Information injection-pump assembly
BOSCH
9 400 615 650
9400615650
ZEXEL
101607-1881
1016071881
MITSUBISHI
ME076883
me076883
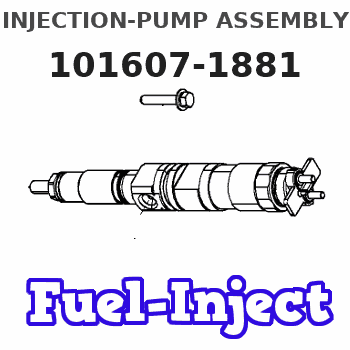
Rating:
Service parts 101607-1881 INJECTION-PUMP ASSEMBLY:
1.
_
6.
COUPLING PLATE
7.
COUPLING PLATE
8.
_
9.
_
11.
Nozzle and Holder
ME076953
12.
Open Pre:MPa(Kqf/cm2)
15.7{160}/21.6{220}
14.
NOZZLE
Cross reference number
BOSCH
9 400 615 650
9400615650
ZEXEL
101607-1881
1016071881
MITSUBISHI
ME076883
me076883
Zexel num
Bosch num
Firm num
Name
Calibration Data:
Adjustment conditions
Test oil
1404 Test oil ISO4113 or {SAEJ967d}
1404 Test oil ISO4113 or {SAEJ967d}
Test oil temperature
degC
40
40
45
Nozzle and nozzle holder
105780-8140
Bosch type code
EF8511/9A
Nozzle
105780-0000
Bosch type code
DN12SD12T
Nozzle holder
105780-2080
Bosch type code
EF8511/9
Opening pressure
MPa
17.2
Opening pressure
kgf/cm2
175
Injection pipe
Outer diameter - inner diameter - length (mm) mm 6-2-600
Outer diameter - inner diameter - length (mm) mm 6-2-600
Overflow valve
131424-8420
Overflow valve opening pressure
kPa
255
221
289
Overflow valve opening pressure
kgf/cm2
2.6
2.25
2.95
Tester oil delivery pressure
kPa
157
157
157
Tester oil delivery pressure
kgf/cm2
1.6
1.6
1.6
Direction of rotation (viewed from drive side)
Left L
Left L
Injection timing adjustment
Direction of rotation (viewed from drive side)
Left L
Left L
Injection order
1-5-3-6-
2-4
Pre-stroke
mm
3.2
3.15
3.25
Beginning of injection position
Governor side NO.1
Governor side NO.1
Difference between angles 1
Cal 1-5 deg. 60 59.5 60.5
Cal 1-5 deg. 60 59.5 60.5
Difference between angles 2
Cal 1-3 deg. 120 119.5 120.5
Cal 1-3 deg. 120 119.5 120.5
Difference between angles 3
Cal 1-6 deg. 180 179.5 180.5
Cal 1-6 deg. 180 179.5 180.5
Difference between angles 4
Cyl.1-2 deg. 240 239.5 240.5
Cyl.1-2 deg. 240 239.5 240.5
Difference between angles 5
Cal 1-4 deg. 300 299.5 300.5
Cal 1-4 deg. 300 299.5 300.5
Injection quantity adjustment
Adjusting point
-
Rack position
12.4
Pump speed
r/min
700
700
700
Each cylinder's injection qty
mm3/st.
113.4
110
116.8
Basic
*
Fixing the rack
*
Standard for adjustment of the maximum variation between cylinders
*
Injection quantity adjustment_02
Adjusting point
Z
Rack position
9.5+-0.5
Pump speed
r/min
600
600
600
Each cylinder's injection qty
mm3/st.
11.5
9.8
13.2
Fixing the rack
*
Standard for adjustment of the maximum variation between cylinders
*
Injection quantity adjustment_03
Adjusting point
A
Rack position
R1(12.4)
Pump speed
r/min
700
700
700
Average injection quantity
mm3/st.
113.4
112.4
114.4
Basic
*
Fixing the lever
*
Boost pressure
kPa
42.7
42.7
Boost pressure
mmHg
320
320
Injection quantity adjustment_04
Adjusting point
B
Rack position
R1+1.15
Pump speed
r/min
1350
1350
1350
Average injection quantity
mm3/st.
132.7
128.7
136.7
Fixing the lever
*
Boost pressure
kPa
42.7
42.7
Boost pressure
mmHg
320
320
Injection quantity adjustment_05
Adjusting point
C
Rack position
R2(R1-0.
4)
Pump speed
r/min
500
500
500
Average injection quantity
mm3/st.
