Information injection-pump assembly
ZEXEL
101606-9850
1016069850
NISSAN-DIESEL
16713Z6273
16713z6273
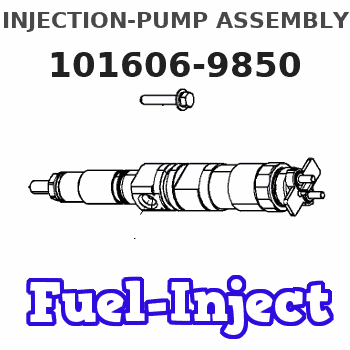
Rating:
Service parts 101606-9850 INJECTION-PUMP ASSEMBLY:
1.
_
6.
COUPLING PLATE
7.
COUPLING PLATE
8.
_
9.
_
11.
Nozzle and Holder
12.
Open Pre:MPa(Kqf/cm2)
19.6(200)
15.
NOZZLE SET
Cross reference number
ZEXEL
101606-9850
1016069850
NISSAN-DIESEL
16713Z6273
16713z6273
Zexel num
Bosch num
Firm num
Name
Calibration Data:
Adjustment conditions
Test oil
1404 Test oil ISO4113 or {SAEJ967d}
1404 Test oil ISO4113 or {SAEJ967d}
Test oil temperature
degC
40
40
45
Nozzle and nozzle holder
105780-8250
Bosch type code
1 688 901 101
Nozzle
105780-0120
Bosch type code
1 688 901 990
Nozzle holder
105780-2190
Opening pressure
MPa
20.7
Opening pressure
kgf/cm2
211
Injection pipe
Outer diameter - inner diameter - length (mm) mm 6-2-600
Outer diameter - inner diameter - length (mm) mm 6-2-600
Overflow valve
131424-8921
Overflow valve opening pressure
kPa
157
123
191
Overflow valve opening pressure
kgf/cm2
1.6
1.25
1.95
Tester oil delivery pressure
kPa
157
157
157
Tester oil delivery pressure
kgf/cm2
1.6
1.6
1.6
Direction of rotation (viewed from drive side)
Left L
Left L
Injection timing adjustment
Direction of rotation (viewed from drive side)
Left L
Left L
Injection order
1-4-2-6-
3-5
Pre-stroke
mm
3.7
3.65
3.75
Beginning of injection position
Governor side NO.1
Governor side NO.1
Difference between angles 1
Cal 1-4 deg. 60 59.5 60.5
Cal 1-4 deg. 60 59.5 60.5
Difference between angles 2
Cyl.1-2 deg. 120 119.5 120.5
Cyl.1-2 deg. 120 119.5 120.5
Difference between angles 3
Cal 1-6 deg. 180 179.5 180.5
Cal 1-6 deg. 180 179.5 180.5
Difference between angles 4
Cal 1-3 deg. 240 239.5 240.5
Cal 1-3 deg. 240 239.5 240.5
Difference between angles 5
Cal 1-5 deg. 300 299.5 300.5
Cal 1-5 deg. 300 299.5 300.5
Injection quantity adjustment
Adjusting point
-
Rack position
11.3
Pump speed
r/min
800
800
800
Average injection quantity
mm3/st.
89
87.4
90.6
Max. variation between cylinders
%
0
-3.5
3.5
Basic
*
Fixing the rack
*
Standard for adjustment of the maximum variation between cylinders
*
Injection quantity adjustment_02
Adjusting point
Z
Rack position
9+-0.5
Pump speed
r/min
340
340
340
Average injection quantity
mm3/st.
9.5
7.7
11.3
Max. variation between cylinders
%
0
-10
10
Fixing the rack
*
Standard for adjustment of the maximum variation between cylinders
*
Injection quantity adjustment_03
Adjusting point
A
Rack position
R1(11.3)
Pump speed
r/min
800
800
800
Average injection quantity
mm3/st.
89
88
90
Basic
*
Fixing the lever
*
Injection quantity adjustment_04
Adjusting point
B
Rack position
R1+0.95
Pump speed
r/min
1450
1450
1450
Average injection quantity
mm3/st.
96
92
100
Fixing the lever
*
Injection quantity adjustment_05
Adjusting point
I
Rack position
-
Pump speed
r/min
100
100
100
Average injection quantity
mm3/st.
115
115
125
Fixing the lever
*
Rack limit
*
Timer adjustment
Pump speed
r/min
1160
Advance angle
deg.
1
1
1.5
Timer adjustment_02
Pump speed
r/min
1450
Advance angle
deg.
