Information injection-pump assembly
BOSCH
9 400 615 702
9400615702
ZEXEL
101607-6450
1016076450
MITSUBISHI
ME077803
me077803

Rating:
Service parts 101607-6450 INJECTION-PUMP ASSEMBLY:
1.
_
6.
COUPLING PLATE
7.
COUPLING PLATE
8.
_
9.
_
11.
Nozzle and Holder
ME076952
12.
Open Pre:MPa(Kqf/cm2)
15.7{160}/21.6{220}
14.
NOZZLE
Cross reference number
BOSCH
9 400 615 702
9400615702
ZEXEL
101607-6450
1016076450
MITSUBISHI
ME077803
me077803
Zexel num
Bosch num
Firm num
Name
101607-6450
9 400 615 702
ME077803 MITSUBISHI
INJECTION-PUMP ASSEMBLY
6D16 K 14BF INJECTION PUMP ASSY PE6AD PE
6D16 K 14BF INJECTION PUMP ASSY PE6AD PE
Calibration Data:
Adjustment conditions
Test oil
1404 Test oil ISO4113 or {SAEJ967d}
1404 Test oil ISO4113 or {SAEJ967d}
Test oil temperature
degC
40
40
45
Nozzle and nozzle holder
105780-8140
Bosch type code
EF8511/9A
Nozzle
105780-0000
Bosch type code
DN12SD12T
Nozzle holder
105780-2080
Bosch type code
EF8511/9
Opening pressure
MPa
17.2
Opening pressure
kgf/cm2
175
Injection pipe
Outer diameter - inner diameter - length (mm) mm 6-2-600
Outer diameter - inner diameter - length (mm) mm 6-2-600
Overflow valve
131424-8420
Overflow valve opening pressure
kPa
255
221
289
Overflow valve opening pressure
kgf/cm2
2.6
2.25
2.95
Tester oil delivery pressure
kPa
157
157
157
Tester oil delivery pressure
kgf/cm2
1.6
1.6
1.6
Direction of rotation (viewed from drive side)
Left L
Left L
Injection timing adjustment
Direction of rotation (viewed from drive side)
Left L
Left L
Injection order
1-5-3-6-
2-4
Pre-stroke
mm
3.2
3.15
3.25
Beginning of injection position
Governor side NO.1
Governor side NO.1
Difference between angles 1
Cal 1-5 deg. 60 59.5 60.5
Cal 1-5 deg. 60 59.5 60.5
Difference between angles 2
Cal 1-3 deg. 120 119.5 120.5
Cal 1-3 deg. 120 119.5 120.5
Difference between angles 3
Cal 1-6 deg. 180 179.5 180.5
Cal 1-6 deg. 180 179.5 180.5
Difference between angles 4
Cyl.1-2 deg. 240 239.5 240.5
Cyl.1-2 deg. 240 239.5 240.5
Difference between angles 5
Cal 1-4 deg. 300 299.5 300.5
Cal 1-4 deg. 300 299.5 300.5
Injection quantity adjustment
Adjusting point
-
Rack position
11.7
Pump speed
r/min
850
850
850
Each cylinder's injection qty
mm3/st.
77.4
75.1
79.7
Basic
*
Fixing the rack
*
Standard for adjustment of the maximum variation between cylinders
*
Injection quantity adjustment_02
Adjusting point
Z
Rack position
9.5+-0.5
Pump speed
r/min
800
800
800
Each cylinder's injection qty
mm3/st.
10.8
9.2
12.4
Fixing the rack
*
Standard for adjustment of the maximum variation between cylinders
*
Injection quantity adjustment_03
Adjusting point
A
Rack position
R1(11.7)
Pump speed
r/min
850
850
850
Average injection quantity
mm3/st.
77.4
76.4
78.4
Basic
*
Fixing the lever
*
Injection quantity adjustment_04
Adjusting point
B
Rack position
R1+0.55
Pump speed
r/min
1450
1450
1450
Average injection quantity
mm3/st.
