Information injection-pump assembly
ZEXEL
101606-9940
1016069940
NISSAN-DIESEL
16713Z6308
16713z6308
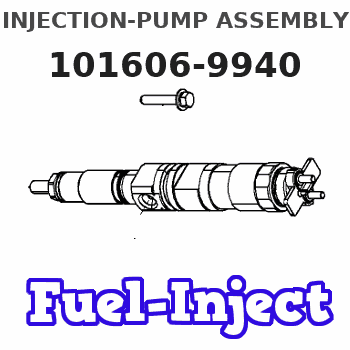
Rating:
Cross reference number
ZEXEL
101606-9940
1016069940
NISSAN-DIESEL
16713Z6308
16713z6308
Zexel num
Bosch num
Firm num
Name
Calibration Data:
Adjustment conditions
Test oil
1404 Test oil ISO4113 or {SAEJ967d}
1404 Test oil ISO4113 or {SAEJ967d}
Test oil temperature
degC
40
40
45
Nozzle and nozzle holder
105780-8140
Bosch type code
EF8511/9A
Nozzle
105780-0000
Bosch type code
DN12SD12T
Nozzle holder
105780-2080
Bosch type code
EF8511/9
Opening pressure
MPa
17.2
Opening pressure
kgf/cm2
175
Injection pipe
Outer diameter - inner diameter - length (mm) mm 6-2-600
Outer diameter - inner diameter - length (mm) mm 6-2-600
Overflow valve
131424-1520
Overflow valve opening pressure
kPa
157
123
191
Overflow valve opening pressure
kgf/cm2
1.6
1.25
1.95
Tester oil delivery pressure
kPa
157
157
157
Tester oil delivery pressure
kgf/cm2
1.6
1.6
1.6
Direction of rotation (viewed from drive side)
Right R
Right R
Injection timing adjustment
Direction of rotation (viewed from drive side)
Right R
Right R
Injection order
1-4-2-6-
3-5
Pre-stroke
mm
3
2.95
3.05
Beginning of injection position
Drive side NO.1
Drive side NO.1
Difference between angles 1
Cal 1-4 deg. 60 59.5 60.5
Cal 1-4 deg. 60 59.5 60.5
Difference between angles 2
Cyl.1-2 deg. 120 119.5 120.5
Cyl.1-2 deg. 120 119.5 120.5
Difference between angles 3
Cal 1-6 deg. 180 179.5 180.5
Cal 1-6 deg. 180 179.5 180.5
Difference between angles 4
Cal 1-3 deg. 240 239.5 240.5
Cal 1-3 deg. 240 239.5 240.5
Difference between angles 5
Cal 1-5 deg. 300 299.5 300.5
Cal 1-5 deg. 300 299.5 300.5
Injection quantity adjustment
Adjusting point
-
Rack position
11.3
Pump speed
r/min
600
600
600
Average injection quantity
mm3/st.
48.2
46.6
49.8
Max. variation between cylinders
%
0
-3.5
3.5
Basic
*
Fixing the rack
*
Standard for adjustment of the maximum variation between cylinders
*
Injection quantity adjustment_02
Adjusting point
-
Rack position
9.8+-0.5
Pump speed
r/min
300
300
300
Average injection quantity
mm3/st.
9
7.2
10.8
Max. variation between cylinders
%
0
-10
10
Fixing the rack
*
Standard for adjustment of the maximum variation between cylinders
*
Remarks
Adjust only variation between cylinders; adjust governor according to governor specifications.
Adjust only variation between cylinders; adjust governor according to governor specifications.
Injection quantity adjustment_03
Adjusting point
A
Rack position
R1(11.3)
Pump speed
r/min
600
600
600
Average injection quantity
mm3/st.
48.2
47.2
49.2
Basic
*
Fixing the lever
*
Injection quantity adjustment_04
Adjusting point
B
Rack position
R1-0.2
Pump speed
r/min
1000
1000
1000
Average injection quantity
mm3/st.
63.6
60.4
66.8
Fixing the lever
*
Injection quantity adjustment_05
Adjusting point
I
Rack position
-
Pump speed
r/min
100
100
100
Average injection quantity
mm3/st.
80
80
90
Fixing the lever
*
Rack limit
*
Timer adjustment
Pump speed
r/min
(1140)
Advance angle
deg.
0
0
0
Remarks
Start
Start
Timer adjustment_02
Pump speed
r/min
1500
Advance angle
deg.