97.5
93.5
101.5
Fixing the lever
*
Boost pressure
kPa
42.7
42.7
Boost pressure
mmHg
320
320
Boost compensator adjustment
Pump speed
r/min
400
400
400
Rack position
R2-1.2
Boost pressure
kPa
4
2.7
5.3
Boost pressure
mmHg
30
20
40
Boost compensator adjustment_02
Pump speed
r/min
400
400
400
Rack position
R2(1-0.4
)
Boost pressure
kPa
29.3
29.3
29.3
Boost pressure
mmHg
220
220
220
Timer adjustment
Pump speed
r/min
1180--
Advance angle
deg.
0
0
0
Remarks
Start
Start
Timer adjustment_02
Pump speed
r/min
1130
Advance angle
deg.
0.5
Timer adjustment_03
Pump speed
r/min
1350
Advance angle
deg.
3.5
3
4
Remarks
Finish
Finish
Test data Ex:
Governor adjustment
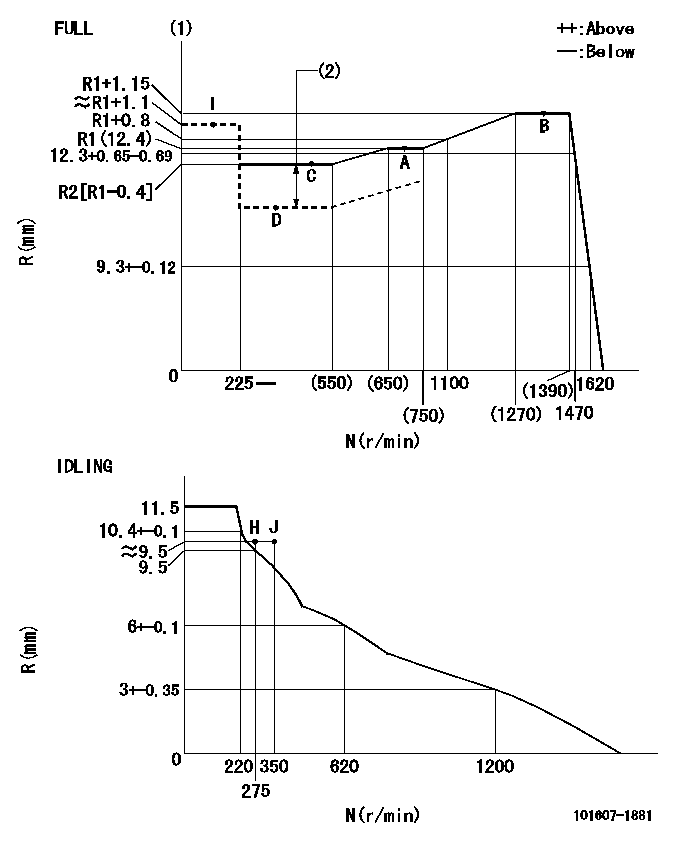
N:Pump speed
R:Rack position (mm)
(1)Torque cam stamping: T1
(2)Boost compensator stroke: BCL
----------
T1=G91 BCL=1.2+-0.1mm
----------
----------
T1=G91 BCL=1.2+-0.1mm
----------
Speed control lever angle
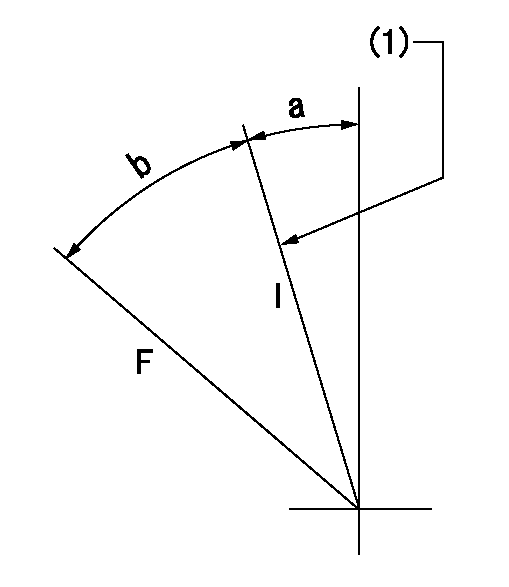
F:Full speed
I:Idle
(1)Stopper bolt set position 'H'
----------
----------
a=18.5deg+-5deg b=(41deg)+-3deg
----------
----------
a=18.5deg+-5deg b=(41deg)+-3deg
Stop lever angle
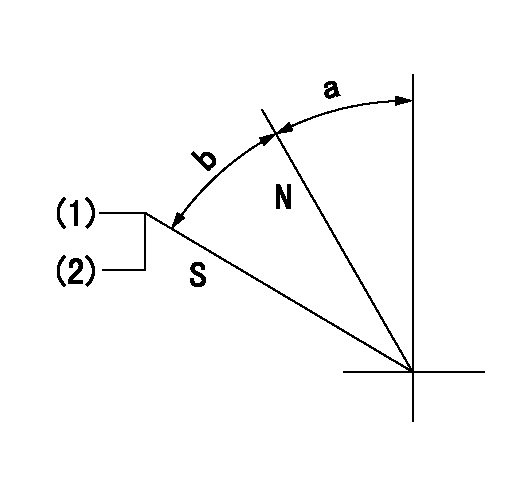
N:Pump normal
S:Stop the pump.
