Information injection-pump assembly
ZEXEL
101607-6691
1016076691
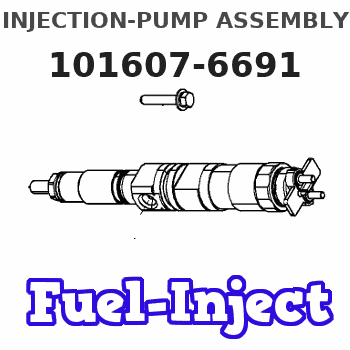
Rating:
Cross reference number
ZEXEL
101607-6691
1016076691
Zexel num
Bosch num
Firm num
Name
101607-6691
INJECTION-PUMP ASSEMBLY
Calibration Data:
Adjustment conditions
Test oil
1404 Test oil ISO4113 or {SAEJ967d}
1404 Test oil ISO4113 or {SAEJ967d}
Test oil temperature
degC
40
40
45
Nozzle and nozzle holder
105780-8140
Bosch type code
EF8511/9A
Nozzle
105780-0000
Bosch type code
DN12SD12T
Nozzle holder
105780-2080
Bosch type code
EF8511/9
Opening pressure
MPa
17.2
Opening pressure
kgf/cm2
175
Injection pipe
Outer diameter - inner diameter - length (mm) mm 6-2-600
Outer diameter - inner diameter - length (mm) mm 6-2-600
Overflow valve
131424-8420
Overflow valve opening pressure
kPa
255
221
289
Overflow valve opening pressure
kgf/cm2
2.6
2.25
2.95
Tester oil delivery pressure
kPa
157
157
157
Tester oil delivery pressure
kgf/cm2
1.6
1.6
1.6
Direction of rotation (viewed from drive side)
Left L
Left L
Injection timing adjustment
Direction of rotation (viewed from drive side)
Left L
Left L
Injection order
1-5-3-6-
2-4
Pre-stroke
mm
3.2
3.15
3.25
Beginning of injection position
Governor side NO.1
Governor side NO.1
Difference between angles 1
Cal 1-5 deg. 60 59.5 60.5
Cal 1-5 deg. 60 59.5 60.5
Difference between angles 2
Cal 1-3 deg. 120 119.5 120.5
Cal 1-3 deg. 120 119.5 120.5
Difference between angles 3
Cal 1-6 deg. 180 179.5 180.5
Cal 1-6 deg. 180 179.5 180.5
Difference between angles 4
Cyl.1-2 deg. 240 239.5 240.5
Cyl.1-2 deg. 240 239.5 240.5
Difference between angles 5
Cal 1-4 deg. 300 299.5 300.5
Cal 1-4 deg. 300 299.5 300.5
Injection quantity adjustment
Adjusting point
-
Rack position
11.5
Pump speed
r/min
850
850
850
Each cylinder's injection qty
mm3/st.
73
70.8
75.2
Basic
*
Fixing the rack
*
Standard for adjustment of the maximum variation between cylinders
*
Injection quantity adjustment_02
Adjusting point
Z
Rack position
9.5+-0.5
Pump speed
r/min
800
800
800
Each cylinder's injection qty
mm3/st.
10.8
9.2
12.4
Fixing the rack
*
Standard for adjustment of the maximum variation between cylinders
*
Injection quantity adjustment_03
Adjusting point
A
Rack position
R1(11.5)
Pump speed
r/min
850
850
850
Average injection quantity
mm3/st.
73
72
74
Basic
*
Fixing the lever
*
Injection quantity adjustment_04
Adjusting point
B
Rack position
R1+0.25
Pump speed
r/min
1450
1450
1450
Average injection quantity
mm3/st.
81
77
85
Fixing the lever
*
Injection quantity adjustment_05
Adjusting point
C
Rack position
R1-0.35
Pump speed
r/min
500
500
500
Average injection quantity
mm3/st.
49.7
45.7
53.7
Fixing the lever
*
Injection quantity adjustment_06
Adjusting point
I
Rack position
-
Pump speed
r/min
100
100
100
Average injection quantity
mm3/st.
115
115
135
Fixing the lever
*
Rack limit
*
Timer adjustment
Pump speed
r/min
950--
Advance angle
deg.
