Information injection-pump assembly
BOSCH
F 019 Z10 239
f019z10239
ZEXEL
101607-6291
1016076291
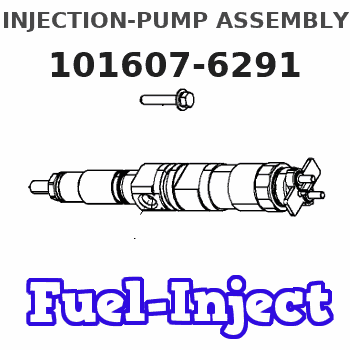
Rating:
Service parts 101607-6291 INJECTION-PUMP ASSEMBLY:
1.
_
6.
COUPLING PLATE
7.
COUPLING PLATE
8.
_
9.
_
10.
NOZZLE AND HOLDER ASSY
11.
Nozzle and Holder
12.
Open Pre:MPa(Kqf/cm2)
13.
NOZZLE-HOLDER
14.
NOZZLE
15.
NOZZLE SET
Include in #1:
101607-6291
as INJECTION-PUMP ASSEMBLY
Include in #2:
104746-6810
as _
Cross reference number
BOSCH
F 019 Z10 239
f019z10239
ZEXEL
101607-6291
1016076291
Zexel num
Bosch num
Firm num
Name
Calibration Data:
Adjustment conditions
Test oil
1404 Test oil ISO4113 or {SAEJ967d}
1404 Test oil ISO4113 or {SAEJ967d}
Test oil temperature
degC
40
40
45
Nozzle and nozzle holder
105780-8140
Bosch type code
EF8511/9A
Nozzle
105780-0000
Bosch type code
DN12SD12T
Nozzle holder
105780-2080
Bosch type code
EF8511/9
Opening pressure
MPa
17.2
Opening pressure
kgf/cm2
175
Injection pipe
Outer diameter - inner diameter - length (mm) mm 6-2-600
Outer diameter - inner diameter - length (mm) mm 6-2-600
Overflow valve
131424-5520
Overflow valve opening pressure
kPa
255
221
289
Overflow valve opening pressure
kgf/cm2
2.6
2.25
2.95
Tester oil delivery pressure
kPa
157
157
157
Tester oil delivery pressure
kgf/cm2
1.6
1.6
1.6
Direction of rotation (viewed from drive side)
Left L
Left L
Injection timing adjustment
Direction of rotation (viewed from drive side)
Left L
Left L
Injection order
1-5-3-6-
2-4
Pre-stroke
mm
3.3
3.25
3.35
Beginning of injection position
Governor side NO.1
Governor side NO.1
Difference between angles 1
Cal 1-5 deg. 60 59.5 60.5
Cal 1-5 deg. 60 59.5 60.5
Difference between angles 2
Cal 1-3 deg. 120 119.5 120.5
Cal 1-3 deg. 120 119.5 120.5
Difference between angles 3
Cal 1-6 deg. 180 179.5 180.5
Cal 1-6 deg. 180 179.5 180.5
Difference between angles 4
Cyl.1-2 deg. 240 239.5 240.5
Cyl.1-2 deg. 240 239.5 240.5
Difference between angles 5
Cal 1-4 deg. 300 299.5 300.5
Cal 1-4 deg. 300 299.5 300.5
Injection quantity adjustment
Adjusting point
-
Rack position
11.2
Pump speed
r/min
850
850
850
Each cylinder's injection qty
mm3/st.
57.7
56
59.4
Basic
*
Fixing the rack
*
Standard for adjustment of the maximum variation between cylinders
*
Injection quantity adjustment_02
Adjusting point
H
Rack position
9.5+-0.5
Pump speed
r/min
275
275
275
Each cylinder's injection qty
mm3/st.
13.7
11.6
15.8
Fixing the rack
*
Standard for adjustment of the maximum variation between cylinders
*
Injection quantity adjustment_03
Adjusting point
A
Rack position
R1(11.2)
Pump speed
r/min
850
850
850
Average injection quantity
mm3/st.