(1)Set the stopper bolt at pump speed = aa and rack position = bb (non-injection rack position). Confirm non-injection.
(2)After setting the stopper bolt, confirm non-injection at speed cc. Rack position = dd (non-injection rack position).
----------
aa=1350r/min bb=7-0.5mm cc=275r/min dd=(8)mm
----------
a=11.5deg+-5deg b=(28deg)+-5deg
----------
aa=1350r/min bb=7-0.5mm cc=275r/min dd=(8)mm
----------
a=11.5deg+-5deg b=(28deg)+-5deg
0000001501 LEVER
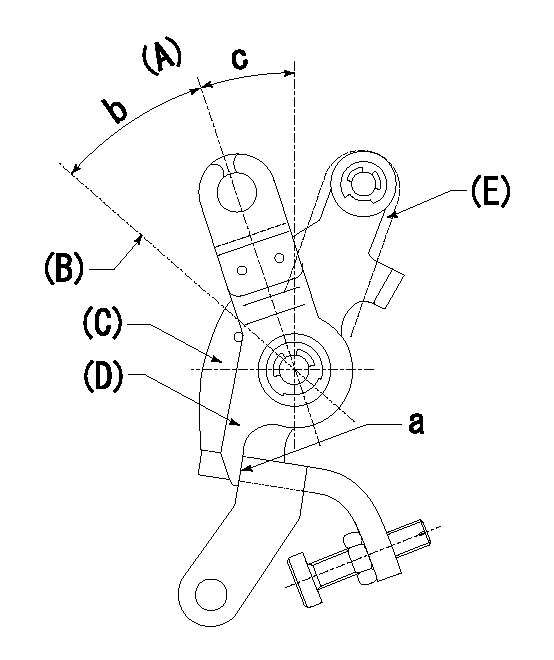
(A) Idle
(B) Full speed
(C) Base lever
(D) Accelerator lever
(E) Accelerator lever delivery position
1. Measure speed lever angle
(1)Measure the angle when the accelerator lever (D) contacted the base lever (C) at a.
----------
----------
b=(41deg)+-3deg c=18.5deg+-5deg
----------
----------
b=(41deg)+-3deg c=18.5deg+-5deg
Timing setting

(1)Pump vertical direction
(2)Position of timer's tooth at No 1 cylinder's beginning of injection
(3)B.T.D.C.: aa
(4)-
----------
aa=10deg
----------
a=(2deg)
----------
aa=10deg
----------
a=(2deg)
Information:
Problem 4
The starting motor remains engaged or the starting motor continues to run after the engine is running.
Check the components of the starting circuit.
Measure the voltages at terminal (TS-26) of the junction box while the engine is running.Result
The voltage at the terminal is zero volts.The problem is in the starting motor (SM), the pinion solenoid (PS), or the magnetic switch (MS). Repair the faulty component. STOP.
The voltage at the terminal is between 15 volts and 32 volts.The START terminals of the start/stop switch are normally closed. This is normal for an automatic start system. In a manual start system, the switches should be normally open. The switch is on terminals (SSS-1) and (SSS-2) for a normal start/stop switch. Repair the faulty switch. STOP.Problem 5
The engine shutdown occurs after the engine runs for more than 3 minutes.
Check the protection switches.
Remove the jumper that is between terminals (TS-9) and (TS-10) of the junction box.
If the engine is equipped with a low oil pressure indicator, disconnect the diode that is between terminals (TS-8) and (TS-10). The cathode lead of the diode should be connected to terminal (TS-10).
If the engine is equipped with a low oil pressure indicator, ensure that a jumper is not installed between terminals (TS-8) and (TS-9).
Start the engine.
