Information injection-pump assembly
BOSCH
9 400 615 725
9400615725
ZEXEL
101607-6740
1016076740
MITSUBISHI
ME075526
me075526
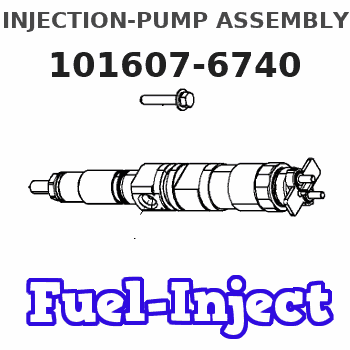
Rating:
Service parts 101607-6740 INJECTION-PUMP ASSEMBLY:
1.
_
6.
COUPLING PLATE
7.
COUPLING PLATE
8.
_
9.
_
11.
Nozzle and Holder
ME076000
12.
Open Pre:MPa(Kqf/cm2)
21.6{220}
15.
NOZZLE SET
Cross reference number
BOSCH
9 400 615 725
9400615725
ZEXEL
101607-6740
1016076740
MITSUBISHI
ME075526
me075526
Zexel num
Bosch num
Firm num
Name
9 400 615 725
ME075526 MITSUBISHI
INJECTION-PUMP ASSEMBLY
6D16 K 14BE INJECTION PUMP ASSY PE6A PE
6D16 K 14BE INJECTION PUMP ASSY PE6A PE
Calibration Data:
Adjustment conditions
Test oil
1404 Test oil ISO4113 or {SAEJ967d}
1404 Test oil ISO4113 or {SAEJ967d}
Test oil temperature
degC
40
40
45
Nozzle and nozzle holder
105780-8140
Bosch type code
EF8511/9A
Nozzle
105780-0000
Bosch type code
DN12SD12T
Nozzle holder
105780-2080
Bosch type code
EF8511/9
Opening pressure
MPa
17.2
Opening pressure
kgf/cm2
175
Injection pipe
Outer diameter - inner diameter - length (mm) mm 6-2-600
Outer diameter - inner diameter - length (mm) mm 6-2-600
Overflow valve
131424-5520
Overflow valve opening pressure
kPa
255
221
289
Overflow valve opening pressure
kgf/cm2
2.6
2.25
2.95
Tester oil delivery pressure
kPa
157
157
157
Tester oil delivery pressure
kgf/cm2
1.6
1.6
1.6
Direction of rotation (viewed from drive side)
Left L
Left L
Injection timing adjustment
Direction of rotation (viewed from drive side)
Left L
Left L
Injection order
1-5-3-6-
2-4
Pre-stroke
mm
3.3
3.25
3.35
Beginning of injection position
Governor side NO.1
Governor side NO.1
Difference between angles 1
Cal 1-5 deg. 60 59.5 60.5
Cal 1-5 deg. 60 59.5 60.5
Difference between angles 2
Cal 1-3 deg. 120 119.5 120.5
Cal 1-3 deg. 120 119.5 120.5
Difference between angles 3
Cal 1-6 deg. 180 179.5 180.5
Cal 1-6 deg. 180 179.5 180.5
Difference between angles 4
Cyl.1-2 deg. 240 239.5 240.5
Cyl.1-2 deg. 240 239.5 240.5
Difference between angles 5
Cal 1-4 deg. 300 299.5 300.5
Cal 1-4 deg. 300 299.5 300.5
Injection quantity adjustment
Adjusting point
-
Rack position
11.2
Pump speed
r/min
700
700
700
Each cylinder's injection qty
mm3/st.
51
49.5
52.5
Basic
*
Fixing the rack
*
Standard for adjustment of the maximum variation between cylinders
*
Injection quantity adjustment_02
Adjusting point
D
Rack position
8.7+-0.5
Pump speed
r/min
500
500
500
Each cylinder's injection qty
mm3/st.
7.6
6.5
8.7
Fixing the rack
*
Standard for adjustment of the maximum variation between cylinders
*
Injection quantity adjustment_03
Adjusting point
A
Rack position
R1(11.2)
Pump speed
r/min
700
700
700
Average injection quantity
mm3/st.
51
50
52
Basic
*
Fixing the lever
*
Injection quantity adjustment_04
Adjusting point
B
Rack position
R1+0.25
Pump speed
r/min
1450
1450
1450
Average injection quantity
mm3/st.