57.7
56.7
58.7
Basic
*
Fixing the lever
*
Injection quantity adjustment_04
Adjusting point
B
Rack position
R1+0.1
Pump speed
r/min
1450
1450
1450
Average injection quantity
mm3/st.
72.6
68.6
76.6
Fixing the lever
*
Injection quantity adjustment_05
Adjusting point
C
Rack position
R1+0.8
Pump speed
r/min
500
500
500
Average injection quantity
mm3/st.
59.7
55.7
63.7
Fixing the lever
*
Injection quantity adjustment_06
Adjusting point
D
Rack position
R1+1.25
Pump speed
r/min
300
300
300
Average injection quantity
mm3/st.
57.1
53.1
61.1
Fixing the lever
*
Injection quantity adjustment_07
Adjusting point
I
Rack position
-
Pump speed
r/min
100
100
100
Average injection quantity
mm3/st.
140
130
150
Fixing the lever
*
Rack limit
*
Timer adjustment
Pump speed
r/min
1250--
Advance angle
deg.
0
0
0
Remarks
Start
Start
Timer adjustment_02
Pump speed
r/min
1200
Advance angle
deg.
0.5
Timer adjustment_03
Pump speed
r/min
1400
Advance angle
deg.
5
4.5
5.5
Remarks
Finish
Finish
Test data Ex:
Governor adjustment
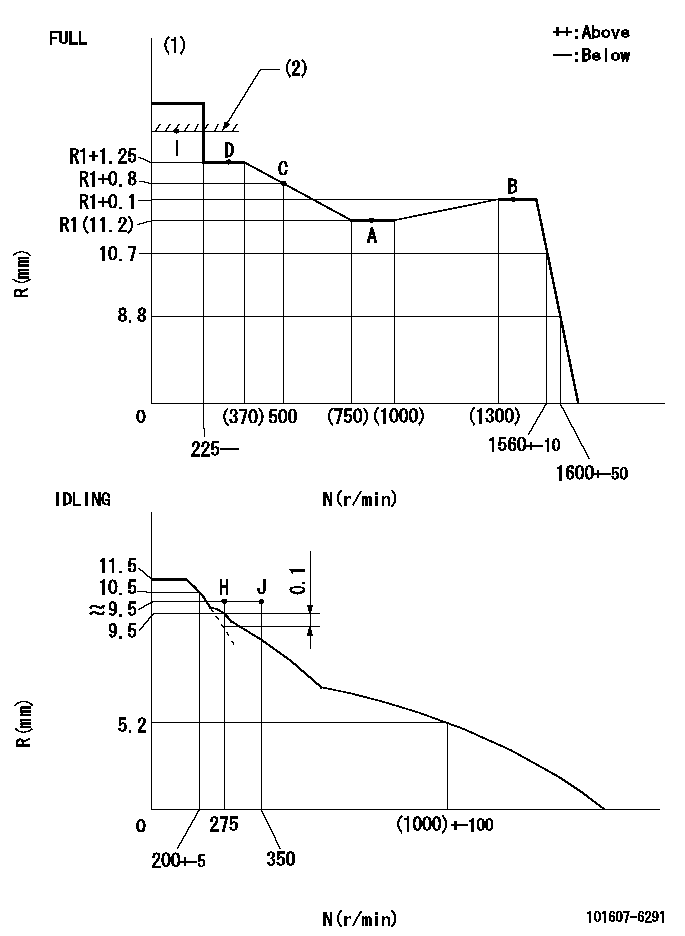
N:Pump speed
R:Rack position (mm)
(1)Torque cam stamping: T1
(2)RACK LIMIT
----------
T1=F21
----------
----------
T1=F21
----------
Speed control lever angle

F:Full speed
I:Idle
(1)Use the hole at R = aa
(2)Stopper bolt set position 'H'
----------
aa=29mm
----------
a=24deg+-5deg b=41deg+-3deg
----------
aa=29mm
----------
a=24deg+-5deg b=41deg+-3deg
Stop lever angle

N:Engine manufacturer's normal use
S:Stop the pump.
(1)Set the stopper bolt so that speed = aa and rack position = bb and confirm non-injection.
(2)After setting the stopper bolt, confirm non-injection at speed = cc. Rack position = actual (non-injection rack position).
