Information injection-pump assembly
ZEXEL
101607-6821
1016076821
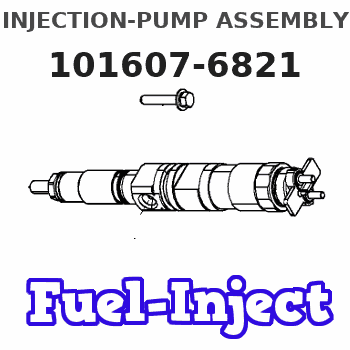
Rating:
Service parts 101607-6821 INJECTION-PUMP ASSEMBLY:
1.
_
6.
COUPLING PLATE
7.
COUPLING PLATE
8.
_
9.
_
11.
Nozzle and Holder
ME075761
12.
Open Pre:MPa(Kqf/cm2)
15.7{160}/21.6{220}
14.
NOZZLE
Cross reference number
ZEXEL
101607-6821
1016076821
Zexel num
Bosch num
Firm num
Name
101607-6821
INJECTION-PUMP ASSEMBLY
Calibration Data:
Adjustment conditions
Test oil
1404 Test oil ISO4113 or {SAEJ967d}
1404 Test oil ISO4113 or {SAEJ967d}
Test oil temperature
degC
40
40
45
Nozzle and nozzle holder
105780-8140
Bosch type code
EF8511/9A
Nozzle
105780-0000
Bosch type code
DN12SD12T
Nozzle holder
105780-2080
Bosch type code
EF8511/9
Opening pressure
MPa
17.2
Opening pressure
kgf/cm2
175
Injection pipe
Outer diameter - inner diameter - length (mm) mm 6-2-600
Outer diameter - inner diameter - length (mm) mm 6-2-600
Overflow valve
131424-8420
Overflow valve opening pressure
kPa
255
221
289
Overflow valve opening pressure
kgf/cm2
2.6
2.25
2.95
Tester oil delivery pressure
kPa
157
157
157
Tester oil delivery pressure
kgf/cm2
1.6
1.6
1.6
Direction of rotation (viewed from drive side)
Left L
Left L
Injection timing adjustment
Direction of rotation (viewed from drive side)
Left L
Left L
Injection order
1-5-3-6-
2-4
Pre-stroke
mm
3.2
3.15
3.25
Beginning of injection position
Governor side NO.1
Governor side NO.1
Difference between angles 1
Cal 1-5 deg. 60 59.5 60.5
Cal 1-5 deg. 60 59.5 60.5
Difference between angles 2
Cal 1-3 deg. 120 119.5 120.5
Cal 1-3 deg. 120 119.5 120.5
Difference between angles 3
Cal 1-6 deg. 180 179.5 180.5
Cal 1-6 deg. 180 179.5 180.5
Difference between angles 4
Cyl.1-2 deg. 240 239.5 240.5
Cyl.1-2 deg. 240 239.5 240.5
Difference between angles 5
Cal 1-4 deg. 300 299.5 300.5
Cal 1-4 deg. 300 299.5 300.5
Injection quantity adjustment
Adjusting point
-
Rack position
11.9
Pump speed
r/min
850
850
850
Each cylinder's injection qty
mm3/st.
86.5
83.9
89.1
Basic
*
Fixing the rack
*
Standard for adjustment of the maximum variation between cylinders
*
Injection quantity adjustment_02
Adjusting point
Z
Rack position
9.5+-0.5
Pump speed
r/min
600
600
600
Each cylinder's injection qty
mm3/st.
10.8
9.2
12.4
Fixing the rack
*
Standard for adjustment of the maximum variation between cylinders
*
Injection quantity adjustment_03
Adjusting point
A
Rack position
R1(11.9)
Pump speed
r/min
850
850
850
Average injection quantity
mm3/st.
86.5
85.5
87.5
Basic
*
Fixing the lever
*
Injection quantity adjustment_04
Adjusting point
B
Rack position
R1+0.25
Pump speed
r/min
1450
1450
1450
Average injection quantity
mm3/st.
