Information injection-pump assembly
ZEXEL
101607-6620
1016076620
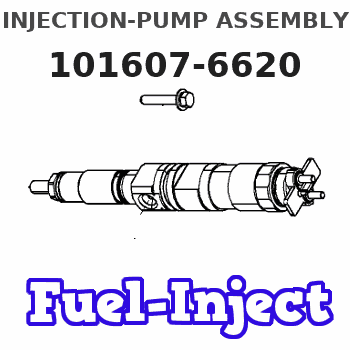
Rating:
Cross reference number
ZEXEL
101607-6620
1016076620
Zexel num
Bosch num
Firm num
Name
101607-6620
INJECTION-PUMP ASSEMBLY
Calibration Data:
Adjustment conditions
Test oil
1404 Test oil ISO4113 or {SAEJ967d}
1404 Test oil ISO4113 or {SAEJ967d}
Test oil temperature
degC
40
40
45
Nozzle and nozzle holder
105780-8140
Bosch type code
EF8511/9A
Nozzle
105780-0000
Bosch type code
DN12SD12T
Nozzle holder
105780-2080
Bosch type code
EF8511/9
Opening pressure
MPa
17.2
Opening pressure
kgf/cm2
175
Injection pipe
Outer diameter - inner diameter - length (mm) mm 6-2-600
Outer diameter - inner diameter - length (mm) mm 6-2-600
Overflow valve
131424-8420
Overflow valve opening pressure
kPa
255
221
289
Overflow valve opening pressure
kgf/cm2
2.6
2.25
2.95
Tester oil delivery pressure
kPa
157
157
157
Tester oil delivery pressure
kgf/cm2
1.6
1.6
1.6
Direction of rotation (viewed from drive side)
Left L
Left L
Injection timing adjustment
Direction of rotation (viewed from drive side)
Left L
Left L
Injection order
1-5-3-6-
2-4
Pre-stroke
mm
3.2
3.15
3.25
Beginning of injection position
Governor side NO.1
Governor side NO.1
Difference between angles 1
Cal 1-5 deg. 60 59.5 60.5
Cal 1-5 deg. 60 59.5 60.5
Difference between angles 2
Cal 1-3 deg. 120 119.5 120.5
Cal 1-3 deg. 120 119.5 120.5
Difference between angles 3
Cal 1-6 deg. 180 179.5 180.5
Cal 1-6 deg. 180 179.5 180.5
Difference between angles 4
Cyl.1-2 deg. 240 239.5 240.5
Cyl.1-2 deg. 240 239.5 240.5
Difference between angles 5
Cal 1-4 deg. 300 299.5 300.5
Cal 1-4 deg. 300 299.5 300.5
Injection quantity adjustment
Adjusting point
-
Rack position
11.7
Pump speed
r/min
850
850
850
Each cylinder's injection qty
mm3/st.
77.5
75.2
79.8
Basic
*
Fixing the rack
*
Standard for adjustment of the maximum variation between cylinders
*
Injection quantity adjustment_02
Adjusting point
Z
Rack position
9.5+-0.5
Pump speed
r/min
800
800
800
Each cylinder's injection qty
mm3/st.
10.8
9.2
12.4
Fixing the rack
*
Standard for adjustment of the maximum variation between cylinders
*
Injection quantity adjustment_03
Adjusting point
A
Rack position
R1(11.7)
Pump speed
r/min
850
850
850
Average injection quantity
mm3/st.
77.5
76.5
78.5
Basic
*
Fixing the lever
*
Injection quantity adjustment_04
Adjusting point
B
Rack position
R1+0.25
Pump speed
r/min
1450
1450
1450
Average injection quantity
mm3/st.
84
80
88
Fixing the lever
*
Injection quantity adjustment_05
Adjusting point
C
Rack position
R1-0.55
Pump speed
r/min
500
500
500
Average injection quantity
mm3/st.
49.6
45.6
53.6
Fixing the lever
*
Injection quantity adjustment_06
Adjusting point
I
Rack position
-
Pump speed
r/min
100
100
100
Average injection quantity
mm3/st.
91
81
101
Fixing the lever
*
Rack limit
*
Timer adjustment
Pump speed
r/min
950--
Advance angle
deg.
0
0
0
Remarks
Start
Start
Timer adjustment_02
Pump speed
r/min
900
Advance angle
deg.
0.5
Timer adjustment_03
Pump speed
r/min
-
Advance angle
deg.
1
0.5
1.5
Remarks
Measure the actual speed.
Measure the actual speed.
Timer adjustment_04
Pump speed
r/min
1200
Advance angle
deg.
1
0.5
1.5
Timer adjustment_05
Pump speed
r/min
1450
Advance angle
deg.
