Information injection-pump assembly
BOSCH
F 019 Z20 001
f019z20001
ZEXEL
101607-6601
1016076601
MITSUBISHI
ME302678
me302678
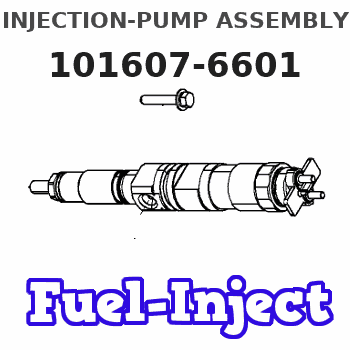
Rating:
Service parts 101607-6601 INJECTION-PUMP ASSEMBLY:
1.
_
6.
COUPLING PLATE
7.
COUPLING PLATE
8.
_
9.
_
11.
Nozzle and Holder
ME035655
12.
Open Pre:MPa(Kqf/cm2)
21.6{220}
15.
NOZZLE SET
Cross reference number
BOSCH
F 019 Z20 001
f019z20001
ZEXEL
101607-6601
1016076601
MITSUBISHI
ME302678
me302678
Zexel num
Bosch num
Firm num
Name
101607-6601
F 019 Z20 001
ME302678 MITSUBISHI
INJECTION-PUMP ASSEMBLY
6D14 K 14BE INJECTION PUMP ASSY PE6A PE
6D14 K 14BE INJECTION PUMP ASSY PE6A PE
Calibration Data:
Adjustment conditions
Test oil
1404 Test oil ISO4113 or {SAEJ967d}
1404 Test oil ISO4113 or {SAEJ967d}
Test oil temperature
degC
40
40
45
Nozzle and nozzle holder
105780-8140
Bosch type code
EF8511/9A
Nozzle
105780-0000
Bosch type code
DN12SD12T
Nozzle holder
105780-2080
Bosch type code
EF8511/9
Opening pressure
MPa
17.2
Opening pressure
kgf/cm2
175
Injection pipe
Outer diameter - inner diameter - length (mm) mm 6-2-600
Outer diameter - inner diameter - length (mm) mm 6-2-600
Overflow valve
131424-5520
Overflow valve opening pressure
kPa
255
221
289
Overflow valve opening pressure
kgf/cm2
2.6
2.25
2.95
Tester oil delivery pressure
kPa
157
157
157
Tester oil delivery pressure
kgf/cm2
1.6
1.6
1.6
Direction of rotation (viewed from drive side)
Left L
Left L
Injection timing adjustment
Direction of rotation (viewed from drive side)
Left L
Left L
Injection order
1-5-3-6-
2-4
Pre-stroke
mm
3.3
3.25
3.35
Beginning of injection position
Governor side NO.1
Governor side NO.1
Difference between angles 1
Cal 1-5 deg. 60 59.5 60.5
Cal 1-5 deg. 60 59.5 60.5
Difference between angles 2
Cal 1-3 deg. 120 119.5 120.5
Cal 1-3 deg. 120 119.5 120.5
Difference between angles 3
Cal 1-6 deg. 180 179.5 180.5
Cal 1-6 deg. 180 179.5 180.5
Difference between angles 4
Cyl.1-2 deg. 240 239.5 240.5
Cyl.1-2 deg. 240 239.5 240.5
Difference between angles 5
Cal 1-4 deg. 300 299.5 300.5
Cal 1-4 deg. 300 299.5 300.5
Injection quantity adjustment
Adjusting point
-
Rack position
11
Pump speed
r/min
850
850
850
Each cylinder's injection qty
mm3/st.
65
63
67
Basic
*
Fixing the rack
*
Standard for adjustment of the maximum variation between cylinders
*
Injection quantity adjustment_02
Adjusting point
H
Rack position
9.5+-0.5
Pump speed
r/min
275
275
275
Each cylinder's injection qty
mm3/st.
10.5
9
12
Fixing the rack
*
Standard for adjustment of the maximum variation between cylinders
*
Injection quantity adjustment_03
Adjusting point
A
Rack position
R1(11)
Pump speed
r/min
850
850
850
Average injection quantity
mm3/st.
65
64
66
Basic
*
Fixing the lever
*
Injection quantity adjustment_04
Adjusting point
B
Rack position
R1(11)
Pump speed
r/min
1450
1450
1450
Average injection quantity
mm3/st.
77.5
75.5
79.5
Fixing the lever
*
Injection quantity adjustment_05
Adjusting point
C
Rack position
R1+0.4
Pump speed
r/min
600
600
600
Average injection quantity
mm3/st.