4
3.5
4.5
Remarks
Finish
Finish
Test data Ex:
Governor adjustment
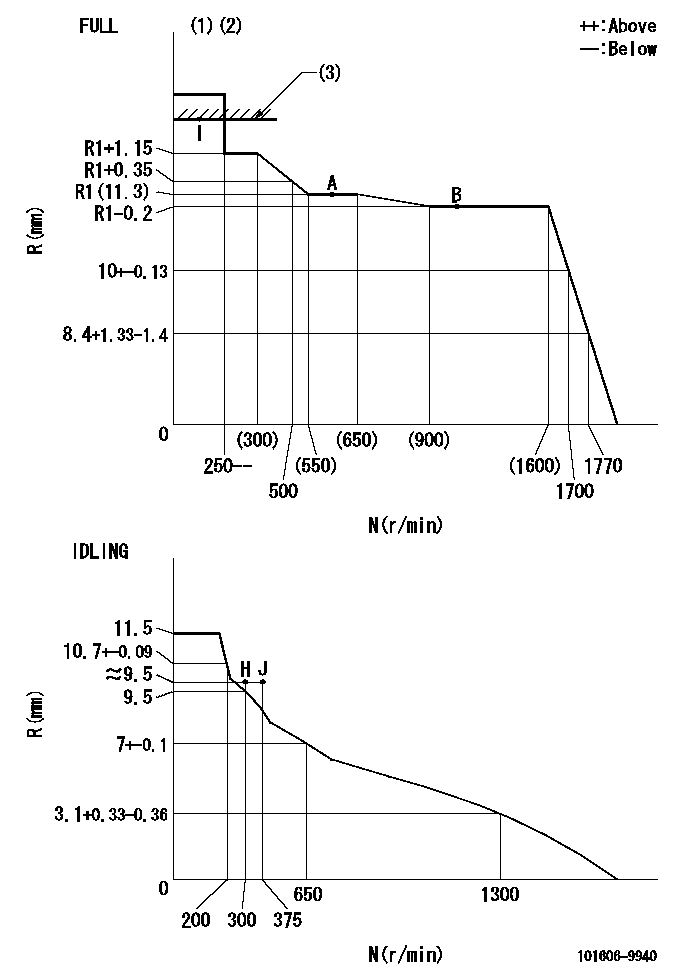
N:Pump speed
R:Rack position (mm)
(1)Torque cam stamping: T1
(2)Tolerance for racks not indicated: +-0.05mm.
(3)RACK LIMIT
----------
T1=C42
----------
----------
T1=C42
----------
Speed control lever angle

F:Full speed
I:Idle
(1)Use the hole at R = aa
(2)Stopper bolt set position 'H'
----------
aa=36mm
----------
a=26.5deg+-5deg b=40deg+-3deg
----------
aa=36mm
----------
a=26.5deg+-5deg b=40deg+-3deg
Stop lever angle
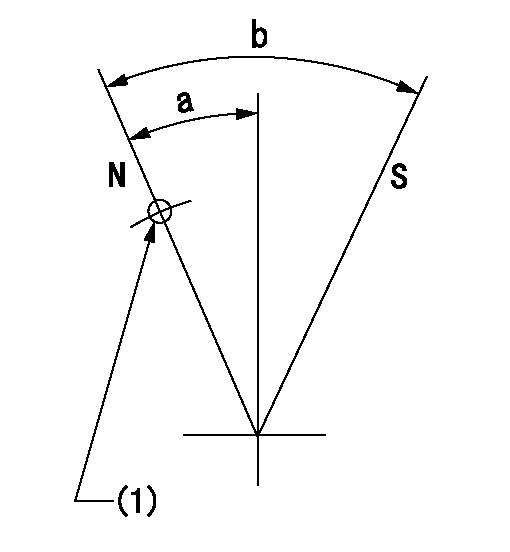
N:Pump normal
S:Stop the pump.
(1)Use the pin at R = aa
----------
aa=42mm
----------
a=27deg+-5deg b=40deg+-5deg
----------
aa=42mm
----------
a=27deg+-5deg b=40deg+-5deg
Timing setting
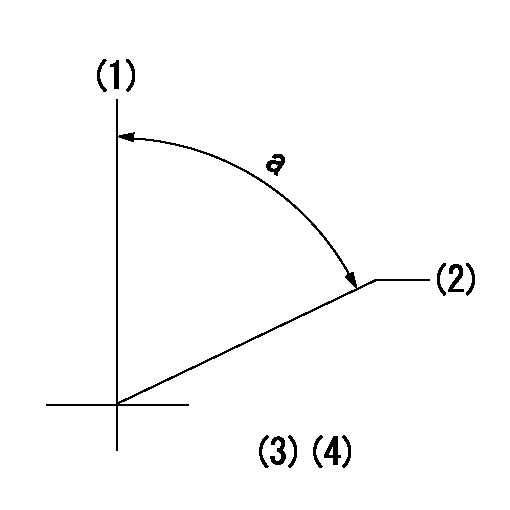
(1)Pump vertical direction
(2)Position of timer's threaded hole at No 1 cylinder's beginning of injection
(3)-
(4)-
----------
----------
a=(60deg)
----------
----------
a=(60deg)
Information:
Start By:a. remove engine balancer group (3114 Engines)b. remove oil pump (3116 Engines) 1. Remove bolts (1), the washers and bearing cap (2). Remove the lower main bearing half from the cap.
