position
Governor side NO.1
Governor side NO.1
Difference between angles 1
Cal 1-5 deg. 60 59.5 60.5
Cal 1-5 deg. 60 59.5 60.5
Difference between angles 2
Cal 1-3 deg. 120 119.5 120.5
Cal 1-3 deg. 120 119.5 120.5
Difference between angles 3
Cal 1-6 deg. 180 179.5 180.5
Cal 1-6 deg. 180 179.5 180.5
Difference between angles 4
Cyl.1-2 deg. 240 239.5 240.5
Cyl.1-2 deg. 240 239.5 240.5
Difference between angles 5
Cal 1-4 deg. 300 299.5 300.5
Cal 1-4 deg. 300 299.5 300.5
Injection quantity adjustment
Adjusting point
-
Rack position
11.9
Pump speed
r/min
850
850
850
Each cylinder's injection qty
mm3/st.
86.5
83.9
89.1
Basic
*
Fixing the rack
*
Standard for adjustment of the maximum variation between cylinders
*
Injection quantity adjustment_02
Adjusting point
Z
Rack position
9.5+-0.5
Pump speed
r/min
600
600
600
Each cylinder's injection qty
mm3/st.
10.8
9.2
12.4
Fixing the rack
*
Standard for adjustment of the maximum variation between cylinders
*
Injection quantity adjustment_03
Adjusting point
A
Rack position
R1(11.9)
Pump speed
r/min
850
850
850
Average injection quantity
mm3/st.
86.5
85.5
87.5
Basic
*
Fixing the lever
*
Injection quantity adjustment_04
Adjusting point
B
Rack position
R1+0.35
Pump speed
r/min
1450
1450
1450
Average injection quantity
mm3/st.
90.5
86.5
94.5
Fixing the lever
*
Injection quantity adjustment_05
Adjusting point
C
Rack position
R1-0.4
Pump speed
r/min
500
500
500
Average injection quantity
mm3/st.
71.5
67.5
75.5
Fixing the lever
*
Injection quantity adjustment_06
Adjusting point
I
Rack position
-
Pump speed
r/min
100
100
100
Average injection quantity
mm3/st.
95
85
105
Fixing the lever
*
Rack limit
*
Timer adjustment
Pump speed
r/min
950--
Advance angle
deg.
0
0
0
Remarks
Start
Start
Timer adjustment_02
Pump speed
r/min
900
Advance angle
deg.
0.5
Timer adjustment_03
Pump speed
r/min
-
Advance angle
deg.
1
0.5
1.5
Remarks
Measure the actual speed.
Measure the actual speed.
Timer adjustment_04
Pump speed
r/min
1100
Advance angle
deg.
1
0.5
1.5
Timer adjustment_05
Pump speed
r/min
1400
Advance angle
deg.
