Information injection-pump assembly
ZEXEL
101607-6813
1016076813
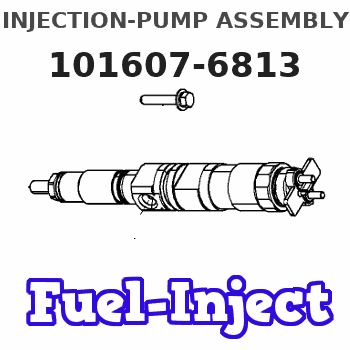
Rating:
Service parts 101607-6813 INJECTION-PUMP ASSEMBLY:
1.
_
6.
COUPLING PLATE
7.
COUPLING PLATE
8.
_
9.
_
11.
Nozzle and Holder
ME075788
12.
Open Pre:MPa(Kqf/cm2)
15.7{160}/21.6{220}
14.
NOZZLE
Cross reference number
ZEXEL
101607-6813
1016076813
Zexel num
Bosch num
Firm num
Name
101607-6813
INJECTION-PUMP ASSEMBLY
Calibration Data:
Adjustment conditions
Test oil
1404 Test oil ISO4113 or {SAEJ967d}
1404 Test oil ISO4113 or {SAEJ967d}
Test oil temperature
degC
40
40
45
Nozzle and nozzle holder
105780-8140
Bosch type code
EF8511/9A
Nozzle
105780-0000
Bosch type code
DN12SD12T
Nozzle holder
105780-2080
Bosch type code
EF8511/9
Opening pressure
MPa
17.2
Opening pressure
kgf/cm2
175
Injection pipe
Outer diameter - inner diameter - length (mm) mm 6-2-600
Outer diameter - inner diameter - length (mm) mm 6-2-600
Overflow valve
131424-8420
Overflow valve opening pressure
kPa
255
221
289
Overflow valve opening pressure
kgf/cm2
2.6
2.25
2.95
Tester oil delivery pressure
kPa
157
157
157
Tester oil delivery pressure
kgf/cm2
1.6
1.6
1.6
Direction of rotation (viewed from drive side)
Left L
Left L
Injection timing adjustment
Direction of rotation (viewed from drive side)
Left L
Left L
Injection order
1-5-3-6-
2-4
Pre-stroke
mm
3.2
3.15
3.25
Beginning of injection position
Governor side NO.1
Governor side NO.1
Difference between angles 1
Cal 1-5 deg. 60 59.5 60.5
Cal 1-5 deg. 60 59.5 60.5
Difference between angles 2
Cal 1-3 deg. 120 119.5 120.5
Cal 1-3 deg. 120 119.5 120.5
Difference between angles 3
Cal 1-6 deg. 180 179.5 180.5
Cal 1-6 deg. 180 179.5 180.5
Difference between angles 4
Cyl.1-2 deg. 240 239.5 240.5
Cyl.1-2 deg. 240 239.5 240.5
Difference between angles 5
Cal 1-4 deg. 300 299.5 300.5
Cal 1-4 deg. 300 299.5 300.5
Injection quantity adjustment
Adjusting point
-
Rack position
11.7
Pump speed
r/min
850
850
850
Each cylinder's injection qty
mm3/st.
78
75.7
80.3
Basic
*
Fixing the rack
*
Standard for adjustment of the maximum variation between cylinders
*
Injection quantity adjustment_02
Adjusting point
Z
Rack position
10+-0.5
Pump speed
r/min
480
480
480
Each cylinder's injection qty
mm3/st.
21.8
18.5
25.1
Fixing the rack
*
Standard for adjustment of the maximum variation between cylinders
*
Injection quantity adjustment_03
Adjusting point
A
Rack position
R1(11.7)
Pump speed
r/min
850
850
850
Average injection quantity
mm3/st.
78
77
79
Basic
*
Fixing the lever
*
Injection quantity adjustment_04
Adjusting point
B
Rack position
R1+0.25
Pump speed
r/min
1450
1450
1450
Average injection quantity
mm3/st.