88
84
92
Fixing the lever
*
Injection quantity adjustment_05
Adjusting point
C
Rack position
R1-0.4
Pump speed
r/min
500
500
500
Average injection quantity
mm3/st.
71.5
67.5
75.5
Fixing the lever
*
Injection quantity adjustment_06
Adjusting point
I
Rack position
-
Pump speed
r/min
100
100
100
Average injection quantity
mm3/st.
95
85
105
Fixing the lever
*
Rack limit
*
Timer adjustment
Pump speed
r/min
950--
Advance angle
deg.
0
0
0
Remarks
Start
Start
Timer adjustment_02
Pump speed
r/min
900
Advance angle
deg.
0.5
Timer adjustment_03
Pump speed
r/min
-
Advance angle
deg.
1
0.5
1.5
Remarks
Measure the actual speed.
Measure the actual speed.
Timer adjustment_04
Pump speed
r/min
1100
Advance angle
deg.
1
0.5
1.5
Timer adjustment_05
Pump speed
r/min
1400
Advance angle
deg.
7
6.5
7.5
Remarks
Finish
Finish
Test data Ex:
Governor adjustment
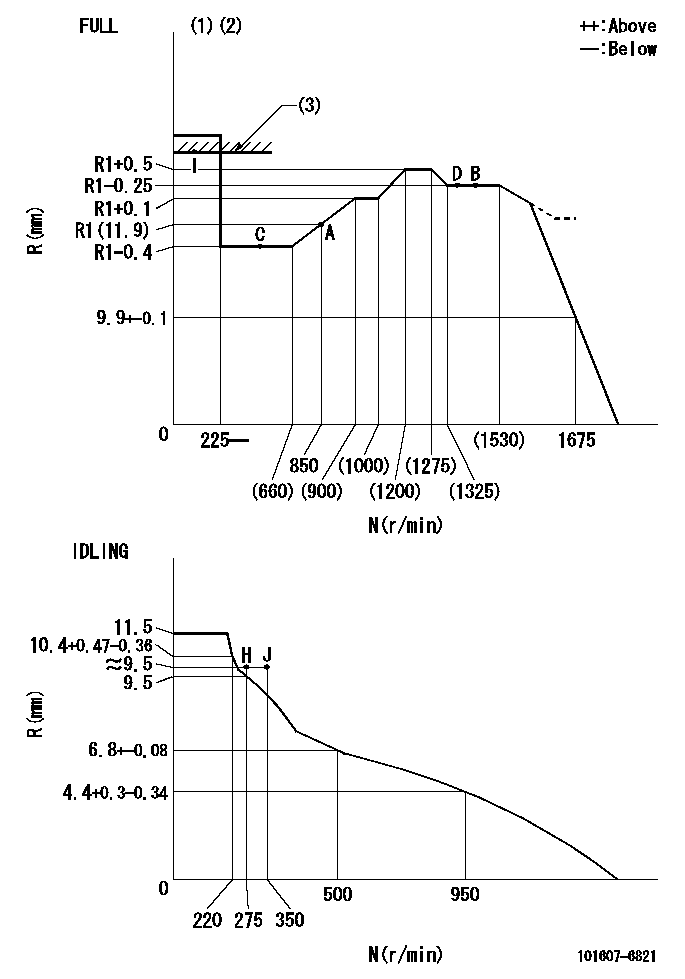
N:Pump speed
R:Rack position (mm)
(1)Torque cam stamping: T1
(2)Tolerance for racks not indicated: +-0.05mm.