59.7
55.7
63.7
Fixing the lever
*
Injection quantity adjustment_06
Adjusting point
I
Rack position
12.1++
Pump speed
r/min
100
100
100
Average injection quantity
mm3/st.
90
80
100
Fixing the lever
*
Rack limit
*
Timer adjustment
Pump speed
r/min
900--
Advance angle
deg.
0
0
0
Remarks
Start
Start
Timer adjustment_02
Pump speed
r/min
850
Advance angle
deg.
0.5
Timer adjustment_03
Pump speed
r/min
900
Advance angle
deg.
0.8
Timer adjustment_04
Pump speed
r/min
1200
Advance angle
deg.
1.9
1.9
1.9
Timer adjustment_05
Pump speed
r/min
1500
Advance angle
deg.
5.5
5
6
Remarks
Finish
Finish
Test data Ex:
Governor adjustment
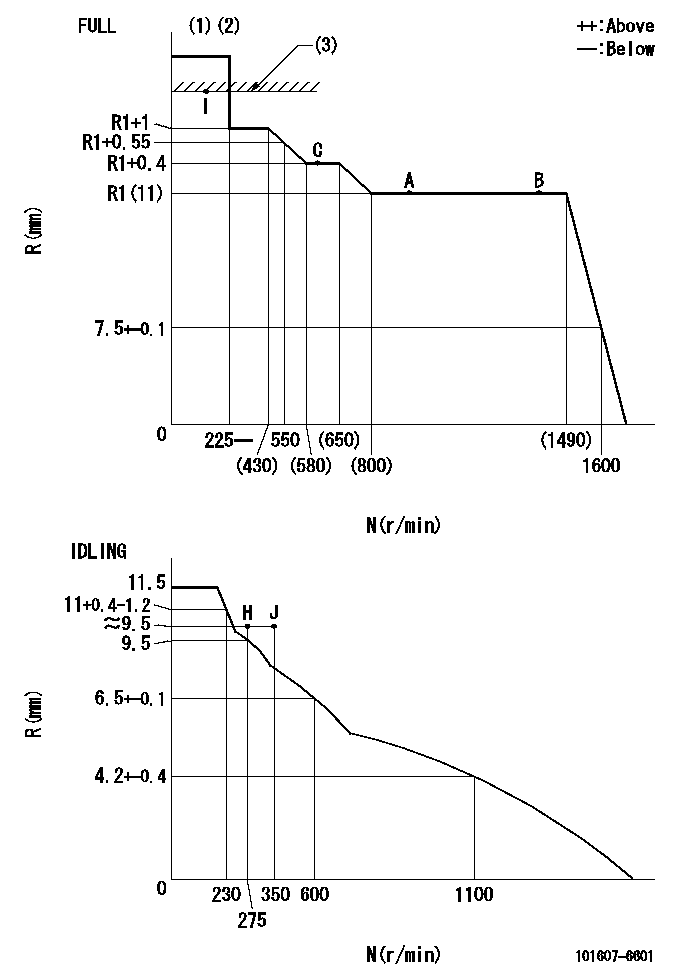
N:Pump speed
R:Rack position (mm)
(1)Torque cam stamping: T1
(2)Tolerance for racks not indicated: +-0.05mm.
(3)RACK LIMIT
----------
T1=D52
----------
----------
T1=D52
----------
Speed control lever angle

F:Full speed
I:Idle
(1)Use the hole at R = aa
(2)Stopper bolt set position 'H'
----------
aa=40mm
----------
a=18.5deg+-5deg b=40.5deg+-3deg
----------
aa=40mm
----------
a=18.5deg+-5deg b=40.5deg+-3deg
Stop lever angle
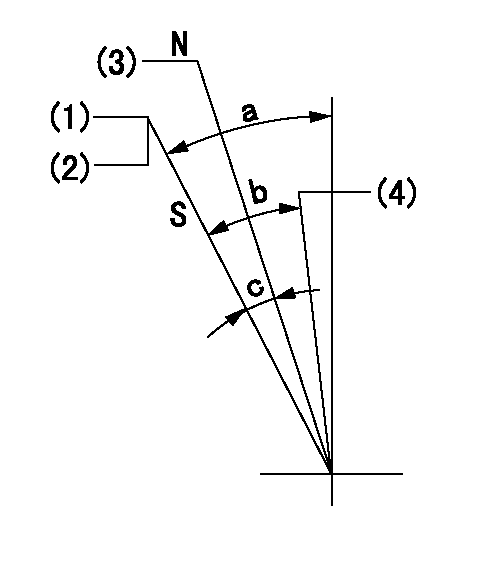
N:Engine manufacturer's normal use
S:Stop the pump.
(1)Set the stopper bolt at pump speed = aa and rack position = bb (non-injection rack position). Confirm non-injection.