87.7
83.7
91.7
Fixing the lever
*
Injection quantity adjustment_05
Adjusting point
C
Rack position
R1-0.4
Pump speed
r/min
500
500
500
Average injection quantity
mm3/st.
56
52
60
Fixing the lever
*
Injection quantity adjustment_06
Adjusting point
E
Rack position
(R1+0.5)
Pump speed
r/min
1100
1100
1100
Average injection quantity
mm3/st.
87.6
83.6
91.6
Fixing the lever
*
Injection quantity adjustment_07
Adjusting point
I
Rack position
-
Pump speed
r/min
100
100
100
Average injection quantity
mm3/st.
91
81
101
Fixing the lever
*
Rack limit
*
Timer adjustment
Pump speed
r/min
1150--
Advance angle
deg.
0
0
0
Remarks
Start
Start
Timer adjustment_02
Pump speed
r/min
1100
Advance angle
deg.
0.5
Timer adjustment_03
Pump speed
r/min
1450
Advance angle
deg.
6
5.5
6.5
Remarks
Finish
Finish
Test data Ex:
Governor adjustment
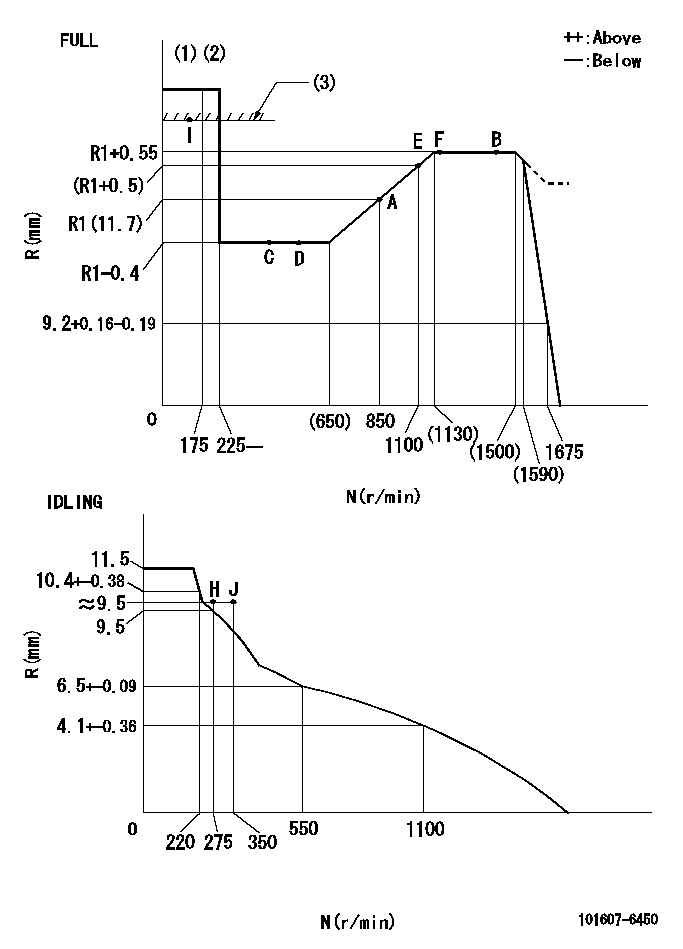
N:Pump speed
R:Rack position (mm)
(1)Torque cam stamping: T1
(2)Tolerance for racks not indicated: +-0.05mm.