7
6.5
7.5
Remarks
Finish
Finish
Test data Ex:
Governor adjustment
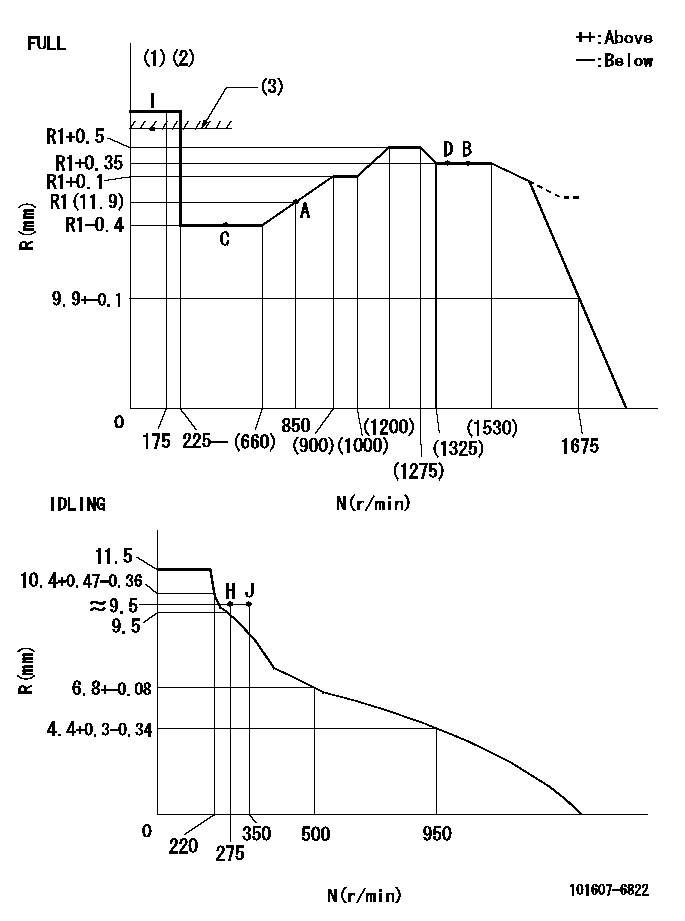
N:Pump speed
R:Rack position (mm)
(1)Torque cam stamping: T1
(2)Tolerance for racks not indicated: +-0.05mm.
(3)RACK LIMIT
----------
T1=K61
----------
----------
T1=K61
----------
Speed control lever angle
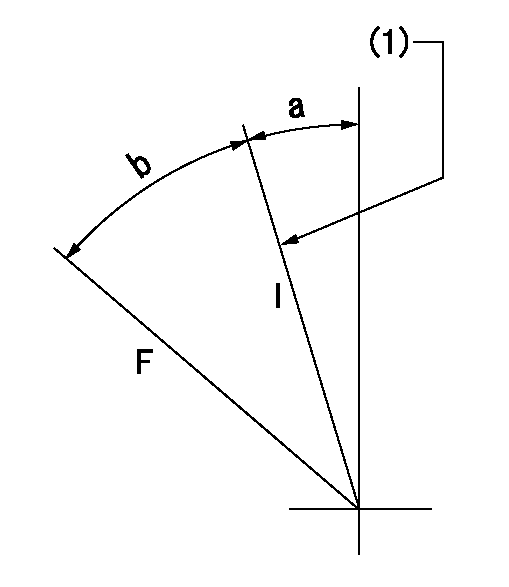
F:Full speed
I:Idle
(1)Stopper bolt set position 'H'
----------
----------
a=24deg+-5deg b=(47.5deg)+-3deg
----------
----------
a=24deg+-5deg b=(47.5deg)+-3deg
Stop lever angle
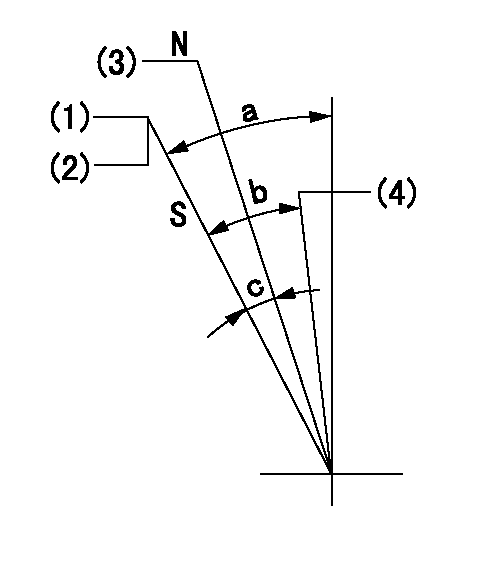
N:Engine manufacturer's normal use
S:Stop the pump.
(1)Set the stopper bolt at pump speed = aa and rack position = bb (non-injection rack position). Confirm non-injection.
(2)After setting the stopper bolt, confirm non-injection at speed cc. Rack position = dd (non-injection rack position).
(3)Rack position = approximately ee (speed lever full, speed = ff).