(2)After setting the stopper bolt, confirm non-injection at speed cc. Rack position = dd (non-injection rack position).
(3)Rack position = approximately ee (speed lever full, speed = ff).
(4)Free (at delivery)
----------
aa=1450r/min bb=4.7-0.5mm cc=275r/min dd=(6.7)mm ee=15mm ff=0r/min
----------
a=38.5deg+-5deg b=(29deg) c=17deg+-5deg
----------
aa=1450r/min bb=4.7-0.5mm cc=275r/min dd=(6.7)mm ee=15mm ff=0r/min
----------
a=38.5deg+-5deg b=(29deg) c=17deg+-5deg
0000001501 LEVER
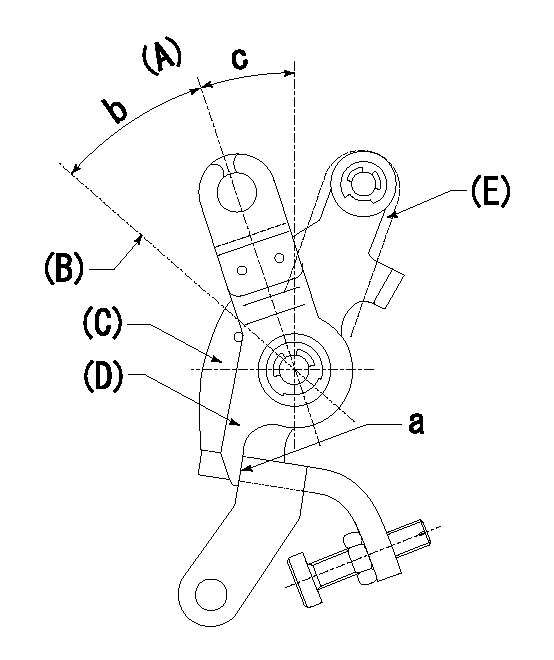
(A) Idle
(B) Full speed
(C) Base lever
(D) Accelerator lever
(E) Accelerator lever delivery position
1. Measure speed lever angle
(1)Measure the angle when the accelerator lever (D) contacted the base lever (C) at a.
----------
----------
b=40.5deg+-3deg c=18.5deg+-5deg
----------
----------
b=40.5deg+-3deg c=18.5deg+-5deg
0000001601 ACS

(A) Housing
(B) Snap ring
(C) adjusting screw
(D) Set screw
(E): Push rod
(F) Spacer
1. Adjustment of the aneroid compensator
(1)Adjust with the (D) set screw so that the clearance between the (A) housing and (B) snap ring is L1.
(2)Select the push rod (E) so that the distance from the end surface of the (F) spacer becomes L2.
(3)(C) Turn the screw to adjust the beginning of aneroid compensator operation.
2. Adjustment when mounting the governor.
(1)Set the speed of the pump to N1 r/min and fix the control lever at the full set position.
(2)Adjust using screw C to obtain the performance shown in the graph above.
(3)After final adjustment, confirm that the gap between housing (A) and snapring (B) is L3.
----------
N1=850r/min L1=1.4~1.7mm L2=0.5+-0.5mm L3=0.1~0.5mm
----------
Ra=R1(11)mm Rb=R1-0.3mm Pa=89.8+-2.7kPa(674+-20mmHg) Pb=79.4kPa(596mmHg) Q1=65+-1cm3/1000st Q2=(59)cm3/1000st
----------
N1=850r/min L1=1.4~1.7mm L2=0.5+-0.5mm L3=0.1~0.5mm
----------
Ra=R1(11)mm Rb=R1-0.3mm Pa=89.8+-2.7kPa(674+-20mmHg) Pb=79.4kPa(596mmHg) Q1=65+-1cm3/1000st Q2=(59)cm3/1000st
Timing setting

(1)Pump vertical direction
(2)Position of timer's tooth at No 1 cylinder's beginning of injection
(3)B.T.D.C.: aa
(4)-
----------
aa=16deg
----------
a=(1deg)
----------
aa=16deg
----------
a=(1deg)
Information:
Tools that are Required for Installation
Table 2
Required Tools    
Tool    Part Number    Part Description    Qty    
B     9U-6862     Tapered Brush     1    
9U-6863 Small Bore Brush     1    
9U-7244 End Brush     1    
9U-7237 Brush Extension     1    
4C-5552 Large Bore Brush     1    
C (1)     221-9778     Puller Stud     1    
D (1)     9U-7258     Driver Cap     1    
E     4C-9507     Retaining Compound     -    
( 1 ) Part of the 9U-6891 Injector Tool Group Removal Procedure
Keep all parts clean from contaminants.Contaminants may cause rapid wear and shortened component life.
