Information injection-pump assembly
ZEXEL
101607-6360
1016076360
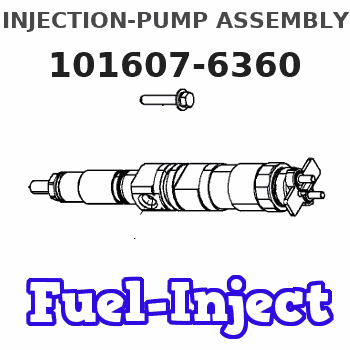
Rating:
Service parts 101607-6360 INJECTION-PUMP ASSEMBLY:
1.
_
6.
COUPLING PLATE
7.
COUPLING PLATE
8.
_
9.
_
11.
Nozzle and Holder
ME076000
12.
Open Pre:MPa(Kqf/cm2)
21.6{220}
15.
NOZZLE SET
Include in #1:
101607-6360
as INJECTION-PUMP ASSEMBLY
Include in #2:
104746-6941
as _
Cross reference number
ZEXEL
101607-6360
1016076360
Zexel num
Bosch num
Firm num
Name
101607-6360
INJECTION-PUMP ASSEMBLY
Calibration Data:
Adjustment conditions
Test oil
1404 Test oil ISO4113 or {SAEJ967d}
1404 Test oil ISO4113 or {SAEJ967d}
Test oil temperature
degC
40
40
45
Nozzle and nozzle holder
105780-8140
Bosch type code
EF8511/9A
Nozzle
105780-0000
Bosch type code
DN12SD12T
Nozzle holder
105780-2080
Bosch type code
EF8511/9
Opening pressure
MPa
17.2
Opening pressure
kgf/cm2
175
Injection pipe
Outer diameter - inner diameter - length (mm) mm 6-2-600
Outer diameter - inner diameter - length (mm) mm 6-2-600
Overflow valve
131424-5520
Overflow valve opening pressure
kPa
255
221
289
Overflow valve opening pressure
kgf/cm2
2.6
2.25
2.95
Tester oil delivery pressure
kPa
157
157
157
Tester oil delivery pressure
kgf/cm2
1.6
1.6
1.6
Direction of rotation (viewed from drive side)
Left L
Left L
Injection timing adjustment
Direction of rotation (viewed from drive side)
Left L
Left L
Injection order
1-5-3-6-
2-4
Pre-stroke
mm
3.3
3.25
3.35
Beginning of injection position
Governor side NO.1
Governor side NO.1
Difference between angles 1
Cal 1-5 deg. 60 59.5 60.5
Cal 1-5 deg. 60 59.5 60.5
Difference between angles 2
Cal 1-3 deg. 120 119.5 120.5
Cal 1-3 deg. 120 119.5 120.5
Difference between angles 3
Cal 1-6 deg. 180 179.5 180.5
Cal 1-6 deg. 180 179.5 180.5
Difference between angles 4
Cyl.1-2 deg. 240 239.5 240.5
Cyl.1-2 deg. 240 239.5 240.5
Difference between angles 5
Cal 1-4 deg. 300 299.5 300.5
Cal 1-4 deg. 300 299.5 300.5
Injection quantity adjustment
Adjusting point
-
Rack position
11.4
Pump speed
r/min
700
700
700
Each cylinder's injection qty
mm3/st.
54.5
52.9
56.1
Basic
*
Fixing the rack
*
Standard for adjustment of the maximum variation between cylinders
*
Injection quantity adjustment_02
Adjusting point
D
Rack position
8.7+-0.5
Pump speed
r/min
500
500
500
Each cylinder's injection qty
mm3/st.
7.6
6.5
8.7
Fixing the rack
*
Standard for adjustment of the maximum variation between cylinders
*
Injection quantity adjustment_03
Adjusting point
A
Rack position
R1(11.4)
Pump speed
r/min
700
700
700
Average injection quantity
mm3/st.
54.5
53.5
55.5
Basic
*
Fixing the lever
*
Injection quantity adjustment_04
Adjusting point
B
Rack position
R1+0.4
Pump speed
r/min
1450
1450
1450
Average injection quantity
mm3/st.
79.8
75.8
83.8
Fixing the lever
*
Injection quantity adjustment_05
Adjusting point
C
Rack position
R1(11.4)
Pump speed
r/min
600
600
600
Average injection quantity
mm3/st.
48.5
44.5
52.5
Fixing the lever
*
Injection quantity adjustment_06
Adjusting point
I
Rack position
14.3+-0.
5
Pump speed
r/min
100
100
100
Average injection quantity
mm3/st.
73
63
83
Fixing the lever
*
Rack limit
*
Injection quantity adjustment_07
Adjusting point
H
Rack position
9.5+-0.5
Pump speed
r/min
275
275
275
Each cylinder's injection qty
mm3/st.
8.7
7.4
10
Fixing the rack
*
Remarks
(check)
(check)
Timer adjustment
Pump speed
r/min
900--
Advance angle
deg.