(3)RACK LIMIT
----------
T1=H50
----------
----------
T1=H50
----------
Speed control lever angle
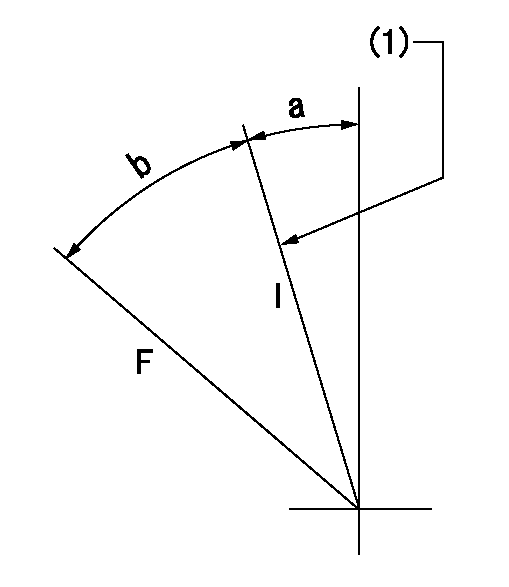
F:Full speed
I:Idle
(1)Stopper bolt set position 'H'
----------
----------
a=18.5deg+-5deg b=(42deg)+-3deg
----------
----------
a=18.5deg+-5deg b=(42deg)+-3deg
Stop lever angle
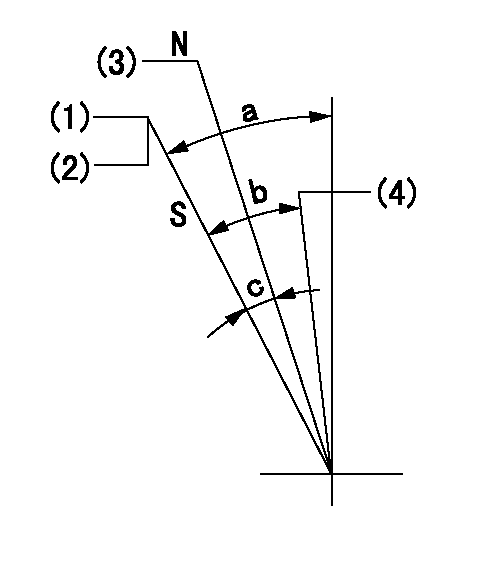
N:Engine manufacturer's normal use
S:Stop the pump.
(1)Set the stopper bolt at pump speed = aa and rack position = bb (non-injection rack position). Confirm non-injection.
(2)After setting the stopper bolt, confirm non-injection at speed cc. Rack position = dd (non-injection rack position).
(3)Rack position = approximately ee.
(4)Free (at delivery)
----------
aa=1450r/min bb=7.2-0.5mm cc=275r/min dd=(8.8)mm ee=15mm
----------
a=36.5deg+-5deg b=(25deg) c=13deg+-5deg
----------
aa=1450r/min bb=7.2-0.5mm cc=275r/min dd=(8.8)mm ee=15mm
----------
a=36.5deg+-5deg b=(25deg) c=13deg+-5deg
0000001501 LEVER
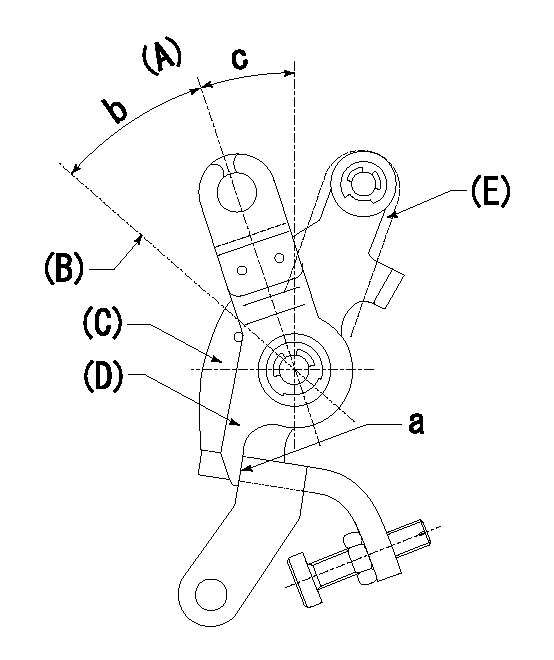
(A) Idle
(B) Full speed
(C) Base lever
(D) Accelerator lever
(E) Accelerator lever delivery position
1. Measure speed lever angle
(1)Measure the angle when the accelerator lever (D) contacted the base lever (C) at a.