(4)Free (at delivery)
----------
aa=1450r/min bb=7.2-0.5mm cc=275r/min dd=(8.8)mm ee=15mm ff=0r/min
----------
a=36.5deg+-5deg b=(25deg) c=13deg+-5deg
----------
aa=1450r/min bb=7.2-0.5mm cc=275r/min dd=(8.8)mm ee=15mm ff=0r/min
----------
a=36.5deg+-5deg b=(25deg) c=13deg+-5deg
0000001501 LEVER
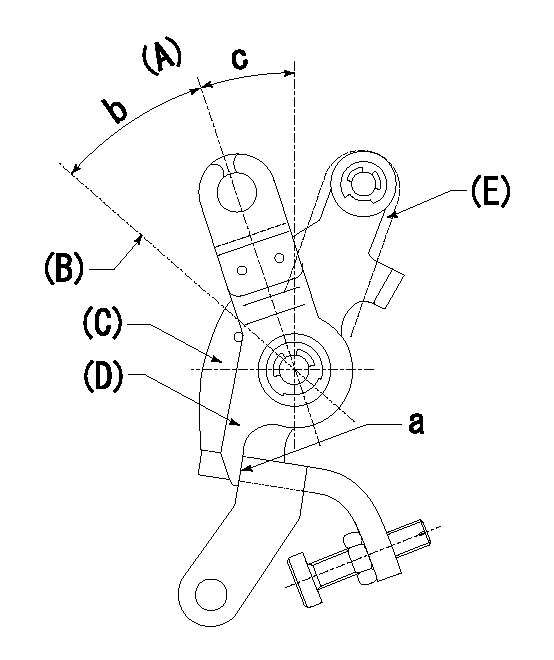
(A) Idle
(B) Full speed
(C) Base lever
(D) Accelerator lever
(E) Accelerator lever delivery position
1. Measure speed lever angle
(1)Measure the angle when the accelerator lever (D) contacted the base lever (C) at a.
----------
----------
b=(47.5deg)+-3deg c=24deg+-5deg
----------
----------
b=(47.5deg)+-3deg c=24deg+-5deg
Timing setting

(1)Pump vertical direction
(2)Position of timer's tooth at No 1 cylinder's beginning of injection
(3)B.T.D.C.: aa
(4)-
----------
aa=7deg
----------
a=(3deg)
----------
aa=7deg
----------
a=(3deg)
Information:
Requirements For The ECM
The Electronic Control Module (ECM) for the Diesel Particulate Filter Monitor System is powered by either a +12 VDC or +24 VDC nominal battery. Refer to Table 1 for the limits for the voltage for the ECM. Refer to Illustration There is one 5 VDC +/-0.25 VDC at 500 mA auxiliary Power Supply on the ECM, routed to the machine pin group. A single return pin is used for this power supply. An "AD" channel monitors this power supply. The ECM internal power supply will provide +5 VDC for external sensor use. Refer to Illustration 1.
Illustration 1 g01340837
Illustration 2 displays mounting the Diesel Particulate Filter Monitor System to the ECM.
Illustration 2 g01340267
Table 1
Power Supply Requirements    
Requirements for 12 VDC or 24 VDC system     Value     Notes    
Operating Minimum Voltage     +9V     Minimum continuous operating voltage without damage to the ECM    
Operating Minimum Voltage     +32V     Maximum continuous operating voltage without damage to the ECM    
Overvoltage Maximum (two minutes continuous)     +80V     At 25 °C (77 °F)    
Reverse Voltage (one hours)     -32V    
85 °C (185 °F)    
power up voltage for the ECM     +9V     Minimum voltage for the ECM in order to run internally. Operating the engine at this voltage will cause damage to the ECM.    
Cranking Voltage            
Maximum current draw with key switch off     10mA        
Maximum current draw with 0 engine speed and no loads being driven     500mA        
Maximum continuous operating current draw     10A     This is highly dependent upon the number and type of loads driven by the ECM.    