72.6
68.6
76.6
Fixing the lever
*
Injection quantity adjustment_05
Adjusting point
C
Rack position
R1(11.2)
Pump speed
r/min
600
600
600
Average injection quantity
mm3/st.
45
41
49
Fixing the lever
*
Injection quantity adjustment_06
Adjusting point
I
Rack position
14.3+-0.
5
Pump speed
r/min
100
100
100
Average injection quantity
mm3/st.
73
63
83
Fixing the lever
*
Rack limit
*
Injection quantity adjustment_07
Adjusting point
H
Rack position
9.5+-0.5
Pump speed
r/min
275
275
275
Each cylinder's injection qty
mm3/st.
8.7
7.4
10
Fixing the rack
*
Remarks
(check)
(check)
Timer adjustment
Pump speed
r/min
900--
Advance angle
deg.
0
0
0
Remarks
Start
Start
Timer adjustment_02
Pump speed
r/min
850
Advance angle
deg.
0.5
Timer adjustment_03
Pump speed
r/min
1500
Advance angle
deg.
4
3.5
4.5
Remarks
Finish
Finish
Test data Ex:
Governor adjustment
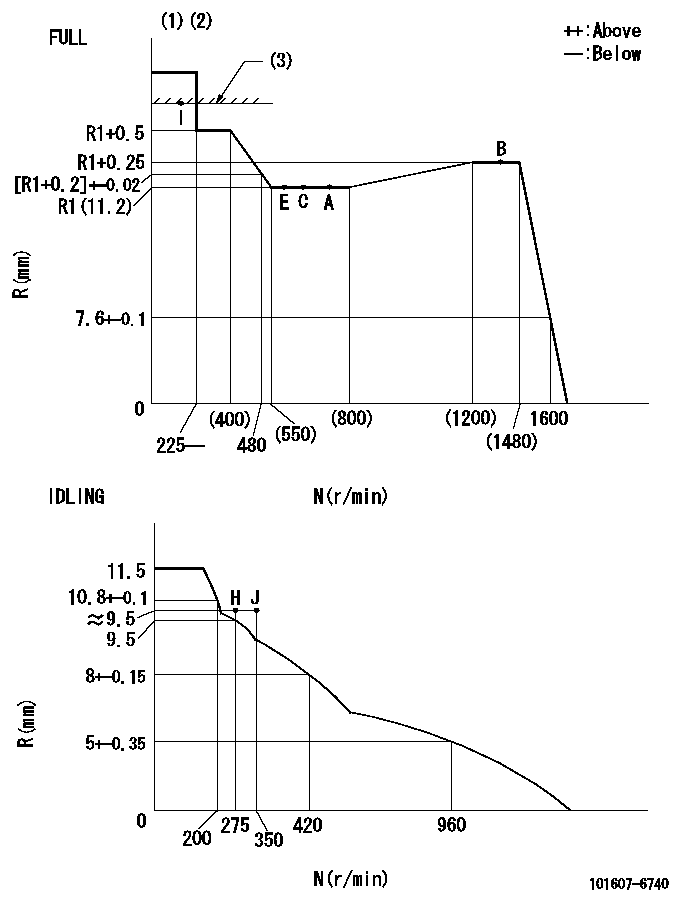
N:Pump speed
R:Rack position (mm)
(1)Torque cam stamping: T1
(2)Tolerance for racks not indicated: +-0.05mm.
(3)RACK LIMIT
----------
T1=D54
----------
----------
T1=D54
----------
Speed control lever angle

F:Full speed
I:Idle
(1)Stopper bolt set position 'H'
----------
----------
a=18.5deg+-5deg b=41deg+-3deg
----------
----------
a=18.5deg+-5deg b=41deg+-3deg
Stop lever angle
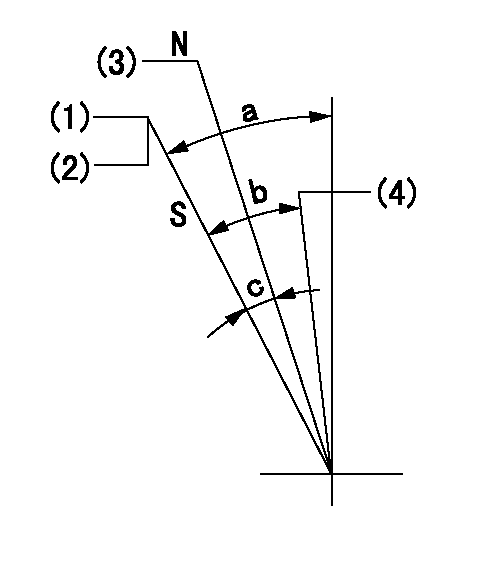
N:Engine manufacturer's normal use
S:Stop the pump.