0
0
0
Remarks
Start
Start
Timer adjustment_02
Pump speed
r/min
850
Advance angle
deg.
0.5
Timer adjustment_03
Pump speed
r/min
1200
Advance angle
deg.
2.7
2.2
3.2
Timer adjustment_04
Pump speed
r/min
1500
Advance angle
deg.
5
4.5
5.5
Remarks
Finish
Finish
Test data Ex:
Governor adjustment
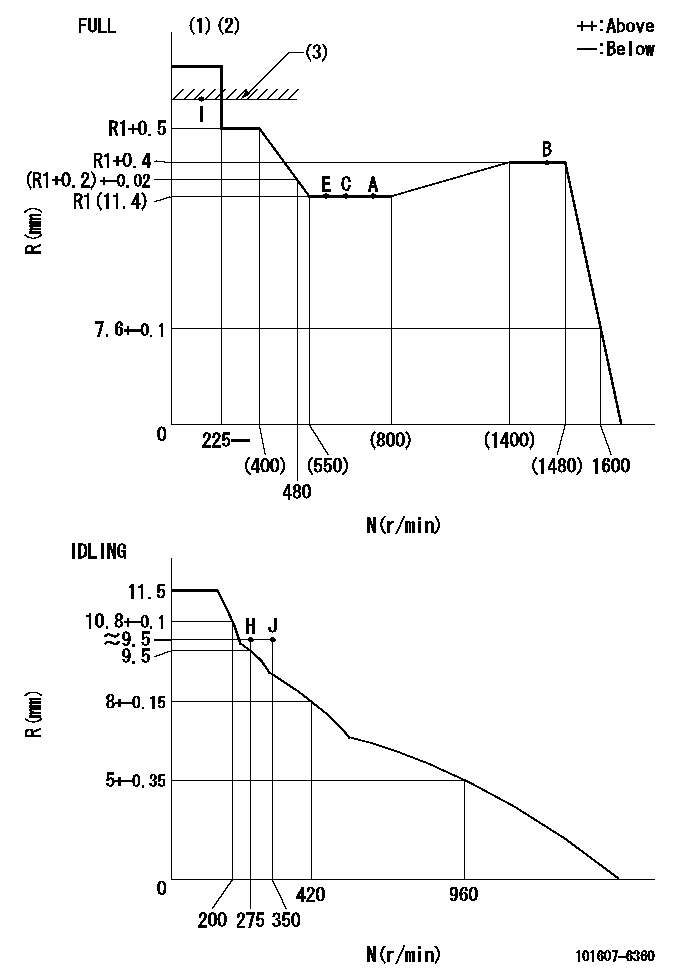
N:Pump speed
R:Rack position (mm)
(1)Torque cam stamping: T1
(2)Tolerance for racks not indicated: +-0.05mm.
(3)RACK LIMIT
----------
T1=D53
----------
----------
T1=D53
----------
Speed control lever angle

F:Full speed
I:Idle
(1)Stopper bolt set position 'H'
----------
----------
a=18.5deg+-5deg b=41deg+-3deg
----------
----------
a=18.5deg+-5deg b=41deg+-3deg
Stop lever angle
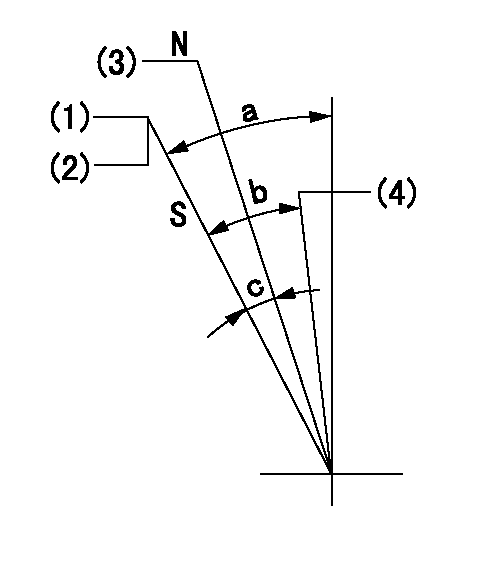
N:Engine manufacturer's normal use
S:Stop the pump.
(1)Set the stopper bolt at pump speed = aa and rack position = bb (non-injection rack position). Confirm non-injection.
(2)After setting the stopper bolt, confirm non-injection at speed cc. Rack position = dd (non-injection rack position).
(3)Rack position = approximately ee (speed lever full, speed = ff).
