Information injection-pump assembly
ZEXEL
101607-6721
1016076721
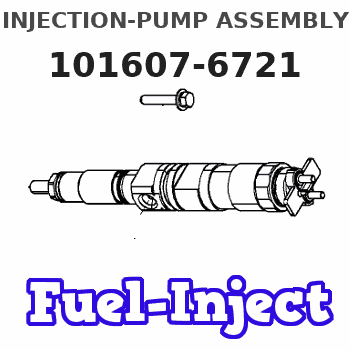
Rating:
Cross reference number
ZEXEL
101607-6721
1016076721
Zexel num
Bosch num
Firm num
Name
101607-6721
INJECTION-PUMP ASSEMBLY
Calibration Data:
Adjustment conditions
Test oil
1404 Test oil ISO4113 or {SAEJ967d}
1404 Test oil ISO4113 or {SAEJ967d}
Test oil temperature
degC
40
40
45
Nozzle and nozzle holder
105780-8140
Bosch type code
EF8511/9A
Nozzle
105780-0000
Bosch type code
DN12SD12T
Nozzle holder
105780-2080
Bosch type code
EF8511/9
Opening pressure
MPa
17.2
Opening pressure
kgf/cm2
175
Injection pipe
Outer diameter - inner diameter - length (mm) mm 6-2-600
Outer diameter - inner diameter - length (mm) mm 6-2-600
Overflow valve
131424-1520
Overflow valve opening pressure
kPa
157
123
191
Overflow valve opening pressure
kgf/cm2
1.6
1.25
1.95
Tester oil delivery pressure
kPa
157
157
157
Tester oil delivery pressure
kgf/cm2
1.6
1.6
1.6
RED3 control unit part number
407910-2
470
RED3 rack sensor specifications
mm
15
Direction of rotation (viewed from drive side)
Left L
Left L
Injection timing adjustment
Direction of rotation (viewed from drive side)
Left L
Left L
Injection order
1-5-3-6-
2-4
Pre-stroke
mm
3.2
3.15
3.25
Beginning of injection position
Governor side NO.1
Governor side NO.1
Difference between angles 1
Cal 1-5 deg. 60 59.5 60.5
Cal 1-5 deg. 60 59.5 60.5
Difference between angles 2
Cal 1-3 deg. 120 119.5 120.5
Cal 1-3 deg. 120 119.5 120.5
Difference between angles 3
Cal 1-6 deg. 180 179.5 180.5
Cal 1-6 deg. 180 179.5 180.5
Difference between angles 4
Cyl.1-2 deg. 240 239.5 240.5
Cyl.1-2 deg. 240 239.5 240.5
Difference between angles 5
Cal 1-4 deg. 300 299.5 300.5
Cal 1-4 deg. 300 299.5 300.5
Injection quantity adjustment
Rack position
(8.9)
Vist
V
2.22
2.22
2.22
Pump speed
r/min
850
850
850
Average injection quantity
mm3/st.
86.5
85.5
87.5
Max. variation between cylinders
%
0
-3
3
Basic
*
Injection quantity adjustment_02
Rack position
(6.5)
Vist
V
2.7
2.6
2.8
Pump speed
r/min
600
600
600
Average injection quantity
mm3/st.
10.8
9.2
12.4
Max. variation between cylinders
%
0
-15
15
Governor adjustment
Pump speed
r/min
-
Advance angle
deg.
0
0
0
Remarks
Measure speed (beginning of operation).
Measure speed (beginning of operation).
Governor adjustment_02
Pump speed
r/min
-
Advance angle
deg.
1
0.5
1.5
Remarks
Measure the actual speed.
Measure the actual speed.
Governor adjustment_03
Pump speed
r/min
-
Advance angle
deg.
1
0.5
1.5
Remarks
Measure the actual speed.
Measure the actual speed.
Governor adjustment_04
Pump speed
r/min
-
Advance angle
deg.
7
6.5
7.5
Remarks
Measure the actual speed, stop
Measure the actual speed, stop
Test data Ex:
Speed control lever angle

N:Pump normal
S:Stop the pump.
(1)Rack position = aa
(2)Rack position bb
----------
aa=1mm bb=16mm
----------
a=31deg+-5deg b=29deg+-5deg
----------
aa=1mm bb=16mm
----------
a=31deg+-5deg b=29deg+-5deg
0000000901

(1)Pump vertical direction
(2)Position of timer's tooth at No 1 cylinder's beginning of injection
(3)B.T.D.C.: aa
(4)-
----------
aa=7deg
----------
a=(4deg)
----------
aa=7deg
----------
a=(4deg)
Stop lever angle

(Rs) rack sensor specifications
(C/U) control unit part number
(V) Rack sensor output voltage
(R) Rack position (mm)
1. Confirming governor output characteristics (rack 15 mm, span 6 mm)
(1)When the output voltages of the rack sensor are V1 and V2, check that the rack positions R1 and R2 in the table above are satisfied.
----------
----------
----------
----------
Information:
Introduction
Do not perform any procedure in this Special Instruction until you have read the information and you understand the information.The actuator and pump groups of these fuel injectors are sensitive to debris in the oil. The injector may malfunction due to debris in the oil, causing seizure, or high leaks in components.
Table 1
Revision Table
Revision Summary of Changes
3 Added serial numbers. Improvement Procedure
Clean oil rail after pump failure.Reference: Refer to Special Instruction, REHS3819 for the procedure to clean the oil rail after engine failure to avoid debris in the oil system.
Use clean oil and clean filters.The life of the injector depends on the oil quality. It can be increased if good cleaning practices are performed before installing the injectors.Reference: Refer to Operation and Maintenance Manual, SEBU6250 and Operation and Maintenance Manual, SEBU6251 for direction on oil sampling intervals and optimizing engine oil life.
Illustration 1 g06207717
(1) Actuator
(2) Pump Group
(3) Valve Seat Damage Due to Debris in the Oil SystemInjector Failure Due To Damage From Debris In The Oil May Not Be A Warrantable Failure
Illustration 2 g06244961
Do not perform any procedure in this Special Instruction until you have read the information and you understand the information.The actuator and pump groups of these fuel injectors are sensitive to debris in the oil. The injector may malfunction due to debris in the oil, causing seizure, or high leaks in components.
Table 1
Revision Table
Revision Summary of Changes
3 Added serial numbers. Improvement Procedure
Clean oil rail after pump failure.Reference: Refer to Special Instruction, REHS3819 for the procedure to clean the oil rail after engine failure to avoid debris in the oil system.
Use clean oil and clean filters.The life of the injector depends on the oil quality. It can be increased if good cleaning practices are performed before installing the injectors.Reference: Refer to Operation and Maintenance Manual, SEBU6250 and Operation and Maintenance Manual, SEBU6251 for direction on oil sampling intervals and optimizing engine oil life.
Illustration 1 g06207717
(1) Actuator
(2) Pump Group
(3) Valve Seat Damage Due to Debris in the Oil SystemInjector Failure Due To Damage From Debris In The Oil May Not Be A Warrantable Failure
Illustration 2 g06244961
Have questions with 101607-6721?
Group cross 101607-6721 ZEXEL
Mitsubishi
Mitsubishi
101607-6721
INJECTION-PUMP ASSEMBLY