82.5
78.5
86.5
Fixing the lever
*
Injection quantity adjustment_05
Adjusting point
C
Rack position
R1-0.45
Pump speed
r/min
500
500
500
Average injection quantity
mm3/st.
54.5
50.5
58.5
Fixing the lever
*
Injection quantity adjustment_06
Adjusting point
I
Rack position
-
Pump speed
r/min
100
100
100
Average injection quantity
mm3/st.
115
115
135
Fixing the lever
*
Rack limit
*
Timer adjustment
Pump speed
r/min
950--
Advance angle
deg.
0
0
0
Remarks
Start
Start
Timer adjustment_02
Pump speed
r/min
900
Advance angle
deg.
0.5
Timer adjustment_03
Pump speed
r/min
-
Advance angle
deg.
1
0.5
1.5
Remarks
Measure the actual speed.
Measure the actual speed.
Timer adjustment_04
Pump speed
r/min
1200
Advance angle
deg.
1
0.5
1.5
Timer adjustment_05
Pump speed
r/min
1450
Advance angle
deg.
7
6.5
7.5
Remarks
Finish
Finish
Test data Ex:
Governor adjustment
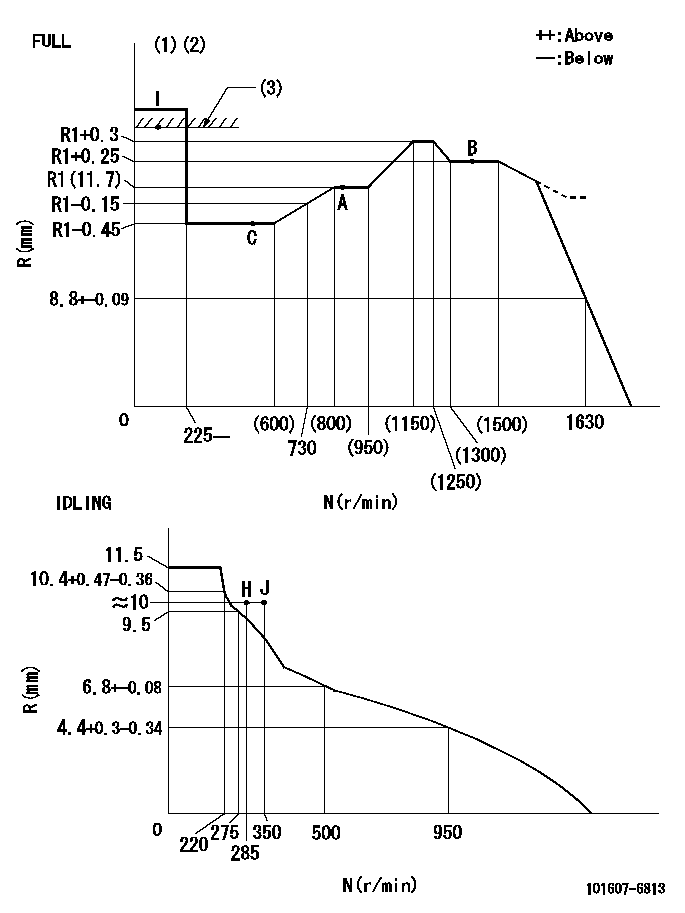
N:Pump speed
R:Rack position (mm)
(1)Torque cam stamping: T1
(2)Tolerance for racks not indicated: +-0.05mm.
