Information injection-pump assembly
ZEXEL
101606-9780
1016069780
NISSAN-DIESEL
16713Z6269
16713z6269
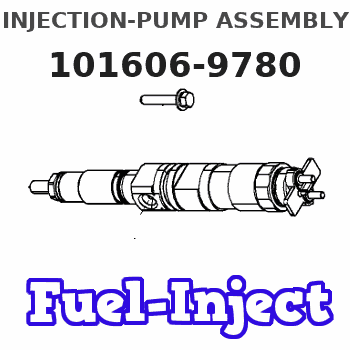
Rating:
Service parts 101606-9780 INJECTION-PUMP ASSEMBLY:
1.
_
7.
COUPLING PLATE
8.
_
9.
_
11.
Nozzle and Holder
16600-Z6003
12.
Open Pre:MPa(Kqf/cm2)
17.7{180}/22.6{230}
14.
NOZZLE
Cross reference number
ZEXEL
101606-9780
1016069780
NISSAN-DIESEL
16713Z6269
16713z6269
Zexel num
Bosch num
Firm num
Name
Calibration Data:
Adjustment conditions
Test oil
1404 Test oil ISO4113 or {SAEJ967d}
1404 Test oil ISO4113 or {SAEJ967d}
Test oil temperature
degC
40
40
45
Nozzle and nozzle holder
105780-8250
Bosch type code
1 688 901 101
Nozzle
105780-0120
Bosch type code
1 688 901 990
Nozzle holder
105780-2190
Opening pressure
MPa
20.7
Opening pressure
kgf/cm2
211
Injection pipe
Outer diameter - inner diameter - length (mm) mm 6-2-600
Outer diameter - inner diameter - length (mm) mm 6-2-600
Overflow valve
131424-8921
Overflow valve opening pressure
kPa
157
123
191
Overflow valve opening pressure
kgf/cm2
1.6
1.25
1.95
Tester oil delivery pressure
kPa
255
255
255
Tester oil delivery pressure
kgf/cm2
2.6
2.6
2.6
Direction of rotation (viewed from drive side)
Left L
Left L
Injection timing adjustment
Direction of rotation (viewed from drive side)
Left L
Left L
Injection order
1-4-2-6-
3-5
Pre-stroke
mm
3.7
3.65
3.75
Beginning of injection position
Governor side NO.1
Governor side NO.1
Difference between angles 1
Cal 1-4 deg. 60 59.5 60.5
Cal 1-4 deg. 60 59.5 60.5
Difference between angles 2
Cyl.1-2 deg. 120 119.5 120.5
Cyl.1-2 deg. 120 119.5 120.5
Difference between angles 3
Cal 1-6 deg. 180 179.5 180.5
Cal 1-6 deg. 180 179.5 180.5
Difference between angles 4
Cal 1-3 deg. 240 239.5 240.5
Cal 1-3 deg. 240 239.5 240.5
Difference between angles 5
Cal 1-5 deg. 300 299.5 300.5
Cal 1-5 deg. 300 299.5 300.5
Injection quantity adjustment
Adjusting point
-
Rack position
11.3
Pump speed
r/min
800
800
800
Average injection quantity
mm3/st.
89
87.4
90.6
Max. variation between cylinders
%
0
-3.5
3.5
Basic
*
Fixing the rack
*
Standard for adjustment of the maximum variation between cylinders
*
Injection quantity adjustment_02
Adjusting point
Z
Rack position
9+-0.5
Pump speed
r/min
340
340
340
Average injection quantity
mm3/st.
9.5
7.7
11.3
Max. variation between cylinders
%
0
-10
10
Fixing the rack
*
Standard for adjustment of the maximum variation between cylinders
*
Injection quantity adjustment_03
Adjusting point
A
Rack position
R1(11.3)
Pump speed
r/min
800
800
800
Average injection quantity
mm3/st.
89
88
90
Basic
*
Fixing the lever
*
Injection quantity adjustment_04
Adjusting point
B
Rack position
R1+0.95
Pump speed
r/min
1450
1450
1450
Average injection quantity
mm3/st.
96
92
100
Fixing the lever
*
Injection quantity adjustment_05
Adjusting point
I
Rack position
-
Pump speed
r/min
100
100
100
Average injection quantity
mm3/st.
115
115
125
Fixing the lever
*
Rack limit
*
Timer adjustment
Pump speed
r/min
1160
Advance angle
deg.
