Information injection-pump assembly
BOSCH
F 01G 09U 04V
f01g09u04v
ZEXEL
101607-1041
1016071041
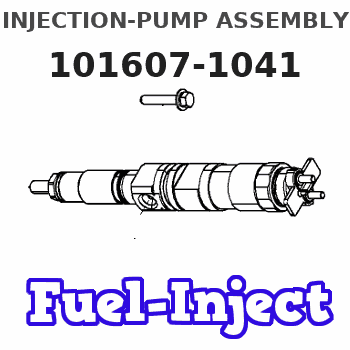
Rating:
Cross reference number
BOSCH
F 01G 09U 04V
f01g09u04v
ZEXEL
101607-1041
1016071041
Zexel num
Bosch num
Firm num
Name
Calibration Data:
Adjustment conditions
Test oil
1404 Test oil ISO4113 or {SAEJ967d}
1404 Test oil ISO4113 or {SAEJ967d}
Test oil temperature
degC
40
40
45
Nozzle and nozzle holder
105780-8140
Bosch type code
EF8511/9A
Nozzle
105780-0000
Bosch type code
DN12SD12T
Nozzle holder
105780-2080
Bosch type code
EF8511/9
Opening pressure
MPa
17.2
Opening pressure
kgf/cm2
175
Injection pipe
Outer diameter - inner diameter - length (mm) mm 6-2-600
Outer diameter - inner diameter - length (mm) mm 6-2-600
Overflow valve
131424-5520
Overflow valve opening pressure
kPa
255
221
289
Overflow valve opening pressure
kgf/cm2
2.6
2.25
2.95
Tester oil delivery pressure
kPa
157
157
157
Tester oil delivery pressure
kgf/cm2
1.6
1.6
1.6
Direction of rotation (viewed from drive side)
Left L
Left L
Injection timing adjustment
Direction of rotation (viewed from drive side)
Left L
Left L
Injection order
1-5-3-6-
2-4
Pre-stroke
mm
3.2
3.15
3.25
Beginning of injection position
Governor side NO.1
Governor side NO.1
Difference between angles 1
Cal 1-5 deg. 60 59.5 60.5
Cal 1-5 deg. 60 59.5 60.5
Difference between angles 2
Cal 1-3 deg. 120 119.5 120.5
Cal 1-3 deg. 120 119.5 120.5
Difference between angles 3
Cal 1-6 deg. 180 179.5 180.5
Cal 1-6 deg. 180 179.5 180.5
Difference between angles 4
Cyl.1-2 deg. 240 239.5 240.5
Cyl.1-2 deg. 240 239.5 240.5
Difference between angles 5
Cal 1-4 deg. 300 299.5 300.5
Cal 1-4 deg. 300 299.5 300.5
Injection quantity adjustment
Adjusting point
-
Rack position
11.6
Pump speed
r/min
850
850
850
Each cylinder's injection qty
mm3/st.
72.5
70.3
74.7
Basic
*
Fixing the rack
*
Standard for adjustment of the maximum variation between cylinders
*
Injection quantity adjustment_02
Adjusting point
H
Rack position
9.5+-0.5
Pump speed
r/min
275
275
275
Each cylinder's injection qty
mm3/st.
8.3
7.1
9.5
Fixing the rack
*
Standard for adjustment of the maximum variation between cylinders
*
Injection quantity adjustment_03
Adjusting point
A
Rack position
R1(11.6)
Pump speed
r/min
850
850
850
Average injection quantity
mm3/st.
72.5
71.5
73.5
Basic
*
Fixing the lever
*
Injection quantity adjustment_04
Adjusting point
B
Rack position
R1-0.15
Pump speed
r/min
1400
1400
1400
Average injection quantity
mm3/st.
79.5
75.5
83.5
Fixing the lever
*
Injection quantity adjustment_05
Adjusting point
C
Rack position
R1+0.65
Pump speed
r/min
500
500
500
Average injection quantity
mm3/st.
71.5
67.5
75.5
Fixing the lever
*
Injection quantity adjustment_06
Adjusting point
I
Rack position
14.8+-0.
2
Pump speed
r/min
100
100
100
Average injection quantity
mm3/st.
120
100
140
Fixing the lever
*
Rack limit
*
Timer adjustment
Pump speed
r/min
1150
Advance angle
deg.
0.5
Timer adjustment_02
Pump speed
r/min
1200
Advance angle
deg.
0.9
0.4
1.4
Timer adjustment_03
Pump speed
r/min
1380
Advance angle
deg.