7
6.5
7.5
Remarks
Finish
Finish
Test data Ex:
Governor adjustment
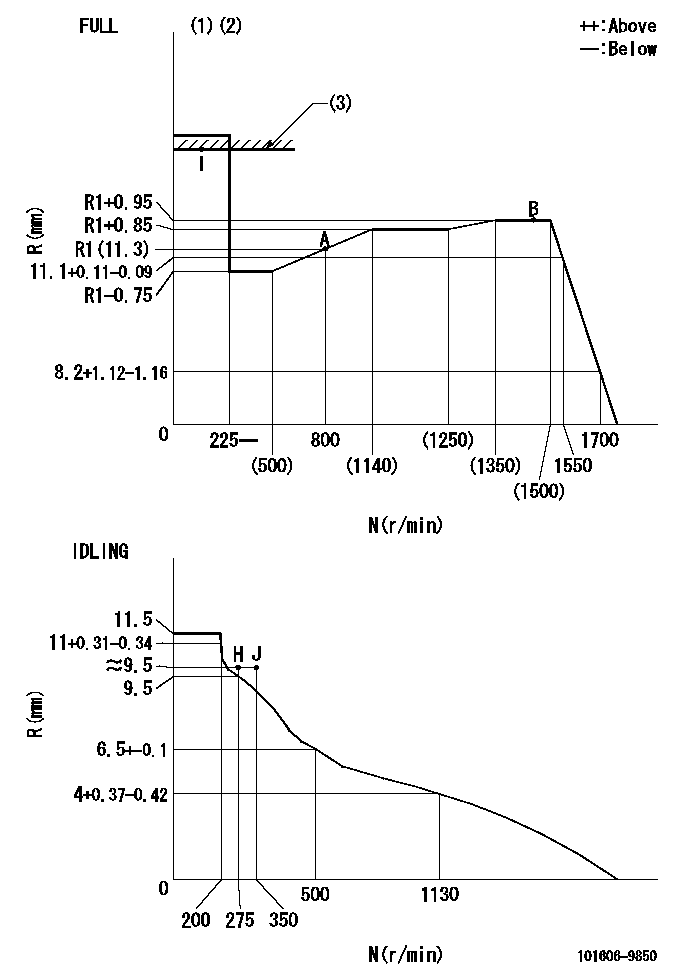
N:Pump speed
R:Rack position (mm)
(1)Torque cam stamping: T1
(2)Tolerance for racks not indicated: +-0.05mm.
(3)RACK LIMIT
----------
T1=J68
----------
----------
T1=J68
----------
Speed control lever angle
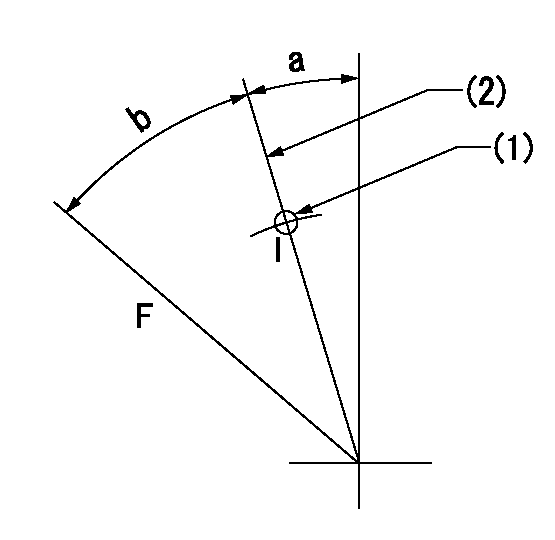
F:Full speed
I:Idle
(1)Use the hole at R = aa
(2)Stopper bolt set position 'H'
----------
aa=39mm
----------
a=5deg+-5deg b=36.5deg+-3deg
----------
aa=39mm
----------
a=5deg+-5deg b=36.5deg+-3deg
Stop lever angle
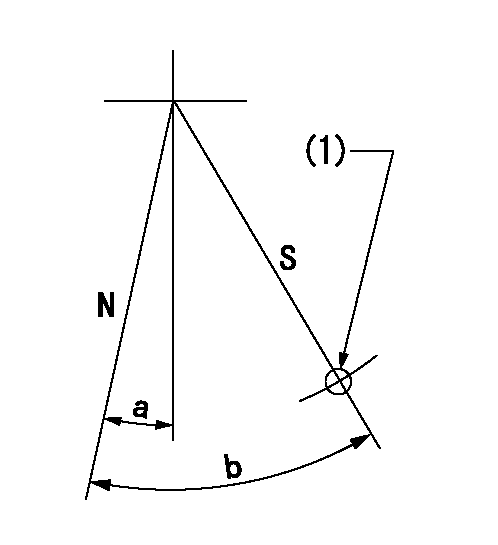
N:Pump normal
S:Stop the pump.