(3)RACK LIMIT
----------
T1=J97
----------
----------
T1=J97
----------
Speed control lever angle
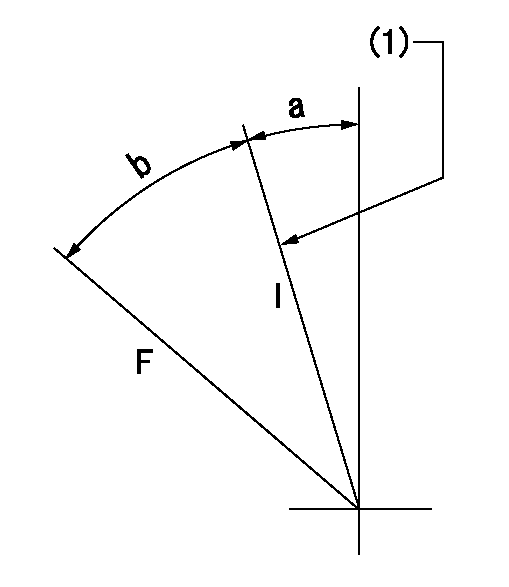
F:Full speed
I:Idle
(1)Stopper bolt set position 'H'
----------
----------
a=26.5deg+-5deg b=(43.5deg)+-3deg
----------
----------
a=26.5deg+-5deg b=(43.5deg)+-3deg
Stop lever angle
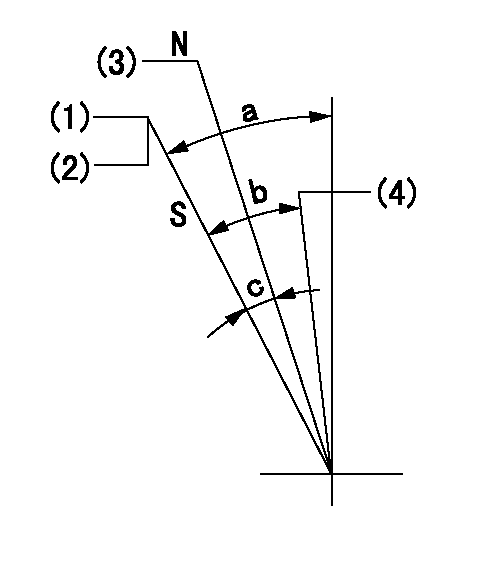
N:Engine manufacturer's normal use
S:Stop the pump.
(1)Set the stopper bolt at pump speed = aa and rack position = bb (non-injection rack position). Confirm non-injection.
(2)After setting the stopper bolt, confirm non-injection at speed cc. Rack position = dd (non-injection rack position).
(3)Rack position = approximately ee (speed lever full, speed = ff).
(4)Free (at delivery)
----------
aa=1450r/min bb=7.2-0.5mm cc=275r/min dd=(8.8)mm ee=15mm ff=0r/min
----------
a=36.5deg+-5deg b=(25deg) c=13deg+-5deg
----------
aa=1450r/min bb=7.2-0.5mm cc=275r/min dd=(8.8)mm ee=15mm ff=0r/min
----------
a=36.5deg+-5deg b=(25deg) c=13deg+-5deg
0000001501 LEVER
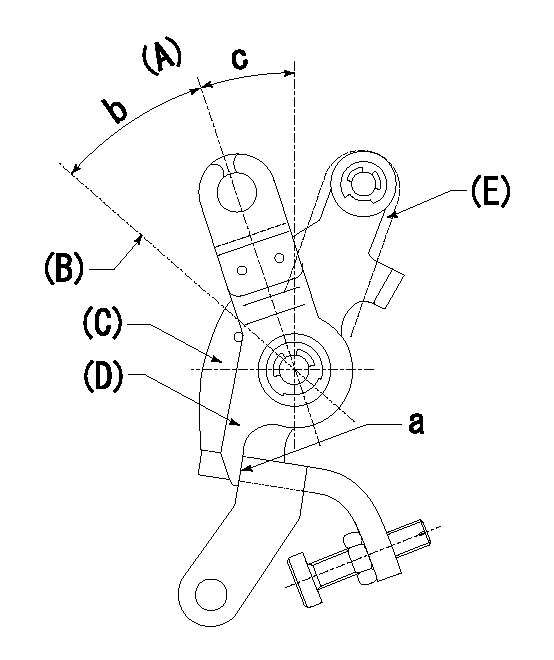
(A) Idle
(B) Full speed
(C) Base lever
(D) Accelerator lever
(E) Accelerator lever delivery position
1. Measure speed lever angle
(1)Measure the angle when the accelerator lever (D) contacted the base lever (C) at a.