5
4.5
5.5
Remarks
Finish
Finish
Test data Ex:
Governor adjustment
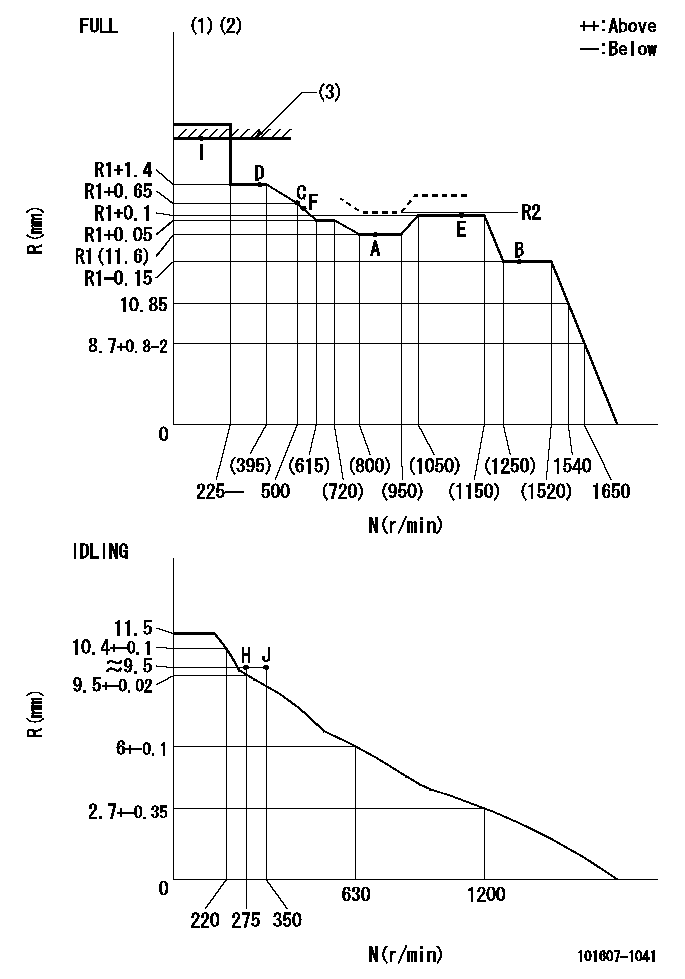
N:Pump speed
R:Rack position (mm)
(1)Torque cam stamping: T1
(2)Tolerance for racks not indicated: +-0.05mm.
(3)RACK LIMIT: RAL
----------
T1=F14 RAL=14.8+-0.2mm
----------
----------
T1=F14 RAL=14.8+-0.2mm
----------
Speed control lever angle
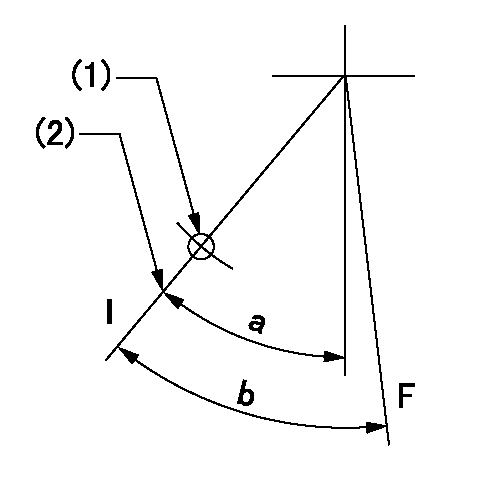
F:Full speed
I:Idle
(1)Use the hole at R = aa
(2)Stopper bolt set position 'H'
----------
aa=35mm
----------
a=33deg+-5deg b=(40deg)+-3deg
----------
aa=35mm
----------
a=33deg+-5deg b=(40deg)+-3deg
Stop lever angle
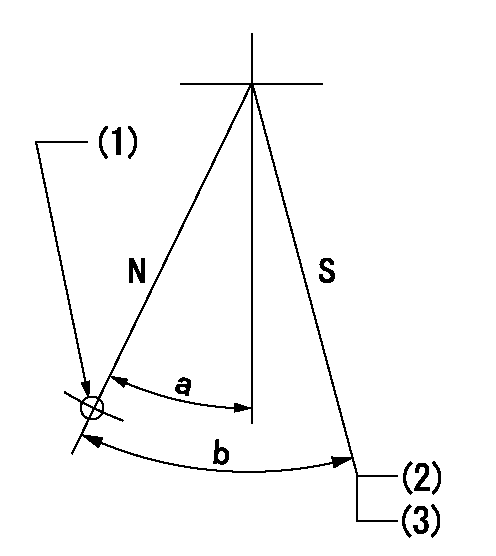
N:Pump normal
S:Stop the pump.
