Information injection-pump assembly
BOSCH
9 400 615 712
9400615712
ZEXEL
101607-6550
1016076550
MITSUBISHI
ME077811
me077811
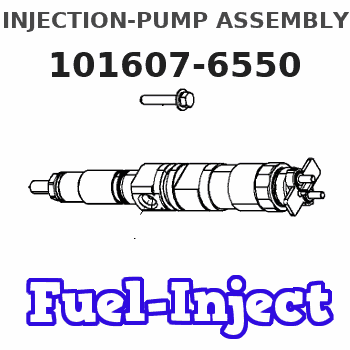
Rating:
Service parts 101607-6550 INJECTION-PUMP ASSEMBLY:
1.
_
6.
COUPLING PLATE
7.
COUPLING PLATE
8.
_
9.
_
11.
Nozzle and Holder
ME076952
12.
Open Pre:MPa(Kqf/cm2)
15.7{160}/21.6{220}
14.
NOZZLE
Cross reference number
BOSCH
9 400 615 712
9400615712
ZEXEL
101607-6550
1016076550
MITSUBISHI
ME077811
me077811
Zexel num
Bosch num
Firm num
Name
101607-6550
9 400 615 712
ME077811 MITSUBISHI
INJECTION-PUMP ASSEMBLY
6D17 K
6D17 K
Calibration Data:
Adjustment conditions
Test oil
1404 Test oil ISO4113 or {SAEJ967d}
1404 Test oil ISO4113 or {SAEJ967d}
Test oil temperature
degC
40
40
45
Nozzle and nozzle holder
105780-8140
Bosch type code
EF8511/9A
Nozzle
105780-0000
Bosch type code
DN12SD12T
Nozzle holder
105780-2080
Bosch type code
EF8511/9
Opening pressure
MPa
17.2
Opening pressure
kgf/cm2
175
Injection pipe
Outer diameter - inner diameter - length (mm) mm 6-2-600
Outer diameter - inner diameter - length (mm) mm 6-2-600
Overflow valve
131424-8420
Overflow valve opening pressure
kPa
255
221
289
Overflow valve opening pressure
kgf/cm2
2.6
2.25
2.95
Tester oil delivery pressure
kPa
157
157
157
Tester oil delivery pressure
kgf/cm2
1.6
1.6
1.6
Direction of rotation (viewed from drive side)
Left L
Left L
Injection timing adjustment
Direction of rotation (viewed from drive side)
Left L
Left L
Injection order
1-5-3-6-
2-4
Pre-stroke
mm
3.2
3.15
3.25
Beginning of injection position
Governor side NO.1
Governor side NO.1
Difference between angles 1
Cal 1-5 deg. 60 59.5 60.5
Cal 1-5 deg. 60 59.5 60.5
Difference between angles 2
Cal 1-3 deg. 120 119.5 120.5
Cal 1-3 deg. 120 119.5 120.5
Difference between angles 3
Cal 1-6 deg. 180 179.5 180.5
Cal 1-6 deg. 180 179.5 180.5
Difference between angles 4
Cyl.1-2 deg. 240 239.5 240.5
Cyl.1-2 deg. 240 239.5 240.5
Difference between angles 5
Cal 1-4 deg. 300 299.5 300.5
Cal 1-4 deg. 300 299.5 300.5
Injection quantity adjustment
Adjusting point
-
Rack position
12
Pump speed
r/min
850
850
850
Each cylinder's injection qty
mm3/st.
85.1
82.5
87.7
Basic
*
Fixing the rack
*
Standard for adjustment of the maximum variation between cylinders
*
Injection quantity adjustment_02
Adjusting point
Z
Rack position
9.5+-0.5
Pump speed
r/min
800
800
800
Each cylinder's injection qty
mm3/st.
10.8
9.2
12.4
Fixing the rack
*
Standard for adjustment of the maximum variation between cylinders
*
Injection quantity adjustment_03
Adjusting point
A
Rack position
R1(12)
Pump speed
r/min
850
850
850
Average injection quantity
mm3/st.
85.1
84.1
86.1
Basic
*
Fixing the lever
*
Injection quantity adjustment_04
Adjusting point
B
Rack position
R1+0.85
Pump speed
r/min
1450
1450
1450
Average injection quantity
mm3/st.
99.9
95.9
103.9
Fixing the lever
*
Injection quantity adjustment_05
Adjusting point
I
Rack position
-
Pump speed
r/min
100
100
100
Average injection quantity
mm3/st.
91
81
101
Fixing the lever
*
Rack limit
*
Timer adjustment
Pump speed
r/min
1150--
Advance angle
deg.
0
0
0
Remarks
Start
Start
Timer adjustment_02
Pump speed
r/min
1100
Advance angle
deg.
0.5
Timer adjustment_03
Pump speed
r/min
1450
Advance angle
deg.