If the crankshaft is turned in the wrong direction during upper main bearing half removal, the tab of the bearing will be pushed between the crankshaft and the cylinder block. This can cause result in damage to either or both the crankshaft and the cylinder block.
Both the center and two end main journals have no oil hole. To remove these upper main bearing halves, put a thin piece of soft material, (that will not damage the crankshaft journal), against the end of the bearing half, opposite the tab. Hit the bearing with the soft material until the tab of the bearing is free from the groove in the cylinder block.2. Remove the upper half of the main bearings as follows: a. Turn the crankshaft until Tool (A) can be installed in the crankshaft journal. Install Tool (A) as shown.b. Turn the crankshaft in the direction which will push the upper main bearing half out, tab end first.c. Check the condition of the main bearings. Refer to "Guideline For Reusable Parts, Main & Connecting Rod Bearings", Form No. SEBF8009 and SEBD0531 as guide for checking bearing condition. The following steps are for the installation of the crankshaft main bearings.3. Clean the bearing surfaces in the cylinder block for the main bearings. Apply clean engine oil on the upper main bearing half. Do not put oil on the back side of the bearing. Using Tool (A), install the upper main bearing half (bearings with the oil holes) in the cylinder block. Be sure the tab on the back side of the bearing engages with the groove in the cylinder block.4. Clean the bearing surface of the main bearing caps. Install the lower main bearing half in the main bearing cap. Be sure the tab on the back side of the bearing engages with the groove in the main bearing cap. Apply clean engine oil on the lower main bearing half. Do no put oil on the back side of the bearing.5. Install the main bearing caps as follows:
Install the main bearing caps with the sequence number to the right, 1 through 5 (for the 4 cylinder) and 1 through 7 (for the 6 cylinder), front to rear.
a. Put main bearing caps (2) in position in the cylinder block with the sequence numbers in the correct positions.b. Apply clean engine oil to the threads of the main bearing cap mounting bolts and on the washer contact faces.c. Install main bearing cap mounting bolts (1) and the washers. Tighten both bolts of each main bearing cap to a torque of 54 7 N m (40 5 lb ft).d. Tighten the bolts and additional 1/4 90 5 degrees ( turn). 6. Check the end play of the crankshaft with Tool (B). The end play of the crankshaft
If the crankshaft is turned in the wrong direction during upper main bearing half removal, the tab of the bearing will be pushed between the crankshaft and the cylinder block. This can cause result in damage to either or both the crankshaft and the cylinder block.
Both the center and two end main journals have no oil hole. To remove these upper main bearing halves, put a thin piece of soft material, (that will not damage the crankshaft journal), against the end of the bearing half, opposite the tab. Hit the bearing with the soft material until the tab of the bearing is free from the groove in the cylinder block.2. Remove the upper half of the main bearings as follows: a. Turn the crankshaft until Tool (A) can be installed in the crankshaft journal. Install Tool (A) as shown.b. Turn the crankshaft in the direction which will push the upper main bearing half out, tab end first.c. Check the condition of the main bearings. Refer to "Guideline For Reusable Parts, Main & Connecting Rod Bearings", Form No. SEBF8009 and SEBD0531 as guide for checking bearing condition. The following steps are for the installation of the crankshaft main bearings.3. Clean the bearing surfaces in the cylinder block for the main bearings. Apply clean engine oil on the upper main bearing half. Do not put oil on the back side of the bearing. Using Tool (A), install the upper main bearing half (bearings with the oil holes) in the cylinder block. Be sure the tab on the back side of the bearing engages with the groove in the cylinder block.4. Clean the bearing surface of the main bearing caps. Install the lower main bearing half in the main bearing cap. Be sure the tab on the back side of the bearing engages with the groove in the main bearing cap. Apply clean engine oil on the lower main bearing half. Do no put oil on the back side of the bearing.5. Install the main bearing caps as follows:
Install the main bearing caps with the sequence number to the right, 1 through 5 (for the 4 cylinder) and 1 through 7 (for the 6 cylinder), front to rear.
a. Put main bearing caps (2) in position in the cylinder block with the sequence numbers in the correct positions.b. Apply clean engine oil to the threads of the main bearing cap mounting bolts and on the washer contact faces.c. Install main bearing cap mounting bolts (1) and the washers. Tighten both bolts of each main bearing cap to a torque of 54 7 N m (40 5 lb ft).d. Tighten the bolts and additional 1/4 90 5 degrees ( turn). 6. Check the end play of the crankshaft with Tool (B). The end play of the crankshaft