(3)Rack position = approximately dd
(4)Free (at delivery)
(5)Use the hole above R = ee
----------
aa=1550r/min bb=7-0.5mm cc=275r/min dd=(16.8)mm ee=50mm
----------
a=36.5deg+-5deg b=(25deg) c=17deg+-5deg
----------
aa=1550r/min bb=7-0.5mm cc=275r/min dd=(16.8)mm ee=50mm
----------
a=36.5deg+-5deg b=(25deg) c=17deg+-5deg
0000001501 MICRO SWITCH
Adjust the bolt to obtain the following lever position when the micro-switch is OFF.
1. Microswitch adjustment (OPEN type)
Confirm with the lever angle at full.
(1)Speed N1
(2)Rack position Ra
----------
N1=1600r/min Ra=8.8+-0.1mm
----------
----------
N1=1600r/min Ra=8.8+-0.1mm
----------
0000001601 RACK SENSOR

V1:Supply voltage
V2f:Full side output voltage
V2i:Idle side output voltage
(A) Black
(B) Yellow
(C) Red
(D) Trimmer
(E): Shaft
(F) Nut
(G) Load lever
1. Load sensor adjustment
(1)Connect as shown in the above diagram and apply supply voltage V1.
(2)Hold the load lever (G) against the full side.
(3)Turn the shaft so that the voltage between (A) and (B) is V2.
(4)Hold the load lever (G) against the idle side.
(5)Adjust (D) so that the voltage between (A) and (B) is V2i.
(6)Repeat the above adjustments.
(7)Tighten the nut (F) at the point satisfying the standards.
(8)Hold the load lever against the full side stopper and the idle side stopper.
(9)At this time, confirm that the full side output voltage is V2f and the idle side output voltage is V2i.
----------
V1=3.57+-0.02V V2f=3+0.05V V2i=1+0.1V
----------
----------
V1=3.57+-0.02V V2f=3+0.05V V2i=1+0.1V
----------
0000001701 LEVER
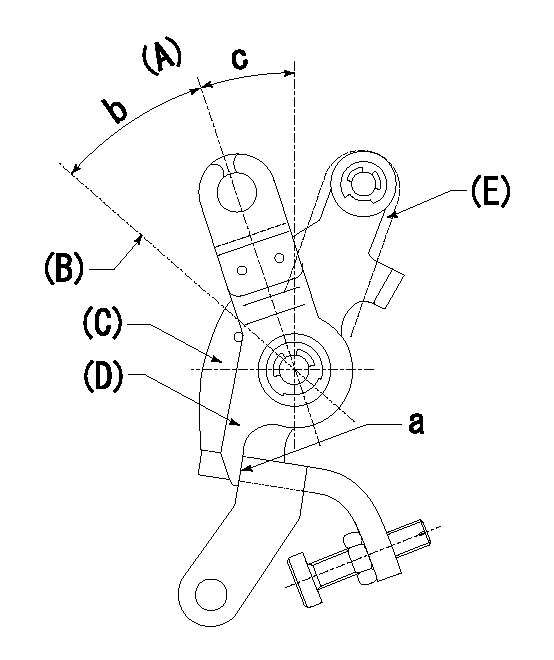
(A) Idle
(B) Full speed
(C) Base lever
(D) Accelerator lever
(E) Accelerator lever delivery position
1. Measure speed lever angle
(1)Measure the angle when the accelerator lever (D) contacted the base lever (C) at a.