7
6.5
7.5
Remarks
Finish
Finish
Test data Ex:
Governor adjustment
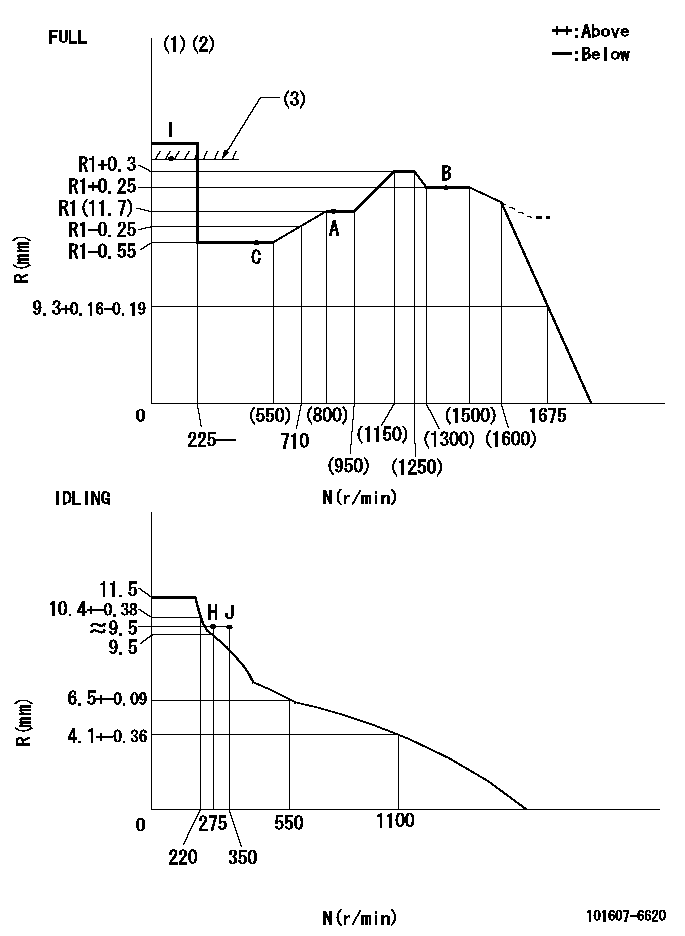
N:Pump speed
R:Rack position (mm)
(1)Torque cam stamping: T1
(2)Tolerance for racks not indicated: +-0.05mm.
(3)RACK LIMIT
----------
T1=J30
----------
----------
T1=J30
----------
Speed control lever angle
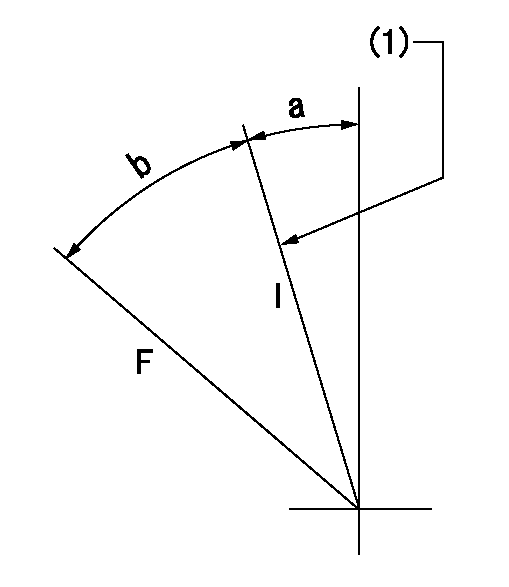
F:Full speed
I:Idle
(1)Stopper bolt set position 'H'
----------
----------
a=18.5deg+-5deg b=42deg+-3deg
----------
----------
a=18.5deg+-5deg b=42deg+-3deg
Stop lever angle
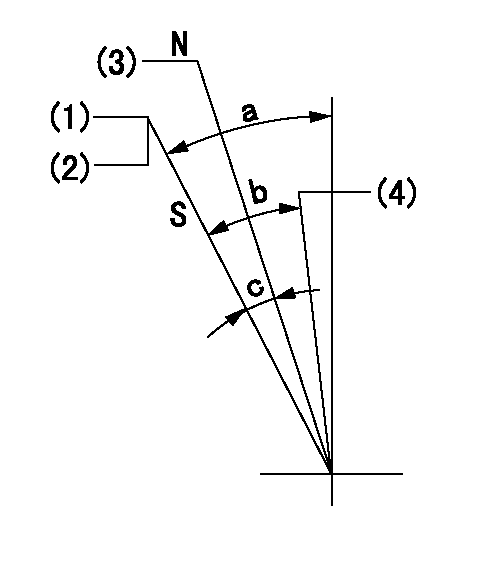
N:Engine manufacturer's normal use
S:Stop the pump.
(1)Set the stopper bolt so that speed = aa and rack position = bb and confirm non-injection.
(2)After setting the stopper bolt, confirm non-injection at speed cc. Rack position = dd (non-injection rack position).
(3)Rack position = approximately ee (speed lever full, speed = ff).
