Information injection-pump assembly
BOSCH
9 400 615 721
9400615721
ZEXEL
101607-6681
1016076681
MITSUBISHI
ME075477
me075477
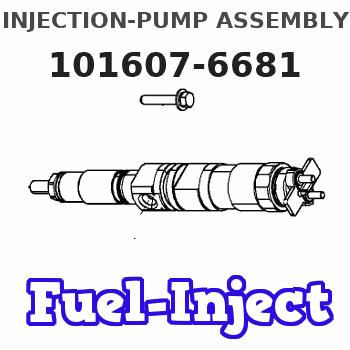
Rating:
Include in #1:
101492-4050
as _
Cross reference number
BOSCH
9 400 615 721
9400615721
ZEXEL
101607-6681
1016076681
MITSUBISHI
ME075477
me075477
Zexel num
Bosch num
Firm num
Name
101607-6681
9 400 615 721
ME075477 MITSUBISHI
INJECTION-PUMP ASSEMBLY
6D17 K
6D17 K
Calibration Data:
Adjustment conditions
Test oil
1404 Test oil ISO4113 or {SAEJ967d}
1404 Test oil ISO4113 or {SAEJ967d}
Test oil temperature
degC
40
40
45
Nozzle and nozzle holder
105780-8140
Bosch type code
EF8511/9A
Nozzle
105780-0000
Bosch type code
DN12SD12T
Nozzle holder
105780-2080
Bosch type code
EF8511/9
Opening pressure
MPa
17.2
Opening pressure
kgf/cm2
175
Injection pipe
Outer diameter - inner diameter - length (mm) mm 6-2-600
Outer diameter - inner diameter - length (mm) mm 6-2-600
Overflow valve
131424-8420
Overflow valve opening pressure
kPa
255
221
289
Overflow valve opening pressure
kgf/cm2
2.6
2.25
2.95
Tester oil delivery pressure
kPa
157
157
157
Tester oil delivery pressure
kgf/cm2
1.6
1.6
1.6
Direction of rotation (viewed from drive side)
Left L
Left L
Injection timing adjustment
Direction of rotation (viewed from drive side)
Left L
Left L
Injection order
1-5-3-6-
2-4
Pre-stroke
mm
3.2
3.15
3.25
Beginning of injection position
Governor side NO.1
Governor side NO.1
Difference between angles 1
Cal 1-5 deg. 60 59.5 60.5
Cal 1-5 deg. 60 59.5 60.5
Difference between angles 2
Cal 1-3 deg. 120 119.5 120.5
Cal 1-3 deg. 120 119.5 120.5
Difference between angles 3
Cal 1-6 deg. 180 179.5 180.5
Cal 1-6 deg. 180 179.5 180.5
Difference between angles 4
Cyl.1-2 deg. 240 239.5 240.5
Cyl.1-2 deg. 240 239.5 240.5
Difference between angles 5
Cal 1-4 deg. 300 299.5 300.5
Cal 1-4 deg. 300 299.5 300.5
Injection quantity adjustment
Adjusting point
-
Rack position
12
Pump speed
r/min
850
850
850
Each cylinder's injection qty
mm3/st.
85.1
82.5
87.7
Basic
*
Fixing the rack
*
Standard for adjustment of the maximum variation between cylinders
*
Injection quantity adjustment_02
Adjusting point
Z
Rack position
9.5+-0.5
Pump speed
r/min
800
800
800
Each cylinder's injection qty
mm3/st.
10.8
9.2
12.4
Fixing the rack
*
Standard for adjustment of the maximum variation between cylinders
*
Injection quantity adjustment_03
Adjusting point
A
Rack position
R1(12)
Pump speed
r/min
850
850
850
Average injection quantity
mm3/st.
85.1
84.1
86.1
Basic
*
Fixing the lever
*
Injection quantity adjustment_04
Adjusting point
B
Rack position
R1+0.85
Pump speed
r/min
1450
1450
1450
Average injection quantity
mm3/st.
99.9
95.9
103.9
Fixing the lever
*
Injection quantity adjustment_05
Adjusting point
I
Rack position
-
Pump speed
r/min
100
100
100
Average injection quantity
mm3/st.
91
81
101
Fixing the lever
*
Rack limit
*
Timer adjustment
Pump speed
r/min
1100
Advance angle
deg.
0.5
Timer adjustment_02
Pump speed
r/min
1300
Advance angle
deg.
2.5
2.5
3.5
Timer adjustment_03
Pump speed
r/min
1450
Advance angle
deg.