----------
----------
b=41deg+-3deg c=24deg+-5deg
----------
----------
b=41deg+-3deg c=24deg+-5deg
Timing setting

(1)Pump vertical direction
(2)Position of timer's tooth at No 1 cylinder's beginning of injection
(3)B.T.D.C.: aa
(4)-
----------
aa=13deg
----------
a=(0deg)
----------
aa=13deg
----------
a=(0deg)
Information:
Touchscreen Serial Port Usage
The optional touchscreen controller for a monitor connects internally to the "COM2" serial port. The touchscreen is configured at the factory with the proper "COM2" and touchscreen driver settings. Therefore, no configuration by the user is required. If the settings are corrupted, reset the "COM2" serial port to the following settings:
9600 bps
8 data bits
1 stop bit
no parityDriver Software
The touchscreen driver is already loaded on the monitor. The driver software is also provided on a floppy disk.Note: The Elo TouchSystems touchscreen utility defaults to the "COM1" serial port setting. Change the setting to the "COM2" serial port when the touchscreen driver is reinstalled.Resistive Touchsceen Technology
Resistive touchscreens are activated when pressure is applied to the touchscreen by the finger of an operator. You can operate a resistive touchsceen while you wear gloves.Note: Do not use sharp instruments to activate the touchscreen. Scratching the surface of the touchscreen could damage the unit.Resistive touchscreens consist of the following layers:
A lower layer (glass substrate) with a resistive coating and an applied voltage
An upper layer (cover sheet) with conductive coating
Clear spacer dots separate the two layers.The upper layer is pressed onto the lower layer by the user. The upper layer receives the voltage that is applied to the lower layer. The touchscreen controller detects the change in voltage on the upper layer. The touchscreen controller alternates the voltage horizontally through the layers. The touchscreen controller alternates the voltage vertically through the layers. The voltage that is transferred to the upper layer is proportional to the location of the touch on the screen.Calibrating the Touchscreen
The touchscreen that is supplied with the monitor is factory installed and calibrated. If the touchscreen needs to be recalibrated, perform the following procedure:
Locate the Elo calibration utility in the Control Panel or insert the touchscreen driver diskette in the floppy disk drive of the monitor.
Run the Elo calibration utility. Use appropriate commands for the operating system.
Follow the instructions in the Elo calibration utility in order to complete the calibration process.Maintenance
Routine Cleaning
Clean the surface of the touchscreen with any glass cleaning solution. Use a cloth that is soft and non-abrasive.Note: Because the touchscreen is sensitive to pressure, directing strong flow of water at the touchscreen during a washdown may activate the touchscreen.
The optional touchscreen controller for a monitor connects internally to the "COM2" serial port. The touchscreen is configured at the factory with the proper "COM2" and touchscreen driver settings. Therefore, no configuration by the user is required. If the settings are corrupted, reset the "COM2" serial port to the following settings:
9600 bps
8 data bits
1 stop bit
no parityDriver Software
The touchscreen driver is already loaded on the monitor. The driver software is also provided on a floppy disk.Note: The Elo TouchSystems touchscreen utility defaults to the "COM1" serial port setting. Change the setting to the "COM2" serial port when the touchscreen driver is reinstalled.Resistive Touchsceen Technology
Resistive touchscreens are activated when pressure is applied to the touchscreen by the finger of an operator. You can operate a resistive touchsceen while you wear gloves.Note: Do not use sharp instruments to activate the touchscreen. Scratching the surface of the touchscreen could damage the unit.Resistive touchscreens consist of the following layers:
A lower layer (glass substrate) with a resistive coating and an applied voltage
An upper layer (cover sheet) with conductive coating
Clear spacer dots separate the two layers.The upper layer is pressed onto the lower layer by the user. The upper layer receives the voltage that is applied to the lower layer. The touchscreen controller detects the change in voltage on the upper layer. The touchscreen controller alternates the voltage horizontally through the layers. The touchscreen controller alternates the voltage vertically through the layers. The voltage that is transferred to the upper layer is proportional to the location of the touch on the screen.Calibrating the Touchscreen
The touchscreen that is supplied with the monitor is factory installed and calibrated. If the touchscreen needs to be recalibrated, perform the following procedure:
Locate the Elo calibration utility in the Control Panel or insert the touchscreen driver diskette in the floppy disk drive of the monitor.
Run the Elo calibration utility. Use appropriate commands for the operating system.
Follow the instructions in the Elo calibration utility in order to complete the calibration process.Maintenance
Routine Cleaning
Clean the surface of the touchscreen with any glass cleaning solution. Use a cloth that is soft and non-abrasive.Note: Because the touchscreen is sensitive to pressure, directing strong flow of water at the touchscreen during a washdown may activate the touchscreen.