(4)Free (at delivery)
----------
aa=1450r/min bb=7.2-0.5mm cc=275r/min dd=(8.8)mm ee=15mm ff=0r/min
----------
a=36.5deg+-5deg b=(25deg) c=13deg+-5deg
----------
aa=1450r/min bb=7.2-0.5mm cc=275r/min dd=(8.8)mm ee=15mm ff=0r/min
----------
a=36.5deg+-5deg b=(25deg) c=13deg+-5deg
0000001501 LEVER
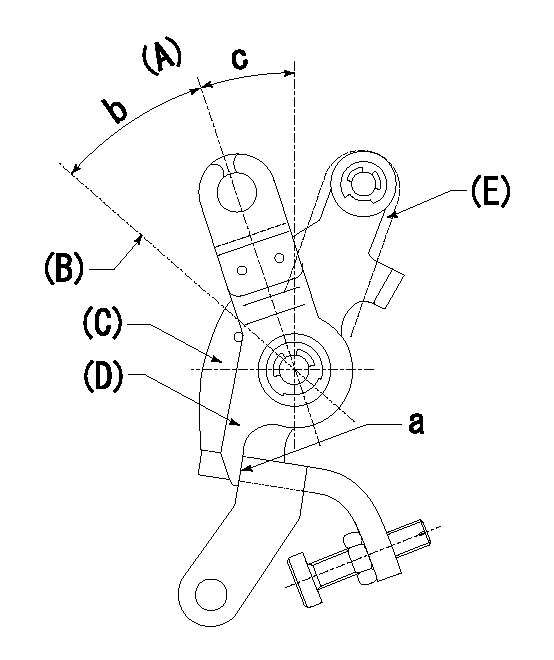
(A) Idle
(B) Full speed
(C) Base lever
(D) Accelerator lever
(E) Accelerator lever delivery position
1. Measure speed lever angle
(1)Measure the angle when the accelerator lever (D) contacted the base lever (C) at a.
----------
----------
b=42deg+-3deg c=18.5deg+-5deg
----------
----------
b=42deg+-3deg c=18.5deg+-5deg
Timing setting

(1)Pump vertical direction
(2)Position of timer's tooth at No 1 cylinder's beginning of injection
(3)B.T.D.C.: aa
(4)-
----------
aa=8.5deg
----------
a=(2deg)
----------
aa=8.5deg
----------
a=(2deg)
Information:
Connect cable (2) to the RS-232 serial port of PC (1) .
Connect cable (2) to communication adapter (3) .
Connect cable (4) to communication adapter (3) .
Connect cable (4) to the service tool connector on the engine mounted CIP.
Turn the engine control switch to the LOCAL position or to the REMOTE position. Turn the fuel control switch to the FUEL OFF position. The engine should be OFF.If Cat ET and the communication adapter do not communicate with the ECM, refer to Troubleshooting, RENR5910, "Electronic Service Tool Will Not Communicate With ECM".Troubleshooting
Refer to Troubleshooting, RENR5084 for more information on the following components.
Sensor faults
Injector faults
Response checks for the throttle input
Shutdown input response checksRequirements for the Electrical System
When you route the wiring, avoid acute bends and sharp edges. To protect the wiring harnesses, route the harnesses through a metal conduit. Use a rigid conduit or a use flexible conduit. A liquid tight conduit is recommended. Use proper support and alignment in order to avoid strain on the conduit.Electronic Service Tools
Caterpillar Electronic Service Tools are designed to help the service technician:
Obtain data.
Diagnose problems.
Read parameters.
Program parameters.
Calibrate sensors.The tools that are listed in Table 12 are required in order to enable a service technician to perform the electrical installation procedures and the initial start-up.Note: Other tools that are needed for measuring operating parameters such as pressure and temperature are not listed in Table 12.
Table 12
Service Tools    
Pt. No.    Description    Functions    
N/A     Personal Computer (PC)     This PC configuration is recommended:
Intel Pentium II 333 mHz processor
64 megabyte of RAM
4.3 GB hard drive
Drive for floppy disks (3.5 inch with 1.44 MB)
14X speed CD-ROM drive
VGA monitor or display
RS-232 port with 16550AF UART
Windows NT 4.0 (1)
Windows 95 (1)
Windows 98 (1)
Mouse    
N/A     Personal Computer (PC)     This PC configuration has the minimum requirements:
IBM PC compatible 100 MHz processor
32 megabyte of RAM
10 MB of available hard drive space
CD-ROM drive
Drive for floppy disks (3.5 inch with 1.44 MB)
Windows NT 4.0 (1)
Windows 95 (1)
Windows 98 (1)
RS-232 port with 16550AF UART
VGA monitor or display
Mouse    
"JERD2124"     Software     Single user license for Caterpillar Electronic Technician (Cat ET)
Use the most recent version of this software.    
"JERD2129"     Software     Data subscription for all engines    
171-4401     Communication Adapter II (1)     The communication adapter is connected between the PC (ET) and the ECM.    
196-0055     Serial Cable As     This cable connects the PC to the 171-4401 Communication Adapter II .    
7X-1414     Data Link Cable As     This cable connects the service tool connector on the engine mounted junction box to the 139-4166 Adapter Cable As .    
8T-8726     Adapter Cable As     This breakout t is for use between the jacks and the plugs of the sensors.    
151-6320     Wire Removal Tool     This tool is used for the removal of pins and sockets from Deutsch connectors and AMP connectors.    
1U-5804     Crimp Tool     This tool is used for work with
Have questions with 101607-6620?
Group cross 101607-6620 ZEXEL
101607-6620
INJECTION-PUMP ASSEMBLY