6
5.5
6.5
Remarks
Finish
Finish
Test data Ex:
Governor adjustment
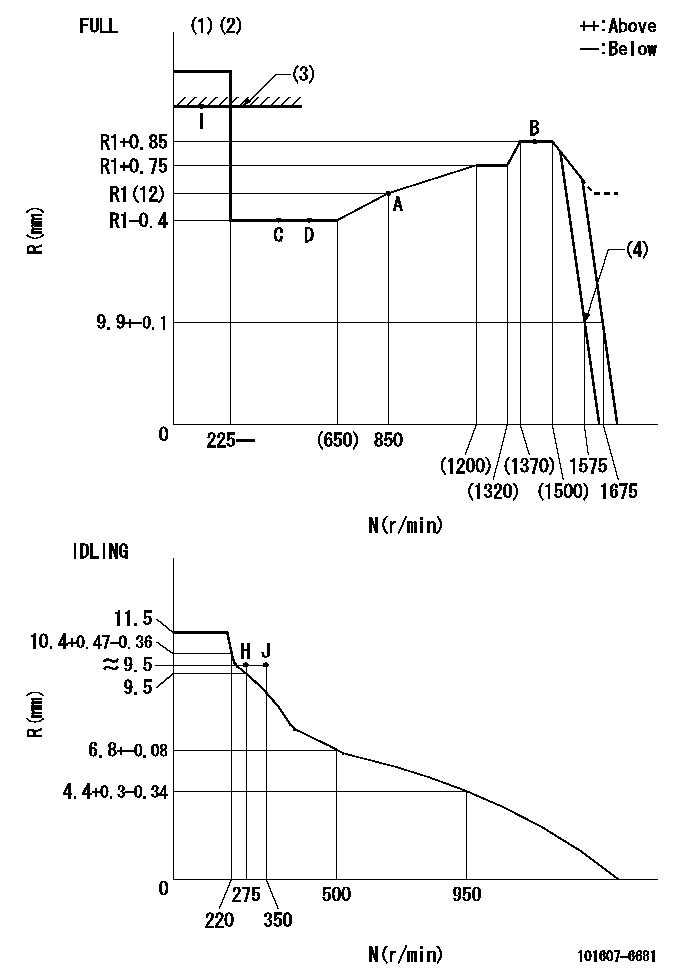
N:Pump speed
R:Rack position (mm)
(1)Torque cam stamping: T1
(2)Tolerance for racks not indicated: +-0.05mm.
(3)RACK LIMIT
(4)Set using the changeover lever.
----------
T1=H28
----------
----------
T1=H28
----------
Speed control lever angle
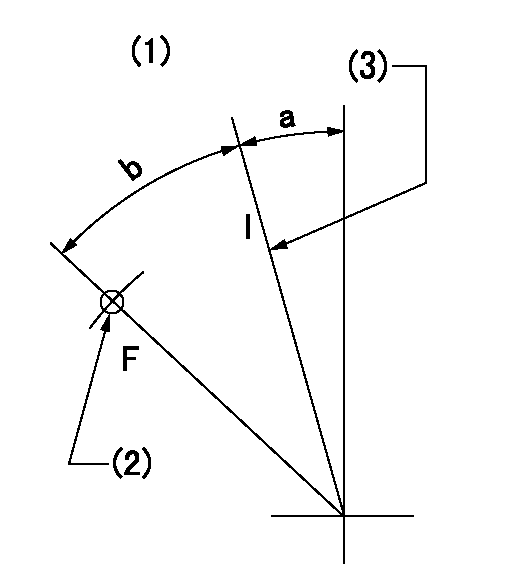
F:Full speed
I:Idle
(1)Accelerator lever
(2)Use the hole at R = aa
(3)Stopper bolt set position 'H'
----------
aa=29mm
----------
a=10deg+-5deg b=(47.5deg)+-3deg
----------
aa=29mm
----------
a=10deg+-5deg b=(47.5deg)+-3deg
Stop lever angle
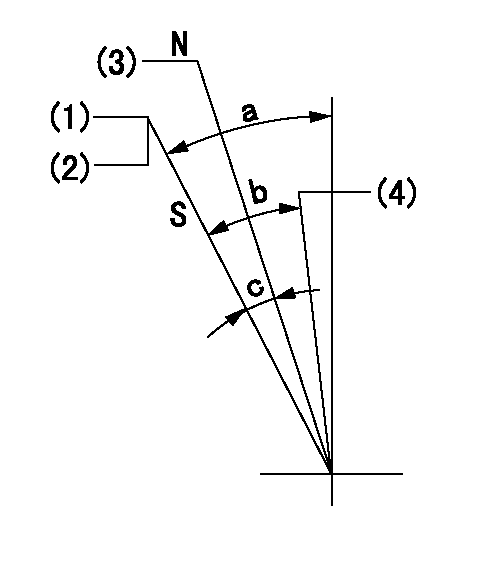
N:Engine manufacturer's normal use
S:Stop the pump.
(1)Set the stopper bolt at pump speed = aa and rack position = bb (non-injection rack position). Confirm non-injection.
(2)After setting the stopper bolt, confirm non-injection at speed cc. Rack position = dd (non-injection rack position).
(3)Rack position = approximately ee.
(4)Free (at delivery)
----------
aa=1450r/min bb=7.2-0.5mm cc=275r/min dd=(8.8)mm ee=15mm
----------
a=36.5deg+-5deg b=(25deg) c=13deg+-5deg
----------
aa=1450r/min bb=7.2-0.5mm cc=275r/min dd=(8.8)mm ee=15mm
----------
a=36.5deg+-5deg b=(25deg) c=13deg+-5deg
0000001201

F:At operation, hold it in the full speed position.