----------
----------
b=(43.5deg)+-3deg c=26.5deg+-5deg
----------
----------
b=(43.5deg)+-3deg c=26.5deg+-5deg
Timing setting

(1)Pump vertical direction
(2)Position of timer's tooth at No 1 cylinder's beginning of injection
(3)B.T.D.C.: aa
(4)-
----------
aa=7deg
----------
a=(3deg)
----------
aa=7deg
----------
a=(3deg)
Information:
Illustration 2 g01178323
Proper Installation of Plug
Illustration 3 g01178325
DT Type sealing plugThe 8T-8729 Connector Pin (2) and the 8T-8730 Connector Socket (1) is designed to accept only one 16/18 AWG wire. Do not insert multiple wires of a smaller wire size. An incorrect method would be using two 24 AWG wires. The 9W-0852 Connector Pin and the 9W-0844 Connector Socket is designed to accept only one 14 AWG wire. Do not insert multiple wires of a smaller wire size. An example of an incorrect method is the use of two 20 AWG wires.
CHECK THE CONNECTORS.
Ensure that the connector is properly locked. Also, ensure that the two halves of the connector can not be pulled apart.
Verify that the latch tab of the connector is properly latched. Verify that the latch tab of the connector is fully latched. Expected Result: The connector will securely lock. The connector and the locking mechanism are without cracks or breaks.Results:OK - The connector will securely lock. The connector and the locking mechanism are without cracks or breaks. Proceed to test Step 2. NOT OK - A problem exists with the connector.Repair: Repair the connector or replace the connector, as required.STOP.
CHECK THE ALLEN HEAD SCREW ON THE HARNESS CONNECTOR OF THE ECM.
Ensure that the connector bolt is properly tightened. Be careful not to tighten the bolt too much. The bolt may break.
Do not exceed 6.0 N m (53.0 lb in) of torque on the connector bolt of the harness when the connector is being installed on the ECM. Expected Result: The harness connector is secure and the connector bolt of the ECM is properly torqued.Results:OK - The harness connector is secure and the connector is properly torqued. Proceed to test Step 3.NOT OK - A problem exists with the connector.Repair: Secure the harness connector of the ECM. Ensure that the connector bolt is properly torqued.STOP.
PERFORM A PULL TEST ON EACH CONNECTOR CONTACT.
Each connector contact should withstand 45 N (10 lb) of pull. Each wire should remain in the connector body. This test checks whether the wire was properly crimped in the contact and whether the contact was properly inserted into the connector.
The DT connectors use an orange wedge to lock the terminals in place.
Check in order to ensure that the orange wedge is not missing and that the orange wedge is installed properly on the DT connectors.Note: A Crimp Tool should ALWAYS be used in order to crimp wires on connector contacts. Do not solder the terminals. Use the proper Crimp Tool.Expected Result: Each connector contact should withstand 45 N (10 lb) of pull. Each wire remains in the connector body. Results:OK - Each connector contact withstands 45 N (10 lb) of pull. Each wire remains in the connector body. Proceed to test Step 4.NOT OK - A problem exists with the connector.Repair: Repair the wiring or replace the connector contact.STOP.
CHECK THE WIRES FOR NICKS OR ABRASIONS IN THE INSULATION.
Carefully inspect each wire for signs of abrasion, nicks, or cuts. The following areas are locations
Have questions with 101607-6813?
Group cross 101607-6813 ZEXEL
101607-6813
INJECTION-PUMP ASSEMBLY