1
0.5
1.5
Timer adjustment_02
Pump speed
r/min
1450
Advance angle
deg.
7
6.5
7.5
Remarks
Finish
Finish
Test data Ex:
Governor adjustment
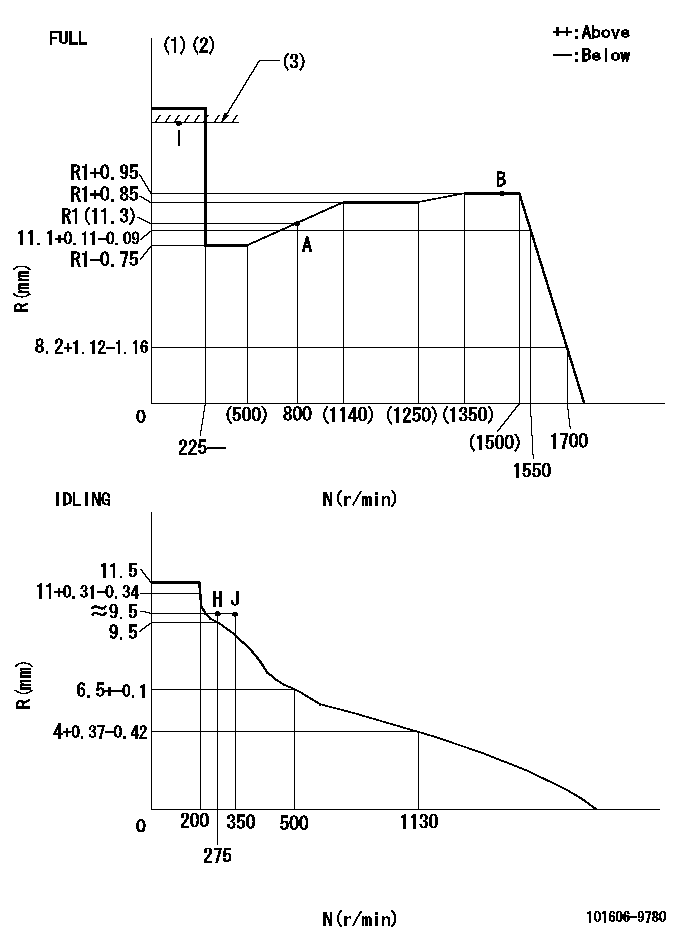
N:Pump speed
R:Rack position (mm)
(1)Torque cam stamping: T1
(2)Tolerance for racks not indicated: +-0.05mm.
(3)RACK LIMIT
----------
T1=J68
----------
----------
T1=J68
----------
Speed control lever angle
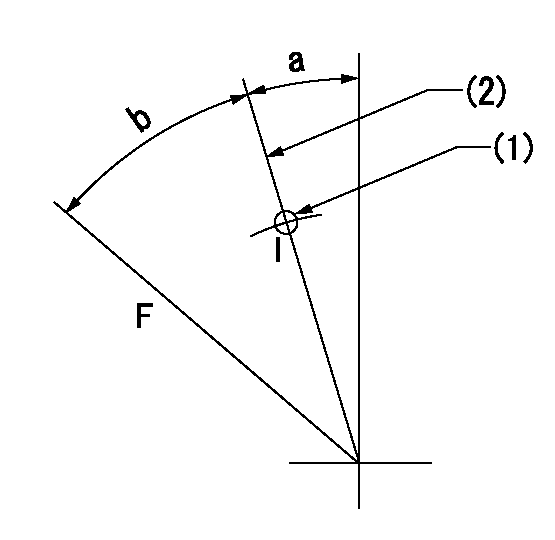
F:Full speed
I:Idle
(1)Use the hole at R = aa
(2)Stopper bolt set position 'H'
----------
aa=38mm
----------
a=5deg+-5deg b=36.5deg+-3deg
----------
aa=38mm
----------
a=5deg+-5deg b=36.5deg+-3deg
Stop lever angle
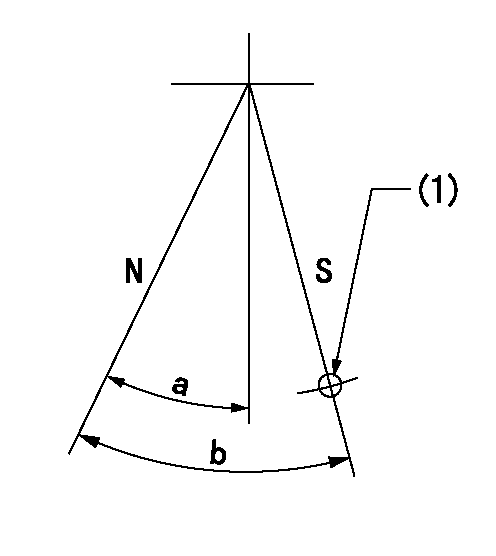
N:Pump normal
S:Stop the pump.