6
5.5
6.5
Remarks
Finish
Finish
Test data Ex:
Governor adjustment
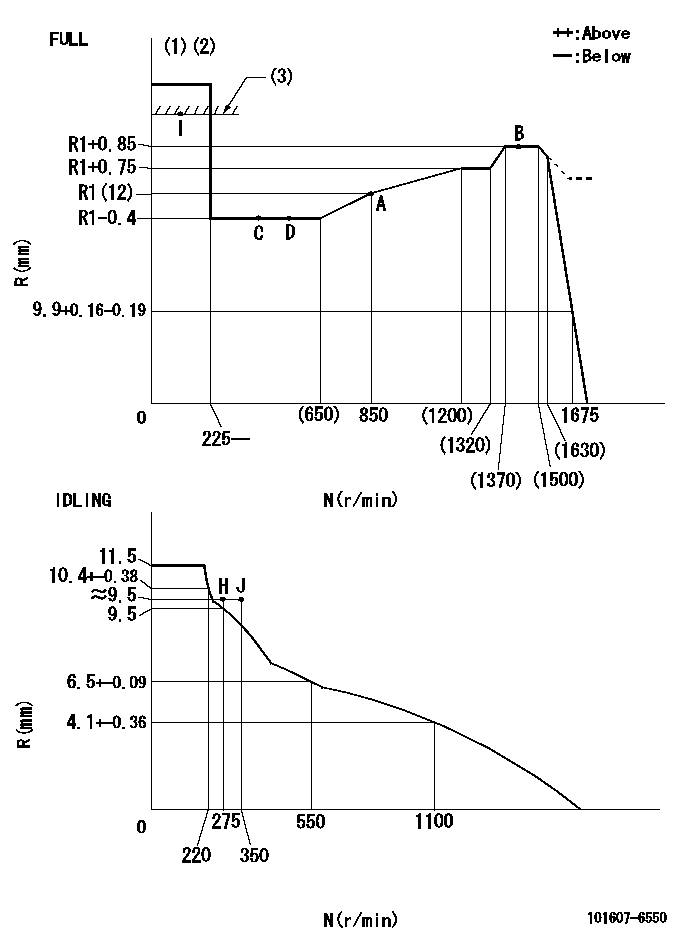
N:Pump speed
R:Rack position (mm)
(1)Torque cam stamping: T1
(2)Tolerance for racks not indicated: +-0.05mm.
(3)RACK LIMIT
----------
T1=G43
----------
----------
T1=G43
----------
Speed control lever angle
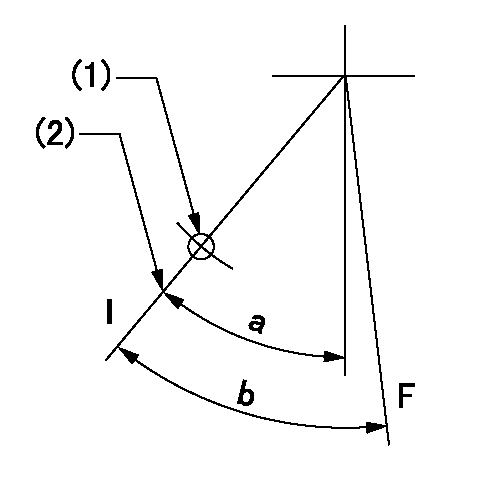
F:Full speed
I:Idle
(1)Use the hole at R = aa
(2)Stopper bolt set position 'H'
----------
aa=35mm
----------
a=33deg+-5deg b=(42deg)+-3deg
----------
aa=35mm
----------
a=33deg+-5deg b=(42deg)+-3deg
Stop lever angle

N:Engine manufacturer's normal use
S:Stop the pump.
(1)Set the stopper bolt so that speed = aa and rack position = bb and confirm non-injection.
(2)After setting the stopper bolt, confirm non-injection at speed cc. Rack position = dd (non-injection rack position).
(3)Rack position = approximately ee (speed lever full, speed = ff).
(4)Free (at delivery)
----------
aa=1450r/min bb=7.2-0.5mm cc=275r/min dd=(8.8)mm ee=15mm ff=0r/min
----------
a=13deg+-5deg b=0deg+-5deg c=(25deg)
----------
aa=1450r/min bb=7.2-0.5mm cc=275r/min dd=(8.8)mm ee=15mm ff=0r/min
----------
a=13deg+-5deg b=0deg+-5deg c=(25deg)
0000001501 MICRO SWITCH
Adjustment of the micro-switch
Adjust the bolt to obtain the following lever position when the micro-switch is ON.
(1)Speed N1
(2)Rack position Ra
----------
N1=400r/min Ra=9.2+-0.1mm
----------
----------
N1=400r/min Ra=9.2+-0.1mm
----------
0000001601 RACK SENSOR

V1:Supply voltage
V2f:Full side output voltage
V2i:Idle side output voltage
(A) Black
(B) Yellow
(C) Red
(D) Trimmer
(E): Shaft
(F) Nut
(G) Load lever
1. Load sensor adjustment
(1)Connect as shown in the above diagram and apply supply voltage V1.