Recommended Battery Fuse size     15A        Programming For The ECM
The ECM is flash programmed via the Customer Data Link (CDL) with the service tool.Key Switch For The ECM
The ECM Key Switch provides the ability to shut down the ECM via a low current switch. The ECM Key Switch also increases the life of the batteries by shutting the ECM off. The Key Switch also allows operators to remotely power off the ECM. The Key Switch controls when the ECM powers up. With the Key Switch "OFF", the ECM current draw will not exceed 10mA.Connector For The ECM
The ECM uses a 70 pin connector to connect to the OEM vehicle wiring harness. The ECM Connector Screw torque should be 6 1 N m (4 0.7 lb ft)Connector Wire Gauge Size For The ECM
The battery positive and negative connections must be made with 14 gauge SAE J1128 type GXL wire for the Deutsch stamped and formed terminal or the Deutsch solid terminal. All other connections may be16 gauge or 18 gauge SAE J1128 type SXL or 14, 16 or 18 gauge SAE J1128 type GXL (or equivalent wire).For most components on the engine an 18 gauge wire has sufficient current capacity, however, many applications will benefit from the increased reliability and durability of 16 gauge
The Electronic Control Module (ECM) for the Diesel Particulate Filter Monitor System is powered by either a +12 VDC or +24 VDC nominal battery. Refer to Table 1 for the limits for the voltage for the ECM. Refer to Illustration There is one 5 VDC +/-0.25 VDC at 500 mA auxiliary Power Supply on the ECM, routed to the machine pin group. A single return pin is used for this power supply. An "AD" channel monitors this power supply. The ECM internal power supply will provide +5 VDC for external sensor use. Refer to Illustration 1.
Illustration 1 g01340837
Illustration 2 displays mounting the Diesel Particulate Filter Monitor System to the ECM.
Illustration 2 g01340267
Table 1
Power Supply Requirements    
Requirements for 12 VDC or 24 VDC system     Value     Notes    
Operating Minimum Voltage     +9V     Minimum continuous operating voltage without damage to the ECM    
Operating Minimum Voltage     +32V     Maximum continuous operating voltage without damage to the ECM    
Overvoltage Maximum (two minutes continuous)     +80V     At 25 °C (77 °F)    
Reverse Voltage (one hours)     -32V    
85 °C (185 °F)    
power up voltage for the ECM     +9V     Minimum voltage for the ECM in order to run internally. Operating the engine at this voltage will cause damage to the ECM.    
Cranking Voltage            
Maximum current draw with key switch off     10mA        
Maximum current draw with 0 engine speed and no loads being driven     500mA        
Maximum continuous operating current draw     10A     This is highly dependent upon the number and type of loads driven by the ECM.    
Recommended Battery Fuse size     15A        Programming For The ECM
The ECM is flash programmed via the Customer Data Link (CDL) with the service tool.Key Switch For The ECM
The ECM Key Switch provides the ability to shut down the ECM via a low current switch. The ECM Key Switch also increases the life of the batteries by shutting the ECM off. The Key Switch also allows operators to remotely power off the ECM. The Key Switch controls when the ECM powers up. With the Key Switch "OFF", the ECM current draw will not exceed 10mA.Connector For The ECM
The ECM uses a 70 pin connector to connect to the OEM vehicle wiring harness. The ECM Connector Screw torque should be 6 1 N m (4 0.7 lb ft)Connector Wire Gauge Size For The ECM
The battery positive and negative connections must be made with 14 gauge SAE J1128 type GXL wire for the Deutsch stamped and formed terminal or the Deutsch solid terminal. All other connections may be16 gauge or 18 gauge SAE J1128 type SXL or 14, 16 or 18 gauge SAE J1128 type GXL (or equivalent wire).For most components on the engine an 18 gauge wire has sufficient current capacity, however, many applications will benefit from the increased reliability and durability of 16 gauge
Have questions with 101607-6822?
Group cross 101607-6822 ZEXEL
101607-6822
INJECTION-PUMP ASSEMBLY