0
0
0
Remarks
Start
Start
Timer adjustment_02
Pump speed
r/min
900
Advance angle
deg.
0.5
Timer adjustment_03
Pump speed
r/min
-
Advance angle
deg.
1
0.5
1.5
Remarks
Measure the actual speed.
Measure the actual speed.
Timer adjustment_04
Pump speed
r/min
1200
Advance angle
deg.
1
0.5
1.5
Timer adjustment_05
Pump speed
r/min
1450
Advance angle
deg.
7
6.5
7.5
Remarks
Finish
Finish
Test data Ex:
Governor adjustment
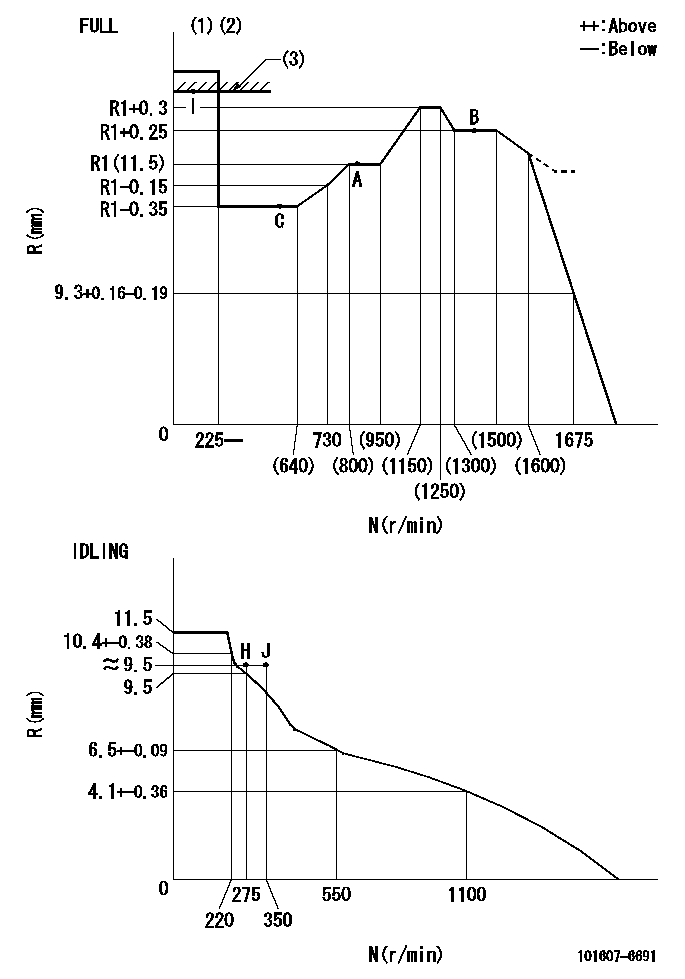
N:Pump speed
R:Rack position (mm)
(1)Torque cam stamping: T1
(2)Tolerance for racks not indicated: +-0.05mm.
(3)RACK LIMIT
----------
T1=J61
----------
----------
T1=J61
----------
Speed control lever angle

F:Full speed
I:Idle
(1)Stopper bolt set position 'H'
----------
----------
a=18.5deg+-5deg b=42deg+-3deg
----------
----------
a=18.5deg+-5deg b=42deg+-3deg
Stop lever angle
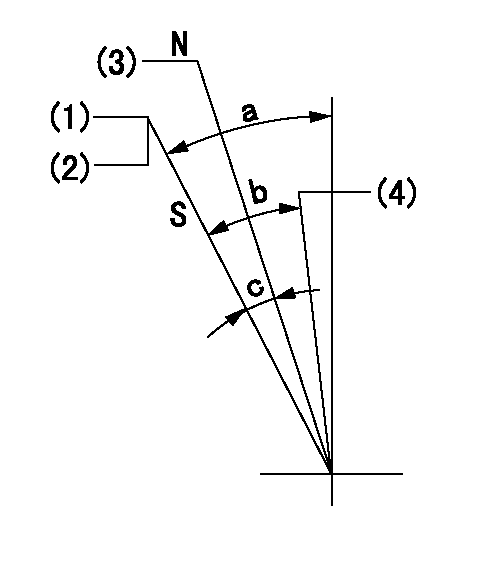
N:Engine manufacturer's normal use
S:Stop the pump.