I:Idle
(1)At rack position aa and pump speed bb, set the stopper bolt. (After setting it, apply red paint.)
(2)Actual measurement
----------
aa=9.9+-0.1mm bb=1575r/min
----------
a=15deg+-5deg
----------
aa=9.9+-0.1mm bb=1575r/min
----------
a=15deg+-5deg
0000001501 RACK SENSOR

V1:Supply voltage
V2f:Full side output voltage
V2i:Idle side output voltage
(A) Black
(B) Yellow
(C) Red
(D) Trimmer
(E): Shaft
(F) Nut
(G) Load lever
1. Load sensor adjustment
(1)Connect as shown in the above diagram and apply supply voltage V1.
(2)Hold the load lever (G) against the full side.
(3)Turn the shaft so that the voltage between (A) and (B) is V2.
(4)Hold the load lever (G) against the idle side.
(5)Adjust (D) so that the voltage between (A) and (B) is V2i.
(6)Repeat the above adjustments.
(7)Tighten the nut (F) at the point satisfying the standards.
(8)Hold the load lever against the full side stopper and the idle side stopper.
(9)At this time, confirm that the full side output voltage is V2f and the idle side output voltage is V2i.
----------
V1=3.57+-0.02V V2f=3+0.05V V2i=1+0.1V
----------
----------
V1=3.57+-0.02V V2f=3+0.05V V2i=1+0.1V
----------
0000001601 MICRO SWITCH
Adjustment of the micro-switch
Adjust the bolt to obtain the following lever position when the micro-switch is ON.
(1)Speed N1
(2)Rack position Ra
----------
N1=1675r/min Ra=9.9+-0.1mm
----------
----------
N1=1675r/min Ra=9.9+-0.1mm
----------
Timing setting

(1)Pump vertical direction
(2)Position of timer's tooth at No 1 cylinder's beginning of injection
(3)B.T.D.C.: aa
(4)-
----------
aa=10deg
----------
a=(2deg)
----------
aa=10deg
----------
a=(2deg)
Information:
Table 1
S O S Oil Sampling Interval for Engine crankcase
Recommended Interval (1)(2) Oil Type
Every 250 Service Hours Cat DEO
Cat DEO-ULS
(1) Severe applications may require a more frequent oil sampling interval.
(2) Under certain conditions, the Cat dealer or the Operation and Maintenance Manual may allow a longer interval between oil samplings.Note: Refer to the Operation and Maintenance Manual for your engine for recommended oil drain intervals.Consult your Cat dealer for complete information and assistance in order to establish an S O S Services program for your engine.More Frequent S O S Sampling Improves Life Cycle Management
Traditionally, the suggested S O S sampling intervals for diesel engines have been at 250 hours. However in severe applications, more frequent oil sampling is recommended. Severe service for lubricated compartments occurs at high loads, in high temperatures, and in dusty conditions. If any of these conditions or other severe service indicators exist, sample the engine oil at 125 hour intervals. These additional samples will increase the chance of detecting a potential failure.Determining Optimum Oil Change Intervals
Sampling the engine oil at every 125 hours provides information for oil condition and for oil performance. This information is used to determine the optimum usable life of a particular oil. Also, more points of data will allow closer monitoring of component wear rates. Close monitoring also allows you to obtain the maximum use of the oil. For detailed information on optimizing oil change intervals, consult your Cat dealer.This Special Publication does not address recommended oil drain intervals. Refer to your engine Operation and Maintenance Manual, and consult your Cat dealer for additional guidance, including but not limited to guidance on establishing optimized and/or acceptable oil drain intervals.To reduce the potential risk of failures associated with extended oil drain periods, Caterpillar recommends that oil drain intervals only be extended based on oil analysis, and subsequent system inspections. Oil analysis alone does not provide an indication of the rate of formation of lacquer, varnish and/or other deposits on surfaces. The only accurate way to evaluate specific oil performance in a specific system using extended oil drain periods is to observe the effects on the system components. Making these observations involves tear-down inspections of systems that have run to the normal overhaul period while using extended oil drain intervals. Following this recommendation will help ensure that excessive component wear does not take place in a given application.Note: The use of Cat S O S Services oil analysis helps environmental sustainability as the best way to optimize oil life. S O S Services will help engines reach expected life. Consult your Cat dealer regarding the testing required to establish a safe, optimized oil drain interval.Standard oil drain intervals as published in engine Operation and Maintenance Manual are for typical applications:
Using recommended oils
Using good fuel
Using recommended filters
Using industry standard good maintenance practices
Following maintenance intervals as published in engine Operation and Maintenance ManualMore severe applications may require shortened oil drain intervals, while less severe applications may allow for longer than standard oil drain intervals. High
Have questions with 101607-6681?
Group cross 101607-6681 ZEXEL
Mitsubishi
Mitsubishi
Mitsubishi
Mitsubishi
Mitsubishi
101607-6681
9 400 615 721
ME075477
INJECTION-PUMP ASSEMBLY
6D17
6D17