(1)Set the stopper bolt at pump speed = aa and rack position = bb (non-injection rack position). Confirm non-injection.
(2)After setting the stopper bolt, confirm non-injection at speed cc. Rack position = dd (non-injection rack position).
(3)Rack position = approximately ee (speed lever full, speed = ff).
(4)Free (at delivery)
----------
aa=1450r/min bb=5.4-0.5mm cc=275r/min dd=(7)mm ee=16.2mm ff=0r/min
----------
a=38.5deg+-5deg b=(29deg) c=17deg+-5deg
----------
aa=1450r/min bb=5.4-0.5mm cc=275r/min dd=(7)mm ee=16.2mm ff=0r/min
----------
a=38.5deg+-5deg b=(29deg) c=17deg+-5deg
0000001501 LEVER
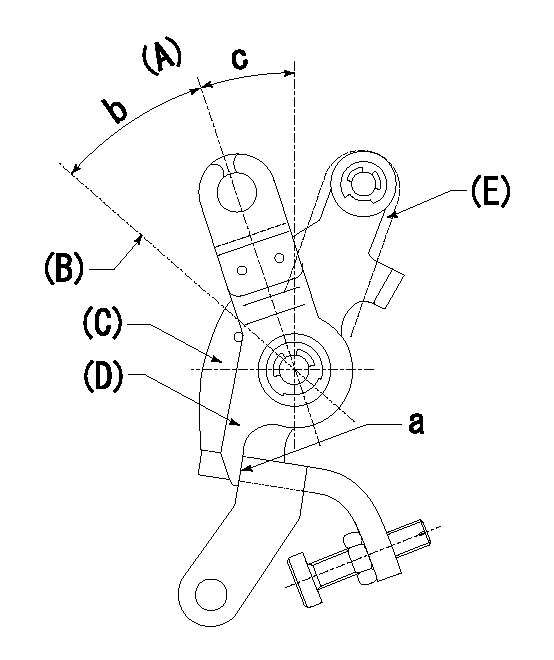
(A) Idle
(B) Full speed
(C) Base lever
(D) Accelerator lever
(E) Accelerator lever delivery position
1. Measure speed lever angle
(1)Measure the angle when the accelerator lever (D) contacted the base lever (C) at a.
----------
----------
b=41deg+-3deg c=18.5deg+-5deg
----------
----------
b=41deg+-3deg c=18.5deg+-5deg
Timing setting

(1)Pump vertical direction
(2)Position of timer's tooth at No 1 cylinder's beginning of injection
(3)B.T.D.C.: aa
(4)-
----------
aa=16deg
----------
a=(1deg)
----------
aa=16deg
----------
a=(1deg)
Information:
Communicating with the Wireless Communication Adapter
Table 23 lists the optional hardware that is needed in order to connect Cat ET by using a wireless connection.
Table 23
Optional Hardware for the Use of Cat ET    
Part Number     Description    
N/A     Personal Computer (PC)    
261-3363 (1)     Wireless Communication Adapter Gp    
( 1 ) Refer to Tool Operating Manual, "Using the 261-3363 Wireless Communication Adapter Gp " for information that is related to the installation and the configuration.
Illustration 81 g01297379
(1) Personal computer (PC) (7) 261-4867 Card (PCMCIA) (8) 239-9955 Communication Radio Gp (9) 259-3183 Data Link Cable As Note: Items (7), (8), and (9) are part of the 261-3363 Wireless Communication Adapter Gp .Use the following procedure in order to connect the wireless communication adapter for use with Cat ET.
Remove the electrical power from the ECM.
Ensure that the computer has been correctly configured for the 261-4867 Card (PCMCIA). Verify that the PC card is installed in the computer PCI expansion slot.
Connect cable (9) between communication radio (8) and the service tool connector.