(1)Set the stopper bolt at pump speed = aa and rack position = bb (non-injection rack position). Confirm non-injection.
(2)After setting the stopper bolt, confirm non-injection at speed cc. Rack position = dd (non-injection rack position).
(3)Rack position = approximately ee.
(4)Free (at delivery)
----------
aa=1450r/min bb=7.2-0.5mm cc=275r/min dd=(8.8)mm ee=15mm
----------
a=36.5deg+-5deg b=(25deg) c=13deg+-5deg
----------
aa=1450r/min bb=7.2-0.5mm cc=275r/min dd=(8.8)mm ee=15mm
----------
a=36.5deg+-5deg b=(25deg) c=13deg+-5deg
0000001501 LEVER
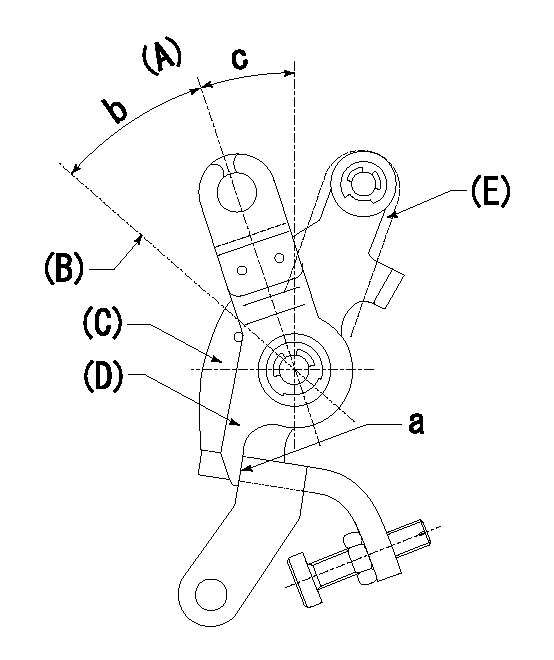
(A) Idle
(B) Full speed
(C) Base lever
(D) Accelerator lever
(E) Accelerator lever delivery position
1. Measure speed lever angle
(1)Measure the angle when the accelerator lever (D) contacted the base lever (C) at a.
----------
----------
b=42deg+-3deg c=18.5deg+-5deg
----------
----------
b=42deg+-3deg c=18.5deg+-5deg
0000001601 RACK SENSOR

V1:Supply voltage
V2f:Full side output voltage
V2i:Idle side output voltage
(A) Black
(B) Yellow
(C) Red
(D) Trimmer
(E): Shaft
(F) Nut
(G) Load lever
1. Load sensor adjustment
(1)Connect as shown in the above diagram and apply supply voltage V1.
(2)Hold the load lever (G) against the full side.
(3)Turn the shaft so that the voltage between (A) and (B) is V2.
(4)Hold the load lever (G) against the idle side.
(5)Adjust (D) so that the voltage between (A) and (B) is V2i.
(6)Repeat the above adjustments.
(7)Tighten the nut (F) at the point satisfying the standards.
(8)Hold the load lever against the full side stopper and the idle side stopper.
(9)At this time, confirm that the full side output voltage is V2f and the idle side output voltage is V2i.
----------
V1=3.57+-0.02V V2f=3+0.05V V2i=1+0.1V
----------
----------
V1=3.57+-0.02V V2f=3+0.05V V2i=1+0.1V
----------
0000001701 MICRO SWITCH
Adjust the bolt to obtain the following lever position when the micro-switch is ON.
1. Microswitch adjustment (OPEN type)
Confirm with the lever angle at full.
(1)Speed N1
(2)Rack position Ra
2. Idle side microswitch adjustment (OPEN type)
Confirm with the lever angle at idle.
(1)Speed N2
(2)Rack position Rb
----------
N1=1675r/min Ra=8.5+-0.1mm N2=275r/min Rb=9.7+-0.1mm
----------
----------
N1=1675r/min Ra=8.5+-0.1mm N2=275r/min Rb=9.7+-0.1mm
----------
Timing setting

(1)Pump vertical direction
(2)Position of timer's tooth at No 1 cylinder's beginning of injection
(3)B.T.D.C.: aa
(4)-
----------
aa=8.5deg
----------
a=(3deg)
----------
aa=8.5deg
----------
a=(3deg)
Information:
Introduction
The following Special Instruction must be used to package a DPF for a core return.