(1)Use the hole at R = aa
(2)Set the stopper bolt at speed = bb and rack position = cc (non-injection rack position). Confirm non-injection.
(3)After setting the stopper bolt, confirm non-injection at speed dd. Rack position = ee (non-injection rack position)
----------
aa=50mm bb=1400r/min cc=6.9-0.5mm dd=275r/min ee=(8.9)-0.5mm
----------
a=25deg+-5deg b=25deg+-5deg
----------
aa=50mm bb=1400r/min cc=6.9-0.5mm dd=275r/min ee=(8.9)-0.5mm
----------
a=25deg+-5deg b=25deg+-5deg
0000001501 MICRO SWITCH
Adjustment of the micro-switch
Adjust the bolt to obtain the following lever position when the micro-switch is ON.
(1)Speed N1
(2)Rack position Ra
----------
N1=400r/min Ra=9.2+-0.1mm
----------
----------
N1=400r/min Ra=9.2+-0.1mm
----------
0000001601 TAMPER PROOF
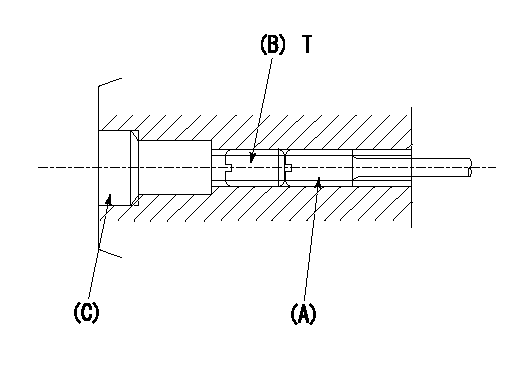
1. Method for setting tamperproof proofing
(1)After governor adjustment (torque cam phase adjustment), move the load lever to increase the full rack position to Ra.
(2)At speed N1 screw in screw (A) to obtain the rack position (actual measurement: Rb) for injection quantity Q1.
(3)Temporarily caulk using the tip of a screwdriver
(4)Confirm that the rack at that time is at Rc.
(5)Lock using setscrew (B). (Tightening torque = T)
(6)Next, coat (C) with adhesive and then pressfit.
(7)Then, readjust the full rack position using the load lever.
----------
N1=850r/min Q1=78.3+-1mm3/st Ra=(0.4)mm Rb=R2mm Rc=R2mm
----------
T=3.4~4.9N-m(0.35~0.5Kgf-m)
----------
N1=850r/min Q1=78.3+-1mm3/st Ra=(0.4)mm Rb=R2mm Rc=R2mm
----------
T=3.4~4.9N-m(0.35~0.5Kgf-m)
0000001701 LEVER

(A) Accelerator lever stopper bolt
(B) Link
(c) Nut
(D) Lever
(E) Pin
(f) lever
(G) Stopper bolt
(H) Return spring
(J) Pin (E) contacts lever.
(K) Load sensor terminal
(1)Black
(2)Blue-yellow
(3)Blue-red
Setting the accelerator lever angle, load sensor adjustment
1. Accelerator lever setting method
(1)Position the speed lever against the idle stopper bolt and fix.
(2)Screw in the accelerator lever stopper bolt (A) and back off the stopper bolt (A) from the position where the accelerator lever pin contacts the speed lever and set. (Gap: approx. 1 mm)
Tightening torque: 4.9~7 N.m {0.5~0.7 kgf.m}
2. Load sensor adjustment (See fig 1)
(1)Load sensor output measuring circuit
Apply DC5+-0.01V to the load sensor terminals and measure the output voltage.
(2)Load sensor output adjustment procedure
Hold the speed lever against the full side stopper bolt and fix. Adjust the load sensor output voltage to VF = 0.417+-0.1 V using the link (B) and then fix temporarily using nut (C).
Turn the speed lever from the idle side to the full side and confirm that output voltage VF = 0.417+-0.1 V is obtained. Confirm several times and then fix using nut (C).