Restore the electrical power to the ECM. If Cat ET and the communication radio do not communicate with the ECM, refer to troubleshooting without a diagnostic code Troubleshooting, "Electronic Service Tool Will Not Communicate with ECM".Starting System
The EUI system requires that the crankshaft rotate at a minimum of 70 rpm. The engine starting system must be able to supply the air pressure and flow to the starting motor in order to start the engine. The vane type starting motors may be replaced with turbine type starting motors.If the existing starting system does not meet the 70 rpm requirement, the starting motors must be replaced with turbine type starting motors. Refer to Table 24 for a list of part numbers for the recommended turbine type starting motors for 3600 Engines. For a dual starting motor application, two of the motor group part number must be ordered.Air lines to the starting motors must be modified for the turbine starters. A lubricating device is not required for the turbine type starting motors. Any lubricating device must be removed. The air lines for a single starting motor must have a minimum diameter of 38.1 mm (1.5 inch). Air lines for dual starting motors must have a minimum diameter of 76.2 mm (3.0 inch).
Table 24
Turbine Type Starting Motors for 3600 Engine Applications    
Sales Model     Standard Rotation     Reverse Rotation     Quantity    
3606 and 3608     269-3839     275-8518     1    
3612 (1)     295-6006     295-6007    
246-1241 246-4483     2    
3616
( 1 ) 3612 Engines can be started by dual starting motors or by a single starting motor. A single starting motor may only be used in cases when minimal parasitic torque is coupled to the engine during cranking. Dual starters may be required in applications when a 3612 Engine must be started in cold ambient conditions. Cold ambient condition will raise the viscosity of the
Table 23 lists the optional hardware that is needed in order to connect Cat ET by using a wireless connection.
Table 23
Optional Hardware for the Use of Cat ET    
Part Number     Description    
N/A     Personal Computer (PC)    
261-3363 (1)     Wireless Communication Adapter Gp    
( 1 ) Refer to Tool Operating Manual, "Using the 261-3363 Wireless Communication Adapter Gp " for information that is related to the installation and the configuration.
Illustration 81 g01297379
(1) Personal computer (PC) (7) 261-4867 Card (PCMCIA) (8) 239-9955 Communication Radio Gp (9) 259-3183 Data Link Cable As Note: Items (7), (8), and (9) are part of the 261-3363 Wireless Communication Adapter Gp .Use the following procedure in order to connect the wireless communication adapter for use with Cat ET.
Remove the electrical power from the ECM.
Ensure that the computer has been correctly configured for the 261-4867 Card (PCMCIA). Verify that the PC card is installed in the computer PCI expansion slot.
Connect cable (9) between communication radio (8) and the service tool connector.
Restore the electrical power to the ECM. If Cat ET and the communication radio do not communicate with the ECM, refer to troubleshooting without a diagnostic code Troubleshooting, "Electronic Service Tool Will Not Communicate with ECM".Starting System
The EUI system requires that the crankshaft rotate at a minimum of 70 rpm. The engine starting system must be able to supply the air pressure and flow to the starting motor in order to start the engine. The vane type starting motors may be replaced with turbine type starting motors.If the existing starting system does not meet the 70 rpm requirement, the starting motors must be replaced with turbine type starting motors. Refer to Table 24 for a list of part numbers for the recommended turbine type starting motors for 3600 Engines. For a dual starting motor application, two of the motor group part number must be ordered.Air lines to the starting motors must be modified for the turbine starters. A lubricating device is not required for the turbine type starting motors. Any lubricating device must be removed. The air lines for a single starting motor must have a minimum diameter of 38.1 mm (1.5 inch). Air lines for dual starting motors must have a minimum diameter of 76.2 mm (3.0 inch).
Table 24
Turbine Type Starting Motors for 3600 Engine Applications    
Sales Model     Standard Rotation     Reverse Rotation     Quantity    
3606 and 3608     269-3839     275-8518     1    
3612 (1)     295-6006     295-6007    
246-1241 246-4483     2    
3616
( 1 ) 3612 Engines can be started by dual starting motors or by a single starting motor. A single starting motor may only be used in cases when minimal parasitic torque is coupled to the engine during cranking. Dual starters may be required in applications when a 3612 Engine must be started in cold ambient conditions. Cold ambient condition will raise the viscosity of the