Wear goggles, gloves, protective clothing, and a National Institute for Occupational Safety and Health (NIOSH) approved P95 or N95 half-face respirator when handling a used Diesel Particulate Filter or Catalytic Converter Muffler. Failure to do so could result in personal injury.
Note: Whenever the filter is replaced the engine ash model must be reset. Refer to the section below for information on how to reset the ash model.Reset the Engine Ash Model
The engine ash model must be reset whenever the filter is cleaned or replaced. Reseting the ash model places the DPF volume back to the "Clean State". The resetting will allow the regeneration of the DPF to function properly.
Use Cat ET to access the configuration parameters. Select "Service" from the top menu then select "Service Procedures" then select "DPF Ash Service" from the menu in the service tool.
Choose the correct replacement type of diesel particulate filter in the menu that appears. The types of replacements for the diesel particulate filter are the following:
"Field cleaned" A DPF that has been cleaned and reapplied.
"New" A new DPF replacement.
"Remanufactured" A remanufactured DPF replacement.
Once the reset is completed, a log of the reset is captured and visible as a new row of information in the "DPF Ash Service" screen. Resetting the engine ash model does not reset the soot level.
Perform a "Manual DPF Regeneration" with Cat® ET to reset the soot levelPackaging Instructions
Note: The replacement DPF will be packaged with a bag and zip-tie that are used to repackage the DPF that has been removed.
Place the DPF being returned in the enclosed bag and seal the bag with the enclosed zip-tie.
Place the enclosed warning label on the outside of the bag.
Place half of the foam insert on the bottom of the original shipping box with the cut out in the insert facing up.
Place the DPF into the box fitting the DPF into the cut out in the insert.
Place the second half of the foam insert on to of the DPF with the cut out in the insert facing down onto the DPF.
Seal the box with packing tape.Note: If the package weighs over 16 kg (35 lb), additional tape or banding might be required.
Label the package for return shipment.
The following Special Instruction must be used to package a DPF for a core return.
Wear goggles, gloves, protective clothing, and a National Institute for Occupational Safety and Health (NIOSH) approved P95 or N95 half-face respirator when handling a used Diesel Particulate Filter or Catalytic Converter Muffler. Failure to do so could result in personal injury.
Note: Whenever the filter is replaced the engine ash model must be reset. Refer to the section below for information on how to reset the ash model.Reset the Engine Ash Model
The engine ash model must be reset whenever the filter is cleaned or replaced. Reseting the ash model places the DPF volume back to the "Clean State". The resetting will allow the regeneration of the DPF to function properly.
Use Cat ET to access the configuration parameters. Select "Service" from the top menu then select "Service Procedures" then select "DPF Ash Service" from the menu in the service tool.
Choose the correct replacement type of diesel particulate filter in the menu that appears. The types of replacements for the diesel particulate filter are the following:
"Field cleaned" A DPF that has been cleaned and reapplied.
"New" A new DPF replacement.
"Remanufactured" A remanufactured DPF replacement.
Once the reset is completed, a log of the reset is captured and visible as a new row of information in the "DPF Ash Service" screen. Resetting the engine ash model does not reset the soot level.
Perform a "Manual DPF Regeneration" with Cat® ET to reset the soot levelPackaging Instructions
Note: The replacement DPF will be packaged with a bag and zip-tie that are used to repackage the DPF that has been removed.
Place the DPF being returned in the enclosed bag and seal the bag with the enclosed zip-tie.
Place the enclosed warning label on the outside of the bag.
Place half of the foam insert on the bottom of the original shipping box with the cut out in the insert facing up.
Place the DPF into the box fitting the DPF into the cut out in the insert.
Place the second half of the foam insert on to of the DPF with the cut out in the insert facing down onto the DPF.
Seal the box with packing tape.Note: If the package weighs over 16 kg (35 lb), additional tape or banding might be required.
Label the package for return shipment.
Have questions with 101607-6691?
Group cross 101607-6691 ZEXEL
101607-6691
INJECTION-PUMP ASSEMBLY