(1)Use the hole at R = aa
----------
aa=32mm
----------
a=10deg+-5deg b=40deg+-5deg
----------
aa=32mm
----------
a=10deg+-5deg b=40deg+-5deg
0000001501 LEVER

(a) Speed lever
(B) Accelerator lever
(C) Accelerator lever stopper bolt
1. Accelerator lever setting method
With the speed lever in the idling position, back off the accelerator lever stopper bolt L1 from where it contacts point a.
----------
r1=39mm r2=38mm L1=1+0.5mm
----------
----------
r1=39mm r2=38mm L1=1+0.5mm
----------
Timing setting
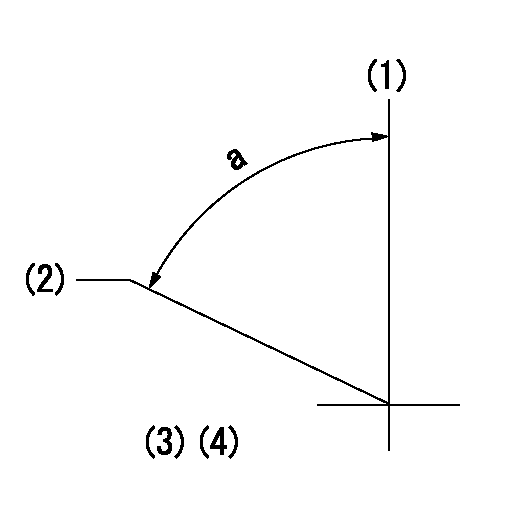
(1)Pump vertical direction
(2)Position of timer's threaded hole at No 1 cylinder's beginning of injection
(3)-
(4)-
----------
----------
a=(80deg)
----------
----------
a=(80deg)
Information:
If there is clearance available, it is recommended that the oil pan be removed prior to removing the rear seal carrier. A new oil pan gasket must be installed after the rear seal carrier has been installed.1. Loosen oil pan mounting bolts (2). Carefully lower the oil pan away from the cylinder block.2. Remove eight bolts (1) and the washers that hold the rear seal carrier to the cylinder block. Using a screwdriver, carefully pry the rear seal carrier off of the two dowels in the cylinder block. The following steps are for the installation of the rear seal carrier.
1U8846 Gasket Maker is used on the joint face of the rear seal carrier. Do not allow the gasket maker to get into the oil passage in the cylinder block mounting face.
3. Prepare rear seal carrier (3) for installation as follows: a. Clean the joint face of the rear seal carrier with 8T9011 Component Cleaner.b. Apply 6V1541 Quick Cure Primer to the joint face of the rear seal carrier. Allow the primer to air dry three to five minutes.c. Apply 1U8846 Gasket Maker to the joint face of the rear seal carrier. Spread the gasket maker uniformly. The rear seal carrier must be installed within ten minutes after application of the gasket maker.4. Put rear seal carrier (3) in position on the dowels in the rear of the cylinder block. If necessary, use a soft faced hammer to position the rear seal carrier against the cylinder block.5. Apply 9S3263 Thread Lock on the threads of eight bolts (1). Install eight bolts (1) and the washers that hold the rear seal carrier to the cylinder block.6. Check the condition of the oil pan gasket. If the gasket is not damaged, raise the oil pan into position, and tighten oil pan mounting bolts (2). If the gasket is damaged, remove the oil pan, and replace the gasket. See the topic "Remove & Install Oil Pan" in this module.End By:a. install flywheel housing
1U8846 Gasket Maker is used on the joint face of the rear seal carrier. Do not allow the gasket maker to get into the oil passage in the cylinder block mounting face.
3. Prepare rear seal carrier (3) for installation as follows: a. Clean the joint face of the rear seal carrier with 8T9011 Component Cleaner.b. Apply 6V1541 Quick Cure Primer to the joint face of the rear seal carrier. Allow the primer to air dry three to five minutes.c. Apply 1U8846 Gasket Maker to the joint face of the rear seal carrier. Spread the gasket maker uniformly. The rear seal carrier must be installed within ten minutes after application of the gasket maker.4. Put rear seal carrier (3) in position on the dowels in the rear of the cylinder block. If necessary, use a soft faced hammer to position the rear seal carrier against the cylinder block.5. Apply 9S3263 Thread Lock on the threads of eight bolts (1). Install eight bolts (1) and the washers that hold the rear seal carrier to the cylinder block.6. Check the condition of the oil pan gasket. If the gasket is not damaged, raise the oil pan into position, and tighten oil pan mounting bolts (2). If the gasket is damaged, remove the oil pan, and replace the gasket. See the topic "Remove & Install Oil Pan" in this module.End By:a. install flywheel housing