(2)Hold the load lever (G) against the full side.
(3)Turn the shaft so that the voltage between (A) and (B) is V2.
(4)Hold the load lever (G) against the idle side.
(5)Adjust (D) so that the voltage between (A) and (B) is V2i.
(6)Repeat the above adjustments.
(7)Tighten the nut (F) at the point satisfying the standards.
(8)Hold the load lever against the full side stopper and the idle side stopper.
(9)At this time, confirm that the full side output voltage is V2f and the idle side output voltage is V2i.
----------
V1=3.57+-0.02V V2f=3+0.05V V2i=1+0.1V
----------
----------
V1=3.57+-0.02V V2f=3+0.05V V2i=1+0.1V
----------
Timing setting

(1)Pump vertical direction
(2)Position of timer's tooth at No 1 cylinder's beginning of injection
(3)B.T.D.C.: aa
(4)-
----------
aa=10deg
----------
a=(1deg)
----------
aa=10deg
----------
a=(1deg)
Information:
Table 2
Ethylene Glycol Concentration
Concentration Freeze Protection Boil Protection(1)
20 Percent −8° C (18° F) 102° C (216° F)
50 Percent −37 °C (−34 °F) 106 °C (223 °F)
60 Percent −52 °C (−62 °F) 111 °C (232 °F)
(1) Boiling protection is increased with the use of a pressurized radiator.Do not use propylene glycol in concentrations that exceed 50 percent glycol because of the reduced heat transfer capability. Use ethylene glycol in conditions that require additional protection against boiling or freezing. Do not use ethylene glycol in concentrations that exceed 60 percent glycol.
Table 3
Propylene Glycol Concentration
Concentration Freeze Protection Boil Protection(1)
50 Percent −32 °C (−26 °F) 106 °C (223 °F)
(1) Boiling protection is increased with the use of a pressurized radiator.Propylene glycol coolant that is used in the cooling systems for Cat diesel engines must meet ASTM D6210-06, "Fully-Formulated Glycol-Based Engine Coolant for Heavy-Duty Engines". When propylene glycol coolant is used in heavy-duty diesel engines, a regular addition of SCA is required for protection against liner cavitation. Consult your Cat dealer for additional information.Ethylene or propylene glycols used in cooling systems for Cat diesel engines must meet ASTM E1177-06, "Standard Specification for Engine Coolant Grade Glycol".Testing the Concentration of Glycol
To check the concentration of glycol, use the 245-5829 Coolant/Battery Tester/Refractometer or 360-0774 refractometer. The tester can be used with ethylene or propylene glycol.
Illustration 1 g01189253
Approximate curve of the freezing point for a typical ethylene glycol solution.
Table 4
Freeze Protection for Antifreeze Concentrations(1)
Protection to: Concentration
−8° C (18° F) 20% glycol
80% water
−15 °C (5 °F) 30% glycol
70% water
−24 °C (−12 °F) 40% glycol
60% water
−37 °C (−34 °F) 50% glycol
50% water
−52 °C (−62 °F) 60% glycol
40% water
(1) Ethylene glycol-based antifreeze.Alternative products that are used to protect from boiling or freezing of the engine coolant include:
“1,3 propandiol” (PDO)
glycerin
mixtures of these alternative products with glycolAt the time of publication of this document, there currently exists no ASTM, "specifications" for coolants using these chemicals. Until specifications are published and then evaluated by Cat, use of PDO and glycerin or glycerin/glycol coolants are not recommended in Cat cooling systems.Embitterment
Ethylene glycol is a toxic chemical with a naturally sweet taste. In order to avoid accidental excessive ingestion by humans or animals, coolants may contain embittering agents that make the coolant taste bad. All Cat glycol containing coolants (Cat ELC, Cat DEAC, and Cat NGEC) are embittered. Embittering agents have no beneficial or detrimental effect on coolant performance or characteristics.Coolant Terminology
Extended Life Coolant (ELC) - A coolant that relies largely on organic inhibitors for corrosion and cavitation protection. Carboxylate is an example of organic corrosion and cavitation inhibitors. Cat ELC and Cat ELI in water are extended life coolants that also include nitrites and molybdates for increased cavitation protection.
Commercial extended life coolants containing silicate do not meet the additional requirements set in this Special Publication for coolants claiming to meet Cat EC-1 specification.
Do not use commercial extended life coolants with more than 125 ppm silicon (present in the coolant in the form of silicate)
Extended life coolants that meet
Have questions with 101607-6550?
Group cross 101607-6550 ZEXEL
Mitsubishi
101607-6550
9 400 615 712
ME077811
INJECTION-PUMP ASSEMBLY
6D17
6D17