(4)Free (at delivery)
----------
aa=1450r/min bb=4.7-0.5mm cc=275r/min dd=(6.3)mm ee=15mm ff=0r/min
----------
a=38.5deg+-5deg b=(29deg) c=17deg+-5deg
----------
aa=1450r/min bb=4.7-0.5mm cc=275r/min dd=(6.3)mm ee=15mm ff=0r/min
----------
a=38.5deg+-5deg b=(29deg) c=17deg+-5deg
0000001501 LEVER
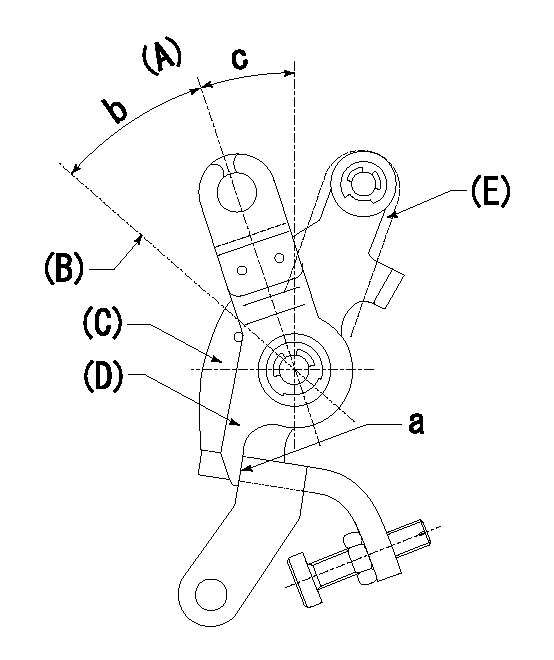
(A) Idle
(B) Full speed
(C) Base lever
(D) Accelerator lever
(E) Accelerator lever delivery position
1. Measure speed lever angle
(1)Measure the angle when the accelerator lever (D) contacted the base lever (C) at a.
----------
----------
b=41deg+-3deg c=18.5deg+-5deg
----------
----------
b=41deg+-3deg c=18.5deg+-5deg
Timing setting

(1)Pump vertical direction
(2)Position of timer's tooth at No 1 cylinder's beginning of injection
(3)B.T.D.C.: aa
(4)-
----------
aa=16deg
----------
a=(1deg)
----------
aa=16deg
----------
a=(1deg)
Information:
Oils that have more than 1% total sulfated ash should not be used in aftertreatment device equipped engines.In order to achieve expected ash service intervals, performance, and life, aftertreatment device equipped diesel engines require the use of Cat DEO-ULS or oils meeting the Cat ECF-3 specification and the API CJ-4 oil category. Use of oils with more than 1% total sulfated ash in aftertreatment device equipped engines will cause the need for more frequent ash service intervals, and/or cause loss of performance. Refer to your engine specific Operation and Maintenance Manual, and refer to your aftertreatment device documentation for additional guidance.
API category oils that have not met the requirements of at least one Cat ECF specification may cause reduced engine life.
In selecting oil for any engine application, both the oil viscosity and oil performance category/specification as specified by the engine manufacturer must be defined and satisfied. Using only one of these parameters will not sufficiently define oil for an engine application.
In order to make the proper diesel engine oil viscosity grade choice, refer to the applicable “Lubricant Viscosities for Ambient Temperatures” table in this Special Publication.
Failure to follow these oil recommendations can cause shortened engine service life due to deposits and/or excessive wear.
Total Base Number (TBN) and Fuel Sulfur Levels for Direct Injection (DI) Diesel Engines
The minimum required Total Base Number (TBN) for oil depends on the fuel sulfur level. The TBN for new oil is typically determined by the "ASTM D2896" procedure. For direct injection engines that use distillate fuel, the following guidelines apply.
Table 3
TBN recommendations for applications in Cat engines
Fuel Sulfur Level percent (ppm) Cat Engine Oils TBN of Commercial Engine Oils
≤0.05 percent (≤500 ppm) Cat DEO-ULS, Cat DEO Min 7
0. 1 - 0.05 percent (1000-500 ppm) Cat DEO-ULS, Cat DEO Min 7
Above 0.1 percent (above 1000 ppm) Cat DEO Min 10 Reaching one half of new oil TBN is one of the condemning factors for diesel engine oil. In order to help provide the best protection for your engine, Cat S O S Services oil analysis is the preferred method for determining oil life. TBN of the oil is typically measured using "ASTM D2896" and/or the "ASTM D4739" test methods. It is recommended to change the oil when one half of new oil TBN with either method is reached.For example, new oil with a TBN of 10 by "ASTM D2896" should be changed when, during use, the TBN deteriorates to 5 as determined by the "ASTM D2896" test method. New oil with a TBN of 10 by "ASTM D4739" should be changed when, during use, the TBN deteriorates to 5 as determined by the "ASTM D4739" test method.Note: TBN is also commonly referred to as Base Number (BN).Excessive piston deposits can be produced by oil with a high TBN and/or high ash. These deposits can lead to a loss of control of the oil consumption and to the polishing of the cylinder bore.The use of Cat S O S Services oil analysis helps the environmental
Have questions with 101607-6360?
Group cross 101607-6360 ZEXEL
Mitsubishi
Mitsubishi
Mitsubishi
101607-6360
INJECTION-PUMP ASSEMBLY