----------
----------
b=(42deg)+-3deg c=18.5deg+-5deg
----------
----------
b=(42deg)+-3deg c=18.5deg+-5deg
Timing setting

(1)Pump vertical direction
(2)Position of timer's tooth at No 1 cylinder's beginning of injection
(3)B.T.D.C.: aa
(4)-
----------
aa=10deg
----------
a=(2deg)
----------
aa=10deg
----------
a=(2deg)
Information:
Do not use a commercial coolant/antifreeze that only meets the ASTM "D3306" specification. This type of coolant/antifreeze is made for light duty automotive applications.Use only the coolant/antifreeze that is recommended.
Caterpillar recommends a 1:1 mixture of properly inhibited distilled or deionized water and glycol. This mixture will provide optimum heavy-duty performance as a coolant/antifreeze.Note: Cat DEAC does not require a treatment with an SCA at the initial fill. However, a commercial heavy-duty coolant/antifreeze that only meets "ASTM D4985", by specification, WILL require a treatment with an SCA at the initial fill. A commercial heavy-duty coolant/antifreeze that meets the "ASTM D6210" specification WILL NOT require a treatment with an SCA at the initial fill. Read the label or the instructions that are provided by the manufacturer of the commercial heavy-duty coolant/antifreeze.Note: When adding SCA at initial fill to a coolant/antifreeze that only meets the "ASTM D4985", ensure the SCA is compatible with the antifreeze/coolant. For example, a HOAT coolant that meets the "ASTM D4985" specification may not be compatible with an SCA designed for use with conventional coolants. It is the responsibility of the coolant manufacturer to provide sources of compatible SCAs. It is the responsibility of the coolant manufacturer and SCA manufacturer to demonstrate a positive influence on reducing cavitation corrosion in an operating diesel engine.Note: These coolants WILL require a treatment with a supplemental coolant additive on a maintenance basis.Note: When adding SCA at initial fill to a coolant/antifreeze that only meets the "ASTM D4985", it is a collective responsibility of the user, coolant manufacturer, and SCA manufacturer to ensure the SCA is compatible with the antifreeze/coolant based on the recommendations provided by the coolant manufacturer and SCA manufacturer. One of the test methods required to be used to help ensure SCA compatibility with the antifreeze/coolant concentrate is "ASTM D5828-97". 6% SCA in the solution that is 60 parts antifreeze/coolant of interest, 34 parts water, and 6 parts SCA must have no more than 0.1 mL of formed insolubles. 12% SCA in a solution that is 60 parts antifreeze/coolant of interest, 28 parts water, and 12 parts SCA must have no more than 2 mL of formed insolubles. The SCA manufacturer is responsible for ensuring their SCA is compatible with water meeting the "Caterpillar Minimum Acceptable Water Quality Requirements" as found in this Special Publication and as found in "ASTM D6210-06", Table X1.1.
All Cat diesel engines equipped with air-to-air aftercooling (ATAAC) require a minimum of 30 percent glycol in order to help prevent water pump cavitation.
Note: Refer to the engine Operation and Maintenance Manual for exceptions.
Table 1
Service Life Before Flushing and Before Refilling    
Coolant     Service Life (1) (2) (3)    
Cat ELC     965,606 kilometers (600,000 miles)
12000 hours
6 years (4)    
Commercial coolant that meets the Caterpillar EC-1 specification    
482,803 kilometers (300,000 miles)
6000 hours
6 years (5)    
Cat DEAC    
321,869 kilometers (200,000 miles)
3000 hours
3 years    
Commercial Heavy-Duty Coolant/Antifreeze that meets "ASTM D4985" or "ASTM D6210"    
241,402 kilometers (150,000 miles)
3000 hours
1 year
Have questions with 101607-6450?
Group cross 101607-6450 ZEXEL
Mitsubishi
Mitsubishi
101607-6450
9 400 615 702
ME077803
INJECTION-PUMP ASSEMBLY
6D16
6D16