(3)RACK LIMIT
----------
T1=J70
----------
----------
T1=J70
----------
Speed control lever angle
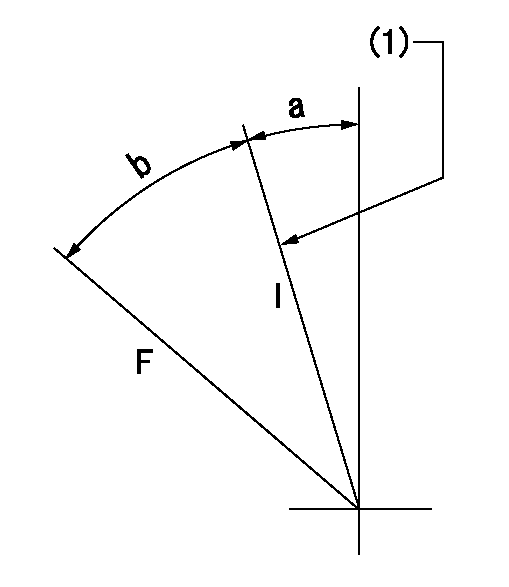
F:Full speed
I:Idle
(1)Stopper bolt set position 'H'
----------
----------
a=24deg+-5deg b=(47.5deg)+-3deg
----------
----------
a=24deg+-5deg b=(47.5deg)+-3deg
Stop lever angle
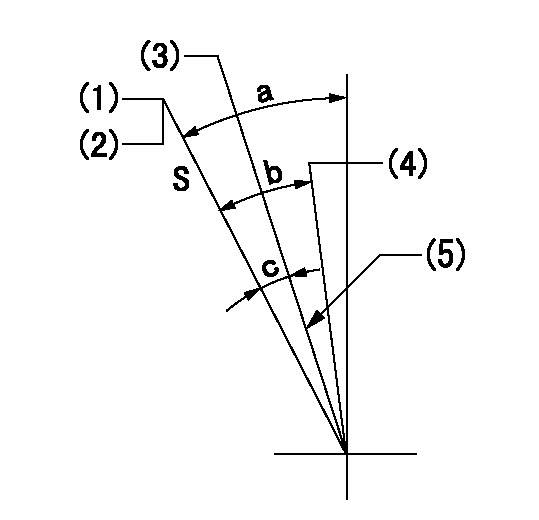
S:Stop the pump.
(1)Set the stopper bolt at pump speed = aa and rack position = bb (non-injection rack position). Confirm non-injection.
(2)After setting the stopper bolt, confirm non-injection at speed cc. Rack position = dd (non-injection rack position).
(3)Rack position = approximately ee (speed lever full, speed = ff).
(4)Free (at delivery)
(5)Normal use set at engine manufacturer.
----------
aa=1450r/min bb=7.2-0.5mm cc=275r/min dd=(8.8)mm ee=15mm ff=0r/min
----------
a=36.5deg+-5deg b=(25deg) c=13deg+-5deg
----------
aa=1450r/min bb=7.2-0.5mm cc=275r/min dd=(8.8)mm ee=15mm ff=0r/min
----------
a=36.5deg+-5deg b=(25deg) c=13deg+-5deg
0000001501 LEVER
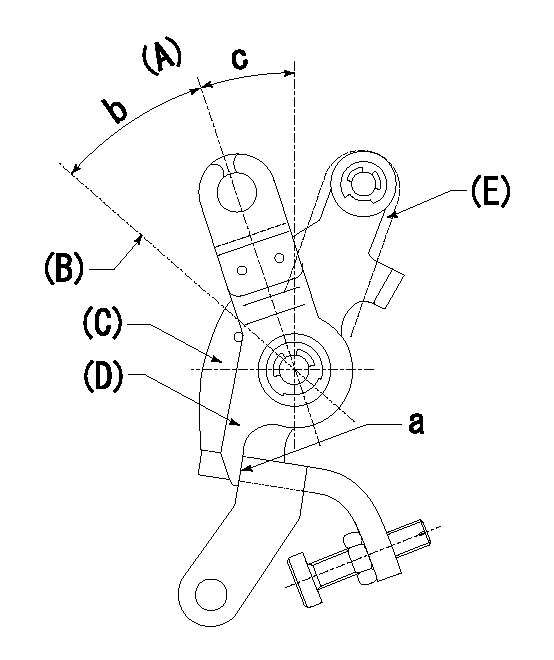
(A) Idle
(B) Full speed
(C) Base lever
(D) Accelerator lever
(E) Accelerator lever delivery position
1. Measure speed lever angle
(1)Measure the angle when the accelerator lever (D) contacted the base lever (C) at a.