Reconnect the jumper that is between terminals (TS-9) and (TS-10) of the junction box after the test is completed.Result
The engine starts and the engine runs.The problem is in the oil pressure switch or the water temperature contactor switch. Go to Step 5 of "Problem 1".
The engine starts but engine shutdown occurs immediately.Go to Step 1 of "Problem 3".
The engine starts and the engine runs but engine shutdown occurs after the engine runs for more than 3 minutes.Go to Step 2.
The engine cranks but the engine does not start.Go to Step 1 of "Problem 1".
Check the start/stop switch and slave relay (SR1).
Disconnect the wire in the junction box that connects terminal (SR1-85) of the slave relay (SR1) to terminal (TD-7) of the time delay relay (TD).
Crank the engine. Activate the emergency stop switch, if necessary.Result
The engine starts and the engine runs.The start/stop switch has a short circuit or a wiring problem is causing a voltage at terminal (TD-7). Reconnect the wire to the terminal. STOP.
Engine shutdown still occurs after several minutes.The contacts of (SR1) periodically close. The problem may also be with the governor or the fuel supply to the engine. Refer to the Engine Service Manual. If a 2301A Electric Governor is used, the SR1 contacts may be opening. Refer to 2301A Electric Governor Service Manual, SENR3585. Test SR1. Refer to Testing and Adjusting, "Slave Relay Test".Problem 6
Engine shutdown does not occur when a fault is detected.
Check the protection switches and the crank terminate switch of the electronic speed switch.
Reset circuit breaker (CB7).
Start the engine and run the engine at low idle.
Contact with electrical components can cause injury or death.Remove all jewelry and avoid contact with electrical components. Use properly insulated tools when working on the junction box of an
The starting motor remains engaged or the starting motor continues to run after the engine is running.
Check the components of the starting circuit.
Measure the voltages at terminal (TS-26) of the junction box while the engine is running.Result
The voltage at the terminal is zero volts.The problem is in the starting motor (SM), the pinion solenoid (PS), or the magnetic switch (MS). Repair the faulty component. STOP.
The voltage at the terminal is between 15 volts and 32 volts.The START terminals of the start/stop switch are normally closed. This is normal for an automatic start system. In a manual start system, the switches should be normally open. The switch is on terminals (SSS-1) and (SSS-2) for a normal start/stop switch. Repair the faulty switch. STOP.Problem 5
The engine shutdown occurs after the engine runs for more than 3 minutes.
Check the protection switches.
Remove the jumper that is between terminals (TS-9) and (TS-10) of the junction box.
If the engine is equipped with a low oil pressure indicator, disconnect the diode that is between terminals (TS-8) and (TS-10). The cathode lead of the diode should be connected to terminal (TS-10).
If the engine is equipped with a low oil pressure indicator, ensure that a jumper is not installed between terminals (TS-8) and (TS-9).
Start the engine.
Reconnect the jumper that is between terminals (TS-9) and (TS-10) of the junction box after the test is completed.Result
The engine starts and the engine runs.The problem is in the oil pressure switch or the water temperature contactor switch. Go to Step 5 of "Problem 1".
The engine starts but engine shutdown occurs immediately.Go to Step 1 of "Problem 3".
The engine starts and the engine runs but engine shutdown occurs after the engine runs for more than 3 minutes.Go to Step 2.
The engine cranks but the engine does not start.Go to Step 1 of "Problem 1".
Check the start/stop switch and slave relay (SR1).
Disconnect the wire in the junction box that connects terminal (SR1-85) of the slave relay (SR1) to terminal (TD-7) of the time delay relay (TD).
Crank the engine. Activate the emergency stop switch, if necessary.Result
The engine starts and the engine runs.The start/stop switch has a short circuit or a wiring problem is causing a voltage at terminal (TD-7). Reconnect the wire to the terminal. STOP.
Engine shutdown still occurs after several minutes.The contacts of (SR1) periodically close. The problem may also be with the governor or the fuel supply to the engine. Refer to the Engine Service Manual. If a 2301A Electric Governor is used, the SR1 contacts may be opening. Refer to 2301A Electric Governor Service Manual, SENR3585. Test SR1. Refer to Testing and Adjusting, "Slave Relay Test".Problem 6
Engine shutdown does not occur when a fault is detected.
Check the protection switches and the crank terminate switch of the electronic speed switch.
Reset circuit breaker (CB7).
Start the engine and run the engine at low idle.
Contact with electrical components can cause injury or death.Remove all jewelry and avoid contact with electrical components. Use properly insulated tools when working on the junction box of an