(1)Use the hole at R = aa
----------
aa=32mm
----------
a=10deg+-5deg b=40deg+-5deg
----------
aa=32mm
----------
a=10deg+-5deg b=40deg+-5deg
Timing setting
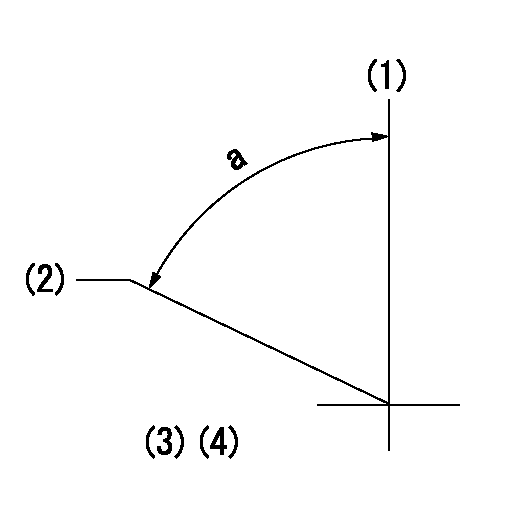
(1)Pump vertical direction
(2)Position of timer's threaded hole at No 1 cylinder's beginning of injection
(3)-
(4)-
----------
----------
a=(80deg)
----------
----------
a=(80deg)
Information:
Illustration 62 g02807941
Remove the plug
Remove plug (2) .
Illustration 63 g02807956
Set speed by turning adjusting screw
Adjust speed. If Ng exceeds TMI specifications, tighten the adjusting screw. If Ng is less than the specified value, loosen the adjusting screw.
Illustration 64 g02807957
Adjust the maximum-speed stopper bolt
Adjust the maximum-speed stopper bolt until the speed at the start of high-speed control is Nf.
Check that the no-load maximum speed is Ng (described in Step 1). Continue adjustment until the specified value is obtained.
Illustration 65 g02807958
Increase pump speed to make sure that the control rack position reaches Ra.
Illustration 66 g02807959
Full-load Adjustment
Illustration 67 g02807997
Install the cover and adjust full-load stopper bolt
Install cover (3) on governor using bolts and lockwashers (2). Use caution when installing the cover to make sure that the O-ring seal is in the seal groove.
Illustration 68 g02807999
Position the control lever at maximum-speed position.
Adjust full-load stopper bolt (1) to the f"ull-load fuel injection quantity" position. See TMI for the specifications (Point A).
Install cap.Control Lever Angle Measurement
Illustration 69 g02808016
Measuring control lever angle at the "full-speed" and "idling" positions.
Measuring the control lever angle at the "idling" and "full" positions.
If the angle is not as specified by TMI, replace the shifters shim. If the control lever is positioned toward the "full" position, replace the shifters shim with a thicker one. When control lever is toward the "idling" position, replace the shim with a thinner one.Check Starting Delivery
Illustration 70 g02808018
Remove measurement adapter
Remove measurement adapter (1) .
Illustration 71 g02808038
Cap must be installed to check delivery rate
Install cap (2) .
Run pump at speed specified in TMI.
Check delivery rate with specifications listed in TMI.
Stop pump rotation.
Illustration 72 g02808058
Adjusting screw for setting fuel flow
If delivery rate does not meet TMI specifications, remove cap (2), loosen lock nut, and adjust screw (3). Adjusting screw outward decreases fuel flow and inward increases fuel flow.
Install cap (2) and recheck delivery rate. Repeat Steps 2 through 6 until delivery rate is at specified value.Lockwiring Caps of Adjustment Screws
All adjustment stops (screws) that directly affect engine performance should be lockwired after adjustment. Do not readjust any stop without using the test stand can adversely affect the engine and engine performance.