Tightening torque: 3.4~4.9 N.m {0.35~0.5 kgf.m}
3. Setting the step motor's idle side stopper bolt
After adjustment in previous 1 and 2, position speed lever against idle stopper bolt and fix. Then, screw in stopper bolt G until step motor lever D's pin E contacts lever F. Back off 10+2 deg (approx. 3.5 mm) from this position and fix G. (See fig. 3)
4. Speed lever return confirmation
(1)Remove return spring (H) and confirm that the speed lever is returned to the idle position by the torsion spring.
(2)Reinstall the return spring (H) in its original position.
----------
----------
----------
----------
Timing setting

(1)Pump vertical direction
(2)Position of timer's tooth at No 1 cylinder's beginning of injection
(3)B.T.D.C.: aa
(4)-
----------
aa=11deg
----------
a=(1deg)
----------
aa=11deg
----------
a=(1deg)
Information:
Low power and engine response complaints can be caused by very different reasons and require different repairs, but are often the same complaint from the operator. A discussion with the operator is needed to help correctly diagnose whether to repair for low power or slow response. At times, full engine horsepower is available, but the operator still complains of low power. Repairs for low power would not provide a satisfactory result, and may consume many hours with expensive repairs. The actual complaint may be the engines ability to respond to a changing load or shifting gears.Normally, engine power can be measured to determine if it is within specifications. When troubleshooting a "low horsepower" complaint, if fuel consumption, timing, speeds, and manifold pressure are within specification, do not spend additional time looking for "low engine horsepower". If it is still believed that performance of the vehicle is below that expected, look for horsepower losses in the transmission, differential, clutches, parasitic loads (fan, air compressor, air conditioner, etc), tires, low fuel density or high temperatures, but not the engine.Owner/Operator Input
The following are some of the questions which should be asked before beginning any diagnosis or repair for an engine performance complaint. There Are No Hard And Fast Answers For These Questions. There are many different truck engine specifications and truck vehicle specifications which will provide acceptable results. There are also a variety of customer expectations which are acceptable. The answers to these questions will give you a better understanding and perspective on the complaint and may identify characteristics which will help pinpoint the cause of the complaint quickly. 1. Is there a particular operating condition when the complaint occurs?Low power and response complaints require different repairs. Complaints during shifting will be different from complaints of low power in certain speed ranges or in certain terrains. 2. What are the customer's expectations for fuel mileage and power and why does he have those expectations?Comparisons to other trucks on the road often have many unseen variables. If comparison to others is the basis for the complaint, you must insure that the comparison is valid. 3. What are the normal upshift and downshift rpm's?If the shift points are too high, find out why. If the driver is operating this way out of habit or because he is taught to drive that way, arrange for him to receive the Caterpillar driver training information. If his shift points are too high because of poor performance, you may be able to correct this in the engine. 4. What are the normal routes and loads for the truck?You should be looking for the amount of city versus highway driving, versus mountainous, heavy versus light loads, and cold climate versus warm climate. 5. Can the operator detect a misfire?This can lead you to a diagnosis of just one cylinder rather than an entire engine system. 6. Does the engine smoke excessively, and if so, under what conditions?Excessive smoke can give indications about engine settings and engine internal conditions.
The following are some of the questions which should be asked before beginning any diagnosis or repair for an engine performance complaint. There Are No Hard And Fast Answers For These Questions. There are many different truck engine specifications and truck vehicle specifications which will provide acceptable results. There are also a variety of customer expectations which are acceptable. The answers to these questions will give you a better understanding and perspective on the complaint and may identify characteristics which will help pinpoint the cause of the complaint quickly. 1. Is there a particular operating condition when the complaint occurs?Low power and response complaints require different repairs. Complaints during shifting will be different from complaints of low power in certain speed ranges or in certain terrains. 2. What are the customer's expectations for fuel mileage and power and why does he have those expectations?Comparisons to other trucks on the road often have many unseen variables. If comparison to others is the basis for the complaint, you must insure that the comparison is valid. 3. What are the normal upshift and downshift rpm's?If the shift points are too high, find out why. If the driver is operating this way out of habit or because he is taught to drive that way, arrange for him to receive the Caterpillar driver training information. If his shift points are too high because of poor performance, you may be able to correct this in the engine. 4. What are the normal routes and loads for the truck?You should be looking for the amount of city versus highway driving, versus mountainous, heavy versus light loads, and cold climate versus warm climate. 5. Can the operator detect a misfire?This can lead you to a diagnosis of just one cylinder rather than an entire engine system. 6. Does the engine smoke excessively, and if so, under what conditions?Excessive smoke can give indications about engine settings and engine internal conditions.