Remove the electronic unit injector. Refer to Disassembly and Assembly, "Electronic Unit Injector - Remove".
Illustration 1 g01016237
Install the puller stud from Tooling (A) into unit injector sleeve (1) .
Install the following parts from Tooling (A) over the stud: bridge puller, thrust bearing, hard washer and nut.
Tighten the nut until unit injector sleeve (1) is pulled free of the cylinder head assembly.Installation Procedure
Use Tooling (B) to clean the bore in the cylinder head for the electronic unit injector sleeve.
Ensure that the electronic unit injector sleeve and the cylinder head bore are completely free of oil, dirt, and sealant debris.
Illustration 2 g01120522
Install new O-ring seals (2) on electronic unit injector sleeve (1) .Note: Do not apply Tooling (E) to the cylinder head surfaces. Apply Tooling (E) on the electronic unit injector sleeve only.
Apply Tooling (E) to the contact surface of electronic unit injector sleeve (1) on the surface that is marked "X".
Lubricate O-ring seals (2) with clean engine oil.
Illustration 3 g01076119
Install Tooling (C) into the threads of electronic unit injector sleeve (1) .
Position Tooling (C) and the electronic unit injector sleeve in the cylinder head. Use care not to damage the O-ring seal on the electronic unit injector sleeve.
Use Tooling (D) and a hammer to install electronic unit injector sleeve (1) in the cylinder head.
Ensure that the electronic unit injector sleeve is properly seated in the cylinder head. The Tooling will "RING" when the electronic unit injector sleeve is fully seated in the bore of the cylinder head.
Remove Tooling (D) and Tooling (C). Use a clean towel and remove excess Tooling (E) .
Install the electronic unit injector. Refer to Disassembly and Assembly, "Electronic Unit Injector - Install".
Fill the cooling system with coolant. Refer to Operation and Maintenance, "Refill Capacities" for the cooling system capacity.
Table 2
Required Tools    
Tool    Part Number    Part Description    Qty    
B     9U-6862     Tapered Brush     1    
9U-6863 Small Bore Brush     1    
9U-7244 End Brush     1    
9U-7237 Brush Extension     1    
4C-5552 Large Bore Brush     1    
C (1)     221-9778     Puller Stud     1    
D (1)     9U-7258     Driver Cap     1    
E     4C-9507     Retaining Compound     -    
( 1 ) Part of the 9U-6891 Injector Tool Group Removal Procedure
Keep all parts clean from contaminants.Contaminants may cause rapid wear and shortened component life.
Remove the electronic unit injector. Refer to Disassembly and Assembly, "Electronic Unit Injector - Remove".
Illustration 1 g01016237
Install the puller stud from Tooling (A) into unit injector sleeve (1) .
Install the following parts from Tooling (A) over the stud: bridge puller, thrust bearing, hard washer and nut.
Tighten the nut until unit injector sleeve (1) is pulled free of the cylinder head assembly.Installation Procedure
Use Tooling (B) to clean the bore in the cylinder head for the electronic unit injector sleeve.
Ensure that the electronic unit injector sleeve and the cylinder head bore are completely free of oil, dirt, and sealant debris.
Illustration 2 g01120522
Install new O-ring seals (2) on electronic unit injector sleeve (1) .Note: Do not apply Tooling (E) to the cylinder head surfaces. Apply Tooling (E) on the electronic unit injector sleeve only.
Apply Tooling (E) to the contact surface of electronic unit injector sleeve (1) on the surface that is marked "X".
Lubricate O-ring seals (2) with clean engine oil.
Illustration 3 g01076119
Install Tooling (C) into the threads of electronic unit injector sleeve (1) .
Position Tooling (C) and the electronic unit injector sleeve in the cylinder head. Use care not to damage the O-ring seal on the electronic unit injector sleeve.
Use Tooling (D) and a hammer to install electronic unit injector sleeve (1) in the cylinder head.
Ensure that the electronic unit injector sleeve is properly seated in the cylinder head. The Tooling will "RING" when the electronic unit injector sleeve is fully seated in the bore of the cylinder head.
Remove Tooling (D) and Tooling (C). Use a clean towel and remove excess Tooling (E) .
Install the electronic unit injector. Refer to Disassembly and Assembly, "Electronic Unit Injector - Install".
Fill the cooling system with coolant. Refer to Operation and Maintenance, "Refill Capacities" for the cooling system capacity.
Have questions with 101607-6601?
Group cross 101607-6601 ZEXEL
Mitsubishi
101607-6601
F 019 Z20 001
ME302678
INJECTION-PUMP ASSEMBLY
6D14
6D14