----------
----------
b=(47.5deg)+-3deg c=24deg+-5deg
----------
----------
b=(47.5deg)+-3deg c=24deg+-5deg
Timing setting

(1)Pump vertical direction
(2)Position of timer's tooth at No 1 cylinder's beginning of injection
(3)B.T.D.C.: aa
(4)-
----------
aa=7deg
----------
a=(3deg)
----------
aa=7deg
----------
a=(3deg)
Information:
Illustration 1 g01339995
Over Temperature Alarm
The Over Temperature alarm monitors the particulate filter temperature and the over temperature alarm produces an alarm if the temperature exceeds a configurable threshold. The operator is informed of an Over Temperature Alarm. The Over-Temperature Warning alarm is set to the "ON" state when the monitored temperature reaches or exceeds the Assert Alarm temperature value as configured by the user through the monitoring system. Pin 59 in the "ON" state will illuminate the optional Over-Temperature LED. Refer Systems Operation Troubleshooting, Testing and Adjusting, KENR6695-00, "Input Components".Through the CAT ET service tool, the users may configure the conditions to reset the Over-Temperature Warning alarm to "OFF" by choosing one of two methods:
The Over-Temperature Warning alarm will automatically be set to the "OFF" state when the monitored temperature drops below the Assert Alarm temperature value.
The Over-Temperature Warning alarm will stay latched in the "ON" state until cleared by the user through Cat ET.Over-Pressure Alarm
The Over-Pressure Alarm monitors the particulate filter pressure and annunciates an alarm if the pressure exeeds a configurable threshold. The operator should be informed of an Over-Pressure Alarm. There are two configurable Over-Pressure Alarm sets of conditions. By programming the two configurable Over-Pressure Alarm sets differently, one may be considered a Warning alarm and the other as a Critical alarm. The Warning alarm will be associated with Pin 60 (the optional Over-Pressure LED) and the Critical alarm will be associated with Pin 61 (the optional System Problem LED).
The Warning alarm is associated with the Over-Pressure LED.
The Critical alarm is associated with the System Problem LED.Refer Systems Operation Troubleshooting, Testing and Adjusting, KENR6695-00, "Input Components"Conditions To Set The Over-Pressure Alarm To The "ON" State
When the pressure exceeds the Pressure Threshold for the programmed percent of time (Duty Cycle) over the Time Interval, then the appropriate alarm (Over-Pressure or System Problem) is set to "ON". The pressure is sampled in 1 second intervals.Conditions To Set The Over-Pressure Alarm To The "OFF" State
The user may configure the conditions to reset the Over-Pressure alarms to "OFF" by choosing one of two methods:
The Over-Pressure alarm is set to the "OFF" state when the "ON" conditions are no longer met.
The Over-Pressure alarm will stay latched in the "ON" state until the Logged Event is cleared by the user through Cat ET.Configurable Parameters - The following parameters are configurable through the CAT ET service tool,
Particulate Trap Over-Pressure Warning Activation Time Percentage – Default is 10%
Particulate Trap Over-Pressure Warning Alarm Reset Configuration – Default is Manual
Particulate Trap Over-Pressure Critical Alarm Activation Time Percentage – Default is 10%Programmable Monitoring System
The purpose of the programmable monitoring system is to give the customers the ability to customize how the system reacts to possible engine damaging conditions. This feature reduces the number of custom personality modules, and part numbers, needed to meet widely varying customer needs. CAT ET can be used to view Programmable Monitoring System settings and customize the Programmable Monitoring System if allowed via security settings. Table 1 describes the programmable monitoring system. In
Have questions with 101607-6821?
Group cross 101607-6821 ZEXEL
101607-6821
INJECTION-PUMP ASSEMBLY